Why are amorphous materials becoming a game-changer in the development of drone motor cores? In the rapidly evolving world of drone technology, efficiency and performance are paramount. Amorphous materials for drone motor cores offer unparalleled advantages, including superior magnetic properties and lower energy losses, which are critical in enhancing motor performance.
This blog will guide you through the benefits, manufacturing processes, and innovative applications of amorphous materials in drone motors. By the end, you’ll understand why and how these materials are revolutionizing drone technology, providing you with the knowledge to stay ahead in the field of advanced motor design.
Advantages of Amorphous Materials in Drone Motor Cores
Amorphous materials stand out in drone motor core applications primarily due to their high magnetic permeability and minimal core losses. Here’s how these features contribute to motor efficiency:
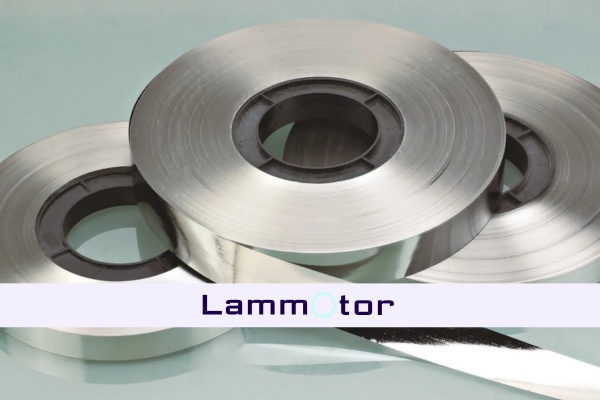
High Magnetic Permeability: Amorphous materials allow for a more concentrated magnetic field in motor cores. This quality helps in achieving greater efficiency during the conversion of electrical energy into mechanical energy. Motors using amorphous materials are not only more responsive but also more reliable in performance.
Low Core Losses: Traditional materials often lose considerable energy in the form of heat due to magnetic hysteresis and eddy currents. Amorphous materials, in contrast, exhibit lower hysteresis loss. This efficiency in energy use results in motors that run cooler and have a longer lifespan.
Reduced Eddy Current Losses: The non-crystalline structure of amorphous materials plays a crucial role here. Their lack of a defined, regular atomic arrangement significantly impedes the flow of eddy currents. Additionally, the materials’ thin ribbon thickness further restricts these currents, minimizing energy dissipation.
These properties collectively enhance the performance of drone motors by improving their efficiency and reliability, reducing operational costs, and extending the durability of the motor cores. Through these advantages, amorphous materials are redefining what’s possible in drone technology.
Manufacturing Process of Amorphous Motor Cores
The manufacturing process of amorphous drone motor cores involves precise steps to ensure optimal performance and durability. Here’s a closer look at these steps:
Cutting: The process begins with the amorphous material being precisely cut into strips. The width of these strips is determined based on the specific design requirements of the motor. This cutting process must be accurate to ensure the material maintains its beneficial properties.
Coiling: After cutting, the thin strips are wound into cores using specialized amorphous motor core coiling machines. This step is crucial as it shapes the amorphous material into the functional core that will be at the heart of the motor. Proper winding ensures that the core will function efficiently and effectively.
Surface Treatment: The final step in the manufacturing process is surface treatment. Common treatments include annealing, which relieves internal stresses and enhances magnetic properties, and copper plating, which improves both electromagnetic performance and corrosion resistance. These treatments are essential for ensuring the longevity and effectiveness of the motor cores.
We use amorphous materials instead of silicon steel as the stator core part of the motor. Amorphous materials still have the characteristics of high saturation magnetic induction, low loss, and high magnetic density at high frequencies. Therefore, it can increase the number of stator poles of the permanent magnet motor, thereby obtaining smaller size, energy consumption, higher efficiency, and torque at the same power and speed.
Normally, the common material for drone motor cores is electrical steel, click the link to learn more manufacturing process of electrical steel drone motor cores.
Other Applications of Amorphous Alloy Materials
Amorphous alloy motors focus on medium and high-frequency motors with high power density requirements, and their application prospects are very broad!
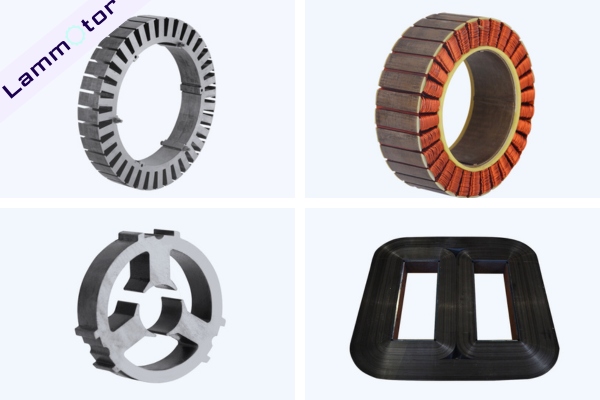
New energy vehicle motor: 400~2000Hz, 1~200kW;
High-speed spindle motor: 60,000 to 200,000 rpm, 1.25 to 80kW;
High-frequency motors for fans and water pumps: rotation speed 20K~100K;
Medium frequency motors/generators for navigation, aviation and aerospace;
High-performance air conditioning compressors for automobiles and commercial applications;
High-speed micro motors for power tools, medical care, home appliances, and industry.
Conclusion
Amorphous materials represent a significant advancement in the technology of drone motor cores, offering unparalleled efficiency and performance enhancements. The material ensures that drone motors are not only more efficient but also more durable and reliable.
For those interested in leveraging these advancements, we invite you to contact us to customize your amorphous drone motor stator cores, ensuring your projects harness the cutting-edge benefits of this remarkable material.
How do amorphous materials improve the efficiency of drone motors?
Amorphous materials significantly enhance drone motor efficiency through their inherent properties of high saturation magnetic induction and low loss at high frequencies. This allows for an increase in the number of stator poles in the motor, resulting in a compact design with reduced energy consumption. Consequently, these motors achieve higher efficiency and greater torque at the same power and speed levels. This optimal performance profile makes amorphous materials ideal for advanced drone applications.