Did you know? The Tesla Model S Plaid and Lucid Air motor, as two of the top performers in today’s electric vehicle market, not only compete in speed and acceleration but also showcase different motor technologies behind them.
The Model S Plaid is equipped with three drive motors, delivering a total power of 1020 horsepower. It can reach a top speed of 322 km/h and accelerate from 0 to 100 km/h in just 2.1 seconds. On the other hand, the Lucid Air has a robust output of 1111 horsepower, achieving 0-100 km/h in just 2.6 seconds, with an impressive driving range of 836 kilometers.
So, what are the differences in their motor technologies? Which vehicle has the more forward-thinking design? In this article, we will dive into the stator and rotor technologies of both vehicles, comparing their core motor technologies in detail.
If you’re interested in electric vehicle motor technology, you may also want to check out our other articles: “Comparison of Motor Stator and Rotor Technologies of Tesla, BYD, and Huawei” and “Tesla Model 3 Motors: Induction Motor and Permanent Magnet Synchronous Motor”, for more insights into motor technology!
Stator Technology Comparison
Stator Laminations:
The design of the stator laminations in the Lucid Air and Tesla Model S Plaid differs.
Lucid Air: It uses 0.25mm thick laminations, with 72 slots and around 462 laminations stacked. The design incorporates four different shapes of laminations, all stamped from the same mold to form the stator core structure. Additionally, the cooling system inside the stator is cleverly positioned in the center of the lamination stack to optimize heat dissipation.
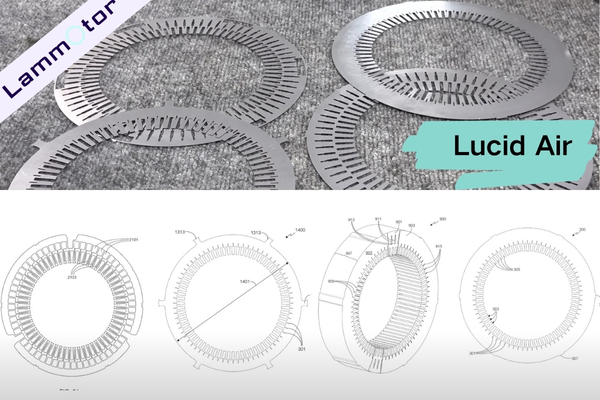
Tesla Model S Plaid: In comparison, the Tesla Model S Plaid also uses 0.25mm thick laminations but only has 54 slots and uses a single lamination shape. This simplifies the manufacturing process but still retains a similar cooling system design, where the cooling manifold is located at the center of the stack.
Stator Windings
Tesla Model S Plaid Stator Winding: Round Wire Winding
The Model S Plaid is the first and only Tesla vehicle to feature three drive motors—one in the front and two to independently drive the rear wheels.
The stator of the Model S Plaid uses traditional round wire windings, a simpler and more cost-effective winding design. The round wire manufacturing process is mature, simpler, and cheaper than flat wire. Additionally, round-wire manufacturing is more scalable and has less waste, which helps reduce production costs.
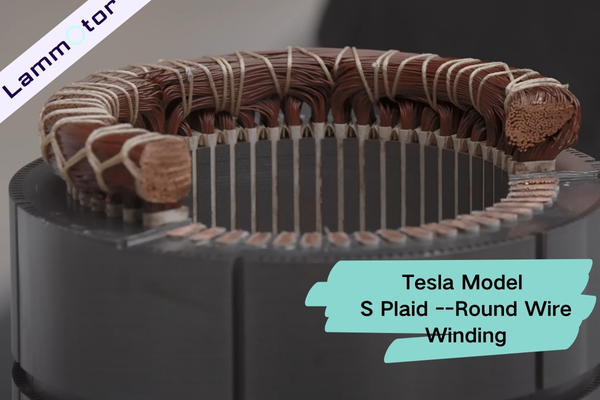
However, the height of the windings at the ends, especially at the bottom, is about 40mm, and the design is tied with string, in contrast to the more automated and precise winding processes used in the Lucid.
Lucid Air Stator Winding: Continuous Wave Winding
In stator winding, Lucid Air outperforms the Tesla Model S Plaid.
