Rotor Laminations Manufacturer in China
As a rotor laminations China manufacturer, we specialize in providing various types of rotor lamination stacks for various motors. We support your stator and rotor assembly needs from prototype to volume production. Our commitment to excellence and dedication to quality means we use only the best materials and manufacturing processes to create superior products.
We have the knowledge and expertise needed to produce rotor laminations that meet your exact specifications, ensuring optimal performance and efficiency for your motor.
Whether you need stamping and laser cutting rotor laminations, we can deliver high-quality products that exceed your expectations. Trust us to be your reliable partner in meeting your stator and rotor lamination needs.
Rotor Core Laminations Stamping
Stamping rotor laminations is a crucial process in the manufacturing of electric motors, generators, and transformers. A rotor lamination is made up of thin metal sheets that are stamped with specific shapes and patterns to form the rotor core.
We provide three different stamping methods for rotor laminations: progressive, compound, and rotary notching. And our lamination thickness is generally from 0.1 to 0.5mm.
Additionally, we can design and manufacture stamping dies according to your specific requirements, ensuring a high-quality end product.
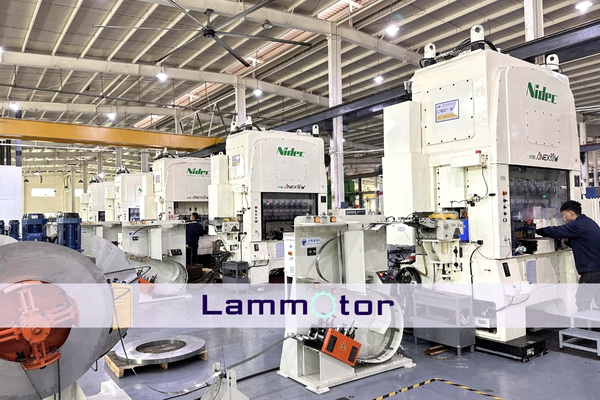
Laser Cutting rotor Laminations
We provide laser-cutting rotor lamination services. Laser cutting is a technology in the manufacturing of motor rotor laminations, especially in prototyping.
The laser cutting process involves the use of high-powered lasers to cut and shape silicon steel sheets into specific patterns with high precision and accuracy.
It also produces clean cuts with high-edge quality, reducing the need for additional finishing processes.
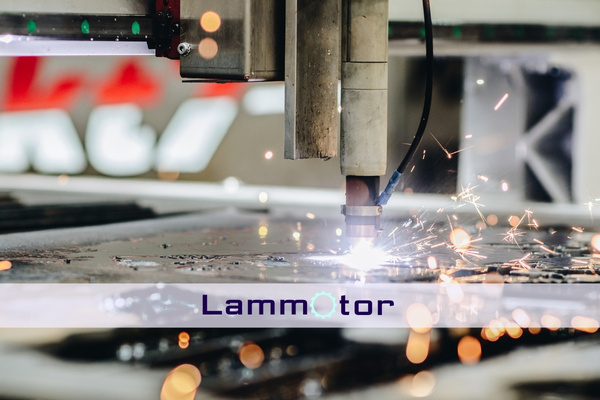
Materials Used in Rotor Lamination Stacks
The most commonly used materials for rotor laminations are silicon steel, nickel-iron alloys, and cobalt-iron alloys. These materials are chosen because they have low magnetic losses and exhibit good mechanical properties.
Silicon Steel
Electrical steel is the most common material used for rotor laminations. It has excellent magnetic properties and low core losses. Silicon steel comes in different grades, including M19, M27, and M36, depending on the required magnetic flux density.
Cobalt-based alloys
These alloys have high magnetic permeability, making them suitable for applications that require high frequencies. They also have good mechanical strength and resistance to corrosion.
Nickel-based alloys
Nickel alloys have high strength, heat resistance, and resistance to corrosion. They are often used in high-performance motors that operate under extreme conditions.
