custom Lamination stacks for motor cores manufacturer in china
We are a professional custom motor lamination stacks manufacturer based in China. With decades of experience in the field, we are proud to be one of the leading suppliers of rotor stator lamination stacks products worldwide. We offer a comprehensive range of standard shapes and custom-designed solutions built to meet industry standards. And we can quickly prototype motor core lamination.
custom stator & rotor lamination stacks for motor
Customizing stator & rotor lamination stacks is essential for manufacturing electric motors. This process involves shaping and forming the lamination of the stator and rotor core to meet the motor’s desired specifications and performance requirements.
With our mold design and engineering expertise, we can produce high-quality custom electrical steel laminations tailored to your needs. We have a variety of stamping methods, progressive stamping, compound stamping, and single-slot stamping. We also provide prototyping services.
design and manufacture stamping molds
Our experienced engineers carefully design each die to give you a perfect fit for your specific motor core size or shape requirements. With our meticulous attention to detail, we guarantee that each die will provide consistent results for production efficiency and cost savings.
We use our expertise in die design to customize stamping dies for our customers’ specifications. Meanwhile, we are responsible for maintaining and repairing all production molds. Furthermore, we offer a fast turn-around time on our custom dies so your parts can be made quickly and efficiently.
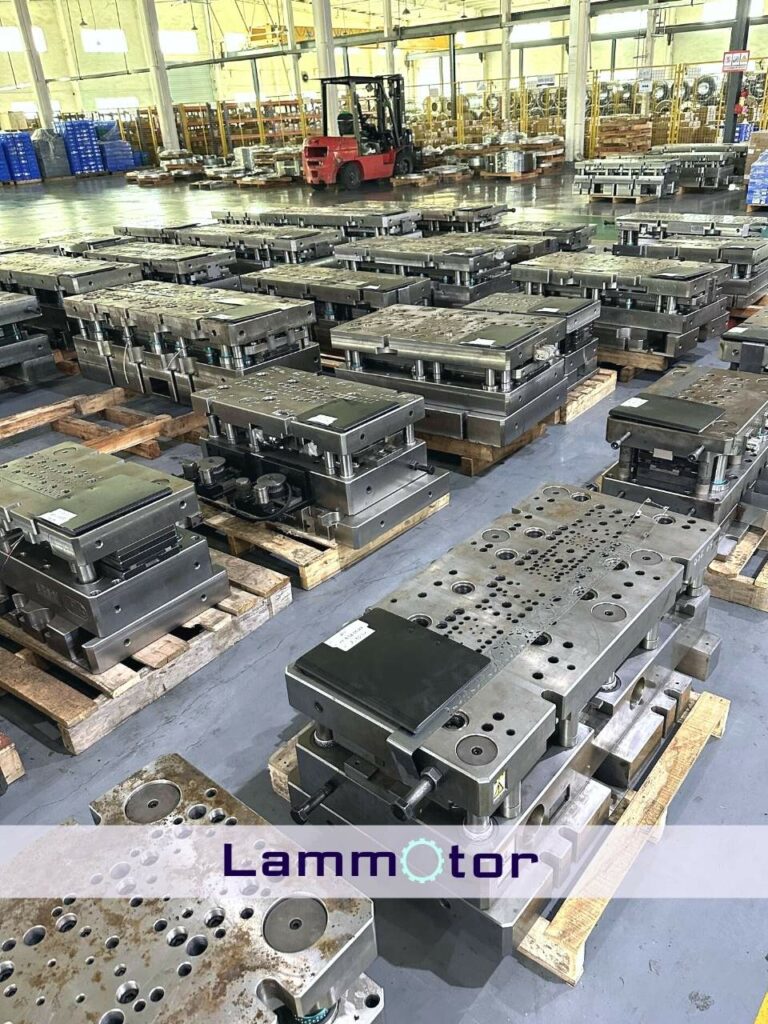
stamping capabilities for custom stator rotor lamination Stacks
As a professional motor lamination stacks manufacturer in China, we offer many lamination stack manufacturing capabilities to create highly efficient motor rotor stator core lamination products. Our advanced equipment includes modern presses with automated feeders and stackers and robotic welding systems capable of producing complex designs quickly and accurately.