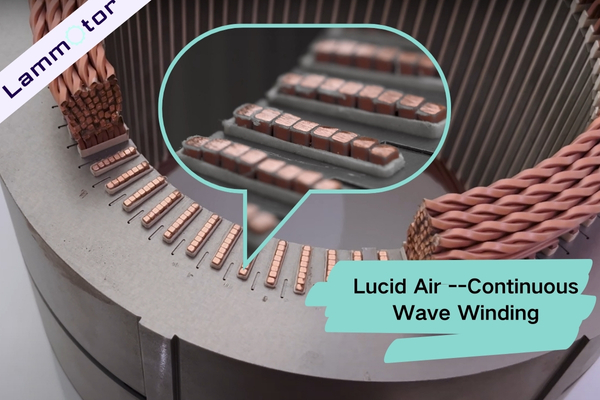
Lucid Air uses continuous wave windings, also known as W-pin windings (Continuous hairpin/wave winding), abbreviated as W-pin.
Compared to other winding types, the W-pin winding shortens the stator length by about 30%, but increases torque density by more than 50%.
Additionally, the W-pin winding has a higher space utilization rate compared to hairpin windings, making it more suitable for the current trend of 800V oil-cooling technology.
W-pin windings can be made in two forms: full-wave and segmented-wave. After forming, the ends of the windings don’t need to be welded, and the winding ends are lower. The W-pin winding design is particularly suitable for multi-slot, multi-layer motor designs.
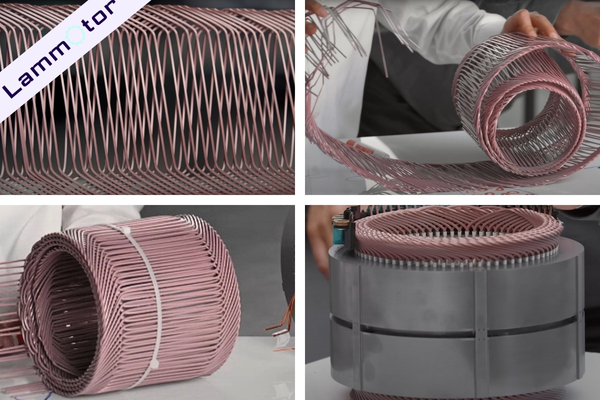
Lucid first individually wound and then embedded into the stator core to create a complete stator. Each stator slot contains 8 flat wires, and in the end, Lucid’s stator has only 24 solder points connected to the inverter. The process is fully automated, ensuring consistency in the product.
Stator Oil Cooling
Lucid Air Stator Oil Cooling:
The stator laminations in Lucid’s motor feature small holes, creating micro channels. These holes form cooling oil pathways closer to the copper windings, resulting in more efficient heat dissipation.
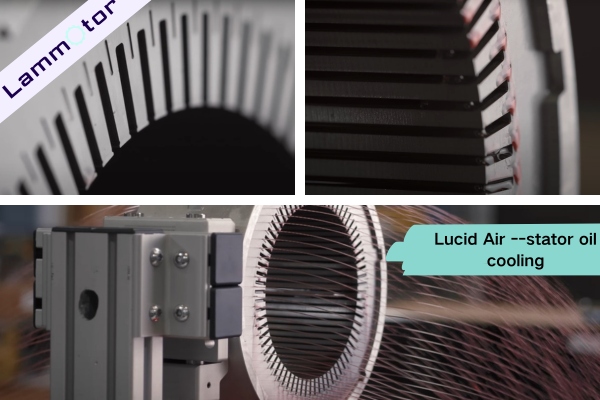
The holes vary in size, forming different-sized oil channels inside the stator. This design helps direct the coolant flow, especially at the stator ends, where the holes are smallest to precisely spray the coolant onto the copper windings.
Lucid’s oil cooling system uses axial spray technology instead of the radial oil spray method used by Tesla. The axial spray technology uses large-flow micro-spray coolant channels, which directly spray the coolant onto the stator winding surface for faster and more efficient cooling.
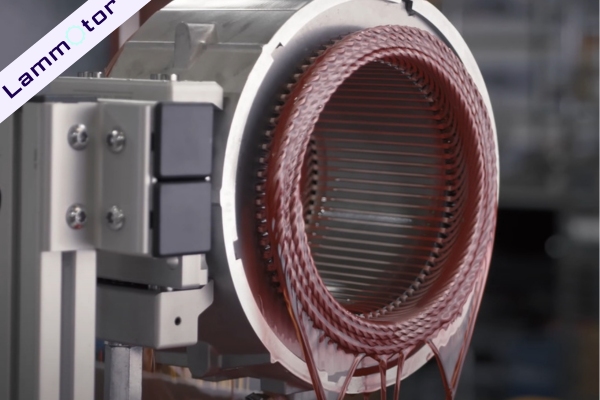
The core technology of Lucid electric oil cooling is that they find the Dead Zone in the motor. That is, after mathematical modeling of the electromagnetic field inside the motor, it is found that there are several areas in the stator that are not helpful for conducting electricity, but the Lucid motor cleverly uses these Spaces and arranges cooling pipes in them.
