Axial Flux Stator Laminations Stacks Manufacturer in China
Axial flux motors are extremely high-efficiency motors. As a leading manufacturer in China, our company excels in crafting custom axial flux stator laminations with precision. In addition, we can produce customized high-speed and high-efficiency motors. Whether you need a large motor, a small motor, or segmented stator laminations, we can meet you.
We can custom stamp dies, enabling the production of high-quality Disc motor cores tailored to your specifications. Additionally, we offer comprehensive stator winding services. The versatility of our manufacturing processes positions us as a reliable partner for meeting your unique requirements.
Customize Axial Flux Stator Lamination Stacks
Axial flux stator laminations play a pivotal role in the functionality of electric motors, serving as essential components that significantly impact their performance. Unlike traditional radial flux designs, Disc motor stators feature a distinctive arrangement where the magnetic flux travels parallel to the rotor’s axis.
These laminations are typically composed of high-quality magnetic materials and are precisely crafted to optimize the motor’s efficiency. Their unique design allows for a more compact and lightweight motor construction, making them ideal for applications where space and weight considerations are crucial. We also can customize amorphous axial flux stators.
The applications of axial flux stator laminations span a wide range of electric motor systems, including but not limited to electric vehicles, renewable energy generators, industrial machinery, and robotics.
We can custom such stators for elevator traction Motors, direct drive appliance motors, EV motor applications, etc.
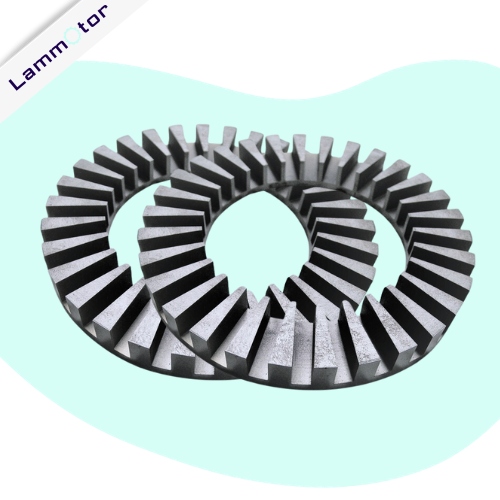
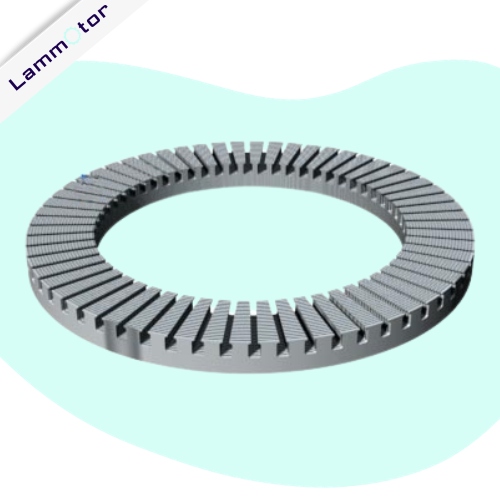
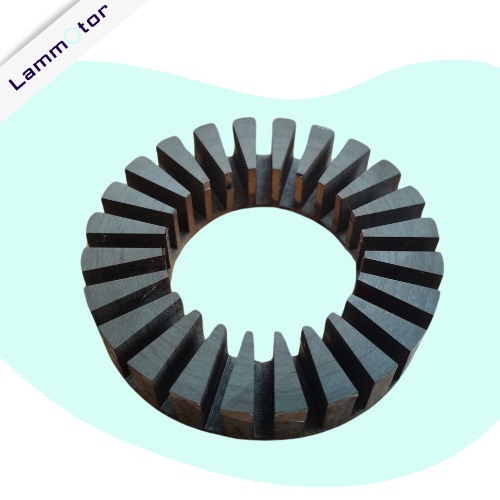