Progressive stamping
Progressive stamping is an efficient, cost-effective manufacturing process for motor lamination stacks. This technique involves using a series of dies to form a specific shape from a flat sheet metal blank and helps to reduce the overall production costs.
The progressive stamping process is automated and precise, resulting in quick and accurate production with minimal waste. With this type of stamping, we can produce motor core lamination stacks quickly and efficiently with excellent uniformity, regardless of quantity or complexity.
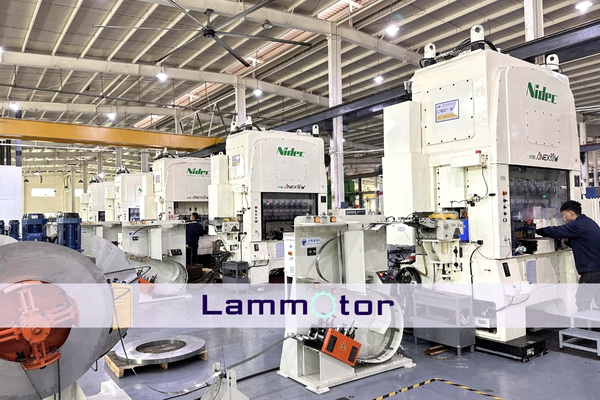
compound stamping
Compound stamping is an essential production process used to manufacture motor lamination stacks. The process involves the simultaneous cutting and forming of sheet metal, which is then pressed into a desired shape to create a finished product such as motor cores.
The compound stamping process begins with an upper die containing a punch or other tool that cuts the metal piece from its flat form into a specific shape. Then, this cut piece is placed between two dies that work together to bend or form it into its final shape.
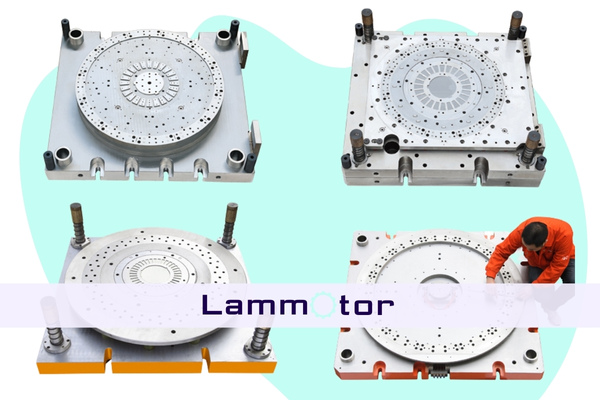
rotary notching
Rotary notching cuts notches on an electric motor’s primary and secondary lamination cores.
This method provides high-quality, consistent notches that enable better air circulation within the motor housing, creating a more efficient cooling system.
This technique is highly accurate and can be used for both small projects as well as large production runs.
prototyping lamination Stacks for motor cores
We provide support for the rapid prototyping of lamination stacks for motor cores. Our team has developed cutting-edge techniques to help customers get their projects off the ground quickly and efficiently. We use laser cutting and wire EDM to prototype motor lamination stacks. We can create customized cores for various types of motors to meet the specific needs of their customers. Our prototyping time is usually 5-10 days.
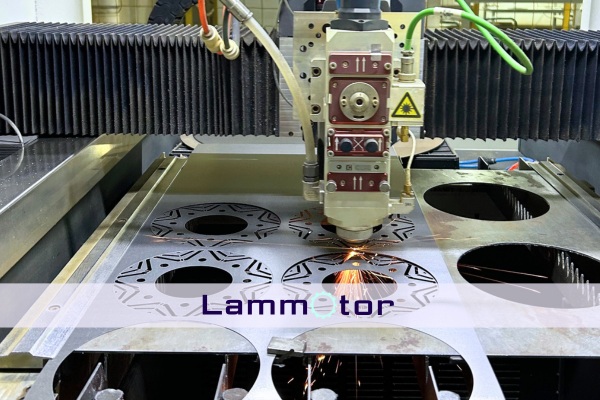
laser cutting lamination
Laser-cutting motor lamination is an advanced technology for rapid prototype motor lamination. This method of manufacturing motors allows for greater flexibility and accuracy in production. We can create precise shapes from a range of materials quickly and efficiently through laser cutting. Meanwhile, it produces small burr-free edges with no material loss.
