Have you ever wondered what kind of motor an eVTOL (Electric Vertical Takeoff and Landing aircraft) uses to fly smoothly and efficiently? The choice of motor directly affects the performance of the aircraft. In this article, we will discuss the different types of motors used in eVTOLs, their advantages, and which ones are most suitable for these futuristic flying vehicles.
Currently, eVTOLs (Electric Vertical Takeoff and Landing aircraft) primarily use the following types of electric motors, each with different advantages depending on their characteristics and applications:
1. Permanent Magnet Synchronous Motor (PMSM)
eVTOL aircraft requires motors with high efficiency and torque density, making permanent magnet synchronous motors (PMSM) a promising solution for electric propulsion systems.
Compared to DC motors and induction motors, PMSMs have high power density, a wide speed range, and strong electromagnetic torque. Their ability to maintain full torque is especially useful for eVTOLs during takeoff and landing.
Current electric vertical takeoff and landing aircraft, such as the Joby S4, Archer, and Midnight, all use PMSM.
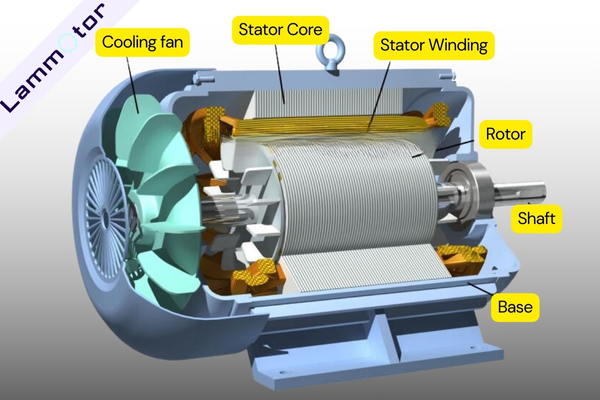
Features:
- High power density and efficiency, ideal for lightweight designs.
- Uses rare-earth magnets (such as neodymium-iron-boron) with strong magnetic fields and low losses.
- Sine wave control for smooth operation, perfect for precise speed control.
Advantages:
- Maintains high efficiency at partial load, ideal for long-duration flights.
- Compact size, suited for multi-motor configurations in distributed propulsion systems.
Application Cases:
- eVTOL models from companies like Joby Aviation and Archer Aviation widely use PMSM.
- EHang’s manned drone also utilizes similar technology.
2. Brushless DC Motor (BLDC)
Brushless DC motors (BLDC) are also widely used in eVTOLs due to their efficiency, reliability, and durability.
Features:
- Trapezoidal wave drive, simple structure, and relatively easy control.
- High startup torque, suitable for quick response scenarios (such as vertical takeoff and landing).
Advantages:
- Low maintenance cost (no brush wear), highly reliable.
- Generally lower cost than PMSMs, suitable for medium and small eVTOLs.
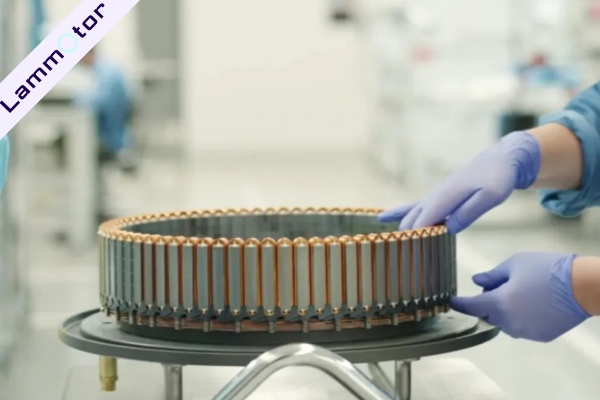
Application Case:
EHang: EHang’s 216 autonomous eVTOL uses BLDC motors as the main propulsion system. The brushless motors provide reliable power, enabling safe, quiet flights, especially during short flights in urban environments.
3. Axial Flux Motor (AFM)
Axial flux motors (AFM) offer significant advantages for eVTOL applications, making them the preferred motor type for many aerospace companies and electric aircraft manufacturers.
Advantages of Axial Flux Motors in eVTOL:
- High Power Density: Axial flux motors typically offer more than 30% higher power density than traditional radial motors, allowing more power in a smaller, lighter package.
- Compact and Lightweight Design: The magnetic field in axial flux motors extends along the axis rather than radially, making the design more compact and reducing material usage, achieving a lightweight goal.
- Higher Efficiency: The simple structure and shorter magnetic path in axial flux motors reduce energy loss, improving the eVTOL’s range and endurance, especially with limited battery life.
- High Torque Density: Axial flux motors provide stronger torque output in smaller sizes, ideal for eVTOLs that need high thrust and high speed.
- Cooling and Thermal Management: Due to their smaller size, axial flux motors generate less concentrated heat, providing better thermal management during long operations. This allows the motor to operate efficiently for extended periods, making it suitable for demanding flight applications.
- Low Noise: Compared to traditional electric propulsion systems, axial flux motors generate less noise due to their structural advantages. This is particularly important for eVTOLs operating in urban air mobility (UAM) applications, as low noise reduces environmental impact.
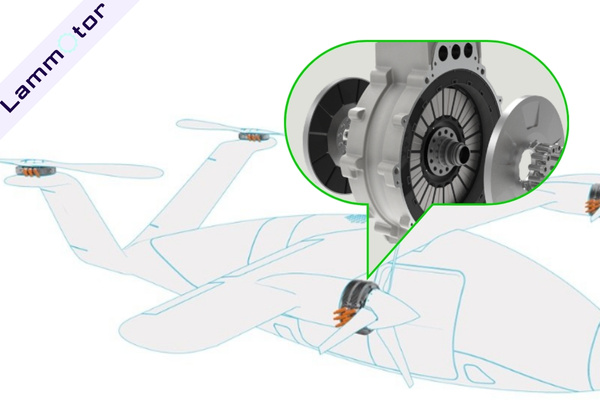
Application Cases:
- Magnax: The AXF225 axial flux motor developed by Magnax in Belgium demonstrates excellent performance. With higher coil density, up to 98% efficiency, and a weight of just 16 kg, it can reach a peak power of 200 kW. Its peak torque of 250 Nm is significantly better than the radial motor used in the BMW i3. Although not yet widely used in large aircraft, its performance indicates great potential for small aircraft in the future.
- EHang: China’s EHang also utilizes axial flux motors in their eVTOL development. The motor’s high power density and lightweight design help EHang’s aircraft improve efficiency while maintaining a lower weight.
- Vertical Aerospace: The VA-X4 eVTOL from Vertical Aerospace uses axial flux motors to achieve higher power output and lower weight. This aircraft is expected to enter commercial operation in the coming years, with the use of axial flux motors significantly boosting performance.
- Lilium: Lilium’s Lilium Jet, an electric vertical takeoff and landing aircraft, uses high-power-density axial flux motors. These motors’ efficiency and compactness are key to achieving Lilium’s goal of seamless urban air mobility.
If you have more questions or insights about the choice of motors for eVTOLs, feel free to leave a comment below. Let’s discuss and share more ideas and experiences together!