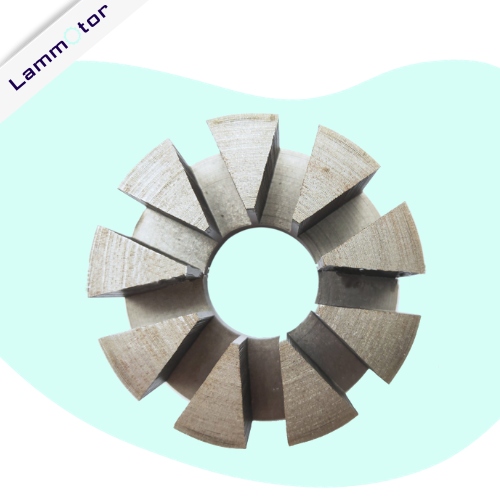
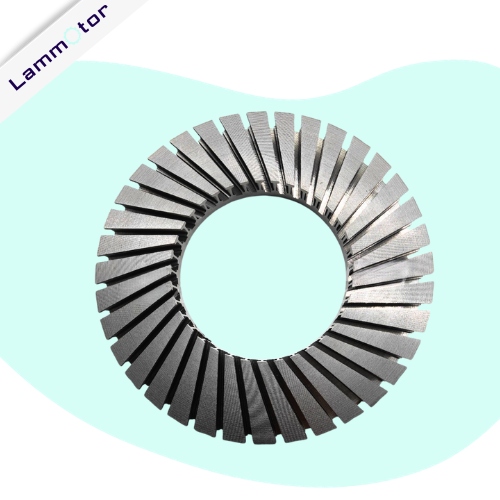
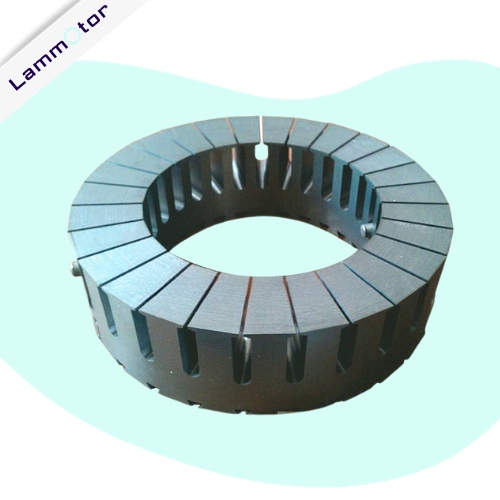
Materials of Axial Flux Motor Stators
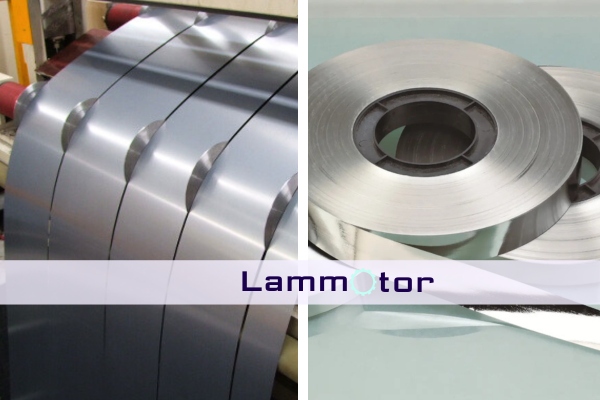
For axial flux motor stators, three primary materials are commonly employed: silicon steel sheet and amorphous alloys and soft magnetic material.
Silicon steel sheet, known for its excellent magnetic properties, is often utilized for its high permeability and low core loss, making it ideal for efficiently channeling magnetic flux within the stator.
But Amorphous alloy materials can completely replace silicon steel sheets. Amorphous materials can reduce motor core losses by 80%-93%. Its iron loss at high frequency is 1/8-1/10 of silicon steel sheet, which reduces the temperature rise of the motor and increases the efficiency by 3%-10%.
Soft magnetic materials exhibit high magnetic permeability and low coercivity, allowing them to rapidly magnetize and demagnetize in response to alternating currents. Through powder metallurgy processing, secondary operations can be largely eliminated, such as: punching, grinding, drilling, etc.
OUR SERVICES
Manufacturing Process Of Disk Stators
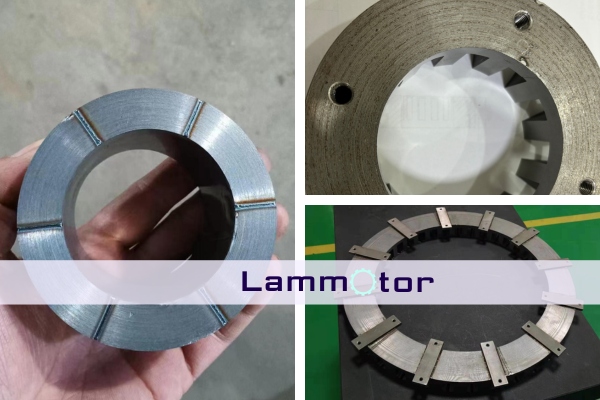
The disk stator is made with special stamping and winding equipment, the slot shape is stamped by a special stamping die. The servo synchronization control system is adopted to precisely control the frequency of stamping and the speed of winding to achieve consistent alignment of the product from the inner diameter to the outer diameter.
We have been researching and developing the production and process of disk motor stators for many years, and have a complete production line for disk motor stators. We provide a one-stop solution for stamping, winding, drilling, bonding, welding, annealing, and winding of coiled stators.
