Why aren’t axial flux motors used in all electric vehicles yet, despite their clear power density and efficiency advantages?
While these motors are often touted as the future of electric propulsion, several challenges are slowing their widespread adoption in electric vehicles.
In this blog, we’ll explore why axial flux motors, despite their impressive potential, are not yet commonplace in all EVs.
If you would like to dive deeper into the benefits of axial flux motors and learn more about top manufacturers in the field, be sure to check out our other posts: Axial Flux Motor vs Radial Flux Motor and Top 9 Axial Flux Motor Manufacturers.
Technical Challenges of Axial Flux Motors in Electric Vehicles
Although axial flux motors offer significant technical advantages and have made great strides over the years. However, large-scale application is still some time away, and design and manufacturing challenges must be overcome.
Manufacturing Equipment is Underdeveloped
Due to a lack of research and accumulation, the industry has limited knowledge about the manufacturing methods for axial flux motors. Manufacturing equipment is hard to obtain, and the supply chain is not well-established.
High Manufacturing Precision Requirements
There are usually two air gaps in the single-stator, dual-rotor topology: one between the first rotor disc and the stator, and another between the second rotor disc and the stator.
A uniform air gap between the rotor and stator is crucial for optimizing NVH (Noise, Vibration, and Harshness). Since radial flux motors only have one air gap, it’s easier to control this uniformity in radial flux motor topologies.
For axial flux motors, it is essential to maintain an even air gap between the rotor and stator because the magnetic forces are much stronger than in radial flux motors.
Considering that adjusting the air gap in the manufacturing process of axial flux motors is difficult, precise control over the manufacturing tolerances of key components is needed.
How to Fix the Segmented No-Yoke Stator Core
This technical challenge is related to the no-yoke axial flux motor. The stator yoke is typically the ring-like structure that connects the stator core parts. By removing the stator yoke, the magnetic flux path becomes more direct, reducing additional magnetic losses caused by the yoke.
So, without a stator yoke, how can the stator teeth be fixed?
YASA solves this with a “fixed plate” structure, as shown in the image below. This part is made of plastic material. It’s called “Clam shells.”
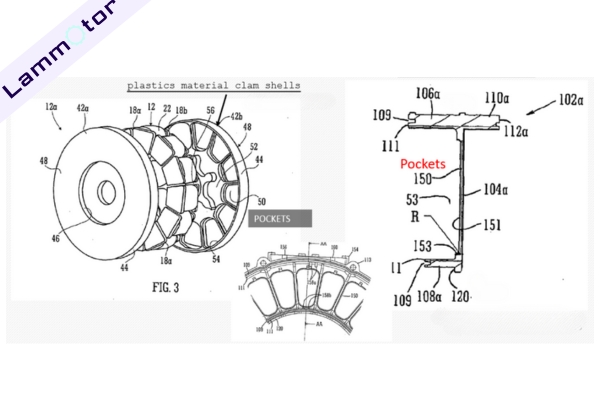
As the name suggests, it is a supportive structure that wraps around the stator teeth. The wrapping is done by several pockets, each containing a stator tooth structure, which helps with the positioning and fastening of the stator.
Its supporting function is evident in how the outer wall of this fixed plate fits with the motor housing and the inner wall fits with the bearing chamber, providing structural support throughout the motor.
Heat Management and Thermal Design Challenges
Axial flux motors adopt a sandwich structure, and for dual-rotor axial flux motors with a middle stator and dual-stator axial flux motors with a middle rotor, heat dissipation is difficult. Additionally, due to the high power density of axial flux motors, their thermal capacity is small, which leads to serious overheating issues.
How to cool the motor? This is another challenge.
For radial flux motors, the stator is typically cooled indirectly from the outside through a water jacket in the motor housing.
Newer radial flux motors are cooled using what is called direct oil cooling. Direct oil cooling is more efficient than indirect cooling because it removes heat directly from the heat-generating parts, such as in the permanent magnet motors used in the Tesla Model 3.
