compound stamping Lamination stacks for motor core in china
We are a custom electric motor lamination stacks China manufacturer and provide our customers with motor core lamination compound stamping services. Our compound stamping process enables us to produce precision components with high accuracy, repeatability, and reliability.
Our compound stamping services are beneficial for both high-volume and low-volume production runs. They offer precision, accuracy, and repeatability that can help improve your product’s performance and quality. All our products come with a satisfaction guarantee, so you can rest assured that your project is in good hands!
stator and rotor compound stamping molds
We have a catalog of hundreds of molds for the production of motor lamination. We also design and manufacture proprietary stamping dies for specific customer requirements.
Meanwhile, we have advanced slow-moving wire-cutting equipment to manufacture motor lamination compound stamping dies. We provide our customers with various benefits, including better precision and accuracy, higher speed production, improved reliability and durability, and reduced costs.
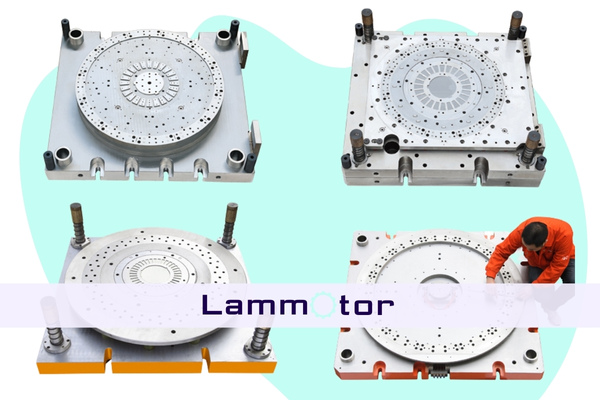
Our compound Stamping Capabilities For Motor lamination stacks
We are proud to have strong motor core lamination stamping capabilities. Our advanced stamping technology allows us to produce high-accuracy, precision lamination stacks in various motor applications.
Composite stamping is suitable for medium motor laminating. Therefore, the mold size is relatively large, and the entire mold is fixed between the piston and the press base. The disc is instantly stamped into a stack, and the whole process of feeding and unloading can be operated by an automated system or manually. It runs much faster than rotary slotting.
We offer a wide range of stator and rotor lamination stacks sizes. Our stamping process utilizes advanced technologies to ensure a consistent product. This ensures that each part is precise and uniform in size, shape, and thickness.
In addition to our compound stamping capabilities, we also offer annealing, grinding, assembly, and progressive stamping services to ensure that we can provide a complete motor lamination stack manufacturing solution.
After compositing the laminated sheets, we stack them in the die by gluing, welding, and riveting to form the core components.
In conclusion, we offer custom designs to fit your application requirements. Whether you need a prototype lamination or high-volume production, we can help you design the perfect stamping tooling for your needs.
materials used in stator and rotor lamination
We have years of experience providing our customers with the best materials for this type of stamping. Our selection includes a variety of options to accommodate different requirements when it comes to motor lamination stack compound stamping.
Silicon steel is a common material used for motor core lamination compound stamping. These steel alloys are usually made from iron and steel and are corrosion-resistant and magnetic, which makes them suitable for this task.
We also provide other materials for stator and rotor lamination, such as:
Silicon steel
Nickel alloys
Cobalt alloys
Thin-gauge electrical steel
Grain Oriented steel
Non-Grain Oriented Steel
Cold Rolled Motor Lamination Steel
Comprehensive Testing Services
quality control
We have a strict inspection process to ensure the quality of motor lamination stacks.
First, we use quality materials when manufacturing their motor laminations, which will help guarantee that they remain effective and reliable over time.
Second, we accurately measure and monitor each part of the process.
This means taking precise measurements before, during, and after lamination to ensure that all components have been cut properly and adhere to set specifications.
Our testing equipment includes the projector, CMMs, a tension meter, a vernier caliper, and so on.
Finally, we also inspect their completed motors thoroughly before shipping them out.
A series of stator & rotor lamination stacks we customized
Compound stamping motor core products provide the necessary structural support for electric motors, making them ideal for various automotive, aerospace, and electrical equipment applications. We can customize a series of electric motor laminations for the industrial component.
