Ever wondered what breathes life into the buzzing drones that crisscross our skies? It’s not just electronics and software; the heart of a drone’s motor lies in its stator, a component crucial for transforming electrical energy into the mechanical power that lifts and propels. This blog post dives into the intricacies of manufacturing drone motor stators, a process combining precision, innovation, and a touch of alchemy.
By the time you reach the end, you’ll not only understand the step-by-step journey of creating these essential parts but also grasp the nuances that make one stator stand out from another.
Whether you’re a budding engineer, a drone enthusiast, or simply curious about the magic behind the machines, you’re in the right place.
Welcome to a comprehensive guide that promises to elevate your knowledge, layer by insightful layer, on everything you need to know about the manufacturing process of drone motor stators.
The Significance of Drone Motor Stators
At the core of every drone’s motor lies the stator, an unsung hero in the UAV world. This stationary part of the motor works in tandem with the rotating component, the rotor, to create the magnetic field necessary for motion. It’s the stator’s design and manufacturing quality that dictates a drone’s efficiency and reliability in the air.
A well-crafted BLDC stator ensures optimal electromagnetic interaction, leading to smoother flights and longer battery life. Conversely, a subpar stator can be the Achilles’ heel of a drone, prone to overheating and reduced performance.
Thus, understanding the significance of drone motor stators is crucial for anyone looking to delve into the nuances of UAV technology and its advancement.1.
1. Manufacturing UAV Motor Laminations
When it comes to crafting the intricate layers of a brushless DC drone motor stator, manufacturers have a few tricks up their sleeve: stamping, laser cutting, and EDM wire cutting.
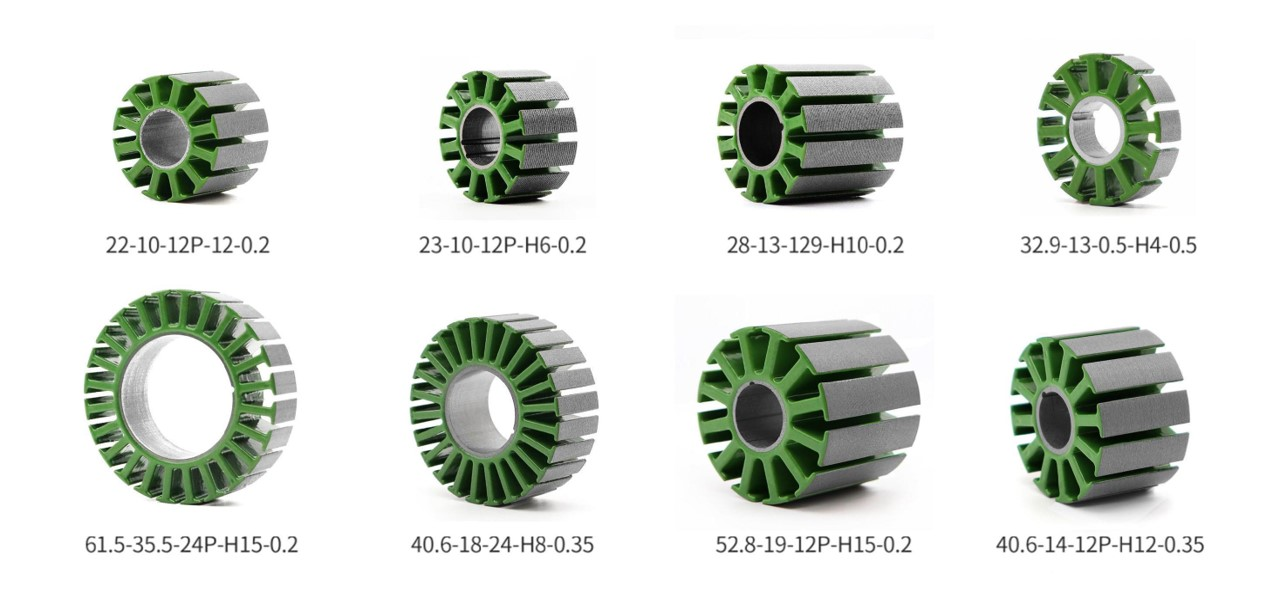
Stamping
High-speed stamping shines in mass production, churning out stator laminations with speed and cost-efficiency. However, its high upfront costs for dies and molds make it less viable for small-scale endeavors.
Enter laser cutting and EDM (Electrical Discharge Machining) wire cutting, the heroes of prototyping and short runs.
The Common material is electrical steel sheets. but now amorphous materials becoming a game-changer in the development of drone motor cores. Amorphous materials for drone motor cores offer unparalleled advantages, including superior magnetic properties and lower energy losses, which are critical in enhancing motor performance.
Laser Cutting
Laser cutting boasts incredible precision, slicing through silicon steel sheets with a focused light beam. It’s ideal for complex shapes and high-precision requirements. Yet, it struggles with thicker materials, where its prowess wanes.
EDM Wire Cutting
EDM wire cutting, on the other hand, uses electrical discharges to cut through conductive materials, offering precision that rivals laser cutting, especially for thicker electrical steel. However, its slower pace and higher operational costs can be a drawback for larger production volumes.
Each method holds its ground, but choosing the right technique hinges on balancing cost, precision, and production scale in drone motor stator manufacturing.
2. Stacking Techniques: Interlock, Welding, and Bonding
Stacking the laminations to form a drone motor stator comes down to three main techniques: interlocking, welding, and bonding.
Interlocking
Interlocking involves mechanically fitting pieces together, a method that enhances precision and alignment without additional materials, boosting the stator’s structural integrity.
Welding
Welding offers robustness, fusing laminations into a single, sturdy unit that withstands high operational stresses, enhancing the motor’s durability.
