Are you familiar with electrical steel? It is commonly known as silicon steel, an essential soft magnetic alloy for the power, electronics, and military industries. It’s a low-carbon silicon-iron alloy, with silicon content ranging from 0.8% to 4.8%, and is rolled into thin sheets less than 1mm thick.
Adding silicon improves electrical resistance and magnetic permeability while reducing core losses and coercivity. This material is vital for motor, generator, and transformer cores.
In this blog, we will explore the differences between Grain Oriented Electrical Steel (GOES) and Non-Grain Oriented Electrical Steel (NGOES), helping you understand which is best for your electrical applications.
Classification of Silicon Steel by Silicon Content
Silicon steel sheets are classified into two types based on their silicon content: low silicon and high silicon.
Low Silicon Sheets
Low silicon sheets contain less than 2.8% silicon and have a certain mechanical strength. They are mainly used in motor manufacturing and are commonly referred to as motor silicon steel sheets.
High Silicon Sheets
High silicon sheets contain 2.8% to 4.8% silicon, offering better magnetic properties but are more brittle. They are primarily used in transformer cores and are known as transformer silicon steel sheets. In practical applications, there is no strict boundary between the two, and high silicon sheets are often used in large motors.
Classification of Silicon Steel by Production Process
Cold-rolled silicon steel and hot-rolled silicon steel are essential materials used in electric motors, transformers, and other electromagnetic equipment. They are made from silicon steel through different manufacturing processes, each with distinct properties.
1. Cold-Rolled Silicon Steel
Cold-rolled silicon steel is produced by rolling steel at room temperature. This process creates thinner, smoother steel sheets with higher precision.
Cold-rolled silicon steel has better magnetic performance, including lower iron loss and higher permeability. It is widely used in high-efficiency electrical equipment like transformers and motors.
There are two types: grain-oriented (GO) and non-grain-oriented (NGO). Grain-oriented steel has superior magnetic properties in a specific direction, while non-grain-oriented steel provides consistent performance in all directions.
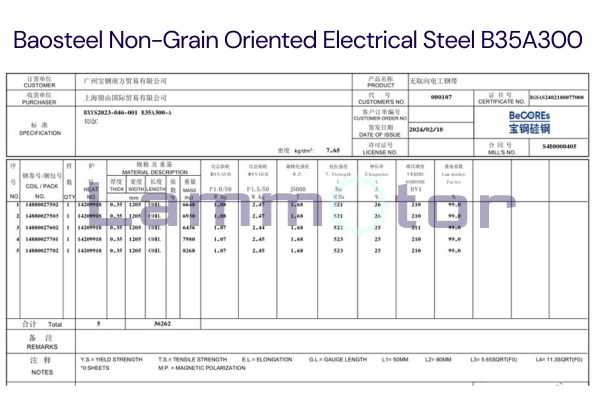
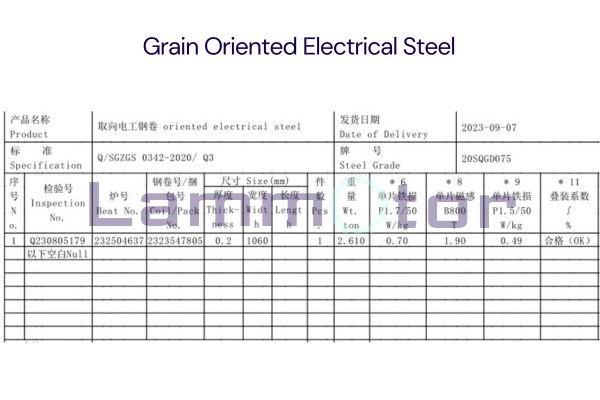
So, today we mainly discuss the two classifications of cold-rolled silicon steel.
Cold-rolled silicon steel is divided into grain-oriented and non-grain-oriented types.
Non-grain-oriented cold-rolled steel is typically used for motor cores and welding transformers, while grain-oriented steel is applied in power transformers, pulse transformers, and magnetic amplifiers.
Grain-oriented steel is produced by further processing silicon steel strips of 0.30 or 0.35mm thickness through pickling, cold-rolling, and annealing. Non-grain-oriented steel is hot-rolled into 2.3mm thick coils and then cold-rolled.
Cold-rolled electrical steel offers flat surfaces, uniform thickness, high stacking factor, and excellent punchability, with better magnetic properties and lower iron losses compared to hot-rolled steel.
Using cold-rolled steel in motors or transformers can reduce weight and volume by 0%-25%, while grain-oriented steel can improve energy efficiency and reduce transformer energy consumption by 45%-50%.
2. Hot-Rolled Silicon Steel
Hot-rolled silicon steel is made by rolling steel at high temperatures. This process typically results in thicker sheets with a rougher surface compared to cold-rolled steel.
Hot-rolled silicon steel has higher iron loss and lower magnetic performance than cold-rolled steel. It is mainly used in equipment with lower performance requirements, such as smaller motors and some lower-end transformers.
Cold-rolled silicon steel features uniform thickness, superior surface quality, and better magnetic properties. Due to these advantages, cold-rolled steel is gradually replacing hot-rolled steel in many industrial applications.
Key Differences Between Non-Grain Oriented Electrical Steel And Grain Oriented Electrical Steel
1. Silicon Content
Both GOES and NGOES are cold-rolled silicon steels, but they differ in silicon content. NGOES has a silicon content between 0.5%-3.0%, while GOES contains more than 3.0%.
2. Differences in the Production Process
Non-Grain Oriented Steel (NGOES) Requires Less Complex Processing.
