For an electric vehicle (EV), the motor is one of the core elements that determine its performance. As the three giants in the global electric vehicle industry, Tesla, BYD, and Huawei are all strong competitors in motor design and technological innovation.
So, what are the differences in the motor stator’s and rotor’s design? How do these technical differences affect the performance, efficiency, and stability of electric vehicles?
Today, we will reveal the advantages and disadvantages of these three brands’ motor technologies, helping you better understand how each company uses motor innovation to drive the development of electric vehicles.
In the previous article, we discussed the motor of Tesla Model 3, and Tesla Model S Plaid vs Lucid Air. If you are interested, click the link to learn more.
Stator Technology Comparison
Stator Structure:
BYD, Tesla, and Huawei have differences in their motor stator structures, mainly in the number of slots and the thickness of the laminations.
Brands | Lamination Thickness | Number of Slots |
BYD | 0.20mm | 72 slots |
Tesla | 0.28mm | 54 slots |
Huawei | 0.25mm | 54 slots |
Number of Slots:
The number of slots directly affects the motor’s electromagnetic performance. The more slots, the more uniform the stator magnetic field distribution and current distribution, improving motor efficiency.
BYD’s stator uses a 72-slot design, which is advantageous for increasing power density and stability. Tesla and Huawei use a 54-slot design, suitable for high-speed and lower noise requirements.
Lamination Thickness:
The thickness of electrical steel laminations affects the stator’s magnetic losses and efficiency.
BYD uses a 0.20mm lamination thickness, which helps reduce iron losses and improve efficiency.
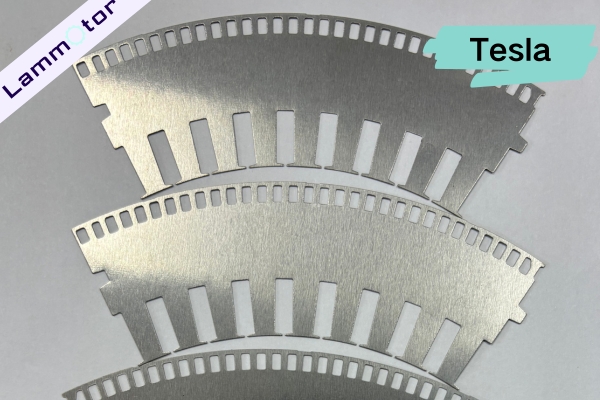
Tesla and Huawei use thicker laminations (0.25mm and 0.28mm), which enhance mechanical strength and adapt to high-load and high-temperature operating environments.
Stator Oil Cooling of Tesla, BYD, and Huawei
Oil cooling plays a crucial role in motor cooling. Compared to water cooling, oil cooling has a higher tolerance since oil has non-magnetic and non-conductive properties, making it more effective in improving motor stability and efficiency. Tesla, Huawei, and BYD each have their own unique oil-cooling designs.
Tesla Stator Oil Cooling:
Tesla’s design features square oil holes in the stator core yoke, allowing coolant to directly flow into the core for cooling. This design avoids complicated external oil passages, reducing casting costs.
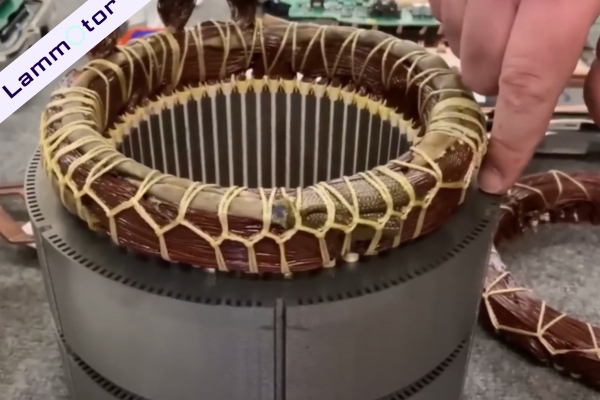
Advantages:
• Simple oil circuit design reduces casing manufacturing costs.
• Oil flows directly into the core, ensuring even and efficient cooling.
