Have you ever wondered how motor laminations are stamped with high precision and efficiency? As a motor lamination designer, I have spent years working with metal stamping processes that shape the performance of electric motors.
In this article, I will guide you through the key techniques used in motor lamination metal stamping, explaining why the right stamping method is crucial for reducing energy loss and improving motor efficiency.
What is a Motor Lamination?
A DC motor consists of two main components: the stator and the rotor. The core laminations form the rotor and include slots that support the windings and coils. When the core rotates in a magnetic field, it induces voltage in the coils, which in turn generates eddy currents.
Reducing eddy currents is essential to improving motor efficiency. Thinner laminations are used instead of a solid metal core to minimize the cross-sectional area, thereby increasing electrical resistance and reducing energy loss. These individual steel sheets, called motor laminations, form the armature core.
The primary reason for using multiple thin laminations is to reduce eddy current loss. The thinner the sheets, the higher the electrical resistance, resulting in lower eddy current losses. This improves overall motor efficiency.
Materials for Motor Laminations
Motor laminations are made of electrical steel, commonly known as silicon steel. This steel is specially designed for electrical applications, such as motor stators, rotors, and transformers.
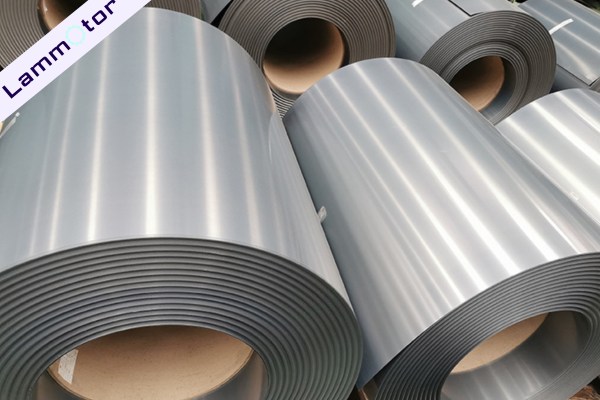
Adding silicon to steel increases its electrical resistance and reduces magnetic hysteresis loss, which enhances its efficiency in alternating magnetic fields. Silicon also helps to reduce corrosion, but its primary purpose is to minimize hysteresis loss, ensuring that the steel can quickly establish and maintain a magnetic field.
Types of Metal Stamping for Motor Laminations
Metal stamping is a cold-forming process that uses dies and presses to shape metal sheets into specific forms. In motor lamination metal stamping, various techniques are used to manufacture high-precision laminations.
1. Progressive Stamping
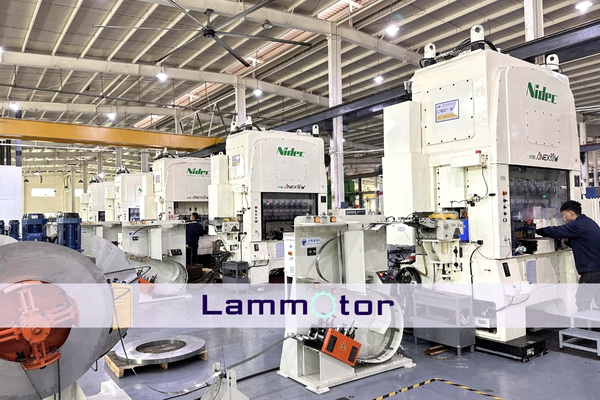
Progressive stamping is a highly automated method where a metal strip passes through multiple stations, completing punching, bending, and forming operations in sequence. This process is ideal for high-volume production due to its efficiency and consistency.
To further optimize progressive stamping, two advanced techniques are often used:
(1) Notching Rotational Stacking
This method involves rotating each lamination layer at a specific angle during stacking to reduce tolerance buildup and improve both magnetic performance and geometric precision.
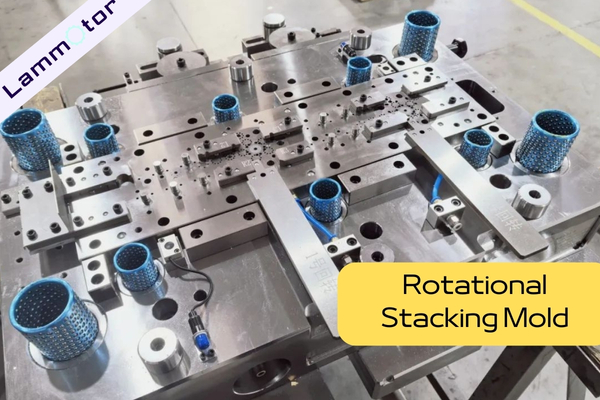
Key Advantages:
- Enhanced Magnetic Performance – Reduces hysteresis loss and improves motor efficiency.
- Improved Dimensional Accuracy – Enhances flatness, parallelism, and concentricity.
- Versatile Application – Supports stacking angles such as 45°, 60°, 72°, 90°, 120°, and 180°, making it ideal for high-precision motor laminations.
