Motor Lamination Stacks Stamping in china
We are a motor lamination stacks China manufacturer and specialize in stamping stator and rotor lamination stacks for motors and have been essential to many projects. Our services are always reliable, efficient, and accurate. Whether you require lamination stacks for automotive, wind power, motor pumps, or any other industrial application, we have the expertise and flexibility to meet your needs. We pay great attention to detail to guarantee our customer’s satisfaction with each product we create.
Stamping Capabilities for motor lamination stacks
With our modern stamping equipment and experienced team, we can tackle any task regardless of complexity or size. Meanwhile, we can manufacture and maintain stamping molds.
We ensure every motor assembly is up to the highest standard before being sent out for use in different industrial applications.
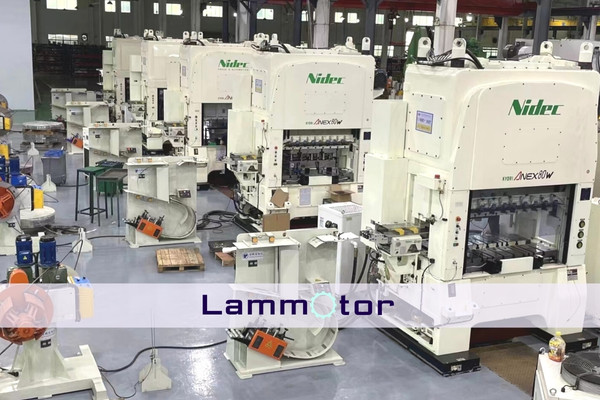
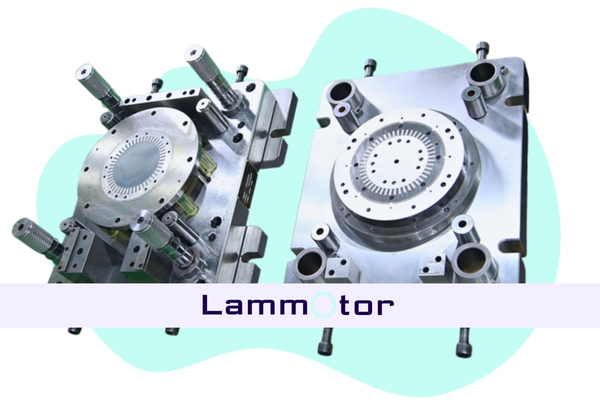
compound stamping
Compound stamping is a process used to produce laminations for electric motors.
It produces a complete part in one station. It involves using multi-stage dies and various processes such as punching, blanking, and forming. This results in parts with intricate shapes and high structural integrity.
progressive stamping
Progressive stamping is a metal-forming process that produces electrical steel lamination from sheet material. It is a cost-effective and efficient way of mass-producing components for various motors, mechanical assemblies, and electronic devices.
Progressive stamping produces a complete part with no secondary operation. As a result, it can produce a large number of parts in a short time. Although dies often take longer to make and generally incur higher manufacturing costs, it is ideal for complex parts that require precise tolerances.
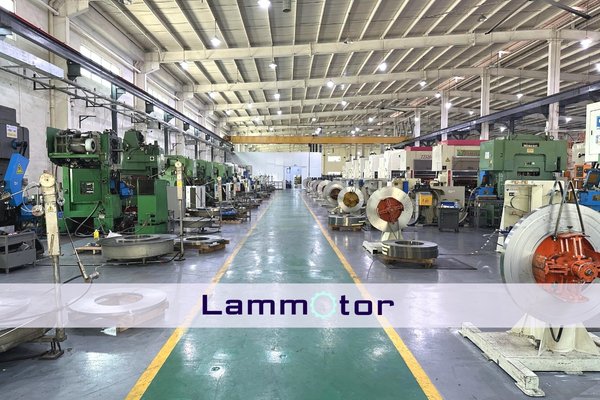
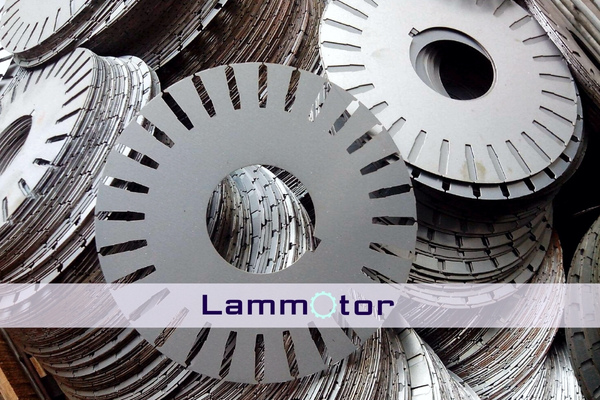
rotary notching
Rotary notching is a specialized process to punch and create patterns on the lamination core. It is an efficient and accurate way to create motor stator and rotor lamination patterns.