Disadvantages:
• The oil ring’s assembly with the stator core has sealing risks, which can cause oil circuit instability.
• The yoke requires additional oil hole space, which may increase radial space.
• The oil ring is cheaper than oil pipes, but still relatively costly.
Huawei Stator Oil Cooling:
Huawei’s design involves mounting end plates at both ends of the stator core to create coolant flow channels. The coolant is sprayed from nozzles on the end plates to cool the windings. This design ensures the coolant uniformly covers the windings, improving cooling efficiency.
Advantages:
• Clear oil circuit design is easier to implement and maintain.
• Flexible nozzle design allows for adjustments in oil spray direction and angle.
• No need for oil holes in the stator core, preserving radial space.
Disadvantages:
• End plates are costly, increasing the motor’s manufacturing cost.
• End cooling may cause thermal stress on the stator ends.
• Small mating surface between the stator and casing may affect torque transmission and heat dissipation.
BYD Stator Oil Cooling:
BYD’s Seagull motor stator is equipped with two oil pipes on top (shown as yellow circles) to spray oil for cooling the windings. The leftmost oil pipe head has small holes to divert some oil to the motor end cover, providing lubrication for the rear bearing.
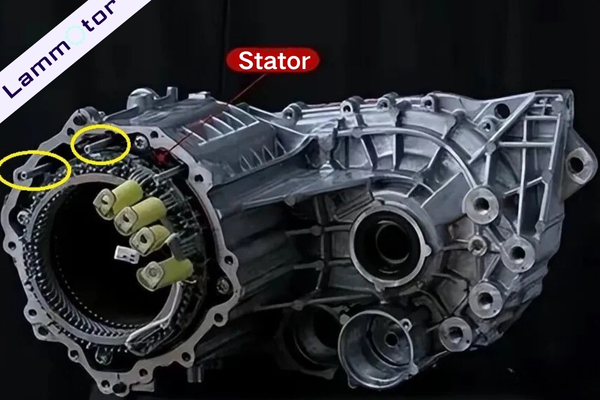
This design is similar to Hyundai’s E-GMP platform oil pipe design, where stainless steel pipes spray oil to cool the stator.
This design is simpler than the E-GMP, eliminating the need for the sealing structure at the oil entry, with the entry and casing having a clearance fit. The stator cooling only sprays oil around the windings from the top, and there are no dedicated rotor oil holes to spray oil on the inner windings.
The image below shows a temperature sensor embedded within the stator near the oil-cooling channel. This location is designed to provide accurate temperature data, as external temperature measurements would be less effective for overall thermal control.
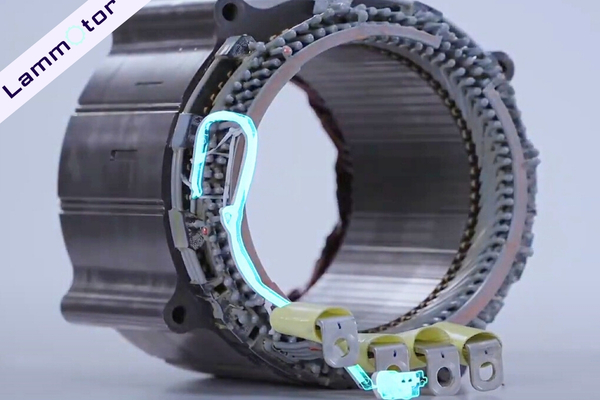
Stator Windings:
BYD, Tesla, and Huawei each have unique stator winding technologies for electric vehicles.
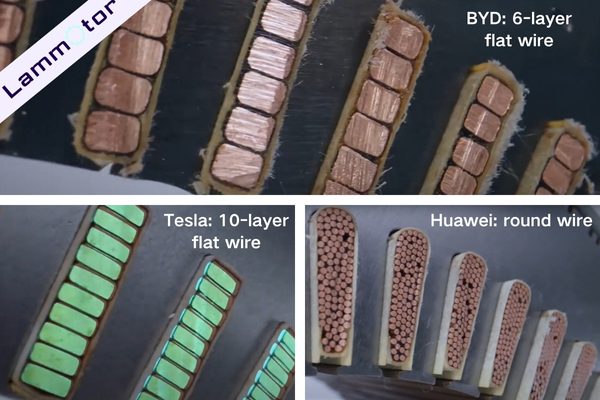
BYD uses a 6-layer flat wire coil design. This structure increases the motor’s fill factor, improving efficiency and heat dissipation.
