Lamination stacks, comprising layers of materials bonded together, play a pivotal role across industries. The choice between bonding and welding lamination stacks methods significantly influences the structural integrity and performance of these stacks.
In this article, we delve into the crucial decision-making process of selecting the appropriate technique. Understanding the nuances of bonding and welding becomes imperative to optimize durability and functionality.
The subsequent sections will explore each method, providing insights into its applications, advantages, and drawbacks. This comprehensive analysis aims to guide manufacturers in making informed decisions for successful lamination stack fabrication.
What Are Motor Lamination Stacks?
Motor lamination stacks, a fusion of meticulously arranged layers, form the core of many industrial applications. These rotor and stator stacks typically consist of laminated metal sheets, strategically arranged to enhance efficiency. Their importance spans diverse industries, from automotive to electronics.
The unique composition of lamination stacks is designed to optimize electrical and magnetic properties, making them indispensable in motor manufacturing. Understanding the intricate design and application nuances is key to harnessing their full potential in enhancing motor performance.
In manufacturing processes, these stacks act as foundational elements, influencing the overall efficiency and reliability of motors across a spectrum of applications.
What Is Bonding Lamination Stacks?
Bonding motor lamination stacks involves the strategic fusion of layers using adhesive methods, a process vital in various manufacturing domains. The bonding technology, utilizing diverse adhesive agents, creates a cohesive structure within the laminated layers. This technique ensures a robust adhesion, enhancing the overall strength and durability of the lamination stack. Common methods are adhesive bonding and self-bonding.
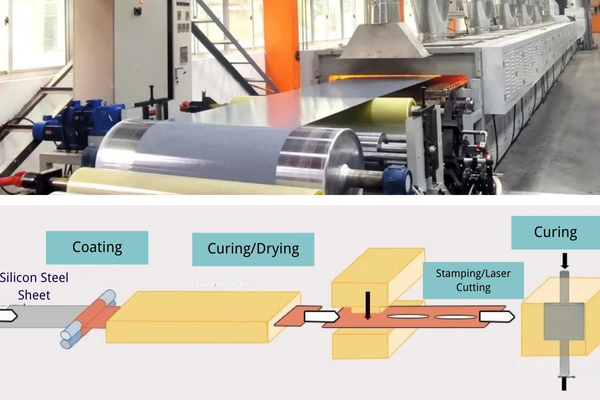
Common bonding agents include epoxies, polyurethanes, and acrylics, each tailored to specific application needs. Exploring the types of bonding agents and their unique characteristics provides valuable insights into the selection process, enabling manufacturers to make informed decisions based on the specific requirements of their electrical motor lamination stack applications.
Advantages and Disadvantages of Bonding Motor Core Lamination Stacks
Advantages
Enhanced Structural Integrity: Bonding ensures a strong and cohesive connection between laminations.
Cost-Effectiveness: Generally, bonding processes are more economical, reducing overall production costs.
Material Compatibility: Bonding accommodates a diverse range of materials, offering flexibility in design.
Reduced Weight: Bonding methods often result in lighter structures, advantageous in applications where weight is a critical factor.
Vibration Damping: Bonding can absorb vibrations, contributing to improved motor performance.
Disadvantages:
Long-term Stability: Adhesives used in bonding may degrade over time, affecting stability.
Initial Cure Time: Bonding processes may require additional time for curing or setting, impacting production speed.
Environmental Impact: Some bonding agents may have environmental considerations.
Limited to Certain Materials: While versatile, bonding may have limitations with certain materials.
Potential Weight Increase: Bonding can introduce additional weight, which may be a concern in weight-sensitive applications.
Applications Of Motor Lamination Bonding In Different Industries
Bonding stator and rotor lamination stacks find widespread applications across diverse industries, exemplifying their versatility and adaptability.
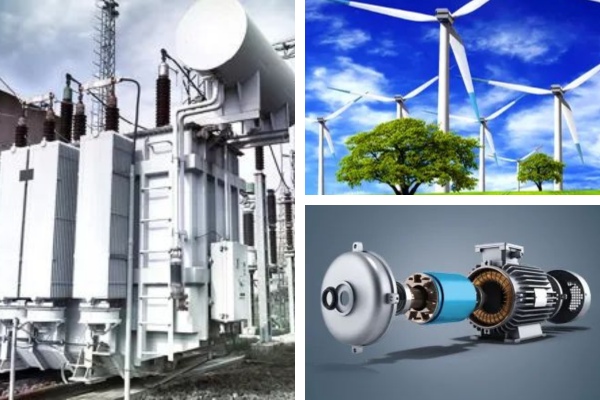
In the automotive sector, manufacturers utilize bonding for laminated cores in electric motors, enhancing efficiency. The aerospace industry benefits from the weight reduction achieved through bonding, contributing to fuel efficiency.
Within the electronics realm, backlack proves crucial in manufacturing transformers and magnetic components. In the renewable energy sector, bonding is employed in the fabrication of generator cores, optimizing performance.
Transitioning to the medical field, bonding lamination stacks are utilized in the production of diagnostic equipment. These varied applications underscore the broad spectrum of industries benefiting from the advantages of bonded lamination stacks.
What Is Welding Lamination Stacks
Welding lamination stacks involve the fusion of layers through the application of heat and pressure, creating a unified structure. As a method, welding is a robust process that brings together laminated materials seamlessly.
Various welding techniques contribute to this process, including laser welding, TIG (Tungsten Inert Gas) welding, and MAG (Metal Active Gas) welding. Laser welding utilizes a concentrated beam of light for precision, while TIG welding employs a tungsten electrode to create a strong bond. MAG welding, on the other hand, uses a shielding gas for the fusion process. Each technique offers unique advantages, catering to diverse electrical steel lamination stack requirements.