The process can be applied to single- or double-sided laminations and soft and hard materials. Rotary notching can reduce production time by up to 50% compared with traditional methods.
Secondary Operations
Stacking (Welding/riveting/gluing)
Stacking is done after punching and stamping to assemble the individual laminations. Depending on the application, it can be done using welding, riveting, or gluing.
Electrostatic Motor Epoxy Powder Coating
Electrostatic motor epoxy powder coating can be an additional protective layer over the laminated cores. This provides further protection from corrosion and increases the life of the motor core by many years.
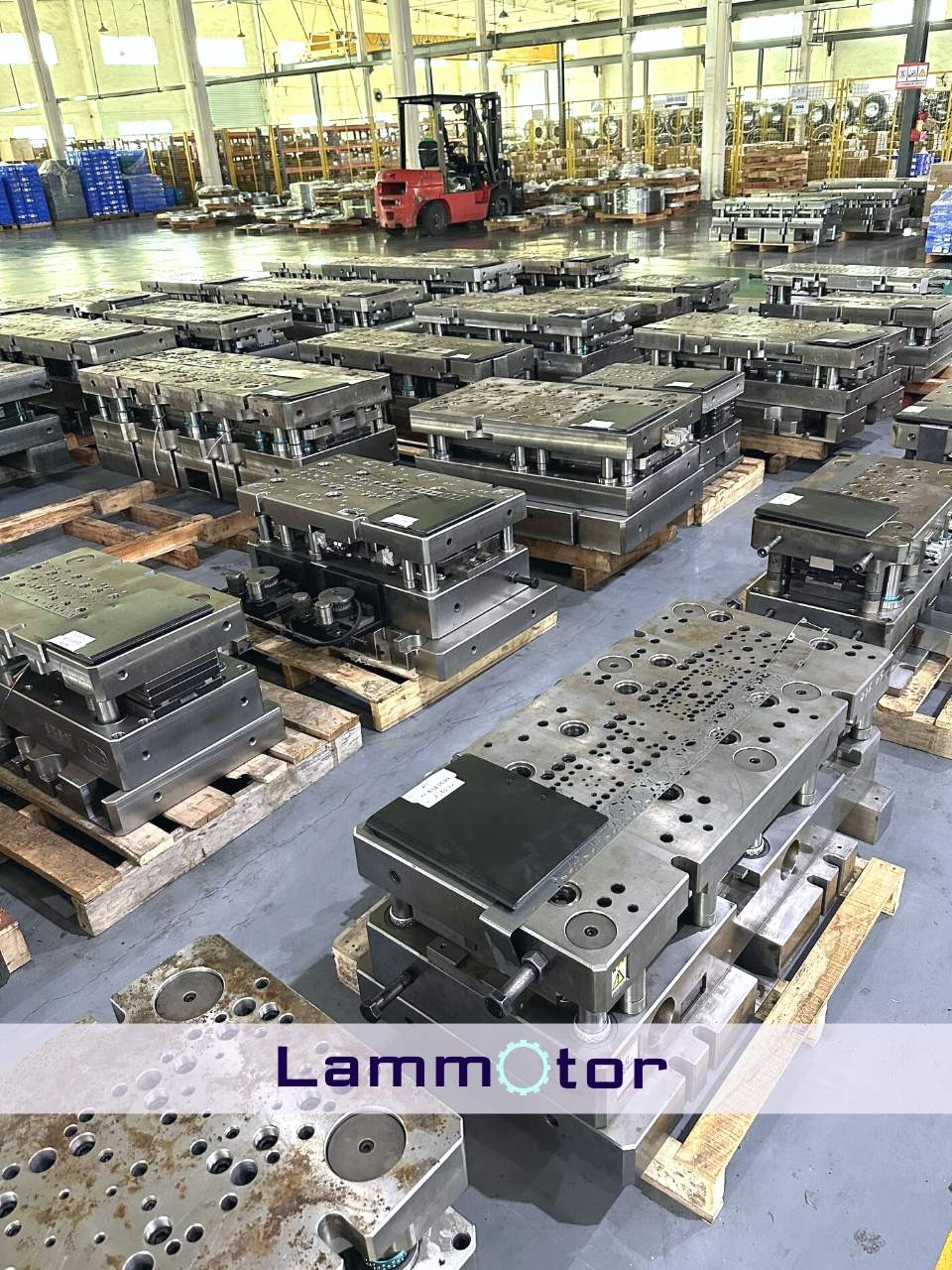
Motor Lamination Stacks Stamping Dies
Our mold department has been designing and manufacturing molds for our products since it started in 2015. We have used various stamping dies, such as progressive, compound, and notching.
