Have you ever struggled to choose the right stamping method? In producing motor cores, progressive die and compound die stamping each has its advantages. But how do you make the right choice between the two? Many motor designers often find themselves in this dilemma.
As a China manufacturer with years of experience in motor core production, I understand that every design decision impacts both motor performance and production costs.
Today, I’ll explain the differences between progressive stamping and compound stamping. This will help you quickly determine which process suits your motor design best.
Ready? Let’s dive into the differences between these two stamping processes and make sure you don’t let the decision become a headache!
Progressive Die Stamping
Progressive stamping is a high-speed stamping technology that integrates equipment, molds, materials, and processes.
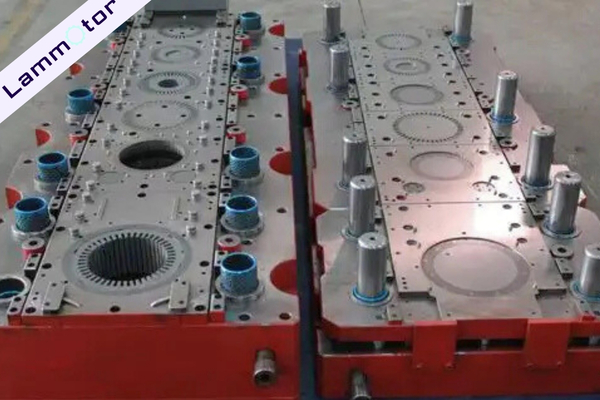
A good stator and rotor core need to be made with precise hardware stamping molds. These molds use automatic riveting processes and are then pressed on high-precision stamping machines.
The benefit of this method is that it ensures maximum flatness and accuracy of the product.
The process starts with electrical steel strips coming from coils. First, they go through a leveling machine, then an automatic feeder delivers the strips to the mold.
The machine can complete the stamping, forming, finishing, trimming, automatic core lamination, and other processes in a continuous manner.
Finally, the finished motor cores are delivered from the mold, and the entire stamping process is done automatically on a high-speed press.
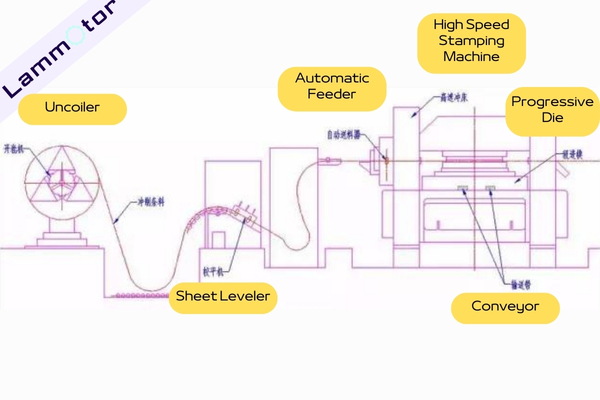
Depending on the size and volume of the product, we may design single, double, or multi-row molds.
Advantages of Progressive Die Stamping:
- High automation
- High dimensional accuracy
- Long tool life
- Ideal for high-volume production
- The multi-station progressive mold integrates many processes into one mold, reducing production steps and improving motor manufacturing efficiency.
Common High-Speed Stamping Equipment
Currently, the main equipment used for high-speed stamping of motor stator and rotor cores includes:
- Germany: SCHULER
- Japan: AIDA, DOBBY, ISIS
- USA: MINSTER
- Taiwan, China: Yingyu
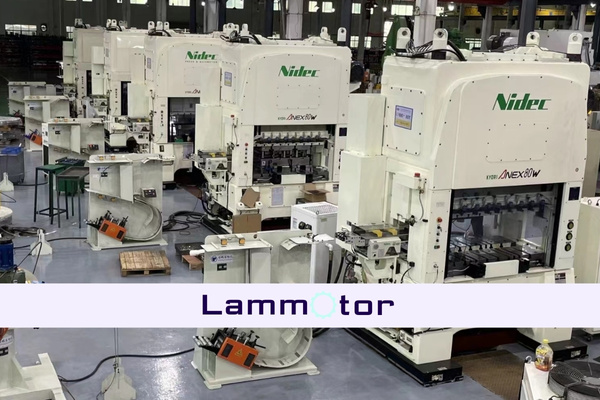
These precise high-speed presses feature high feed accuracy, stamping precision, machine rigidity, and reliable safety systems. Their stamping speed typically ranges from 200 to 600 strokes per minute. They are perfect for stamping motor stator and rotor cores, especially for automatic lamination and parts with twisting, rotating, or automatic riveting lamination structures.
