Do you remember the viral videos of Yushu Robots and Tesla’s humanoid robot, Optimus? These robots, which seem to have come straight out of a sci-fi movie, are already making a big impact in the real world.
Whether it’s walking gracefully, grabbing objects precisely, or completing various tasks flexibly, these robots showcase impressive mobility. But have you ever wondered what powers them? For humanoid robots to move like humans, they need strong “muscles.” This requires high-performance motors. From joint rotations to fine finger movements, each action relies on a dedicated motor working silently behind the scenes.
So, what kinds of motors are used in humanoid robots? Why do different parts need different types of motors? In this article, we will explore the “power sources” behind humanoid robots—the various driving motors!
1. Servo Motors
2. Brushless DC Motors (BLDC)
3. Stepper Motors
4. Frameless Torque Motors
5. Hollow Cup Motors
Servo Motors
Servo motors come in two main types: AC servos and DC servos.
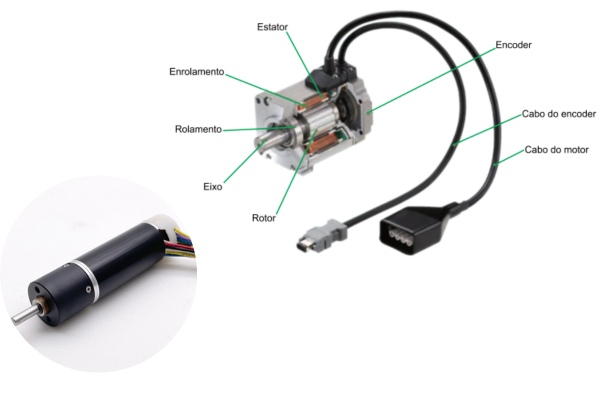
Currently, robots weighing around 10 kg or 6 kg mostly use AC servo motors. AC servos operate with a sine wave and are controlled by pulses. On the other hand, DC servo motors use pulse codes and control methods like square and direct waveforms.
Humanoid robots usually have multiple degrees of freedom to simulate human movements such as walking, grabbing, turning, and even making subtle facial expressions. These actions require high-precision motion control, and servo motors are the main drivers for robot joints due to their high torque density, fast response, and precise control.
Brushless DC Motors (BLDC)
Brushless DC motors are widely used in humanoid robots due to their high efficiency, high torque, and long lifespan. They don’t have carbon brushes, which reduces maintenance needs and failure rates.
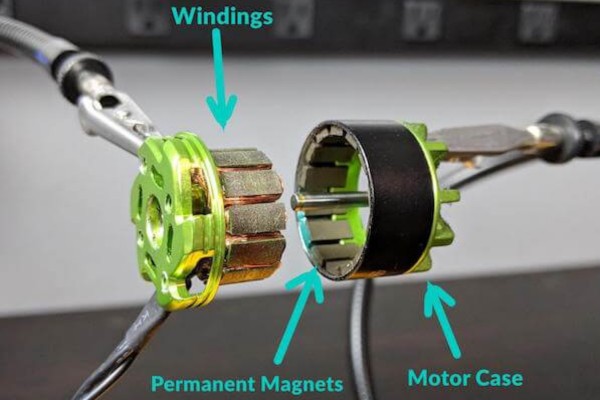
For larger joints like the legs, feet, and back, as well as larger modular areas like the torso, brushless DC motors play a crucial role. They provide powerful and stable power output to help the robot run fast, turn flexibly, and easily handle complex terrains.
In logistics warehouses, robots equipped with brushless DC motors can move efficiently between shelves, quickly and accurately handling goods, greatly improving logistics efficiency.
While brushless DC motors are not as precise as servo motors, they can still achieve excellent control effects with the help of closed-loop control technology, meeting the robot’s diverse movement needs.
Moreover, they operate quietly, creating a quieter working environment for robots, making them suitable for noise-sensitive areas like hospitals and libraries.
Stepper Motors
Stepper motors are known for their precise angle control, which is crucial for the fine manipulation of a humanoid robot’s hand.