Tesla uses a 10-layer flat wire coil, which further increases current density, giving the motor an advantage in high-power output applications, particularly for strong acceleration needs.
Huawei uses a traditional round copper wire design. While the fill factor is not as high as flat wire, this structure is simpler to manufacture and offers cost advantages.
These differences reflect the various technical trade-offs each brand has made in terms of motor performance, cost control, and heat dissipation.
Slot Fill Factor:
BYD’s 6-layer flat wire coils occupy a higher percentage of the slot, resulting in a higher slot fill factor and stronger magnetic fields, leading to greater motor power.
Tesla’s 10-layer flat wire coils have more coils, but each layer is insulated with varnish, so the slot fill factor is lower. However, the increased coil count results in a larger surface area for current, helping to increase motor power.
Advantages of Flat Wire Windings Over Traditional Round Copper Wire Windings:
1. Higher Fill Factor:
Flat wire has a shape closer to a rectangle, allowing it to be packed more tightly in the stator slots, reducing gaps and improving the fill factor. This means more copper material is used to conduct current, increasing power density and efficiency.
2. Better Heat Dissipation:
Flat wire has a larger surface area and better contact with the slot walls, enhancing heat dissipation, preventing overheating, and improving motor stability and lifespan.
3. Lower Electrical Loss:
Flat wire has a larger cross-section, reducing resistance and improving efficiency during current conduction, reducing energy loss. This is especially important for high-efficiency motors, enhancing overall power output.
Rotor Technology Comparison
Rotor Laminations:
In rotor lamination stacking technology, BYD, Huawei, and Tesla all use a “interlocking + welding” connection design.
The rotor generates eddy currents when cutting the magnetic field, and welding and point-locking designs create eddy current loops throughout the rotor, increasing iron loss and heat generation. The stator laminations use the same design, but the outer layers of the stator dissipate heat more quickly.
The rotor’s permanent magnets are sensitive to heat, and high temperatures can cause irreversible demagnetization.
However, BYD uses thinner laminations (0.20mm electrical steel laminations) to reduce iron losses from a different angle.
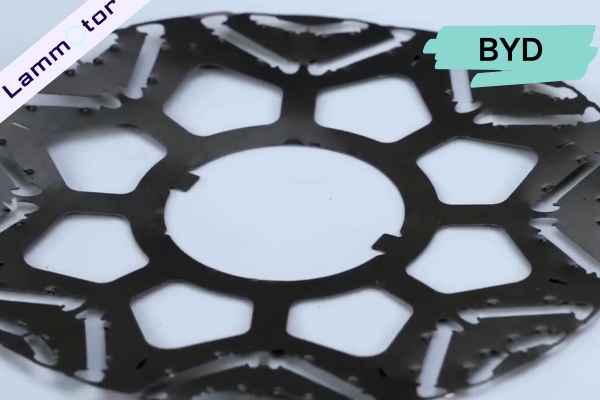
Tesla and Huawei use thicker laminations (0.28mm and 0.25mm electrical steel laminations).
