Ever wondered why your kitchen blender or washing machine runs so efficiently and quietly? The answer lies in the heart of their motors—the stator core. Specifically, the straight strip stator core is revolutionizing home appliances by boosting performance and energy efficiency.
In this post, we’ll dive deep into the straight strip stator core technology, unpacking its benefits and the innovative manufacturing processes behind it.
By the end, you’ll understand why this technology is critical for modern appliances and how it’s setting new standards in motor efficiency. Ready to see what makes your home appliances tick?
What Is A Straight Strip Type Stator Core?
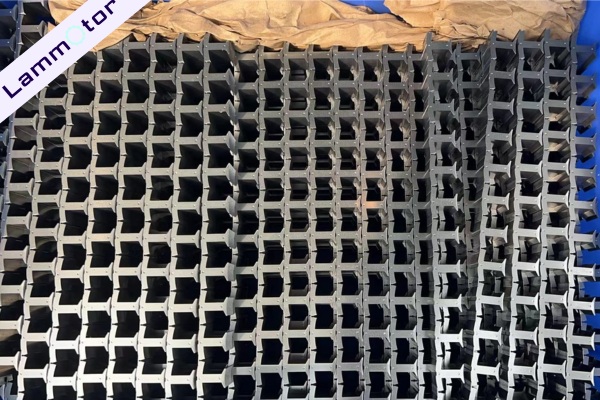
The stator is used for a BLDC motor or home appliances electric machine.
It is comprised of electrical steel laminations, which are initially flat and straight strip in form.
To that end, strip-shaped stamping mold provided with grooves are disposed of so that they form a straight strip.
All of the grooves of the electrical steel laminations are oriented in the same direction, thus lending this stator core the appearance of a comb. This intrinsically flat stator core. But in a subsequent step, this core is rolled into a round shape, yielding final a laminated stator core. It can be used in the same way as conventional annular laminated stator cores.
Manufacturing And Rolling Of Straight Strip Stator Cores
The manufacturing process of straight strip stator cores represents a significant advancement in motor design, particularly for its efficiency and precision. Here’s a closer look at each step:
Design and Manufacture of Stamping Mold: The process begins with the meticulous design and manufacture of a linear straight strip stamping mold. This mold is crucial as it shapes the metal into precise straight strips that form the stator core.
High-Speed Stamping: Once the mold is ready, the electrical steel strips are stamped at high speeds. This step is vital for shaping the straight strips before they are wound into stators.
Quality Control: Post-stamping, each punched stator core is rigorously checked. Any pieces that don’t meet the stringent quality standards are excluded from the batch to ensure that only the best components are used.
Winding: The qualified strips are then fed into an automatic stator winding machine. This machine precisely winds the wires around the straight strips, which is a critical step for the functionality of the stator.
Forming and Welding: After winding, the straight strip is carefully placed on a special rolling machine, which rolls it from a straight strip into a circular stator core. The ends of the strip are then welded together to maintain the core’s shape and integrity.
This streamlined process not only enhances production efficiency but also significantly improves the performance and reliability of the stator cores used in home appliances.
What Is The Benefit Of Linear Straight Strip-Type Motor Stator Stacks?
The primary benefit of using linear straight strip type motor stator stacks is the significant material savings they offer. By utilizing a continuous strip of silicon steel, these stator stacks minimize waste produced during the manufacturing process.
This not only reduces material costs but also enhances the overall sustainability of motor production. Consequently, manufacturers can achieve more efficient use of resources while maintaining high-quality and performance standards in motor design.
Conclusion
We’ve journeyed through the innovative world of straight-strip stator cores, exploring their superior efficiency and robust performance in home appliances. By understanding the manufacturing process, it’s clear about straight strip stator stacks.
Interested in optimizing your appliances with the latest in stator technology? Contact us today to discuss how our custom linear straight strip type stator lamination stacks can revolutionize your products. Let’s power a more efficient future together!