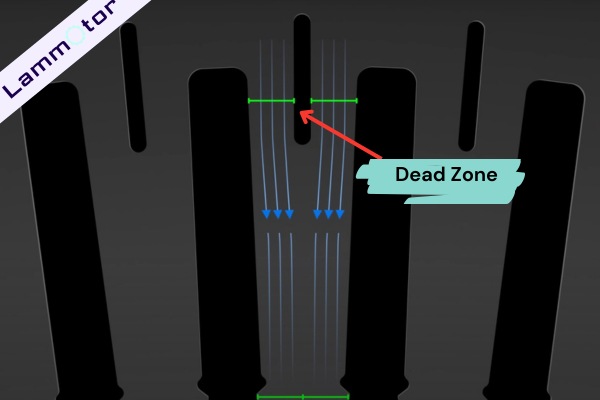
Compared to Tesla’s cooling design, this method doesn’t require additional oil channels in the yoke area, which reduces the motor’s weight and brings the coolant flow closer to the stator windings, improving cooling efficiency.
Lucid Oil Cooling Advantages:
Larger contact area: Axial spray technology allows the coolant to directly contact the winding surface, significantly increasing the contact area and enhancing cooling efficiency.
Reduced flow resistance: Axial flow results in lower resistance compared to radial flow, allowing smoother coolant flow and better cooling.
Avoid unnecessary water resistance: Direct spraying avoids unnecessary resistance from the oil flowing through the ring.
Cost reduction: Lucid’s axial spray technology eliminates the need for additional oil ring components, lowering system costs.
Lucid Oil Cooling Disadvantages:
Oil channel resistance: The oil channels between the teeth may experience resistance due to the windings, requiring a certain coolant flow rate to maintain cooling efficiency.
Clogging risk: During painting, the small oil holes in the teeth may get blocked, which is difficult to clean.
Tesla Model S Plaid Stator Oil Cooling:
Tesla’s design features square oil holes in the stator core’s yoke to allow coolant to flow directly into the core. This design avoids the complexity of external oil pathways and reduces the cost of casting.
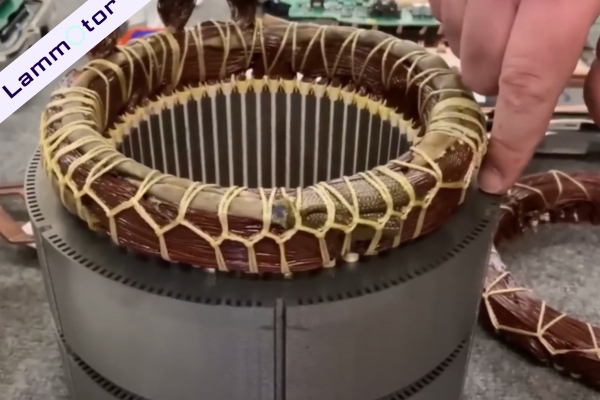
While this design simplifies the oil pathways and offers uniform cooling, it is slightly less efficient than Lucid’s design.
This is because Lucid’s oil cooling holes are closer to the copper windings, enabling faster and more effective cooling.
Rotor Technology Comparison
Lucid Rotor: Hybrid Rotor Assembly
The Lucid rotor has a 6-pole, dual-V structure, designed to increase magnetic reluctance torque. The rotor is made of two rotor cores and balance plates at both ends, riveted together.
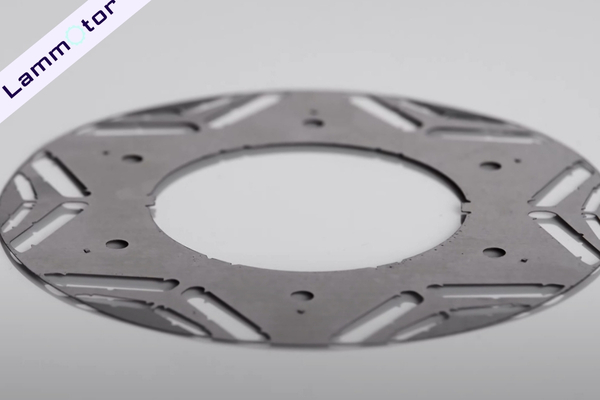
It uses Hybrid Rotor Assembly technology, which maximizes space utilization in the rotor laminations. This technology fills the V-shaped slots of the rotor laminations with sintered permanent magnets and bonded permanent magnets.