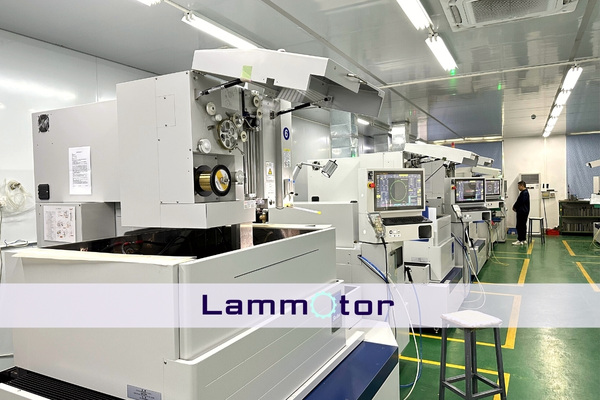
wire EDM lamination
Wire EDM cutting is a reliable and cost-effective method to produce motor lamination prototypes. This technology utilizes electrical discharge machining (EDM) to cut the laminates and weld them together in a permanent bond. Wire EDM lamination offers many advantages, such as high accuracy, repeatability, low cost, and minimal tool wear.
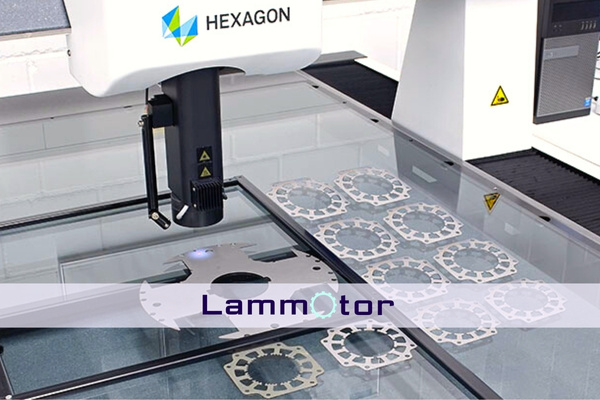
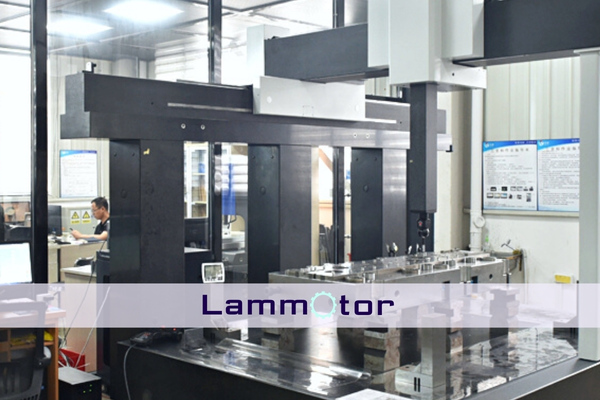
Comprehensive Testing Services
quality control for lamination stacks
When it comes to producing stator & rotor lamination stack, controlling lamination quality is key.
To start, each part must pass a visual inspection before it can be approved for production. Our manufacturing team inspects every component’s material composition and size to ensure they are up to par.
Secondly, we check electrical insulation strength between laminations before stacking them together with epoxy resin glue; this will guarantee no short circuits during operation.
Finally, we will inspect lamination stacks using CMM to ensure that the finished products meet exact tolerances for accuracy and durability. And our end-of-line testing ensures that all parts meet the required specifications before being shipped.
materials used in stator & rotor lamination stacks
An electric motor’s stator and rotor lamination stacks are made of thin metal sheets. These sheets can be welded, bonded, or stacked to form the lamination. For example, silicon steel is a popular material for stator and rotor lamination in electric motors.
Due to its excellent electrical conductivity, Silicon steel is used in electrical components such as generators, motors, and pulse transformers.
Silicon steel is alloyed with small quantities of silicon to reduce eddy current losses in the core.
