Have you heard that Mercedes recently acquired YASA? This acquisition not only highlights YASA’s leadership in electric drive technology but also showcases the huge potential of axial flux motors in the future of electric vehicles.
So, what exactly is an axial flux motor, and how does it compare to traditional motors? In this article, we will delve into the design, features, and applications of YASA axial flux motor. We can help you gain a full understanding of this technology.
In the previous article, we compiled the top 9 axial flux motor manufacturers, if you are interested, you can click on the link. If you want to learn more about how to produce axial flux stator, please check the video and link.
YASA Axial Flux Motor Structure: Single Stator, Dual Rotor
YASA’s electric motor uses a dual rotor, single stator structure, which simplifies manufacturing and supports automated mass production. These motors can achieve a power density of 10 kW/kg at speeds ranging from 2000 to 9000 rpm.
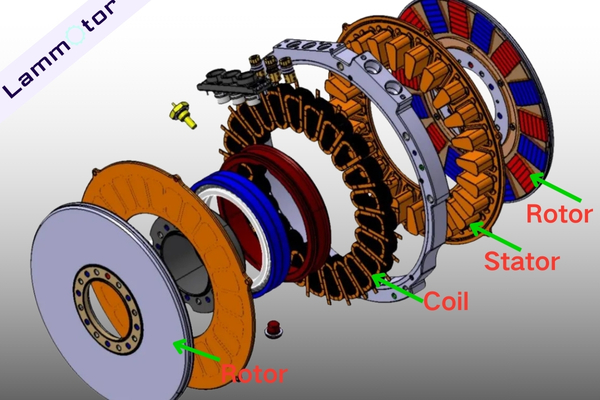
Advantages of the Single Stator, Dual Rotor Design
- Optimized Magnetic Field Path: In the Rotor-Stator-Rotor structure, the magnetic field path is optimized, avoiding the need to pass through the stator’s core. By removing the core, the magnetic circuit becomes more efficient, addressing issues like magnetic saturation in the stator. This reduction in the stator size and weight results in a more compact motor.
- Improved Efficiency: Removing the stator core significantly reduces iron losses, leading to higher efficiency.
- Larger Magnetic Steel Assembly Space: With the rotors placed on either side of the stator, there is more space for additional magnetic steel. As the rotor rotates outside the stator, the effective air gap is larger, increasing the torque produced compared to radial flux motors with the same magnetic material.
Stator Design: Yokeless Segmented Core
YASA’s motors utilize a yokeless segmented stator design, making them some of the smallest and lightest in their class. Compared to traditional motors, YASA’s design uses fewer materials to achieve higher torque and power density, making the motor more efficient.
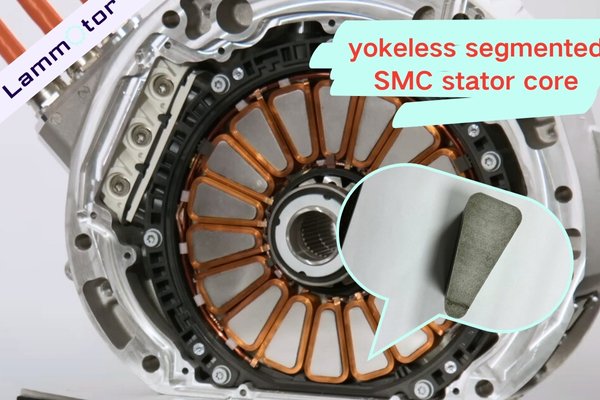
Advantages of Yokeless Segmented Design
- No Core: The absence of a stator core eliminates core saturation and losses, improving efficiency and enabling miniaturization.
- Segmented Structure: This design allows each winding to be independently wound before assembly, facilitating large-scale automated production.
- Tight Winding Design: Independent winding allows for a “wire layout design” that maximizes the use of space, leading to a high slot fill factor. A high slot fill means more copper in the same size, reducing copper losses and further boosting torque density.
YASA Stator Material: Soft Magnetic Composite (SMC)
Traditional axial flux electric motors use a Rotor-Stator-Rotor structure with a core, relying on silicon steel sheet winding techniques. However, YASA has removed the stator core to maximize torque density. This design relies on the maturity of the SMC (Soft Magnetic Composite) stator pressing process.
SMC materials, made from iron powder and insulation coatings, offer good magnetic permeability, low losses, and high electrical insulation properties. They are especially suitable for high-efficiency and high-power-density motor applications.
YASA Stator Windings: Flat Wire
A unique feature of YASA’s yokeless axial flux motor is the fractional-slot concentrated winding, which avoids the hanging portion of the coils. So it makes the windings more compact and efficient.
YASA uses flat wire winding technology, and the windings are grouped and installed on the segmented stator teeth using automated equipment.
The motor has a high slot fill factor, with the copper slot fill rate exceeding 60%, which supports higher torque density.
