Progressive die stamping stands as a pivotal process in the realm of metal forming, revolutionizing the way industries create intricate components. This technique, deeply rooted in high-volume production, has been the cornerstone for numerous sectors, ensuring precision and efficiency in every piece crafted.
The purpose of this post is to delve deep into the intricacies of this method, shedding light on its significance and the myriad benefits it brings to the table.
As we navigate through the world of Progressive Die Stamping, we’ll uncover its processes, advantages, and the industries it has profoundly impacted. Join us on this enlightening journey, and discover the transformative power of this metal-forming marvel.
What is Progressive Die Stamping?
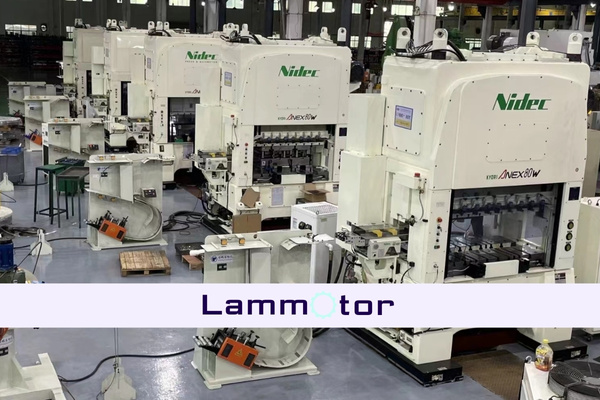
Progressive stamping is a sophisticated metal stamping technique that intricately shapes and crafts metal parts in a sequential manner. At its core, it involves a series of specific stations, each designated for a particular task, ensuring that every piece undergoes a meticulous transformation from a raw metal strip to a refined component.
Predominantly favored for higher-volume production, this method stands out for its ability to churn out large quantities without compromising on precision or quality. The versatility of Progressive Die Stamping is further highlighted by the diverse range of metals it accommodates, including brass, steel, stainless steel, aluminum, and copper.
This adaptability, combined with its efficiency, makes it an indispensable tool in the manufacturing landscape, catering to the ever-evolving demands of various industries.
What’s The Progressive Die Stamping Process?
Stock Strip Layout and Design:
The journey begins with the meticulous design of the stock strip. Manufacturers harness advanced modeling techniques to craft the progressive stamping die, ensuring every bend, punch, and hole is strategically placed on the strip for optimal results.
Tool Steel and Die Set Machining:
Craftsmen then sculpt die blocks from robust tool steel, adhering to precise specifications. This step ensures consistent part repeatability, with each die block undergoing rigorous quality control checks before advancing to production.
Grinding and Heat Treating:
To enhance the durability and stability of parts, they undergo heat treatments, elevating them beyond the alloy’s critical transformation temperature. Post this, grinding refines parts that demand higher dimensional accuracy.
Wire EDM:
An electrically charged brass wire is employed in this phase, shaping the die blocks through controlled metal sparking. This process facilitates the crafting of intricate angles and shapes, adding depth to the design.
Die Assembly:
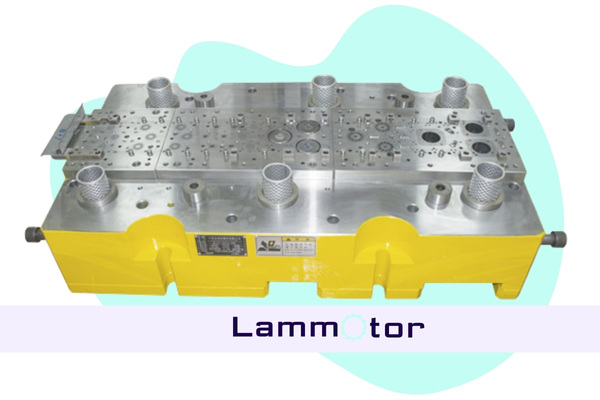
Once all preparatory steps are complete, a die maker meticulously assembles the die. Using precision instruments, they ensure it aligns perfectly with the original design specifications. Once created, the die must be placed into the stamping press. The die opens as the stamping press moves up, and it closes as the stamping press moves down.
Stamping Parts:
The culmination of the process sees the finished die set up in a stamping press. As the metal strip journeys through the die, each station sequentially cuts, punches, and bends it, manifesting the intended design. The die can change the workpiece in various ways, such as embossing, coining, bending, cutting, and more. Once the die closes, it carries out its operation on the workpiece.
Packaging and Shipping:
After the production process, the finished parts are detached from the feed line and ready for further processing or assembly. Once quality checks are completed, these parts are packaged meticulously and dispatched to their destined locations.
Benefits of Progressive Die Stamping
Increased Production Speed:
Progressive die metal stamping accelerates production, leveraging a continuous feed mechanism, enabling industries to produce large parts in a shorter timeframe.
Faster Setup:
Compared to traditional fabrication methods, this technique drastically reduces setup time, streamlining the entire production process for efficiency.
Reduction of Scrap Metal:
With precise manipulation techniques like coining and bending, the method maximizes material use, leading to minimal wastage and reduced scrap.