Each type of stamping die is designed for different tasks, depending on the desired shape and finish. Our team designs molds with a high level of detail, ensuring perfect results for each product.
High-grade Tool Steel
To make them, we generally use high-grade tool steel, such as H13, A2, or D2.
Maintenance
We are also responsible for maintaining and repairing all production molds to ensure we can handle any job.
Materials used in stator and rotor lamination Stacks
Silicon steel is the most common material used in lamination stack manufacturing. It is corrosion and wear-resistant, cost-effective, and has high strength. Other materials used in lamination stamping include cobalt alloys and nickel alloys. Each of these materials has advantages and disadvantages, which must be weighed carefully when choosing the material for motor lamination.
Silicon steel (electrical steel)
Silicon steel is the most commonly used material for motor core lamination. It can withstand large amounts of force from magnetic fields without breaking down quickly or losing efficiency. The combination of these properties makes it perfect for applications such as AC motors and generators, which require reliable performance even under heavy loads.
Cobalt alloys
Cobalt alloys are commonly used in motor core lamination stamping for their excellent performance and durability. These alloys are resistant to corrosion, making them an excellent choice for laminating high-temperature metals such as steel. Additionally, they have high electrical conductivity, which is essential for efficient motor operation.
Nickel alloys
Nickel alloys are used for motor core lamination stamping as they provide high electrical conductivity, excellent corrosion resistance, and good magnetic properties. The alloys are suitable for use in both stator and rotor lamination stamping, which makes them ideal for improving the performance of electric motors. They can be suitable for automotive, aerospace, and industrial.
Thin-Gauge Electrical Steel
Thin-gauge electrical steel has a high magnetic permeability rate, effectively reducing the size of the stator and rotor cores. This helps to reduce the overall weight and cost of the motor. The thickness of this steel can range from 0.35mm to 0.5mm, depending on the application requirements. Overall, thin-gauge electrical steel is crucial for efficient electric motors with reduced costs and weight.
Comprehensive Testing Services
quality control
We are an ISO 9001:2015 certified company. Our quality department has state-of-the-art measuring equipment to accurately measure or reverse engineer our customers’ motor and generator components and electrical steel lamination.
Choose high-quality silicon steel for lamination stacks.
Our stamping machines have precise cutting capabilities.
We use CMM and other precision measuring Instruments to ensure the size of products.
We provide inspection reports.
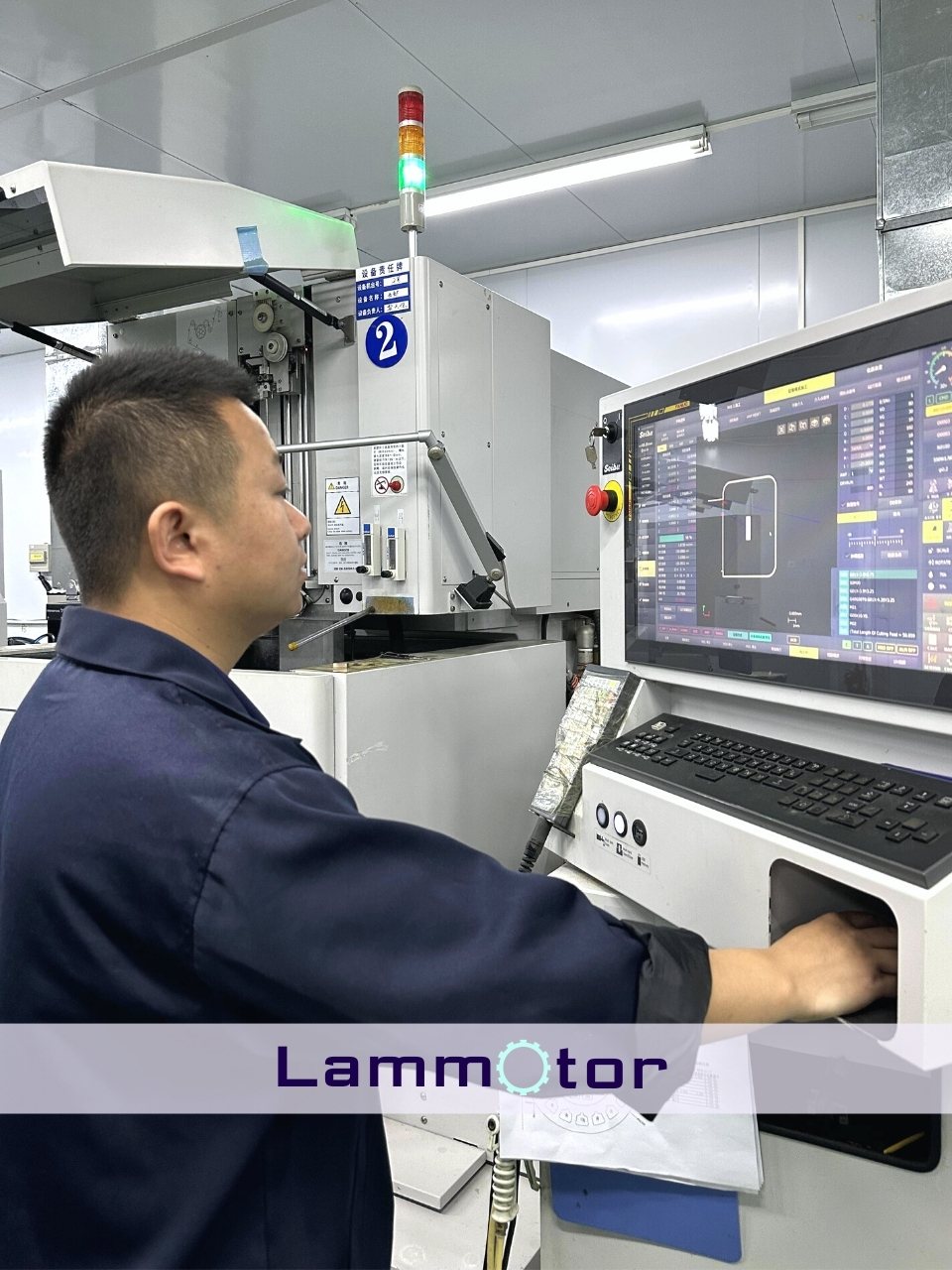
Why choose us
We have experienced engineers and technicians to assist with the design process. – Our efficient production processes minimize costs and lead time while maximizing quality control.
With our expertise in motor lamination stack manufacturing, we can guarantee the execution precision and consistency of your project.
