Why are more electric vehicle (EV) manufacturers turning to flat wire winding for their motors?
Flat wire motor is a new type of drive motor. Its wire is flat instead of round. But it is not a new thing. It has appeared in the industrial field decades ago.
However, the use of flat wire motors in new energy vehicles has only been in recent years. So, how does the flat wire motor work? How does it achieve those advantages? Next, this article will introduce the flat wire motor in detail from multiple aspects.
What is Flat Wire Winding?
Flat wire motor is not a new concept. It has a long history of development, decades. Initially, it was mainly used in high-power motors and generator sets in the industrial field, because these occasions have high requirements for the power and efficiency of motors.
Later, the new energy vehicle industry gradually emerged, and flat-wire motors began to be used in the vehicle field. Many application functions on vehicles use flat wire motors, such as automotive generators, starters, EPS (electric power steering) motors, main drive motors, P2 (parallel hybrid) system motors, etc.
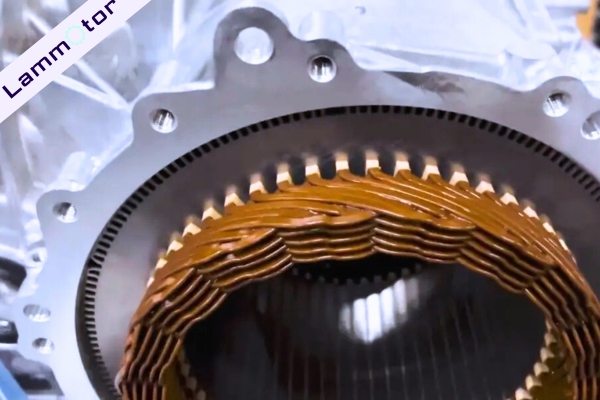
Flat wire winding involves using flat, ribbon-like wires instead of traditional round wires in electric motor windings.
This design increases the surface area for better heat dissipation and allows for a more compact, space-saving motor design.
Flat wire winding also reduces electrical resistance, improving overall motor efficiency. At present, most manufacturers use hairpin conductor structures to manufacture flat wire motors.
By optimizing these aspects, flat wire winding enhances the performance and longevity of electric vehicle (EV) motors, making them more reliable and efficient.
This technology is becoming a cornerstone in the evolution of high-performance EV motors, driving advancements in the industry.
Flat Wire Winding vs. Round Wire Winding
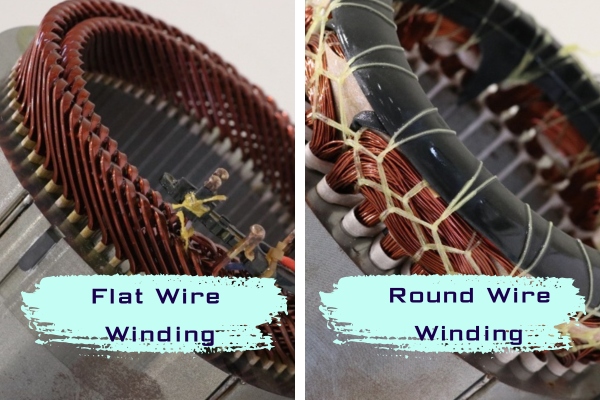
Efficiency: Flat wire winding reduces electrical resistance, resulting in higher efficiency compared to round wire winding. This means less energy loss and better overall performance.
Heat Dissipation: The increased surface area of flat wires allows for superior heat dissipation, which helps in managing the thermal load and prolonging motor life.
Space Utilization: Flat wire winding offers a more compact design, saving space within the motor. This can lead to lighter and more streamlined electric vehicles.
Manufacturing Complexity: While flat wire winding offers numerous benefits, it is more complex and expensive to manufacture than traditional round wire winding.
Durability: Flat wire winding enhances the durability and reliability of the motor by reducing hotspots and potential failure points, ensuring consistent performance over time.
Advantages of Flat Wire Winding in EV Motors
So, what are the advantages of flat wire motors in new energy vehicles? Next, we will analyze the following aspects:
1. Higher Slot Fill Factor:
Generally, the slot fill rate of round wire motors is about 40%, while the slot fill rate of flat wire motors can reach more than 60%. Flat wire motors use copper strips instead of copper wires, increasing the amount of copper conductor in the slots. This enhances the slot fill factor, reducing magnetic field leakage and reluctance, thereby boosting magnetic flux and torque.
2. Greater Power and Efficiency:
Due to the higher slot fill factor, flat copper wire motors can deliver more power in the same or smaller size and weight. This is crucial for electric vehicles, as it means saving space and costs while enhancing energy efficiency and driving range.
3. Lower Noise and Vibration:
Noise and vibration comfort refer to the motor’s operational noise or vibration impact on user comfort. Flat wire motors, with their higher slot fill factor, perform more efficiently under low-speed, high-torque, or high-speed, low-torque conditions. This results in reduced noise and vibration due to less variation in rotational speed.