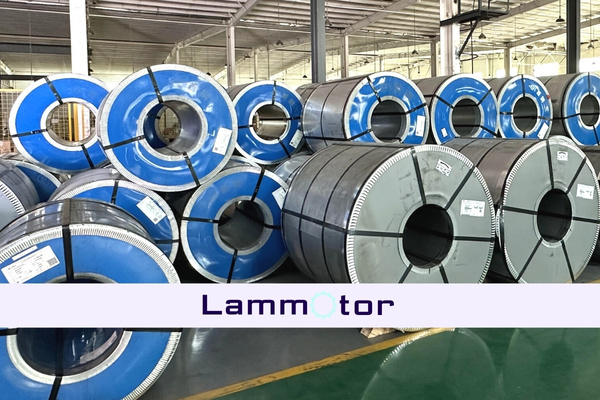
Customize Rotor Lamination Stacks For Various Motors
Rotor lamination stacks are a crucial component in various motors, including DC, AC, servo, and stepper motors.
As a China manufacturer specializing in electrical steel lamination manufacturing, we are capable of customizing rotor lamination stacks to meet the needs of various types of motors.

rotor laminations for DC motors
These motors use a rotor with slotted iron core laminations to reduce eddy current losses and increase efficiency.
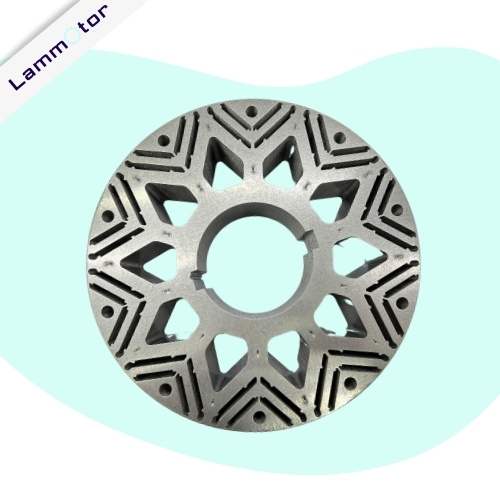
rotor stacks for BLDC motors
The laminations are typically made from thin sheets of silicon steel to minimize eddy current losses.
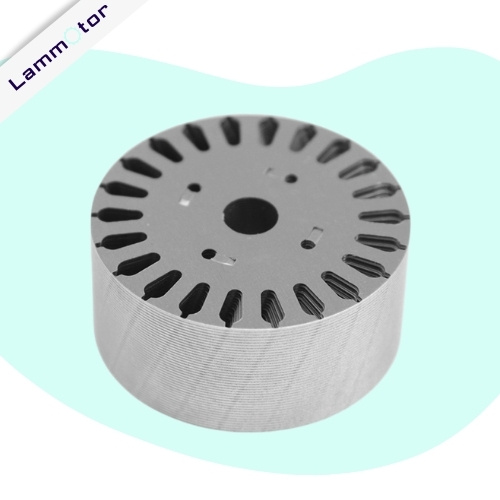
rotor laminations for induction motors
The rotor in these motor cores guides the magnetic flux and reduces eddy current losses.
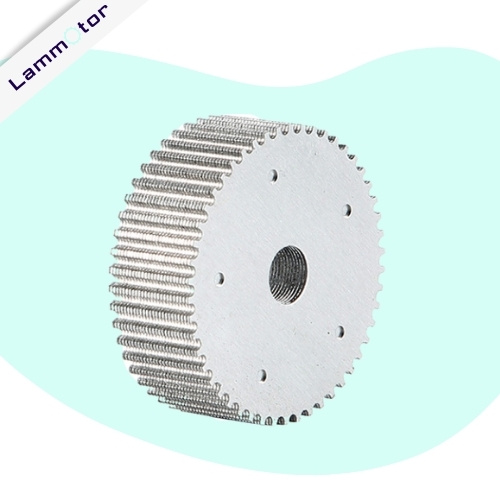
rotor for Stepper motors
The rotor is designed with high-quality laminations made from thin sheets of silicon steel to maximize efficiency and reduce heat generation.