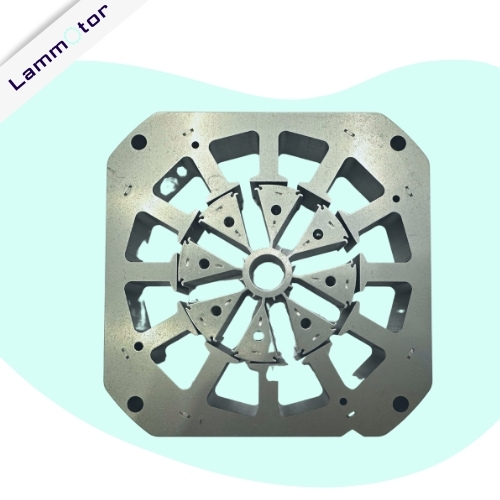
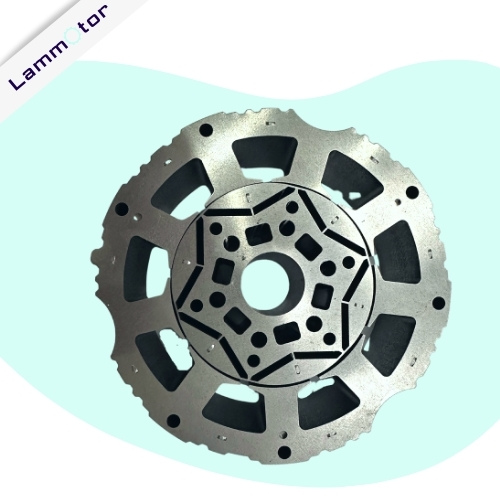
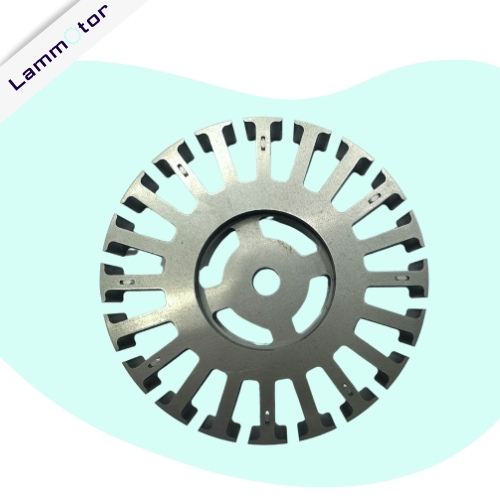
Secondary Operations
stacking
We can stack the laminations into a motor core in various ways, such as rivet, glue, and welding. Stacking them correctly ensures that the motor core won’t fail during operation. When the stator stack length is too large, interlocking and welding can be used simultaneously. The method used to stack the laminations must be chosen based on factors like power requirements and availability of materials.
rivet
Riveting is one way of stacking laminations for a motor core. This technique involves using small metal pins to hold the parts together, which makes it a reliable option for applications with high power demands.
glue
Glue is also an effective way of stacking lamination for smaller motors because it provides good adhesion between parts and creates an airtight seal between them.
welding
It combines multiple silicon steel laminations with welds to form components used in electrical motors, generators, and alternators. There are two types of welding stacking used for stator laminations: laser welding and TIG welding.
OUR SERVICES
why choose us for motor lamination stacks?
We can provide custom solutions for any lamination stacks needs. Besides standard motor stator and rotor lamination stack, we can also produce customized laminations.
Tight Tolerances
Our compound stamping services provide tight tolerances of +/- 0.001″ to ensure precise lamination for motor cores. We use cutting-edge equipment and an experienced team to produce high volumes with fast turnaround times.
strong stamping capabilities
Our compound stamping services for motor lamination offer high levels of accuracy and repeatability. From custom designs to cost-effective production, our stamping capabilities are perfect for large-scale production runs and small custom orders.
years of experience
Our experienced team has extensive experience in the motor core lamination industry and can provide advice on design and materials selection. We offer a wide range of customization options to meet your specific needs.
quality inspection
We use a rigorous quality inspection process to ensure that our products meet the highest standard. Our experienced staff uses advanced technologies to ensure precision stamping and accurate measurements.
Motor lamination compound stamping FAQs
Motor lamination compound stamping is a process used to manufacture electric motors.
It involves using a die and punch to press, cut, and form laminations from cold-rolled steel, which are then stacked to form an electric motor’s stator or rotor core.
The thickness of stator compound stamping typically ranges from 0.5mm to 1mm, depending on the specific application and requirements of the motor core lamination.
This thickness is important as it ensures that the motor core is insulated and protected from electrical damage.
If you’re unsure which thickness is ideal for your motor lamination project, then it’s best to consult us. We can advise you on the right thickness for maximum safety and performance.
Creating these cores can range from simple single-stamping operations to complex compound die systems with multiple stages and operations.
To begin this process, flat steel strips are fed into one end of the machine, punched, and formed into individual laminations with teeth on two sides.
Once this step has been completed, the punched parts can be either stamped again on both sides or combined with other components, such as bearings or shafts, before being pressed together in a stack to create an assembled stator or rotor core.
Motor lamination compound stamping is an efficient and cost-effective production method for motor cores.
Compared to traditional lamination techniques, this process helps reduce the risk of surface defects, such as scratches.
It also results in lamination stacks that are more precise and consistent, which helps to improve the overall performance of the motors.
Need to compound stamp electric motor lamination?
Our rotor and stator steel stamping services are some of today’s most precise and durable options in the electrical steel industry. In addition, we offer an array of electrical steel materials, including silicon steel, nickel alloys, cobalt alloys, and thin-gauge electrical steel. Contact us today if you’d like to learn more about our rotor and stator steel stamping services or any other electrical steel solution.