For stator and rotor lamination stacks, there are many assembly stacking methods. Motor laminations welding is one of them.
Motor lamination welding is a crucial process during the manufacturing of these laminations. The welding process involves joining two or more metal sheets to create a single lamination.
In this blog, we will discuss the different welding techniques for motor laminations, our welding capability, and quality control measures.
What is motor lamination welding?
Motor lamination welding is the process of joining two or more metal sheets to create a single lamination that forms part of an electric motor. Electrical steel laminations are essential components in electric motors as they help reduce energy losses and improve efficiency. The welding process involves heating the metal sheets at the point of contact until they melt, and then pressing them together to form a joint.
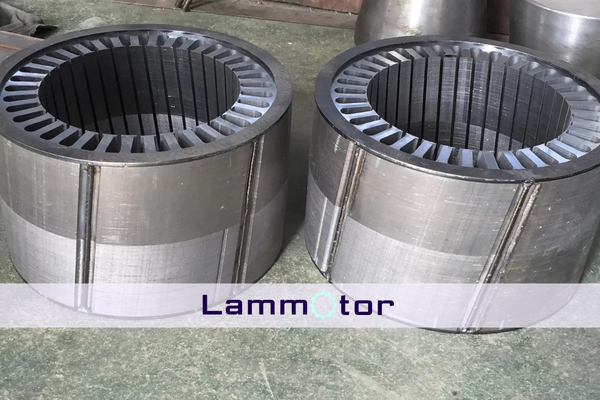
Welding Techniques for Motor Laminations
Different welding techniques can be used for motor lamination welding, including resistance welding, laser welding, Tungsten Inert Gas (TIG) welding, Metal Active Gas (MAG) welding, and electron beam welding.
Each technique has its advantages and disadvantages depending on the properties of the metal being welded, the required strength of the joint, the thickness of the metal sheets, and the cost of the welding method.
Let’s take a closer look at some common techniques:
Resistance Welding
This technique is widely used for rotor and stator lamination welding. It involves passing an electrical current through the metal sheets to generate heat and melt the surfaces where they meet. The sheets are then pressed together to form a single lamination.
Laser Welding
This non-contact welding technique uses a laser beam to melt the metal sheets’ surface before pressing them together.
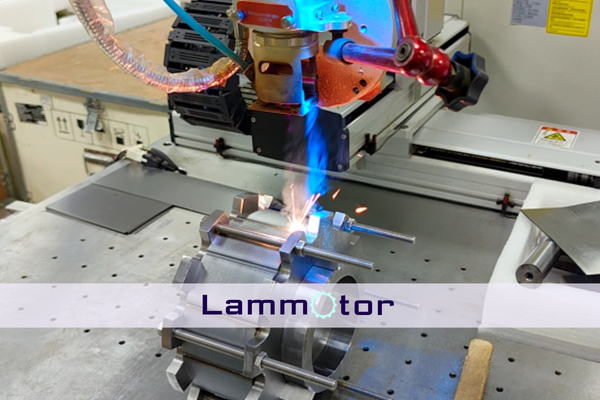
Tungsten Inert Gas (TIG) Welding
TIG welding is a precise welding technique that uses an electrode to produce an arc between the electrode and the workpiece. The arc melts the metal sheets and forms a joint when they cool.
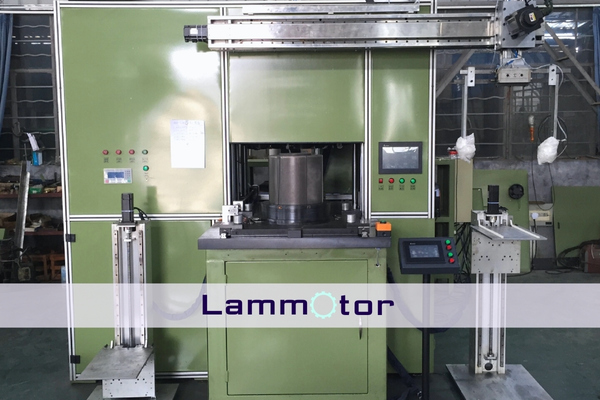
Metal Active Gas (MAG) Welding:
MAG welding is a welding technique that uses a shielding gas and a consumable wire electrode to create a weld. It is commonly used in the automotive and aerospace industries.
Electron Beam Welding
This advanced welding technique uses a high-speed electron beam to melt and fuse metal sheets together. The process takes place in a vacuum, which helps prevent contamination of the metal surface.
Factors to Consider When Selecting a Welding Technique
When selecting a welding technique for motor laminations, there are several factors to consider. These include:
Material
The type of material used for the laminations must be considered when selecting a welding technique. Laminations can be made from various materials such as silicon steel, nickel-iron alloys, or cobalt-iron alloys. Each material requires a specific welding technique.
Joint design
The shape and size of the joint determine the type of welding technique that is suitable. Motor laminations typically have very thin joints that require precision welding techniques like laser welding or micro TIG welding.