For axial flux motors, new cooling methods such as immersion oil cooling, oil-water hybrid cooling, liquid nitrogen cooling, and phase change material cooling need to be employed, along with extremely complex cooling and sealing structures.
Currently, YASA’s axial flux motor uses direct oil cooling technology. The absence of magnetic poles and the segmented armature topology allow the stator core to be fully sealed, and efficient heat dissipation is achieved using oil cooling.
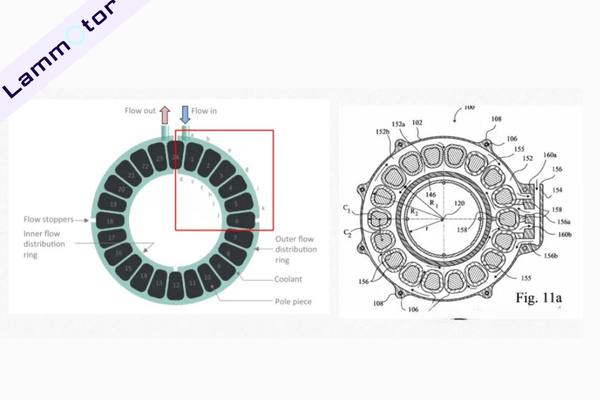
The oil passage design includes inner and outer branch circuits that flow counterclockwise and clockwise, ensuring that every flat wire is fully wrapped by the oil, providing efficient cooling.
Complex Materials and Processes Lead to High Costs
For radial flux motors, the costs of magnets, silicon steel, copper, and structural components, as well as the mass production processes, have been widely recognized in the industry.
However, for the new axial flux motors, the industry is not yet fully aware of the new materials and processes required for their applications. This increases material costs and production costs.
For example, for the stator and rotor cores, high magnetic permeability, low-loss composite materials like Sheet Molding Compound (SMC), amorphous alloys, and oriented silicon steel need to be developed.
For the high-strength stator and rotor requirements, carbon fiber winding and reinforcement processes need to be developed to address the poor tensile strength of permanent magnets.
Additionally, the relevant supply chain and manufacturing equipment may not be fully developed, which affects large-scale motor production and cost efficiency.
Applications of Axial Flux Motors
1. New Energy Vehicles (NEVs)
Axial flux motors are increasingly used in electric vehicles (EVs) due to their superior power density, efficiency, and compact design.
For instance, YASA, a leader in axial flux motor technology, provides motors for high-performance electric cars. Their motors are currently used in vehicles like the Aston Martin Rapide E and other premium EV models, where lightweight, high torque, and efficient energy usage are critical for improving range and performance.
2. Buses
In the electric bus sector, axial flux motors are providing a viable solution for energy efficiency and compact design. Saietta, known for its innovations in axial flux technology, supplies motors for electric buses.
For example, the SE-130 motor is used in Yutong’s electric buses, contributing to a higher energy efficiency rate and enhanced driving range compared to conventional electric motors.
3. Heavy Construction Equipment
In the construction machinery field, axial flux motors are ideal for powering large vehicles such as mining trucks and concrete mixers. For instance, Volvo has implemented axial flux motors in their electric mining truck fleet. These motors provide high torque and efficiency, crucial for the heavy-duty operations in mining environments. Additionally, extended-range generators driven by axial flux motors offer enhanced fuel efficiency and lower emissions for construction equipment.
4. Marine Applications
Saietta’s Propel S1, powered by the AFT 140 axial flux motor, delivers remarkable performance with an overall efficiency of 62%. This technology is essential for reducing emissions and improving the fuel efficiency of marine vessels.
The compact design of axial flux motors allows for easier integration into propulsion systems, optimizing space and reducing the overall weight of the system.