High-speed precision stamping
We offer a high-speed and precision stamping process that produces components with superior quality and accuracy. We use advanced equipment and experienced technicians to ensure consistent results.
High-quality materials
For high-quality motor lamination stack, we use only high-quality silicon steel materials to ensure end products are durable and performance-driven.
Motor lamination stacks stamping FAQs
Lamination stamping can create motor core laminations from sheet metal.
It involves punching holes and slots into the metal before it is stamped using high-grade steel or carbide punch and die tool pieces.
This process can produce high-precision parts with tight tolerances and no burrs.
The laminations are stacked one on top of another to form the core of an electric motor, transformer, or generator.
Lamination stamping increases the efficiency of motors by minimizing electrical losses and reducing size and weight, allowing for easier installation in tight spaces.
Motor lamination stamping is a process that has been suitable for many years in the motor and transformer industry.
This process utilizes precision tools to produce complex iron cores for motors, transformers, and generators.
It offers several benefits over traditional winding methods, including cost savings and improved efficiency.
The main benefit of stator & rotor lamination stack manufacturing is its cost-effectiveness.
This method allows us to produce parts faster than with winding, thus resulting in lower labor costs.
It also eliminates the need for costly secondary operations such as pressing or grinding, reducing manufacturing costs.
Additionally, lamination stamping can produce very uniform and consistent results that are difficult to achieve using other methods.
Motor stators and rotors are components essential to the construction of electric motors, and the most common material is cold-rolled non-oriented silicon steel.
This steel has high thermal conductivity, good electrical insulation properties, and low magnetic losses.
Stamping requires high precision and strength, so materials like nickel and cobalt alloys may also be suitable for some applications.
We can see many different types of motors in the application of motor core laminations, ranging from small electric motors used in consumer electronics to large industrial motors.
Motor core lamination is important in these motors’ efficient operation and performance.
Motor core lamination can be suitable for AC and DC machines, such as electric generators, alternators, induction motors, synchronous motors, inverters, and electric welding machines.
Need to stamp electric motor lamination Stacks?
Working with us offers numerous benefits when punching motor lamination. In addition to providing high-quality products at affordable prices, we offer full-service capabilities that let customers avoid costly mistakes during manufacturing.
We also offer top-level quality control involving stringent testing procedures and inspection processes. Thus, we help ensure consistent performance from part to part and from batch to batch. For electric motor lamination punching and stamping in China, contact us today.