Multi-station progressive molds for high-speed stamping can manufacture structural cores with automatic laminations. The stator and rotor cores can also have twisting slots and large-angle rotating lamination riveting structures.
Compared to regular stamping molds, multi-station progressive molds offer higher precision, increased production efficiency, longer tool life, better consistency in core size accuracy, easier automation, and are ideal for mass production. This is the direction of development for precision molds in the motor industry.
Progressive molds for stators and rotors include rotation mechanisms, counting separation mechanisms, and safety devices. Stamping steps like automatic lamination, rotor twisting, and large-angle rotating lamination riveting are all completed at the stator and rotor stamping stations.
The main parts of progressive molds, including punches and dies, are made of hard carbide material. Each sharpening can handle over 1.5 million strokes, and the mold’s total life exceeds 120 million strokes.
4 Types of Core Stamping Point Shapes
There are two types of laminated core structures:
- Dense Lamination: Laminated cores don’t need external pressure. They reach sufficient bonding force as they exit the mold.
- Semi-Dense Lamination: There are gaps between the laminated sheets when they exit the mold. Additional pressure is required to ensure proper bonding force.
The geometric shapes of core points are:
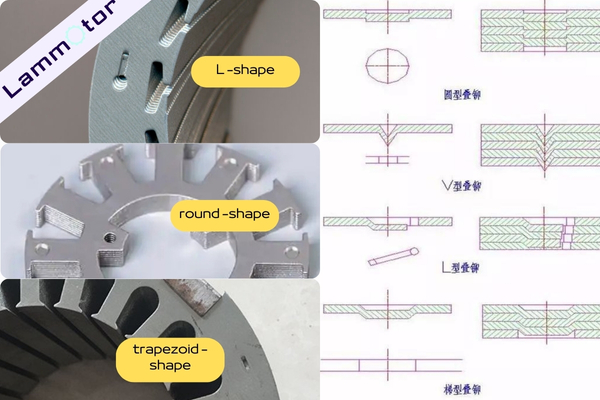
- Cylindrical Points: Suitable for dense lamination structures.
- V-Shaped Points: Known for strong bonding strength between core sheets. Suitable for dense and semi-dense lamination structures.
- L-Shaped Points: Usually used for the twisted lamination of rotor cores in AC motors. Suitable for dense lamination structures.
- Trapezoidal Points: Available in both rounded and long trapezoidal structures, both suitable for dense lamination.
Stamping Adhesive Integration Technology
In addition to the traditional point stacking method inside the mold, there is also an adhesive stacking method.
To achieve fast stamping, curing, and bonding of motor rotor and stator cores inside the mold, the mold uses a stamping and pressing integrated design. Stamping and pressing happen simultaneously, with a rotating pressing mechanism using mechanical automation. This increases the core’s production efficiency and saves manufacturing costs.
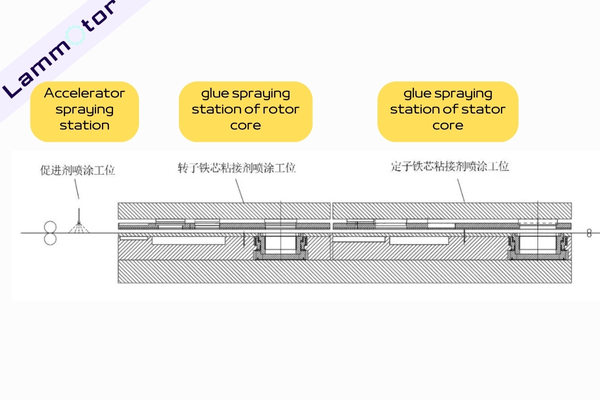
How the Mold Works
The silicon steel strips are fed into the mold for stamping. Adhesive and curing agents are sprayed on the surface of the silicon steel sheets. The contact between the catalyst and adhesive quickly cures the adhesive, allowing the stator and rotor cores to stack.
When the cores reach the preset number of sheets, the glue spraying stops, and the cores are transported from the mold.
The adhesive bonding method between core sheets uses sprayed glue. Compared to traditional welding and riveting methods, adhesive bonding improves motor efficiency. It reduces noise, vibration, and roughness, while increasing the overall strength of the motor core.
Additionally, it improves durability, reduces iron loss, and increases magnetic flux density.
The mold also has an external spraying station. Before the silicon steel strips enter the mold, a fast-curing agent is sprayed onto the strips to facilitate curing.
Compound Die Stamping
Single-stroke dies, also called soft molds or compound molds, typically consist of a die, a punch, and one or more punches. In the stamping process, each stroke can only complete one type of stamping operation. When designing stator and rotor sleeve stamps, separate single-stroke dies are often required.