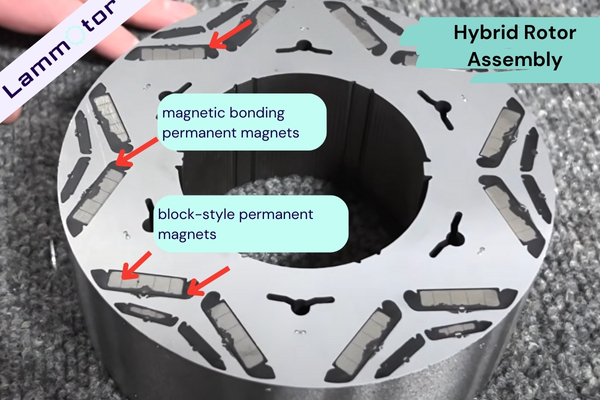
First, sintered rectangular permanent magnets fill the larger spaces, and then adhesive is used to bond permanent magnet powder to fill the remaining spaces.
This increases the volume of the permanent magnets, enhances the magnetic flux, and ensures a tighter contact between the permanent magnets and the laminations.
Tesla Model S Plaid Rotor:
The Plaid rotor uses 529 laminations, shaped in a star pattern. It transitions from traditional round silicon steel sheets to a combination of star-shaped silicon steel sheets in the center and curved silicon steel sheets at the edges.
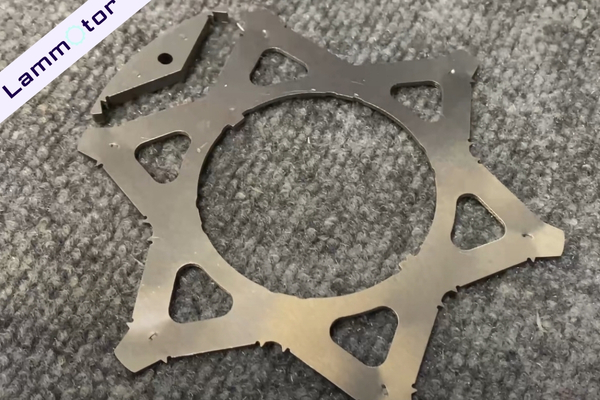
As we know, the permanent magnets inside the Tesla rotor are in a single-V structure and are embedded within the rotor laminations. The permanent magnets are held in place entirely by the strength of the laminations.
When the rotor spins at high speeds, greater centrifugal force requires a stronger fixation. Otherwise, the magnetic bridge at the rotor’s edge may break under pressure.
The design of the magnetic bridge is a contradiction. If it is made thicker to secure the permanent magnets, it would create a local closed magnetic field. This magnetic field would be trapped inside the rotor and unable to interact with the stator’s magnetic field, leading to magnetic leakage.
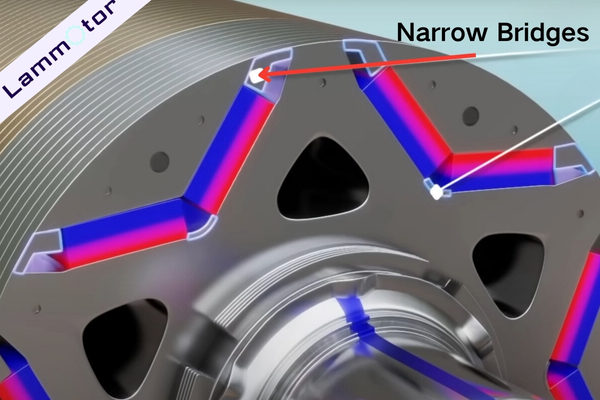
The Tesla Model S Plaid adopts a bold design by eliminating the magnetic bridge. Instead, it cleverly uses the laminations to create a baffle structure. The ends are fixed to balance plates with locating pins, and rivets are inserted in the middle to form a stable structure.