In summary, compared with round wire motors, flat wire motors have the advantages of high slot fill rate, high power density and efficiency, good noise and comfort.
These advantages make flat wire motors have broad application prospects and market potential in the field of new energy vehicles. So, how do flat wire motors achieve these advantages? What is its manufacturing process?
Manufacturing Process of Flat Wire Winding
Material Selection: The process begins with selecting high-quality copper flat wires. These materials are chosen for their excellent electrical conductivity and mechanical properties.
Wire Preparation: The selected flat wires are cleaned and coated with insulation material to prevent short circuits and enhance durability. This insulation can be applied through various methods such as enamel coating or wrapping with insulating tapes.
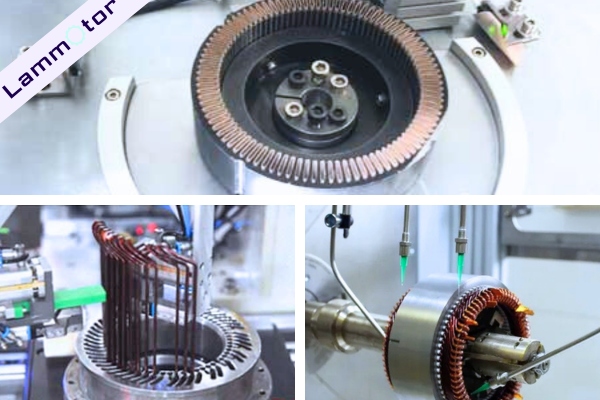
Slot Insulation: The motor slots are insulated to ensure there is no electrical contact between the winding and the motor core. This step involves inserting insulating materials, like paper or plastic liners, into the slots.
Winding Process: The insulated flat wires are then wound onto the motor core using specialized winding machines. These machines are designed to precisely place the flat wires in the slots, ensuring maximum slot fill and minimal gaps.
Interconnection: Once winding is complete, the individual windings are interconnected to form the motor’s electrical circuit. This step involves soldering or welding the wire ends to create a continuous electrical path.
Impregnation and Curing: The wound motor is then impregnated with varnish or resin to secure the windings and improve thermal conductivity. The motor is then cured in an oven to harden the resin, ensuring the windings are firmly in place.
Final Assembly and Testing: After curing, the motor is assembled with other components such as bearings and housings. The finished motor undergoes rigorous testing to verify its electrical and mechanical performance before being packaged and shipped.
This step-by-step process ensures the production of high-quality, reliable flat wire winding motors, ready for use in electric vehicles.
Application of Flat Wire Motors in The New Energy Vehicle Industry
Speaking of the development history of flat wire motors, Chevrolet and Toyota were the first car manufacturers to adopt flat wire motors. With the development and popularization of flat wire motors in China, many new energy vehicle companies, such as Tesla, SAIC New Energy, Zeekr, and BYD, have also begun to gradually apply flat wire motors.
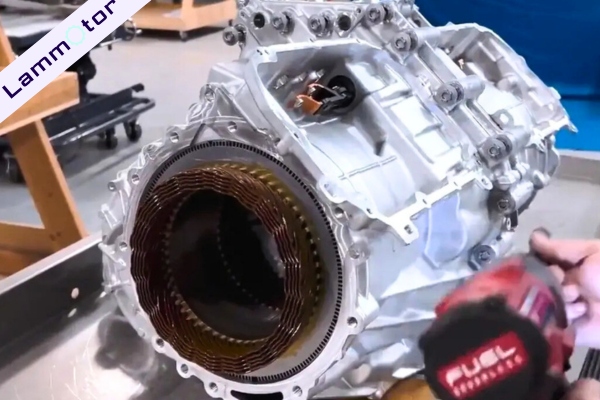
Compared with round wire motors, flat wire motors have the advantages of high slot fill rate, high power density, high efficiency, small size, high efficiency, strong thermal conductivity, low-temperature rise, and low noise.
According to relevant data, flat wire motors are 10% more energy efficient than round wire motors.
According to Chen Guo, an integrated development engineer at BYD, “The new models produced by BYD use flat wire motors.”
It is understood that various OEMs have been intensively deploying flat wire motor business, and best-selling models such as Tesla Model 3/Y, BYD DM-i, BYD Qin PLUSEV, Volkswagen ID.4 and Zeekr 001 are already equipped with flat wire motors.
Conclusion
Stator flat wire winding in EV motors offers significant advantages in efficiency, power, and noise reduction. By improving slot fill factor and enhancing heat dissipation, this technology leads to more powerful and reliable motors. From space-saving designs to quieter operations, the benefits are clear.
Ready to supercharge your electric vehicle projects? Contact us today to discuss custom flat wire winding motor stators tailored to your specific needs. Let’s drive the future of EV technology together!