Cobalt alloys are used in stator and rotor lamination as they provide improved resistance to wear, corrosion, and heat. They are commonly used in high-performance applications, where their high strength and rigidity are required.
In these applications, high-induction and low-loss iron-cobalt alloys are typically used for stator lamination. These alloys have a lower electrical conductivity than steel or aluminum, reducing losses caused by motor resistance.
Nickel alloys are suitable for motor lamination due to their high permeability at low to moderate inductions and low core losses. These alloys require a careful annealing cycle to be useful. They must be processed slowly and at a high temperature to ensure good permeability properties.
Thin-gauge electrical steel is widely used in stator and rotor lamination in traction motors due to its energy efficiency and high performance.
It is relatively economical, lightweight, and has good electrical and magnetic properties, making it ideal for stator and rotor laminations.
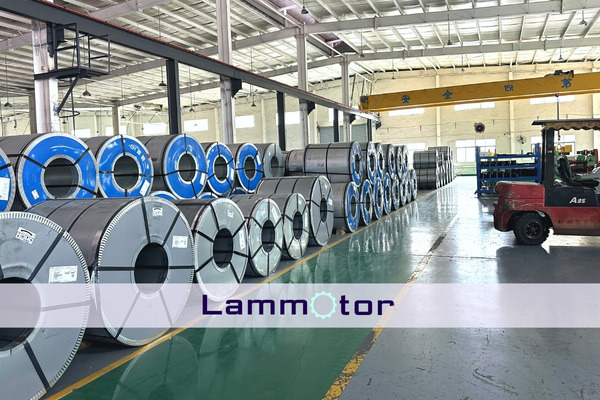
A series of motor lamination stacks we customized
We can customize various motor lamination stacks for many applications. We specialize in manufacturing lamination stacks for various applications, such as automotive new energy, industry, and refrigerator. Finding the right solution for your specific motor needs does not have to be a struggle.
We offer various shapes and sizes so you can find the perfect fit for your project needs. Whether you are looking for a small, lightweight core or a large heavy-duty one, we have just what you need. Furthermore, our expert engineering team will help you through all aspects of product selection, design, production, and testing to ensure the best possible results.
