progressive stamping Lamination Stacks For Motor Core in china
We are a motor lamination China manufacturer and specialize in progressive stamping lamination stacks for motor core. Our state-of-the-art technology and engineering expertise enable us to provide our customers with exceptional quality and competitive prices. Our progressive stamping process utilizes precision tooling to produce motor cores that feature intricate shapes or high levels of detail in a short amount of time.
OUR SERVICES
why choose us for electric motor lamination stacks?
We can provide custom solutions for any motor lamination stamping needs. Besides standard motor stator and rotor lamination stack, we can also produce customized laminations.
high-quality materials
We use high-quality metal alloys for maximum durability and performance. This allows our clients to rely on a lamination solution that will perform consistently and last for years.
quality control
We employ a rigorous inspection process to ensure top quality. Our in-house quality team ensures high standards are met. We can accurately produce parts that meet customer specifications.
fast turnaround
We offer fast turnaround times and competitive pricing on our progressive stamping services. We strive to deliver excellent customer service every time, no matter the size of the order or job description.
Our Progressive Stamping Capabilities For Motor lamination Stacks
We specialize in producing a variety of electrical steel sheets for a variety of products and industries. And we have the expertise to work with customers and design and produce laminates to meet customer specifications.
We ensure every motor assembly is up to the highest standard before being sent out for use in different industrial applications.
At our China-based facility, we can quickly prototype motor lamination and turn around orders from design through completion, allowing you to get the cores you need faster than ever before. With years of experience in progressive stamping for motor core lamination stacks, we are your first choice as a trusted supplier.
In addition, we can produce laminates in the thickness range of 0.011 “to 0.060” with a typical flatness of 0.001 “per inch.
We stamp many lamination materials, such as silicon steel, cobalt, and nickel.
Our advanced quality control systems ensure that your motor lamination parts meet the highest quality and performance standards.
Progressive stamping die
Our stator and rotor progressive stamping die come in various shapes and sizes. They are often designed to match the specific shape or geometry of the stamped part, allowing for efficient and accurate manufacturing.
This die type is typically made of high-quality steel, with precision components like bearings and seals installed. This precision can handle high-pressure and temperature environments, making them an excellent choice for production quantities of parts. We can customize various stamping dies for motor lamination.
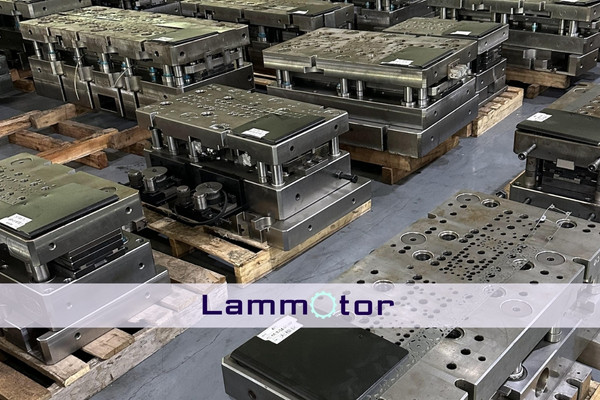
Materials used in stator and rotor lamination Stacks
We offer a wide range of lamination materials, including silicon steel, cobalt alloys, and nickel alloys. Each has unique properties, which can be used to create various lamination materials for various applications.
Silicon steel (electrical steel)
Silicon steel is most commonly used in motor core lamination progressive stamping services. It is an alloy of iron, silicon, and other elements that provides superior electrical properties for motors and generators.
Cobalt alloys
Cobalt alloy has excellent magnetic properties and can be formed into thin sheets, making it ideal for laminations. This makes it a popular choice for applications where high temperatures are a factor, such as in the automotive and aerospace industries.
Nickel alloys
Nickel alloy is a strong and durable material that can withstand high temperatures and electrical currents. It is an ideal choice for applications such as motors, transformers, and other electrical components.
Thin-Gauge Electrical Steel
Thin-Gauge Electrical Steel is ferrous material used in progressive stamping motor lamination. It is highly magnetic, making it an ideal material for electric motors.
Comprehensive Testing Services
quality control
We use high-precision tooling and progressive and compound stamping equipment to ensure precise stamping of the motor core.
And we have an accurate quality control system to monitor each production step, rigorous testing, visual inspection, dimensional checking, and advanced metrology systems for precise measurements.
We have a complete set of quality assurance protocols to ensure the product meets customer requirements.
This could include methods such as process mapping, standardization, and certification.
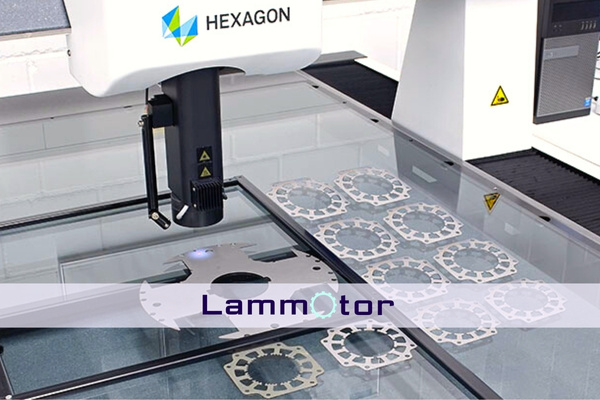
Motor lamination progressive stamping FAQs
Progressive stamping is a metal-forming process that uses dies and punches to form parts from flat metal sheets or coils. It is an automated, cost-effective way to produce high volumes of identical parts with consistent quality in a short amount of time.
Fire, this process produces high-quality parts with tight tolerances and minimal scrap.
Also, progressive stamping allows multiple operations, such as punching, bending, and forming, in one step.
Furthermore, progressive stamping provides consistent repeatability with low setup times, allowing quick and easy production cycles.
All in all, it can be an extremely beneficial tool for producing precision parts or components.
The process involves using progressive dies and presses that progressively shape, form, and cut steel coils to create precise shapes of laminations.
The first step in the motor lamination progressive stamping process is to uncoil steel strip materials from their spools. These strips are fed into a die set containing multiple stages or stations.
With each station, the material is shaped, formed into more complex pieces, and eventually cut out into individual parts.
During this process, an outer layer of insulation can be applied for greater protection against corrosion and other environmental damage.
Afterward, these parts are inspected for accuracy before being packaged together for shipment or further assembly operations.
Compound stamping and progressive stamping are metalworking processes used to create motor laminations, essential components in electrical motors.
Each process has its advantages and disadvantages, so it is important to understand their differences.
Progressive stamping combines several operations that involve a single continuous strip of metal. It begins with a blank part, then moves through punching and forming operations until the desired shape is achieved.
The advantage of this type of stamping is that all steps can be performed at once, resulting in a faster production cycle time.
However, this technique does not allow for complex shapes or multiple parts per cycle.
Compound die stamping uses two or more dies to form the shape of the motor lamination and requires two separate punches rather than one continuous operation.
Need progressive stamping for motor core lamination stacks?
Our progressive stamping ensures the production of top-quality motor laminations, stators, and rotors. The process begins with an accurate die design and analysis.
Look no further if you’re looking for a reliable, cost-effective motor lamination progressive stamping service. Our services come with a wide range of features, making it the perfect choice for your needs.