Each pulse signal corresponds to a fixed rotation angle, allowing for precise position control and ensuring accuracy during tasks like grasping small objects or performing complex assembly operations.
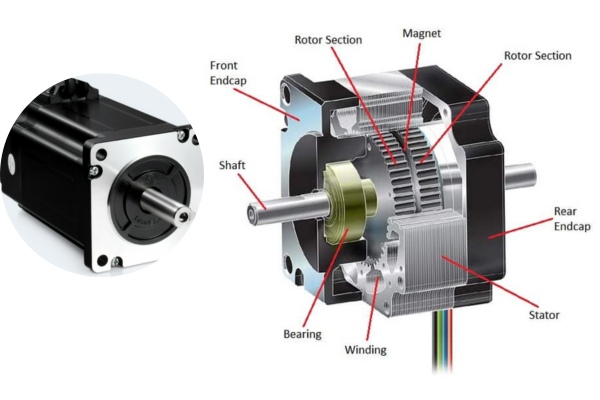
Additionally, the relatively low cost of stepper motors makes them highly attractive for mass production of humanoid robots.
Application Scenarios:
- Head Movement: Stepper motors can control the rotation of a robot’s head with precise angle control and low cost. Since head movements don’t require high precision or speed, stepper motors can achieve stable rotation through pulse signals, allowing the robot to observe and interact.
- Small Subsystems: Stepper motors are suitable for fine adjustments and light load movements in systems like camera angle adjustments, focusing, and small robotic arms, providing stable position control.
- Eye Movement: Stepper motors are small and precise, making them ideal for controlling the movement of humanoid robot eyes. When paired with transmission mechanisms, they enable eye focus and rotation, enhancing human-robot interaction.
Frameless Torque Motors
Frameless torque motors are high-torque, low-speed motors without an outer casing. They typically consist of just the stator and rotor and lack traditional mechanical support structures like casings and bearings.
These motors need to be directly integrated into robot joints or mechanical structures, with the user designing bearings, housings, and cooling systems. This design allows for tight integration with robot joints, offering a more compact and efficient driving solution.
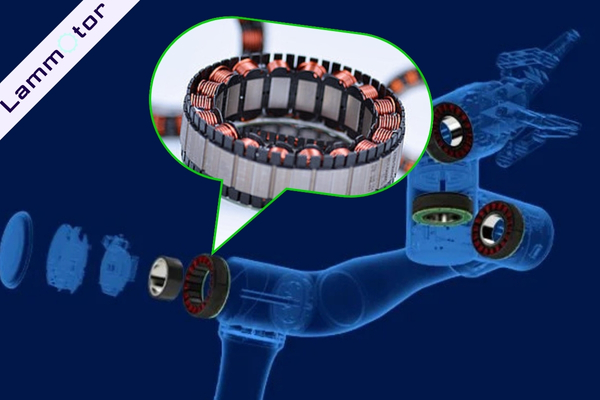
Advantages of Frameless Torque Motors in Humanoid Robots:
- High Torque Density: They deliver high torque output in a small space, making them ideal for robot joint drives.
- Low Inertia: The reduced rotational mass improves dynamic response, making the robot’s movements more agile.
- Compact Integration: They can be directly embedded into joints, saving space and offering greater design flexibility.
- High Efficiency: Direct-drive design reduces transmission losses, improving energy efficiency.
- Precise Control: With high-resolution encoders, they can achieve precise position and speed control.
Currently, leading companies manufacturing frameless torque motors include Kollmorgen, Allied Motion, Parker, TQ Robodrive, Aerotech, TM TECH, Axsys, ETEL, Muirhead Aerospace, and Gomtec.
Tesla’s humanoid robot uses 14 rotating actuators and 14 linear actuators, totaling 28 frameless torque motors. These are distributed in the shoulders (6), elbows (2), wrists (6), torso (2), knees (2), and feet (4).