lamination stacks for new energy vehicles motor core
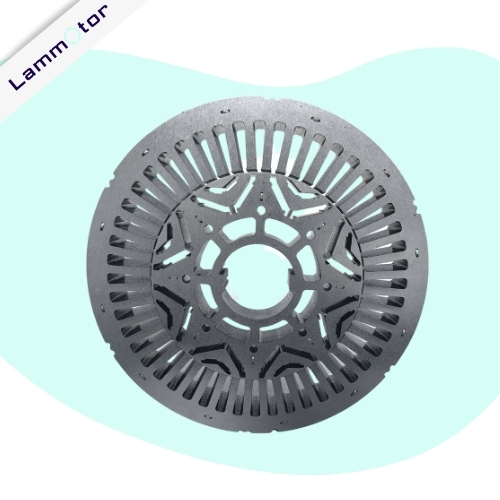
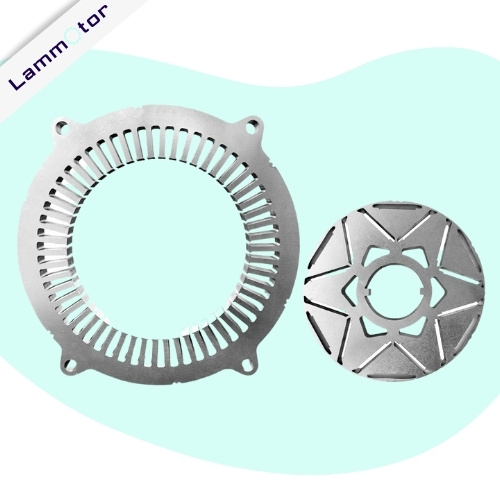
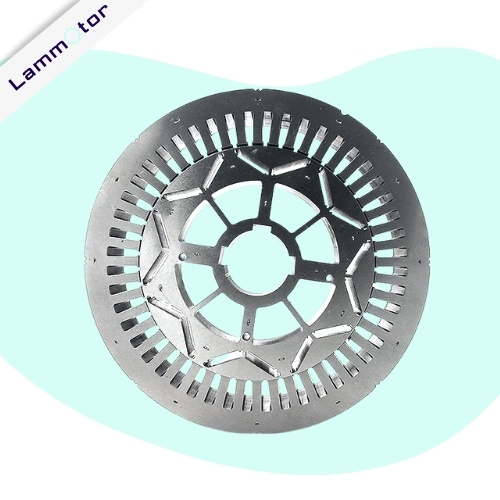
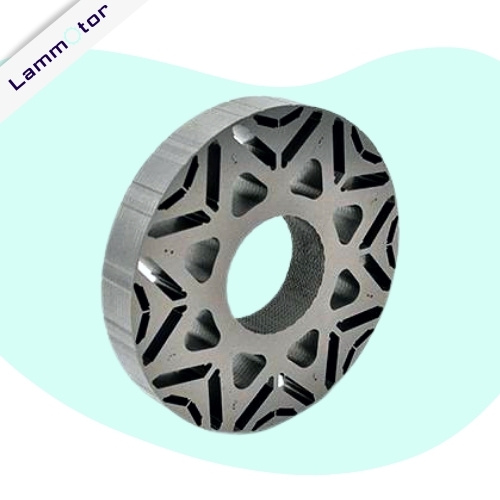
lamination stacks for industry motor core
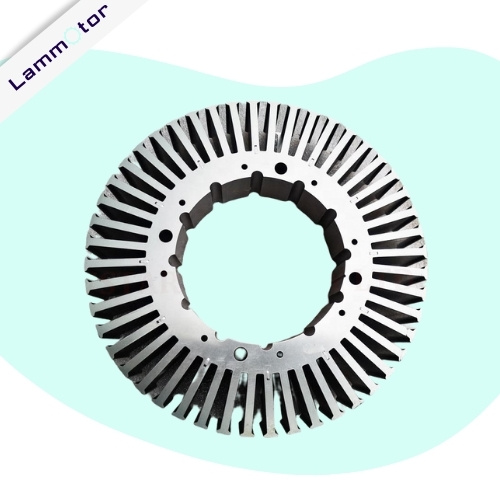
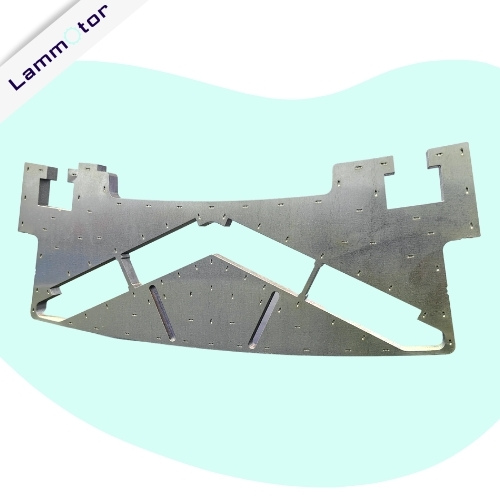
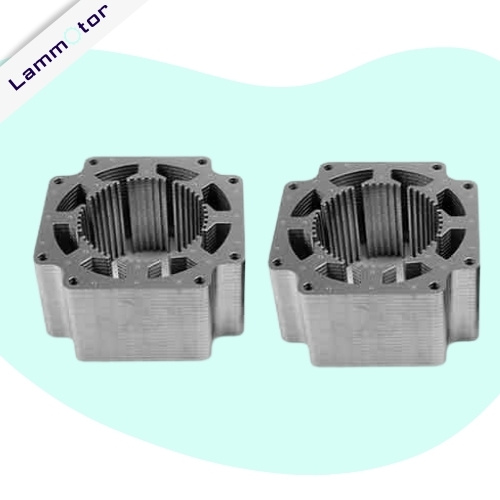
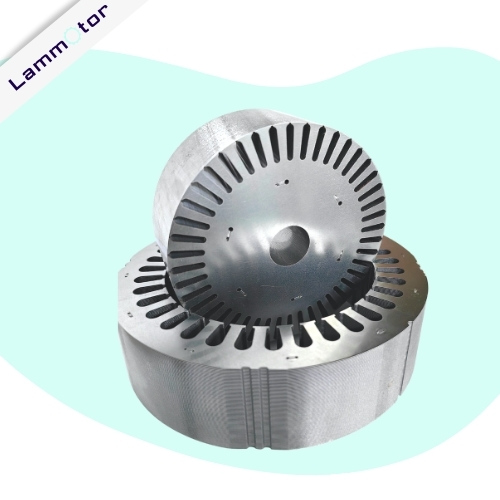
Home appliance motor core lamination stacks
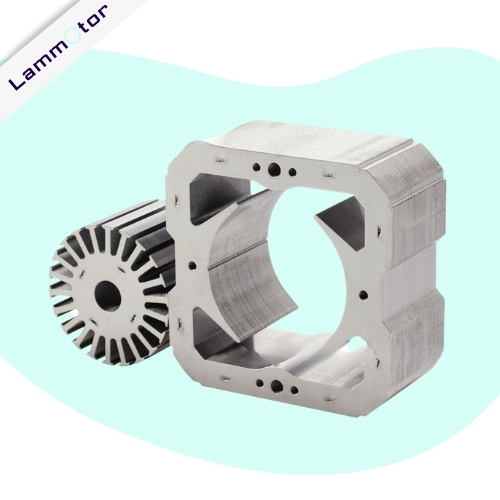
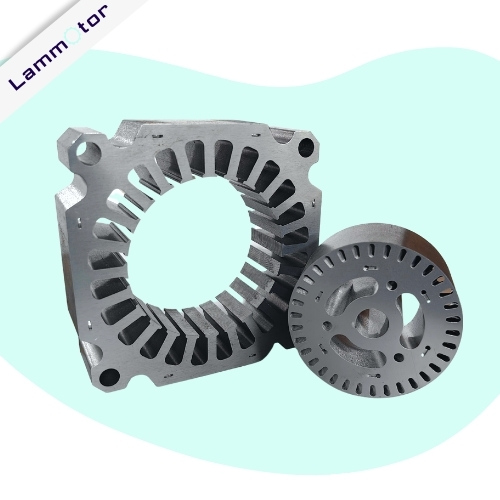
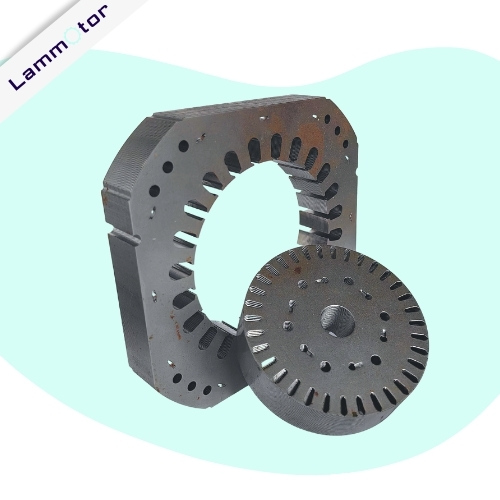
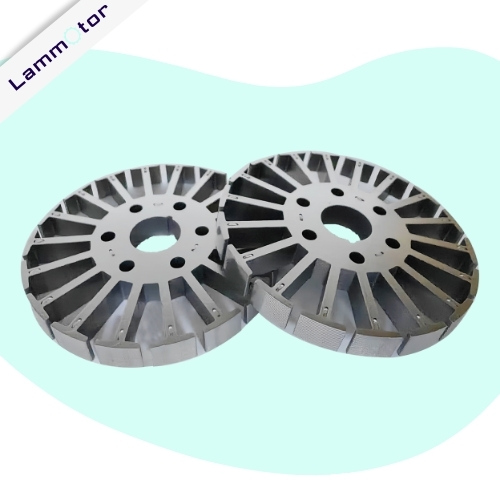
OUR SERVICES
why choose us as your lamination stacks manufacturer for motor cores?