Comprehensive Testing Services
quality control for Rotor laminations
Tight tolerance:
Motor rotor laminations must have precise dimensions to work correctly. Quality control checks should ensure that the dimensions are within the specified tolerances.
Visual inspection:
Each lamination stack should undergo a visual inspection to ensure there are no defects or damage that may affect its performance.
Die wear monitoring:
Manufacturing dies used to cut the laminations can wear over time, causing dimensional issues. Regular monitoring and replacement of the dies can reduce this risk.
OUR SERVICES
Why Choose Us as Your stator and rotor laminations China manufacturer?
We have the expertise needed to provide comprehensive solutions for any project, from design to production to delivery. And our customer support team is available to provide assistance and guidance throughout the entire process, ensuring a smooth and hassle-free experience for our clients.
High-Quality Products
We use top-quality silicon steel and advanced stamping processes to produce high-quality stator and rotor lamination stacks that meet or exceed industry standards.
Timely Delivery
We understand the importance of timely delivery, and we work diligently to ensure our products are delivered promptly and efficiently.
Customization Options
We offer a wide range of customization options to meet the specific needs of our customers, including size, shape, and material selection.
Motor rotor laminations FAQs
Rotor lamination stacks are used in a wide range of industrial applications, including:
A. Electric Motors: In electric motors, rotor laminations are used to create the magnetic field that drives the rotation of the rotor.
B. Generators: In generators, rotor stacks are used to create the magnetic field that induces a current in the stator windings.
C. Transformers: Rotor stacks are also used in transformers to create the magnetic field that transfers energy between the primary and secondary windings.
Rotor laminations are typically manufactured using a stamping or punching process, where a large sheet of metal is fed through a machine that cuts it into the required shape and size.
The laminations are then assembled into stacks and bonded together using adhesives or mechanical fasteners.
When selecting a reliable electric motor rotor lamination chain manufacturer, there are several factors to consider. Here is a list of important criteria to help guide the decision-making process:
Quality Assurance:
Look for a manufacturer that has a strong quality assurance program in place. This will ensure that the rotor laminations meet industry standards and have consistent performance.
Experience:
Choose a manufacturer with a proven track record of producing high-quality rotor laminations. An experienced manufacturer will be able to provide guidance on design and material selection based on their expertise.
Production Capacity:
Verify that the manufacturer has the production capacity to meet your needs. This includes the ability to produce large quantities of laminations while maintaining quality and meeting delivery deadlines.
Customer Service:
Ensure that the manufacturer provides excellent customer service, including timely delivery, responsive communication, and willingness to work with you to address any issues that may arise.
By considering these factors and conducting due diligence in researching potential manufacturers, you can select a reliable electric motor rotor lamination chain manufacturer that meets your needs and expectations.
Rotor lamination stacks are a critical component in the construction of electric motors and generators.
They are made up of thin layers of magnetic material, such as silicon steel or nickel alloy, that are stacked together to form a core.
The lamination stacks help to reduce energy losses due to eddy currents by isolating each layer from the others.
They also increase the efficiency of the motor or generator by providing a smooth path for the magnetic field to travel through.
Rotor lamination stacks come in various shapes and sizes depending on the type of motor or generator they are designed for.
Rotor lamination stacking methods typically involve bonding, welding, or interlocking the layers of magnetic material together.
Bonding involves using an adhesive to bond the layers together, while welding uses heat to fuse the layers together.
Interlocking involves stamping each layer with protrusions and depressions that fit into each other, creating a sturdy mechanical bond.
The method chosen depends on the specific application and the desired characteristics of the motor or generator.
Get High-Quality Rotor Laminations in China From Us!
Rotor laminations are a key component of electric motors, generators, and transformers, among other industrial applications. As a professional motor laminations China manufacturer, we can produce types of lamination stacks for various motors. Contact us for customizing motor laminations.