Weld quality
Motor laminations require high-quality welds to ensure efficiency and longevity. Welding techniques like resistance welding or laser welding produce clean, strong welds that improve motor performance.
Cost
The cost of the welding equipment and consumables will also be a factor in selecting a welding technique. Some techniques may be more expensive upfront but result in cost savings in the long run by reducing scrap rates and increasing efficiency.
Production volume
The production volume of motor laminations will also influence the selection of a welding technique. For high-volume production, techniques like resistance welding or projection welding may be more efficient than manual welding techniques.
By taking these factors into consideration, one can select the best welding technique for motor laminations, resulting in a high-quality product that meets the needs of the application while remaining cost-effective.
Welding Materials for Motor Laminations
The choice of material is essential when it comes to motor lamination welding. Common materials used for motor laminations include silicon steel, cobalt-iron alloys, nickel-iron alloys, and amorphous iron. Each of these materials has properties that impact the welding process.
Our Motor Laminations Welding Capabilities
We stand out in the industry with our exceptional capabilities in laser cutting laminations and motor lamination welding. We have advanced techniques such as laser welding, TIG welding, and MAG welding to create strong, high-quality welds with minimal distortion.
Our team produces clean, aesthetically pleasing welds using TIG welding, while MAG welding is ideal for thicker materials.
Our welding process allows us to seamlessly fuse the individual laminates into a solid core, thereby reducing energy loss and increasing efficiency. It also reduces noise and improves reliability, making it perfect for a wide range of applications.
With these strong capabilities, we are able to produce motor laminations of exceptional quality and durability. Choose us for reliable and efficient motor lamination welding services that meet your specific needs.
Our Quality Control in Motor Lamination Welding
Quality control is crucial in motor lamination welding to ensure that the final product meets the required specifications and standards. Here are some of our key aspects of quality control in motor lamination welding:
Inspection
Regular inspection of the welds during the fabrication process is essential to detect any defects or irregularities. This can be done manually or through automated inspection systems.
Material testing
The materials used for motor laminations must be tested to ensure they meet the required specifications. Testing can include checking for material composition, thickness, and mechanical properties.
Weld testing
Welds must undergo various tests such as visual inspection, dye penetrant testing, and x-ray testing to detect any defects like porosity, cracks, and incomplete fusion.
Process monitoring
Continuous monitoring of the welding process is necessary to ensure that the welding parameters remain within the specified range. Any deviations from the desired parameters should be immediately addressed.
Documentation
All quality control activities should be documented to enable traceability and accountability. Records of inspections, testing, and monitoring should be maintained and readily accessible.
By implementing these quality control measures, manufacturers can ensure that their motor laminations meet the required standards, resulting in efficient and reliable motors.
Conclusion
Motor lamination welding is an essential process in the manufacture of electric motors. Selecting the right welding technique, and materials are essential to ensure each component meets the required standards.
By following the guidelines outlined in this blog, you should have a better understanding of motor lamination welding. And you be able to make more informed decisions when it comes to selecting a welding technique that meets your specific requirements.
If you’re in need of motor lamination welding services, don’t hesitate to contact us today. Our team of experts will work closely with you to understand your requirements and provide you with customized solutions that meet your budget and timeline.
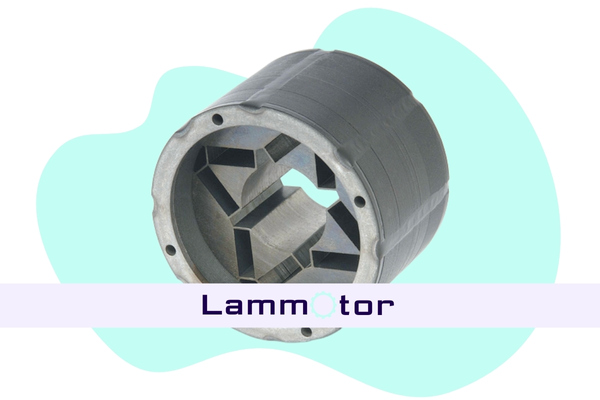
Advantages of motor lamination welding
Motor lamination welding offers several advantages over other techniques used in the manufacture of electric motors.
Stronger and more durable bond compared to other bonding techniques
Can withstand higher stresses and loads
Eliminates the need for adhesives, which can break down over time
Results in a more efficient motor by reducing magnetic flux losses
Reduces air gap between laminations, increasing efficiency
Provides a superior bond that results in a stronger, more durable, and more efficient motor
Motor Lamination Bonding Vs. Welding
Motor lamination bonding and welding are two different techniques used in the assembly process of electric motors.
Bonding involves using an adhesive to bond the laminations together, while welding involves fusing the laminations together using heat and pressure.
Bonding can be a quicker and more cost-effective option, but it may not provide the same level of strength and durability as welding.
Welding, on the other hand, can result in stronger and more durable bonds, but it may be a more complex and time-consuming process, requiring specialized equipment and expertise.
Ultimately, the choice between bonding and welding will depend on the specific requirements of the motor and the desired outcome.