The manufacturing process for NGOES is simpler compared to Grain Oriented Steel (GOES). NGOES is made by hot-rolling steel slabs or cast slabs into coils with a thickness of around 2.3mm.
For low-silicon products, the hot-rolled coils are pickled and then cold-rolled down to a thickness of 0.5mm.
For high-silicon products, the hot-rolled coils are pickled after normalization at 800-850°C. The steel is then cold-rolled to 0.55mm or 0.37mm thickness, annealed at 850°C in a hydrogen-nitrogen atmosphere, and further cold-rolled to a final thickness of 0.50mm or 0.35mm. This small reduction in thickness during cold rolling allows for grain growth during annealing, which lowers core losses.
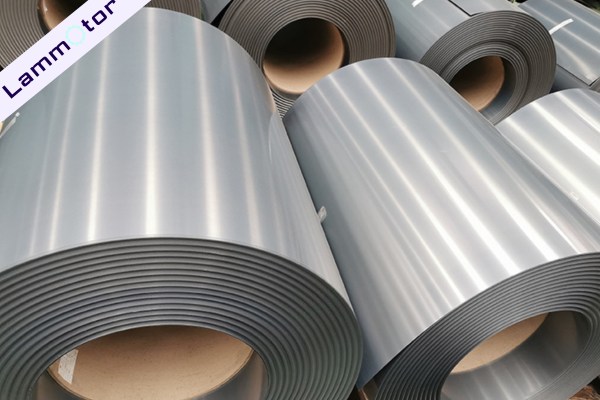
Final Annealing and Coating.
Both GOES and NGOES undergo final annealing in a continuous furnace at 850°C in a 20% hydrogen-nitrogen atmosphere. After annealing, an insulating layer made of phosphate and chromate is applied.
Cold-rolled steel is supplied in thicknesses of 0.35mm and 0.5mm.
Non-Grain Oriented Steel (NGOES) has a higher saturation magnetic flux density (Bs) than Grain Oriented Steel (GOES). GOES requires low oxide impurities in the steel and must contain 0.03-0.05% carbon and inhibitors (second-phase dispersed particles or grain boundary segregation elements). The role of the inhibitors is to prevent grain growth during primary recrystallization and promote the development of secondary recrystallization, achieving a high [001] orientation.
Inhibitors negatively affect magnetic properties, so after their role is complete, a high-temperature annealing process is necessary to purify the steel. When using second-phase inhibitors, the slab heating temperature must be high enough to dissolve coarse second-phase particles, allowing smaller particles to precipitate during hot rolling or normalization to enhance the inhibition effect.
Final Thickness and Performance.
Cold-rolled steel is available in final thicknesses of 0.28mm, 0.30mm, or 0.35mm. Grain-oriented silicon steel strips are produced by further processing 0.30mm or 0.35mm thick strips through pickling, cold rolling, and annealing.
Compared to Non-Grain Oriented Steel, GOES has much lower core losses and exhibits strong magnetic directionality. In the rolling direction, GOES has superior magnetic permeability and low core losses. Its core loss in the rolling direction is only one-third of that in the transverse direction, with a magnetic permeability ratio of 6:1. GOES has half the core loss of hot-rolled steel and 2.5 times the magnetic permeability.
3. Grain Structure
GOES has an ordered grain structure, while NGOES has a random grain orientation. This difference impacts their magnetic properties, with GOES offering superior directionality, making it ideal for transformer cores. NGOES is better suited for motors, compressors, and generators.
4. Performance and Applications
Due to its higher magnetic directionality and lower core loss, GOES is primarily used in transformers, earning it the name “transformer steel.” NGOES, known as “motor steel,” is commonly used in generator manufacturing because of its uniform magnetic properties.
How To Distinguish Between Non-Grain Oriented Electrical Steel And Grain Oriented Electrical Steel?
There are two simple ways to distinguish between Non-Grain Oriented Electrical Steel and Grain Oriented Electrical Steel:
Visual Inspection
Grain Oriented Electrical Steel has a grayish-white color, while Non-Grain Oriented Electrical Steel typically has a more uniform, metallic appearance.
Bending Test
Take a steel sheet and fold it by hand. Grain Oriented Electrical Steel will produce grayish-white particles when bent and will break after two to three folds. In contrast, Non-Grain Oriented Electrical Steel is much more flexible and can be folded up to ten times without breaking.
Contact Lammotor to Manufacture Electric Motor Stator Rotor Cores
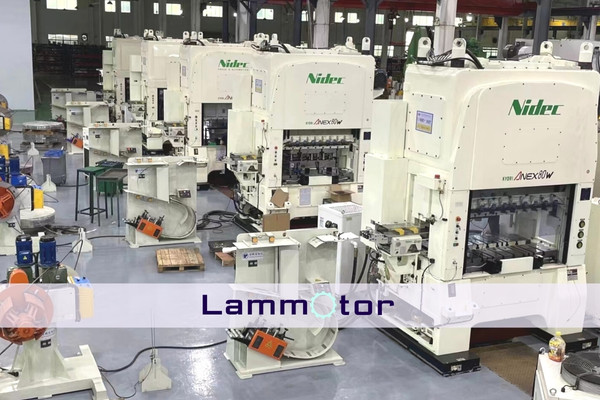
If you are looking for high-quality electrical steel laminations for your motor, contact us now! Lammotor specializes in manufacturing custom stator and rotor electrical steel laminations for a wide range of applications, including transformers, motors, and generators.
Our expert team ensures precision and efficiency in every product. Contact us today to discuss your specific needs and learn how we can provide the ideal solution for your business. Partner with Lammotor for reliable, cost-effective motor stator and rotor cores.