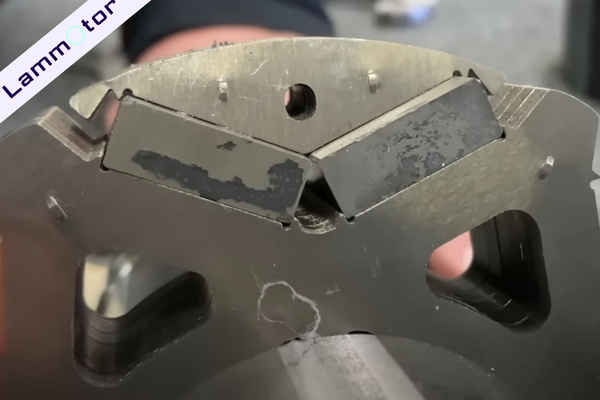
Additionally, the rotor is wrapped in carbon fiber material, ensuring that the entire structure won’t expand due to ultra-high rotational speeds.
Magnetic Bridge’s Function:
In permanent magnet synchronous motors, the magnetic bridge is used to secure the permanent magnets inside the rotor and prevent them from detaching due to centrifugal force during high-speed rotation. However, the magnetic bridge can cause magnetic flux leakage, reducing the efficiency of the permanent magnets and the motor overall.
Carbon Fiber Wrapping Technology
The Tesla Model S Plaid, which can accelerate from 0 to 100 km/h in 2.1 seconds and reach a top speed of 322 km/h, owes its performance to the three motors that use an innovative carbon fiber sleeve rotor, capable of achieving a maximum speed of 20,000 RPM.
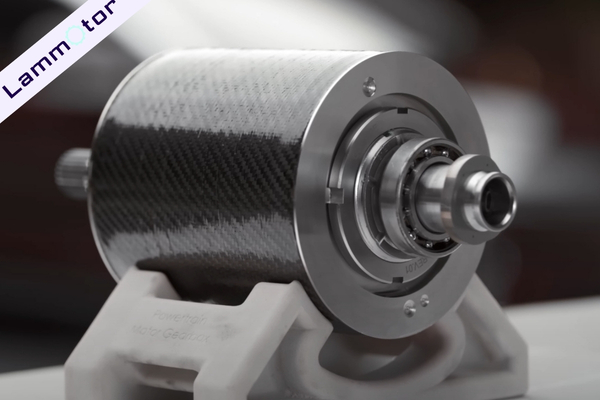
Tesla has added a carbon fiber sleeve around the rotor.
The carbon fiber serves two main purposes:
Effective temperature reduction: A large portion of the rotor’s temperature comes from the stator. The carbon fiber effectively reduces heat conduction, reducing the risk of magnet demagnetization and minimizing centrifugal deformation at high speeds.
Increased rotor magnetic flux: With the same input current, the motor’s speed increases, the work done increases, and efficiency improves.
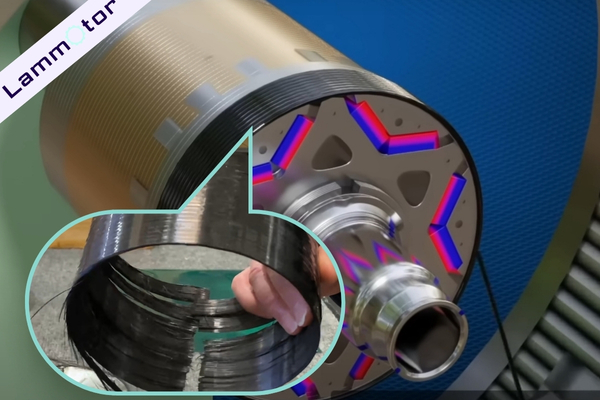
At the same speed, a carbon fiber sleeve rotor motor generates more torque than traditional motors, and by eliminating structures like the magnetic bridge, it can produce greater magnetic flux and higher peak torque.
Recently, Tesla released the Tesla Cybertruck. If you want to know about the Tesla Cybertruck motor, please click on this link.
Get EV Motor Stator and rotor Cores from Lammotor
After comparing the motor technologies of the Lucid Air and Tesla Model S Plaid, do you understand the unique designs behind them? These motor design details not only reflect the companies’ unique technological approaches but also directly influence the performance of the vehicles.
As a consumer, do you prioritize technological innovation or cost efficiency? Feel free to share your thoughts in the comments. If you’re interested in electric vehicle technologies, stay tuned for more professional insights in our future articles!
Also, if you need custom new energy motor stators and rotors, feel free to contact us. We are a professional motor core manufacturer in China with many years of experience, offering sample and mass production of stator cores.