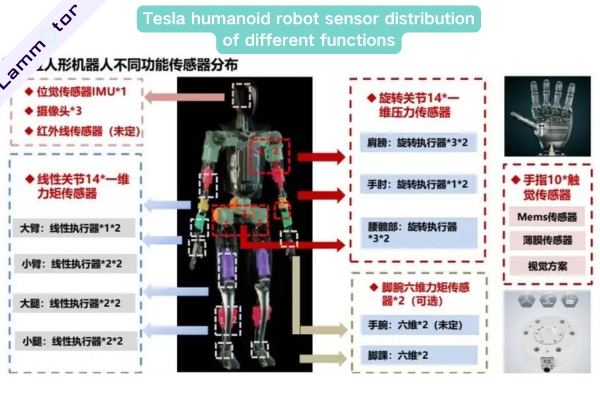
Domestic humanoid robots like Yushu H1, Yuanzheng A1, Xiaomi Cyberone, UBTECH X1, and Fourier GR-1 also use frameless torque motors in their joint units, with a maximum torque of 360Nm. Yushu, Zhiyuan, and Xiaomi robots have developed their own joint motors to better fit their respective products.
Coreless Motors
Coreless motors, also known as “slotless motors,” are a type of DC servo motor with no iron-core rotor. The coils are wound with wire and have no internal supporting structure. These motors are generally small, with a size typically not exceeding 40mm.
Compared to traditional motors, coreless motors are smaller, more precise, have longer lifespans, run faster, are more energy-efficient, and have higher energy density. When compared to iron-core motors of the same power, they are 1/3 to 1/2 lighter and more compact, significantly improving energy density.
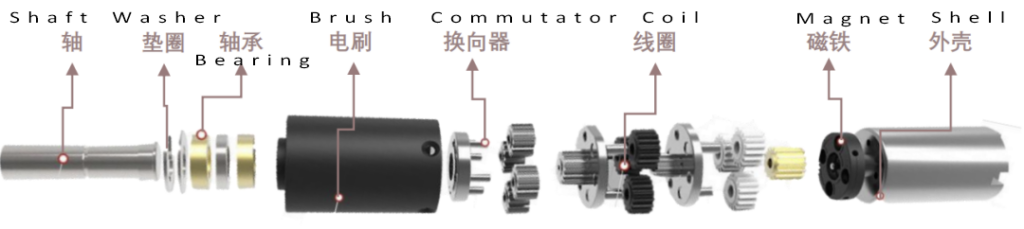
Coreless motors come in brushed and brushless types. Brushless coreless motors are efficient, quiet, long-lasting, and high-torque, typically used in high-end fields like robotics, drones, aerospace, medical devices, and power tools. Brushed coreless motors are cheaper, noisier, have a shorter lifespan, and are less efficient, making them suitable for toys and small appliances.
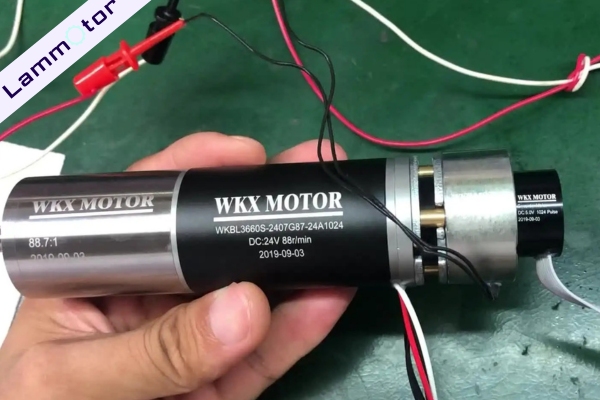
Humanoid robots typically use brushless coreless motors as core components. For example, Tesla’s robot uses a planetary gearbox, hollow cup motors, encoders, drivers, worm gears, and wire drives for its hand actuators, with 12 motors in total, each priced between 1300 and 1500 yuan.
What’s the Future of Humanoid Robots?
As we’ve seen, the various motors used in humanoid robots each play a vital role in enabling these robots to move, interact, and perform complex tasks. From high-precision servo motors to powerful brushless DC motors to coreless motors and frameless torque motors, these motors are the backbone of humanoid robotics, ensuring efficient and effective movement.
Now that you know more about the different types of motors powering humanoid robots, which one do you think holds the most potential for future advancements?