Axial Flux Stator Winding Process
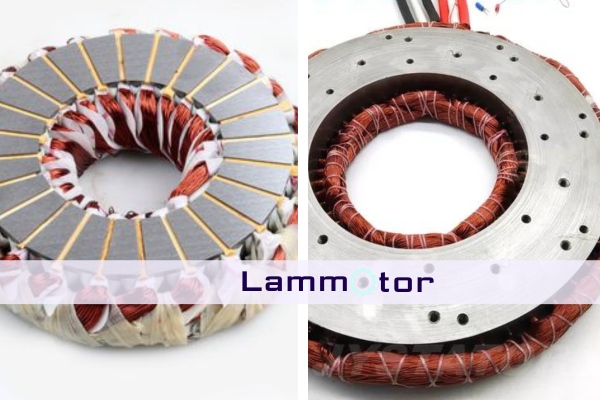
Axial flux stator winding involves the meticulous winding of coils in a direction parallel to the rotor axis. This unique configuration optimizes the magnetic flux path, enhancing power density and overall motor efficiency.
In the axial flux stator winding process, coils are precisely wound around the stator’s laminated core, ensuring a compact and efficient design. The winding arrangement facilitates a shorter magnetic path, reducing energy losses and improving the motor’s power-to-weight ratio.
This winding technique is particularly advantageous in applications where space and weight constraints are paramount, such as electric vehicles and aerospace systems.
As a leader in axial flux technology, Lammotor specializes in delivering high-quality stator winding solutions that elevate the performance of electric motors across diverse industries.
OUR SERVICES
Quality control for Axial Flux Stator Cores
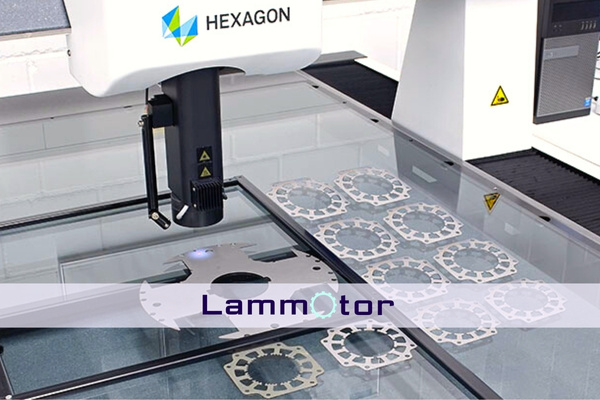
Quality control for Axial Flux Stator Cores is crucial to ensure optimal performance and reliability.
Firstly, dimensional accuracy is meticulously inspected to meet design specifications. Automated testing verifies winding integrity, ensuring proper insulation and alignment.
Magnetic properties, including core losses and permeability, are thoroughly assessed to guarantee efficiency. Electrical testing assesses winding resistance and insulation resistance. High-voltage tests ensure stator integrity under extreme conditions.
Strict adherence to these quality control measures ensures that Axial Flux Stator Cores meet the highest standards, promoting durability and efficiency in various applications.
FAQs
The axial flux motor stator core provides a magnetic pathway for the flux generated by the rotor, facilitating the conversion of electrical energy into mechanical motion. It supports the winding coils and influences the motor’s overall efficiency and performance.
Yes, axial flux motor stator cores can be tailored for various applications by adjusting factors such as the size, shape, and material composition. Customization allows for optimization to meet specific performance, efficiency, and space requirements in diverse industries.
The lamination process for axial flux motors differs significantly from traditional stator stacks. Unlike common stator punching machines used for traditional stators, producing axial flux stators requires specialized equipment for stamping and lamination.
In traditional stators, stamping tooling cuts single sheets and then laminates them in the axial direction using bonding, interlock, or welding methods.
In contrast, axial flux stators involve a stamping tooling that only shapes and sizes the slots, while a rolling machine system, synchronized by a PLC computer system, performs the lamination process.
This unique approach highlights the distinct manufacturing requirements for axial flux motor components.
Key performance factors include material quality, lamination thickness, and the precision of the manufacturing process. Additionally, proper alignment and insulation of the laminations impact the stator core’s efficiency and reliability.
Looking For An Axial Flux Motor Stator Lamination China Manufacturer?
Searching for a reliable axial flux motor stator lamination manufacturer in China? Look no further! Contact us today for cutting-edge solutions and premium-quality stator laminations tailored to your specifications.
With our expertise, advanced technology, and commitment to excellence, we ensure optimal performance and durability in every product.
Reach out to us now for a seamless experience and discover why we are your go-to Disc motor stator lamination China manufacturer. Your satisfaction is our priority!