Increased Repeatability:
The use of hard tooling ensures consistent quality across high-volume runs, guaranteeing uniformity in every product crafted.
Varied Geometries for Parts:
One of its standout features is the ability to produce parts with multiple geometries in a single cycle, showcasing its versatility.
Lower Cost:
By optimizing material use, reducing setup time, and ensuring high-speed production, Progressive Die Stamping significantly lowers the cost per part, offering economic advantages.
Additional Benefits:
Beyond the aforementioned perks, this method boasts higher press tonnage rates, reduced material handling, and the capability to maintain consistently close tolerances, further enhancing its appeal in the manufacturing sector.
Progressive Die Stamping vs. Compound Stamping
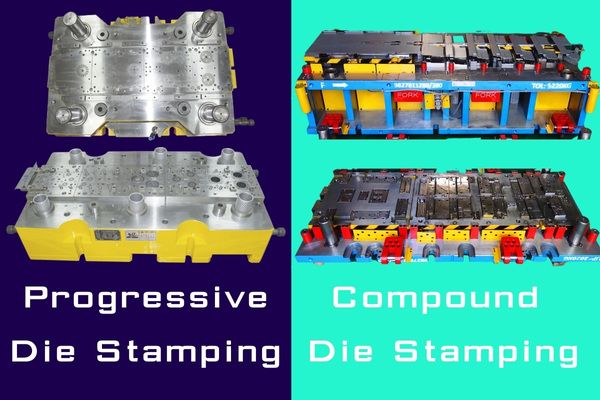
Progressive and compound stamping are both pivotal in the metal-forming domain, but they serve distinct purposes.
The progressive stamping involves a series of operations—like bending, coining, and cutting—performed sequentially on a sheet metal strip as it moves through various stations in a single die. It’s ideal for high-volume productions, ensuring continuous transformation of the metal.
On the other hand, compound stamping performs multiple operations in one stroke, using a single, complex die. It’s best suited for parts requiring precise specifications and is often used for simpler, larger parts. While both methods have their merits, the choice hinges on the complexity, volume, and precision required for the end product.
Industries Benefiting from Progressive Die Stamping
Progressive Die Stamping’s versatility and precision have made it a sought-after technique across a range of industries.
The electronics sector relies on it for crafting intricate components that form the backbone of devices we use daily.
In the automotive industry, parts like brake calipers and motor cores are produced using this method, ensuring vehicles run smoothly and efficiently.
The aerospace industry benefits from the high precision and repeatability of Progressive Die Stamping, crafting components that can withstand extreme conditions.
Household appliances, from toasters to washing machines, contain stamped parts ensuring their functionality.
Even industries like mining, food and beverage, healthcare, and retail harness its capabilities for various equipment and tools.
A notable example is the pull tab lids on beverage cans, a ubiquitous item made possible through this innovative process. The breadth of its applications underscores Progressive Die Stamping’s pivotal role in modern manufacturing.
FAQs
What metals are commonly used in progressive die stamping?
Progressive Die Stamping predominantly employs metals like brass, steel, stainless steel, aluminum, and copper, chosen for their durability and adaptability to the intricate stamping process.
How Are Parts Made Using Progressive Die Stamping?
Progressive die stamping is a forming process used to produce parts in high volumes quickly and accurately. The process involves feeding a metal strip through a series of stations, each with a specific operation, such as cutting, bending, or shaping.
As the strip progresses through the die, each station performs its operation on the metal, gradually forming the final part. This method ensures cost-effective production and consistent quality, making it ideal for industries requiring large volumes of parts.
How does progressive die stamping differ from other stamping methods?
Unlike traditional stamping, progressive stamping operates through a series of stations, each performing a specific task. This sequential approach ensures high precision and efficiency, especially suited for high-volume production runs.
What are the main steps involved in the progressive die-stamping process?
The process encompasses stock strip design, tool steel machining, grinding, heat treating, Wire EDM, die assembly, stamping of parts, and finally, packaging and shipping, ensuring a comprehensive transformation of raw metal to finished product.
Why is progressive die stamping considered cost-effective?
Its ability to produce high volumes with minimal wastage, combined with reduced setup times and optimized material use, makes progressive stamping a cost-efficient choice for manufacturers.
Conclusion
Progressive stamping stands as a testament to the evolution of manufacturing, bridging the gap between intricate design aspirations and tangible high-quality products. Its significance in today’s industrial landscape cannot be overstated, with its ability to cater to high-volume demands while ensuring unparalleled precision.
The myriad benefits, from accelerated production speeds to cost-effectiveness, make it an indispensable tool for industries far and wide. Whether it’s the automotive sector crafting motor cores or the electronics industry developing intricate components, Progressive Die Stamping remains at the heart of these operations.
As we reflect on its transformative impact, it’s evident that this method not only reshapes metals but also redefines the standards of manufacturing excellence. In an ever-evolving industrial world, Progressive Die Stamping emerges as a beacon of innovation, driving progress and perfection in tandem.