Motor laminations are an essential component of efficient motor production. They are thin, flat steel sheets that are punched into specific shapes and sizes to form the core of an electric motor. One of the most critical factors in producing high-quality rotor and stator laminations is selecting the right silicon steel grade for electrical steel laminations.
Silicon steel is a ferromagnetic alloy that contains silicon as well as other elements such as carbon and manganese. It is characterized by its high magnetic permeability and low core losses. In this blog, we will provide a guide on how to select the right grade of silicon steel for your motor lamination project.
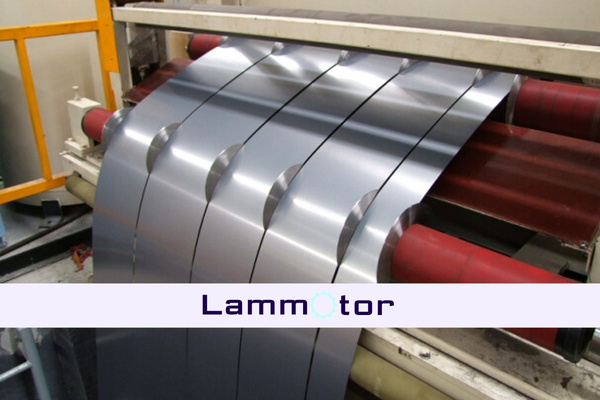
Different Silicon Steel Grades
There are different grades of silicon steel available, each with unique properties that make them suitable for different applications. The most common types of silicon steel used in motor laminations are M19, M27, and M36.
M19
M19 is the most common grade of silicon steel for motor laminations. And M19 is a low-carbon silicon steel that has excellent magnetic properties, making it well-suited for use in transformer cores. Its high magnetic permeability allows for efficient energy transfer, making it an ideal choice for electrical power transmission and distribution.
M27
M27 has a higher magnetic permeability and lower core losses than M19, making it suitable for high-frequency motors.
M36
With a higher silicon content than M19, M36 exhibits lower core loss, making it an excellent choice for applications where minimizing energy loss is critical. This grade of silicon steel is common in the manufacture of motor laminations, electrical transformers, and other components where low core loss is important.
M45
M45 is a popular grade of silicon steel that is frequently used in electrical motors and generators. Its high silicon content provides enhanced magnetic properties, resulting in increased efficiency and performance.
M47
M47 is a specialized grade of silicon steel that is highly resistant to magnetic aging, making it an exceptional choice for use in high-voltage transformers and reactors. Its high magnetic permeability and low core loss make it ideal for demanding electrical applications where reliability and durability are crucial.
M530-50A
M530-50A is a highly specialized grade of silicon steel that exhibits superior strength and magnetic properties, making it well-suited for use in demanding aerospace and defense applications. Its exceptional magnetic properties allow for efficient energy transfer and precise control, while its strength and durability ensure reliable performance even in extreme environments.
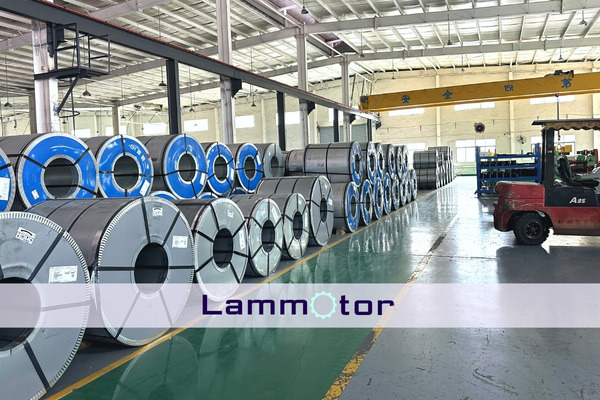
The grain orientation, thickness, and coating also affect the performance of silicon steel. Grain-oriented silicon steel has better magnetic properties than non-oriented silicon steel, but it is more expensive.
Thicker steel sheets result in lower core losses, but they make the lamination stack thicker and increase the weight of the motor. Coatings such as oxide and phosphate can improve the durability and resistance of silicon steel to corrosion.
In addition to silicon steel, there are other materials for motor laminations, such as nickel alloy and cobalt alloys.
Comparison of Common Motor Lamination Steel Grades
To better understand the common differences between the different grades of silicon steel, it is essential to compare them side by side. The table below shows a comparison of the properties of M19, M27, and M36 silicon steel.
Property | M19 | M27 | M36 |
Magnetic Permeability | High | Higher | Highest |
Core Loss | Low | Lower | Lowest |
Magnetic Flux Density | Medium | High | Very High |
Grain Orientation | Non-oriented | Oriented | Oriented |
Thickness | Thin (0.014″) | Thin (0.014″) | Thin (0.014″) |
Coating | Oxide or phosphate | Phosphate or oxide | Phosphate or oxide |
As shown in the table above, each grade of silicon steel has its advantages and disadvantages.