Bonding
Bonding, using adhesives, presents a cleaner alternative, reducing the risk of thermal distortion while maintaining a high level of precision.
Each method plays a crucial role in ensuring the drone motor stator’s durability and performance, with the choice depending on the desired balance between strength, manufacturing complexity, and cost-efficiency.
3. Epoxy Powder Coating Process
The epoxy coating process is a meticulous procedure that significantly enhances the durability and performance of UAV stators. Here’s a step-by-step breakdown:
Design and Manufacture Custom Coating Mask Fixture: Begin by crafting a fixture tailored to the stator’s dimensions, ensuring it can hold the stator core securely during the coating process.
Assemble the Fixture to the Stators: Fit the stators into the custom fixtures, preparing them for an even and precise coating application.
Electrostatic Coating: Use an electrostatic coating machine to uniformly apply epoxy powder onto the stators’ surfaces. This method ensures the powder adheres even to complex geometries.
Brush the OD Surface: After coating, meticulously brush the outer diameter (OD) surface of the stators to remove any excess epoxy powder, preventing irregularities.
Pre-Heat the Stators: Before curing, pre-heat the stators. This step improves the epoxy’s adherence to the stator surface, ensuring a strong bond and smooth finish.
Disassemble the Fixture: Carefully remove the stators from the fixtures, preparing them for the final curing phase.
Curing with Baking Oven: Place the BLDC motor stators into a baking oven. The curing process solidifies the epoxy, enhancing the stator’s insulation properties and resistance to environmental factors.
Each phase of the epoxy coating process is crucial for achieving the desired quality, offering a protective layer that safeguards the stator against wear, corrosion, and electrical interference, ultimately ensuring the longevity and reliability of UAV operations.
4. Drone Stator Winding Techniques
Ever played with a spool of thread, winding and unwinding it? Well, winding drone motor stators is somewhat similar, but with a twist that’s key to powering those agile flyers in the sky. Imagine threading the eye of a needle, but here, the “needle” is the stator, and the “thread” is copper wire, meticulously wound around the stator’s core. This isn’t just about looping wire; it’s a precise dance, where each turn impacts the drone’s thrust and efficiency.
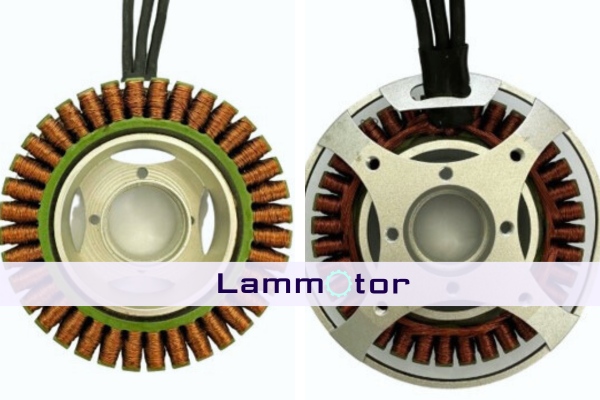
The winding process involves delicately wrapping copper wire around the stator’s teeth – a method that might sound simple but requires precision and expertise.
Each wrap of the wire needs to be just right. Too loose, and the motor loses efficiency; too tight, and we risk damaging the wire or the stator itself. This meticulous process creates electromagnetic poles, which are crucial for the motor’s function. When electricity flows through these wound wires, it generates the magnetic fields that propel the motor, and consequently, the drone, into action.
Why does this matter to you? Because this winding wizardry directly influences how your drone behaves – from hovering in place to darting through the air. It’s the secret sauce to maximizing flight time and power. So, the next time you marvel at a drone zipping by, remember: it’s all in the winding!
5. Quality Control for Drone Motor Stator
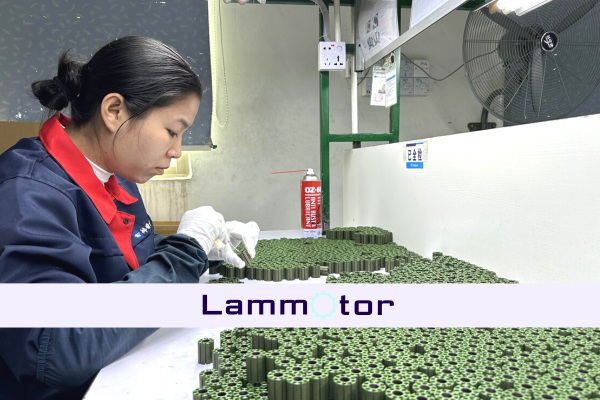
After the dance of wires and the heat of the oven, our drone motor stators aren’t quite ready to take flight just yet. They must first pass the critical eye of Quality Control (QC). This stage is the guardian of excellence, where each stator undergoes rigorous inspections.
We check for precision in the winding, the uniformity of the epoxy coating, and the structural integrity post-stacking. Only the stators that meet our high standards earn their wings, so to speak.
Once they’ve passed this test, they’re carefully packed, ready to be shipped out, and breathe life into drones worldwide.
Conclusion
In the journey of manufacturing the heart of a UAV, the motor stator, we’ve traversed through meticulous steps from precise cutting techniques to intricate winding and rigorous quality controls. Each phase, be it the artful coating or the strategic assembly, plays a pivotal role in ensuring the stator’s performance and durability, ultimately defining the drone’s capability to conquer the skies.
Ready to elevate your drone’s performance with custom or premium brushless DC drone motor stators? Reach out to us. Let’s discuss how our expertly manufactured UAV motor stators can power your aspirations to new heights. Contact us today to start your journey towards superior flight performance and reliability.