Pros And Cons Of Welding Lamination Stacks
Welding lamination stacks presents a range of advantages and disadvantages, influencing its suitability for specific applications.
Pros:
High Strength: Welding creates robust bonds, ensuring structural integrity.
Efficiency: Various welding techniques offer rapid and efficient assembly.
Versatility: Welding suits a broad array of materials, expanding its application range.
Precision: Techniques like laser welding provide precise control over the fusion process.
Longevity: Welded joints often exhibit durability over extended periods.
Cons:
Heat-Affected Zone: Some welding methods introduce a heat-affected zone, potentially impacting material properties.
Cost: Initial equipment and setup costs for welding can be higher.
Complexity: Certain welding techniques demand skilled operators, adding complexity to the manufacturing process.
Potential Distortion: Welding may distort thin materials, affecting dimensional accuracy.
Environmental Impact: Certain welding processes may generate fumes, raising environmental concerns.
Careful consideration of these factors is essential to determine the most suitable welding approach for specific lamination stack applications.
Applications of Welding Motor Laminations
Welding electric motor laminations find extensive applications across industries, showcasing its versatility and effectiveness.
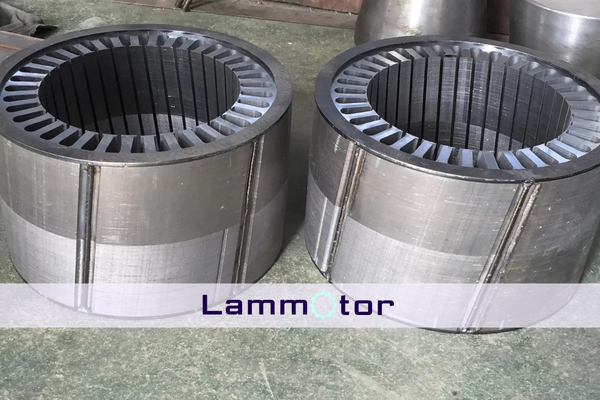
In the automotive sector, welding is employed for the assembly of motor laminations, ensuring robust connections for electric vehicle propulsion systems. The aerospace industry utilizes welding to create durable and lightweight motor components, contributing to enhanced fuel efficiency.
Additionally, welding motor laminations play a pivotal role in the manufacturing of industrial motors, where reliability and efficiency are paramount.
In the renewable energy sector, welding is crucial for fabricating generator cores and supporting the production of sustainable energy solutions. These varied applications highlight the widespread utility of welding in optimizing motor performance across diverse sectors.
Comparative Analysis: Bonding vs Welding
Structural Integrity and Durability:
When comparing bonding and welding in lamination stacks, welding often provides higher structural integrity due to the fusion of materials, enhancing durability. Bonding relies on adhesives, and while effective, long-term stability might be a consideration.
Cost Implications:
Welding may incur higher initial costs due to equipment and skilled labor requirements. Conversely, bonding is generally more cost-effective, making it a favorable option for budget-conscious projects.
Production Efficiency:
Welding processes, particularly automated ones, tend to be faster, enhancing production efficiency. Bonding, while effective, may require more time for curing or setting, impacting overall production speed.
Environmental Considerations:
In terms of environmental impact, bonding often has a lower carbon footprint as certain welding processes can produce emissions. Bonding is considered a greener option, aligning with sustainable manufacturing practices.
Flexibility in Customization and Design:
Bonding offers greater flexibility in design due to its compatibility with a wide range of materials. Welding, while versatile, may have limitations based on material compatibility, influencing design flexibility. Careful consideration of customization needs is crucial in the decision-making process.
Factors Influencing Method Selection
Material Type and Properties:
The choice between bonding and welding for lamination stacks is significantly influenced by the material’s nature and properties. While welding is adept at fusing various metals, bonding offers compatibility with a broader spectrum of materials, including composites and polymers.
Cost Considerations:
Cost plays a pivotal role in method selection. Welding often involves higher initial expenses due to equipment and skilled labor requirements. Bonding, on the other hand, tends to be more cost-effective, making it an attractive option for projects with budget constraints.
Production Speed and Efficiency:
In the fast-paced realm of manufacturing, production speed and efficiency are paramount. Welding, especially automated processes, is generally quicker than bonding, contributing to enhanced overall production efficiency. The urgency of the project and desired timelines should be carefully weighed when determining the appropriate lamination stack fabrication method.
Conclusion
In conclusion, understanding the nuances of bonding vs welding lamination stacks is crucial for optimizing manufacturing processes. By recapitulating the key points highlighted in this exploration, manufacturers can make informed decisions on the suitable method for their specific needs.
As industries evolve, the continuous advancement in bonding and welding technologies promises exciting possibilities, emphasizing the importance of staying abreast of these developments for enhanced efficiency and competitiveness in the dynamic landscape of lamination stack fabrication.
FAQs
What is the lamination bonding technique?
Lamination bonding involves joining layers using adhesive methods, creating a unified structure. Adhesive agents like epoxies or polyurethanes are applied to form a cohesive bond, enhancing strength and durability in lamination stacks.
How are the stator laminations joined together?
Stator laminations are commonly joined through welding or bonding methods. Welding employs heat and pressure for fusion, while bonding uses adhesives to create a cohesive structure in motor components.
What are the primary differences between bonding and welding lamination stacks?
The key distinctions lie in the methods—bonding relies on adhesives for cohesion, offering design flexibility, while welding involves fusion for robust connections, providing higher structural integrity and durability in lamination stacks.
How does the choice between bonding and welding affect the cost of production?
The cost of production is influenced by method choice. Welding typically incurs higher initial costs due to equipment and skilled labor, while bonding is often more cost-effective, making it advantageous for projects with budget considerations.