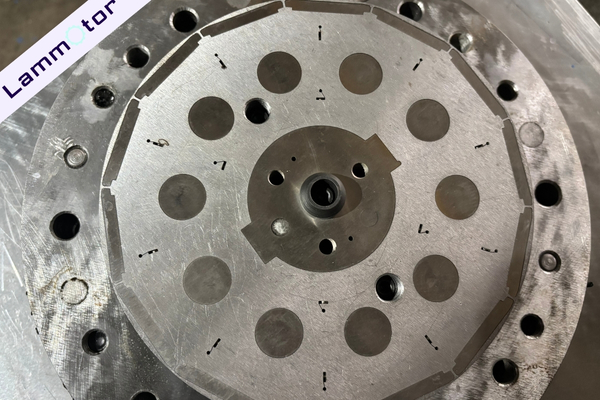
Advantages of Compound Die Stamping:
- Simple structure
- Low mold cost, typically ranging from a few thousand to tens of thousands of dollars depending on product size and design
- Short cycle time, usually 3-4 weeks, with urgent orders completed in 2 weeks
- High flexibility for design changes, which allows for quicker mold redesign and lower costs, especially in the early stages of product development
- Lower product cost compared to wire-cut samples, but achieving similar dimensional accuracy as fine wire cutting.
Disadvantages of Compound Die Stamping:
- Since the process completes in one stroke, it is difficult to control product deformation. The elliptical shape of stamped silicon steel sheets may be poor.
- The simple design of single-stroke dies cannot achieve automatic continuous lamination and riveting, requiring manual stacking and pressing. This makes the per-piece cost higher.
- Designed for prototype validation, the tool life typically doesn’t exceed 1 million strokes, and upgrading the mold doesn’t significantly extend its lifespan.
- The material used for the dies is standard tool steel, so burrs can form on the stamped sheets, and addressing this issue is difficult.
- Single-stroke dies are typically used with low-speed C-frame presses, and since they require manual operation, production efficiency is low. The production rate is typically 30-60 pieces per minute.
Comparison Between Progressive Die and Compound Die Stamping
Comparative Aspect | Progressive Stamping | Compound Stamping |
Production Speed and Quantity | Faster, ideal for large-scale production | Slower, suitable for small-scale production |
Material Efficiency and Waste Reduction | Maximizes material efficiency with optimized layout | Sequential processing causes more waste, especially in prototypes |
Complexity and Design Flexibility | Best for complex designs, more flexible | Suited for simpler designs, fewer complex features |
Mold Cost and Maintenance | Higher mold cost, lower maintenance | Lower mold cost, more frequent maintenance |
Labor and Operating Costs | High automation, low labor cost | Requires more manual labor, higher cost |
Motor Lamination Quality and Precision | Moderate precision | Higher precision, better consistency |
Stamping Applications | Ideal for large motor cores and complex designs, common in power generation, heavy machinery | Best for standardized motor lamination cores, suitable for home appliances, cars, consumer electronics, HVAC systems |
How to Choose the Right Stamping Method for Your Motor Stator and Rotor?
Choosing the right stamping technology depends on the specific requirements of your motor lamination project. Consider the following factors:
Production Volume
Match the required volume to each stamping method’s capabilities. Progressive stamping is ideal for mass production, while compound stamping is better for smaller runs.
Lamination Design Complexity
If your design involves complex shapes or varying sizes, compound stamping’s flexibility may be beneficial. For simpler designs, progressive stamping provides better accuracy and cost efficiency.
Budget Constraints
Consider the available budget for mold and production. While progressive stamping has higher initial costs, it may be more economical for medium to large volumes in the long run.
Delivery Time and Schedule
Evaluate setup and delivery times for each project. Compound stamping may be faster, making it a better option for urgent or short production runs.
Quality and Precision Requirements
For applications requiring excellent precision and consistency, progressive stamping is the preferred choice. If slight variations in precision are acceptable, compound stamping can still deliver satisfactory results.
Applicable Sizes
Compound stamping is ideal for large motor cores with special sizes, while progressive stamping is better for mass-produced small cores.
We also offer rotary notching. We cut the silicon steel sheet to the desired size, and each sheet will be individually stamped into the desired shape. Single-slot stamping is a suitable method for stator laminates with large outside diameters and large sample sizes.
Contact Us for Motor Stator and Rotor Laminations Manufacturing
To help clients quickly verify motor stator and rotor core samples for new projects, Lammotor supports single-stroke die sampling, wire-cutting sampling, and laser-cutting sampling. We customize the sampling methods according to client needs to shorten the product development cycle. If you need motor stator or rotor core sampling or mass production, please contact us.