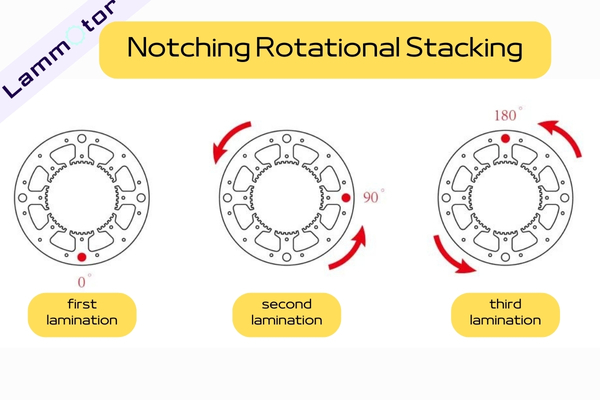
(2) Stamping & Bonding Integration
Instead of traditional riveting or welding, which can introduce mechanical stress, this process applies adhesive between lamination layers for improved stability.
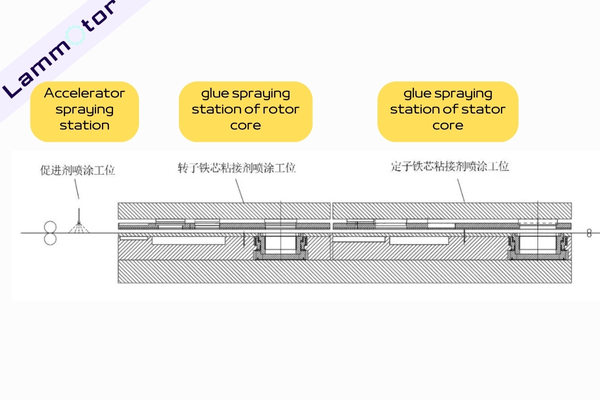
Key Advantages:
- Lower Iron Loss & Higher Efficiency – Eliminates mechanical stress and enhances magnetic flux density.
- Reduced Noise & Vibration – Minimizes structural resonance, leading to smoother motor operation.
- Increased Durability – The bonded core structure is more resistant to loosening and deformation.
2. Compound Stamping
Compound stamping integrates multiple steps into a single-stroke operation, completing punching, forming, and trimming in one go.
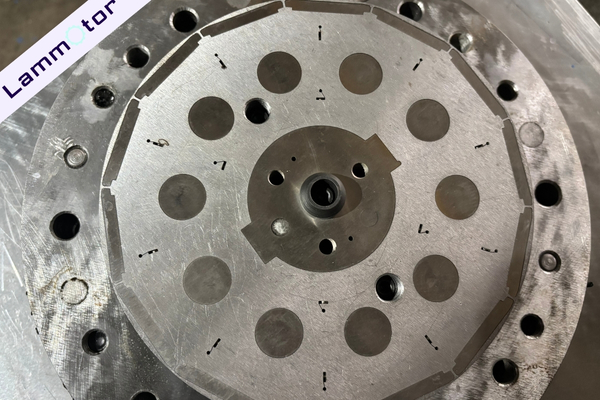
Key Advantages:
- High Precision – Ensures consistent part quality.
- Material Efficiency – Reduces material waste, lowering production costs.
- Ideal for Custom Orders – More flexible than progressive stamping, making it suitable for small-to-medium production runs.
However, compound stamping has slower production speeds and higher tooling costs, making it less suitable for large-scale mass production.
3. Rotary Notching
Rotary notching is commonly used for large-diameter motor laminations, such as those found in wind turbine generators and industrial motors.
Key Advantages:
- Cost-Effective for Custom Production – Eliminates the need for expensive progressive dies.
- Ideal for Large Motor Laminations – Can process cores up to 1250mm in diameter.
- High Precision Notching – Ensures precise and uniform slot formation for optimal motor performance.
While rotary notching is ideal for prototyping and small-batch production, mass production typically transitions to progressive or compound stamping.
Why Are Motor Laminations Stacked?
Stacking motor laminations reduces eddy current losses, improving overall motor efficiency. Each lamination layer is insulated to block eddy currents, preventing excessive heat buildup. The more laminations in a core, the lower the energy loss and the higher the efficiency.
If lamination insulation is absent, eddy currents flow freely, causing overheating and reduced efficiency.
Our Motor Lamination Metal Stamping Die Capabilities
We specialize in high-precision metal stamping dies for motor laminations, providing customized solutions for our clients.
Our mold manufacturing technology enables us to produce motor lamination metal stamping dies in a variety of shapes and sizes, ensuring top-quality motor core manufacturing.
Motor lamination metal stamping is an essential process for high-performance electric motors. By choosing the right stamping method, manufacturers can improve efficiency, reduce energy loss, and enhance durability.
If you want to learn more about motor lamination materials, stamping die design, or advanced manufacturing techniques, explore our website for more information.