5. Electric Aircraft
In the aerospace industry, axial flux motors have proven to be powerful solutions for electric propulsion. The Spirit of Innovation, developed by ACCEL, is a prime example.
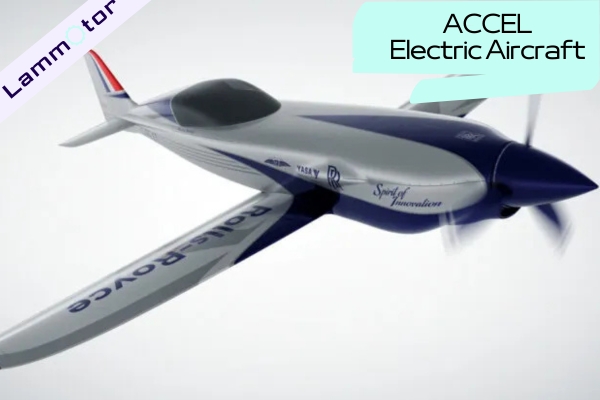
This aircraft, which set the world speed record for a fully electric plane in 2021, is powered by an axial flux motor that produces 400kW of thrust. The high torque density and compact size of the motor enable high-speed, long-range performance, making it ideal for electric aviation.
6. Electric Motorcycles
Axial flux motors are also revolutionizing the electric motorcycle industry, providing greater torque and lighter weight.
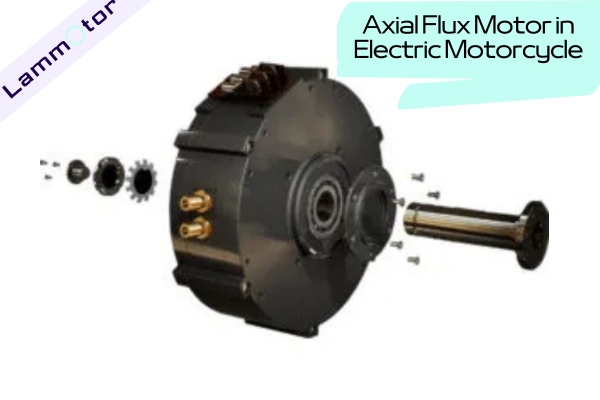
Companies like Norton Motorcycles have incorporated axial flux motors in their Norton V4 RR, achieving significant weight reduction and improving acceleration and top speed.
The increased torque density and efficiency of axial flux motors allow electric motorcycles to perform better than their traditional counterparts, making them an attractive option for both manufacturers and consumers.
7. Electric Bicycles
In electric bicycles, axial flux motors are gaining popularity for their ability to offer high torque while being lightweight and energy-efficient.
GoCycle, a leading electric bike manufacturer, uses axial flux motors in their bikes, allowing for superior acceleration and better battery efficiency.
The compact and lightweight design of axial flux motors makes them particularly well-suited for e-bikes, where performance, weight, and battery life are critical.
8. Robotics
Axial flux motors are transforming robotics by enabling more compact, lightweight designs with higher torque and power density.
For example, Genesis Robotics has achieved good results by using the compact thickness (2cm) of the axial flux motor to mitigate the ground impact force on the joints of the robot’s feet when they contact the ground.
In the field of service robots, Japan’s NIDEC DRIVE TECHNOLOGY uses an axial motor with a thickness of 21mm and a high output of up to 170W to support the start power auxiliary joint, preventing users from being injured by excessive joints when passing through narrow channels.
Contact Us For Manufacturing Axial Flux Stator
In conclusion, while axial flux motors in electric vehicles show immense promise in terms of performance, their adoption is still hindered by factors such as cost, manufacturing challenges, and limited infrastructure.
However, as the technology continues to evolve and these obstacles are addressed, we’ll likely see broader integration of these motors in the EV market. If you’re looking for a professional manufacturer of high-quality axial flux motor stators, we specialize in custom solutions in China. Don’t hesitate to reach out to us for more information or to discuss your project!