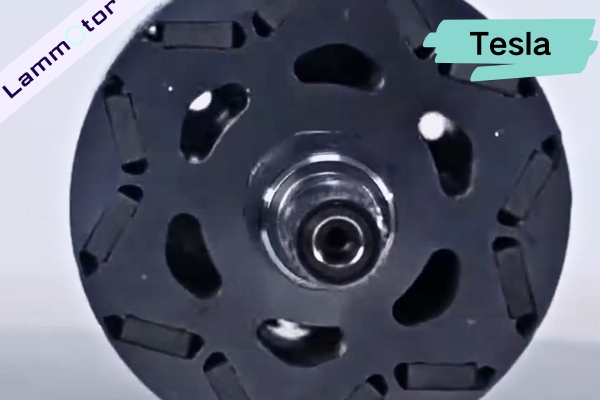
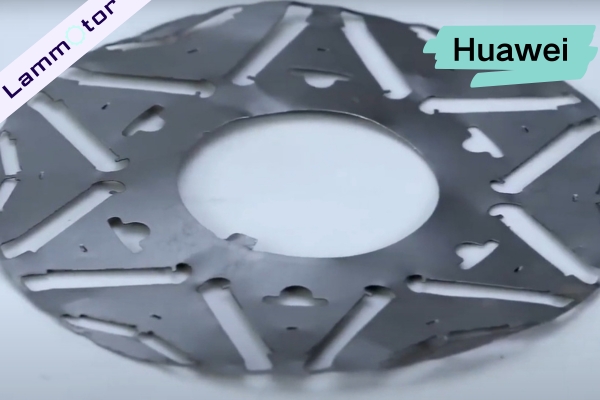
Permanent Magnets:
All three companies use permanent magnets in their rotors, which is a common feature of permanent magnet synchronous motors.
Both BYD and Tesla use sintered neodymium-iron-boron (NdFeB) permanent magnets with regular shapes.
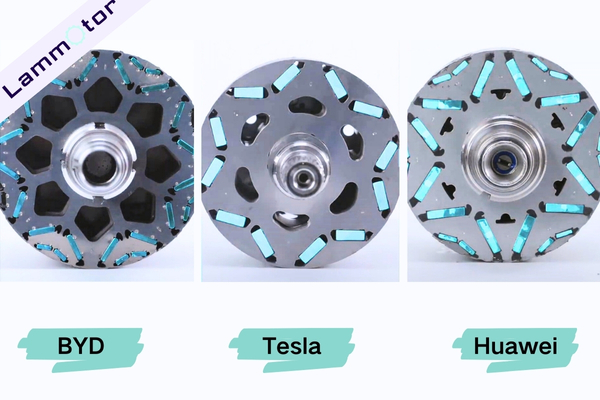
Huawei uses block-style permanent magnets. The two sides of the magnets are bonded with adhesive to secure the magnets and prevent them from loosening or falling off.
However, Huawei’s adhesive is not magnetic, unlike Lucid Air’s magnetic bonding permanent magnets.
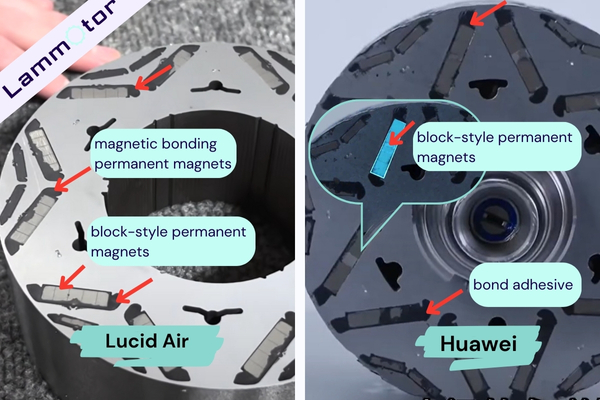
Lucid Air embeds or casts magnetic bonding permanent magnets into V-shaped gaps, forming a hybrid sintered/adhesive magnet. This increases the volume of the permanent magnet, improving magnetic flux and the bonding strength between laminations. They call this technology “Hybrid Rotor Assembly.”
Quiet Slot Design:
Noise control is crucial in electric vehicles, especially at high speeds.
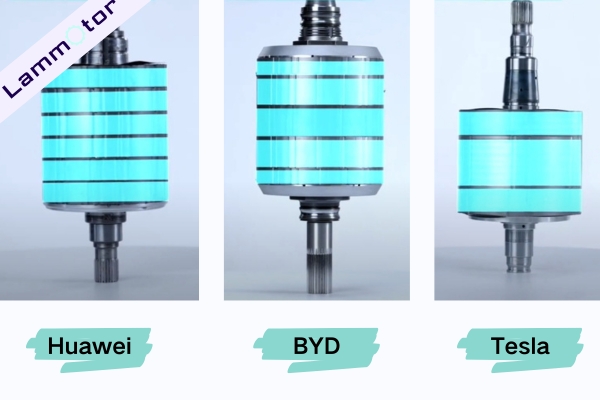
Tesla’s 3D6 rotor uses a classic single-V permanent magnet structure with a three-segment noise-optimization method, where the middle segment is twice as wide as the two edges.