We offer various motor core lamination stack services, including die design, material selection, annealing, and precision tolerances. Our 10+ years of experience in the lamination industry ensures we can customize solutions to meet your unique needs.
high-quality materials
We use high-quality metal alloys for maximum durability and performance. This allows our clients to rely on a lamination solution that will perform consistently and last for years.
quality control
We conform to ISO 9001, IATF 16949 quality management standards for all our motor lamination stack products. And we have advanced CMM equipment to inspect final products.
fast turnaround
We can offer quick turnaround times with our laser and punch-pressing technologies. Our lamination fabrication technology can help reduce manufacturing time and cost while delivering high-quality results.
See Why Our Customers Trust Us

“We’ve worked with several motor core lamination manufacturers in the past, but none have been able to match the quality and service of Lammotor. They’re always our first choice when we need motor laminations.”
– John Doe, Manager

“The laminations from Lammotor are top-notch. They have high precision, and the surface finish is great. We’ve been using them for years and haven’t had any issues.”
– Joe Smith, CEO

“We’ve tried several motor lamination manufacturers, but Lammotor is the best. Their customer service is outstanding, and they always deliver on time.”
– Jamie, Engineer

“If you’re looking for a motor lamination manufacturer that can provide high-quality laminations with quick turnaround times, Lammotor is the right choice. He has strong motor lamination fabrication capabilities!”
– Jyll S, Manager
Secondary Operations
stacking
Stacking involves riveting, gluing, or welding multiple laminations to form a complete motor core. This process is vital for ensuring that the motor core is structurally sound and can withstand the forces it will experience during use. Rivet stacking is the most common method of connecting multiple laminations due to its speed and cost-efficiency.
rivet
Riveting is usually suitable for low-voltage applications where high precision and accuracy are unnecessary. It involves using small metal pins to join two pieces of metal together at several points along their edges.
glue
Glue is often suitable for higher-voltage motors since it provides better insulation than rivets. The glue bonds the layers together while providing an airtight seal to prevent moisture or dust from entering the core.
welding
Welding involves layering individual steel laminations and welding them together, helping to create robust stators with high levels of electrical insulation.
Electrostatic epoxy coating
Electrostatic epoxy coating is a powder-coating process that applies an electrostatically charged powder to the surface of parts using spray nozzles; this creates an even layer for better protection from corrosion and wear damage.
electric Motor lamination FAQs
Motor lamination is an essential component of electric motors. It refers to thin components which make up the core of the motor.
These laminations consist of thin metal sheets stacked, welded, or bonded to form the motor’s core.
Motor lamination is important in many electrical applications and is used in everything from electric vehicles to generators.
When it comes to motor core lamination, electrical steel is the most common material that is used. This is because electrical steel has many magnetic properties that make it ideal for motor lamination.
These properties include high permeability, low coercivity, and high saturation flux density.
Other materials that can be used in motor core lamination include nickel alloy and cobalt alloy.
Motor cores are used in generators, transformers, and other power electronics devices to help provide efficient power conversion and control.
In addition, they can be found in electric vehicles and home appliances such as washing machines and refrigerators.
Due to their robustness and ability to withstand large amounts of heat generated by electricity flowing through them, motor cores have become essential for many industrial machines where reliability is crucial.
Finding a reliable motor core lamination China manufacturer is not as easy as it may sound. It requires research and due diligence to ensure your supplier can meet your needs.
Here are some tips to help you find the best motor core lamination China manufacturer for your business:
First, check the reliability of any potential suppliers. You can do this by looking at customer reviews, trade association membership, and references from other companies that have used their services. Ensure you clearly understand what materials they use and how long it takes them to deliver products.
Additionally, ask about quality control processes and safety standards to ensure they adhere to industry regulations.
Second, consider cost efficiency when choosing a motor core lamination China manufacturer.
Looking for an Electric Motor Lamination China manufacturer?
If you are looking for an electric motor lamination China manufacturer, contact us! We’ll provide reliable customize solutions and professional guidance to help you make the perfect choice for your project. We can also offer magnetic motor laminations in various sizes, shapes, and thicknesses to ensure high performance in any application. Come to Lammotor and experience our high-performance magnetic lamination services!