M19 is the most commonly used grade of silicon steel for motor laminations due to its low cost and suitability for low- and medium-frequency motors.
M27 and M36 are more expensive but are ideal for high- and very high-frequency motors.
Factors to Consider When Selecting Silicon Steel Grade For Your Motor Lamination Projects
When selecting the right electrical steel grade for your stator and rotor lamination project, there are several factors that you need to consider. These include:
Operating frequency
The operating frequency of the motor determines the type of silicon steel that is suitable for the project. Low-frequency motors require M19, while high-frequency motors need M27 or M36.
Core loss requirements
Different applications have varying core loss requirements. Motors with higher efficiency ratings require silicon steel with low core losses.
Magnetic flux density
The magnetic flux density is the amount of magnetic field passing through a unit area of a material. Motors with high magnetic flux density require silicon steel with high magnetic permeability.
Manufacturing processes and cost
The manufacturing process used to produce the laminations can affect the choice of silicon steel grade. The cost of the steel also needs to be factored in when selecting the right grade.
Examples of Silicon Steel Use in Different Motors
Silicon steel is used in a variety of motors, including AC, DC, universal, and stepper motors. The table below shows some examples of the type of silicon steel used in different motors.
Motor Type | Silicon Steel Grade |
AC Motor | M19 |
Brushless DC Motor | M27 or M36 |
Universal Motor | M19 or M27 |
Stepper Motor | M19 or M27 |
Our Electrical Steel Laminations Manufacturing Capabilities
We are well-equipped to handle the manufacturing and production of electrical steel laminations. We have strong capabilities in stamping, laser cutting, wire EDM, and assembly.
With our stamping equipment, we can create precise shapes and sizes for our laminations with ease. Our laser cutting and wire EDM technology allows us to cut and shape laminations with extreme accuracy and speed for prototyping laminations.
If you need to choose a professional and reliable China manufacturer of motor lamination stacks, we are the best choice.
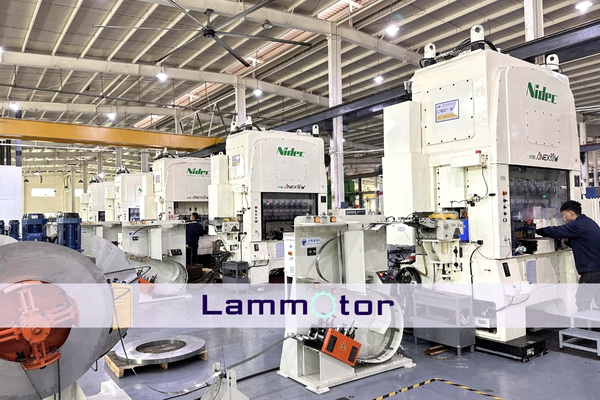
Conclusion
In conclusion, selecting the right grade of silicon steel for your motor lamination steel project is crucial for producing efficient and high-quality motors.
The operating frequency, core loss requirements, magnetic flux density, manufacturing processes, and cost must be considered when selecting the right grade of silicon steel.
By comparing the properties of different grades of silicon steel, such as M19, M27, and M36, you can choose the one that best fits your project’s needs.
Remember that the grade of silicon steel used for motor laminations can affect the motor’s efficiency, durability, and cost.
By making an informed decision about which grade to use, you can ensure that your motor performs optimally and meets your project’s requirements.
If you want to start your electrical steel lamination project, contact us now!
FAQs
What Are The Properties Of Silicon Steel?
Silicon steel, also known as electrical steel, is a ferromagnetic metal alloy that is widely used in electrical applications due to its unique properties. Some of the key properties of silicon steel include:
High magnetic permeability, which allows it to efficiently store and transfer magnetic energy.
Low core losses, which reduces energy consumption and improves efficiency.
Low coercivity, which means it can be magnetized with relatively low magnetic fields.
Good saturation induction, which means it can reach high levels of magnetization without losing its magnetic properties.
High resistivity, which helps to minimize eddy current losses when exposed to alternating magnetic fields.
Good thermal stability, which allows it to maintain its magnetic properties over a wide range of temperatures.
These properties make silicon steel an ideal material for use in electrical transformers, motors, generators, and other devices where efficient energy transfer is critical.
What is non-grain-oriented electrical steel?
Non grain oriented electrical steel, also known as NGOES or simply non-oriented steel, is a type of silicon steel that is specially designed for use in electrical applications.
Unlike grain-oriented electrical steel (GOES), which is manufactured with a specific crystallographic orientation to optimize magnetic properties along one direction, NGOES has no discernible grain orientation.
This means that its magnetic properties are isotropic, or the same in all directions, making it ideal for use in rotating machineries like electric motors and generators.
NGOES is typically made from low-carbon steel that is coated with a thin layer of insulating material to reduce eddy current losses, resulting in high efficiency and reduced energy consumption.
And the other grades of electrical steel include fully processed grades, semi-processed grades, and grain oriented electrical steel.