Tesla’s previous-generation motor rotor had very detailed noise-optimization auxiliary slots on the rotor’s sides, divided into high and low types. Large auxiliary slots are placed at the surface of the V-shaped magnetic steel groove, while small auxiliary slots are near the center of the poles. The 3D6 rotor simplifies this design to a single-radius quiet slot.
BYD’s rotor uses a 6-segment design (with the middle coarse segment considered as two stages, appearing as five segments but actually six). It has a detailed pole-pitch design and more direct oil passage design for better cooling.
Huawei, like BYD, uses a 6-segment rotor. Its cooling capacity is similar to BYD’s, but the oil passages are filled with adhesive, resulting in slightly less effective cooling.
Rotor Oil-Cooling of Tesla, BYD, and Huawei:
Similar to stator oil cooling, rotor oil cooling plays a critical role in ensuring the permanent magnets do not demagnetize under high temperatures.
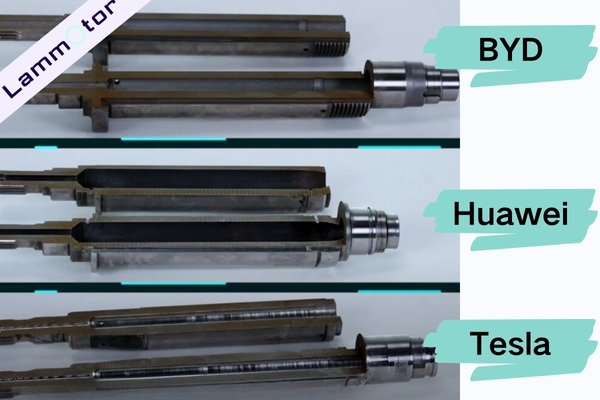
All three companies use through-hole hollow structures for their rotor oil passages.
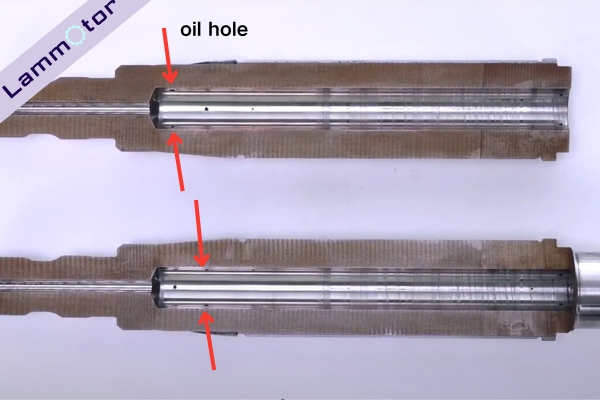
Tesla, BYD, and Huawei have similar oil-cooling methods, but BYD’s oil passage design flows coolant around both sides of the permanent magnets, improving cooling efficiency.
Tesla and Huawei’s oil passages mainly pass through the central weight-reduction holes.
Contact us for Manufacturing EV Motor Stator and rotor Cores.
By comparing the differences in stator and rotor technologies between Tesla, BYD, and Huawei, we can see that each company has made different choices and innovations to improve the performance and user experience of electric vehicles.
Whether it’s an efficient cooling system or a precise rotor design, advances in motor technology continue to drive the electric vehicle industry to new heights.
So, which company’s motor technology do you think is more in line with the future development trend of electric vehicles?
Feel free to share your thoughts and experiences in the comments section. Let’s discuss more.
If you need custom new energy motor stators and rotors, feel free to contact us. We are a professional motor core manufacturer in China with many years of experience, offering sample and mass production of stator cores.