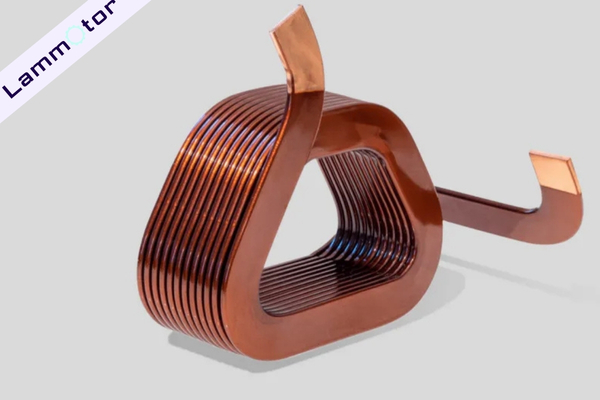
Advantages of Segmented Flat Wire Winding
- Copper Savings: This winding method can save up to 50% by copper. It can reduce copper losses, increase current and torque density, and reduce motor weight.
- Automation-Friendly: This design facilitates automated winding, lowering production costs.
- Suitable for Mass Production: The segmented design is ideal for offline production and parallel manufacturing processes, making large-scale production easier.
- Improved Electrical Performance: The segmented design increases D-axis inductance, improving the motor’s electrical performance and enhancing CPSR (Continuous Power Speed Range) rating.
- Single-Layer Coil Design: Using flat wire for single-layer coils reduces internal thermal resistance, making it better suited for oil-cooling systems.
As we know, increasing power density in a smaller volume means extracting the same amount of heat from a more compact space. To unlock the full potential of the motor, an extremely efficient cooling system is essential.
Therefore, to fully realize the advantages of an axial flux motor, a strong cooling system is crucial.
YASA Axial Flux Motor Oil Cooling Technology
YASA motors use advanced direct oil cooling technology. The yokeless and segmented armature topology allows the stator core to be completely sealed, with oil circulating for efficient heat dissipation.
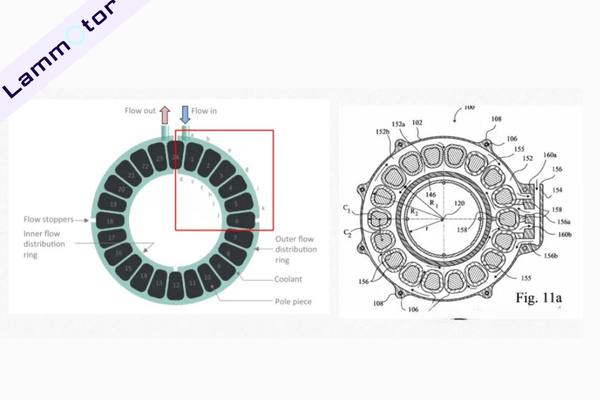
The oil channel design includes inner and outer loops, with counterclockwise and clockwise flow. It ensures that each flat wire is fully surrounded by oil for effective cooling.
This oil-cooling method is more efficient than conventional oil cooling in standard motors.
It not only cools the windings but also cools the stator teeth. Each tooth and winding has multiple surfaces in contact with the coolant, greatly increasing the heat exchange area. The efficient oil-cooling structure significantly enhances torque density.
Additionally, YASA’s design uses dual rotors with a magnetic-free segmented armature, exposing the outer surface of each rotor to an open environment for better heat dissipation.
Main YASA Axial Flux Motor Models
YASA P400R
The YASA P400R is a medium-sized, high-efficiency axial flux motor in the YASA series, widely used in electric vehicles and other power-driven applications. Its key features include:
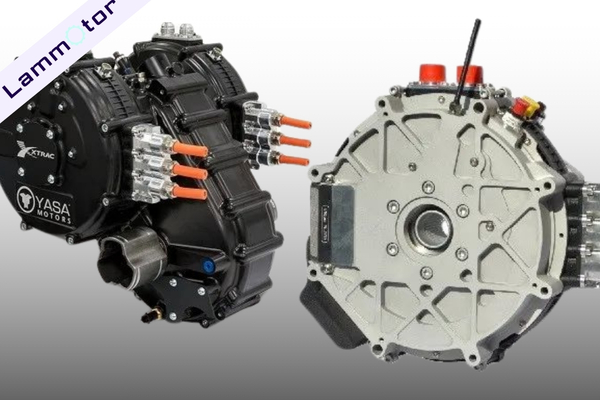
- Power Output: Maximum output power of approximately 400 kW, providing excellent acceleration and continuous drive performance.
- High Power Density: The axial flux design allows higher power output in a smaller size, reducing the overall weight of the vehicle.
- Efficiency: The P400R motor has low energy conversion losses, making it suitable for long-duration, high-load operation.
- Compactness: Compared to traditional radial flux motors, the P400R is smaller and lighter, optimizing electric vehicle designs.
YASA 750R
The YASA 750R is a high-power version in the YASA motor series, designed for high-performance electric vehicles and aerospace applications requiring extremely high power density and torque. It features:
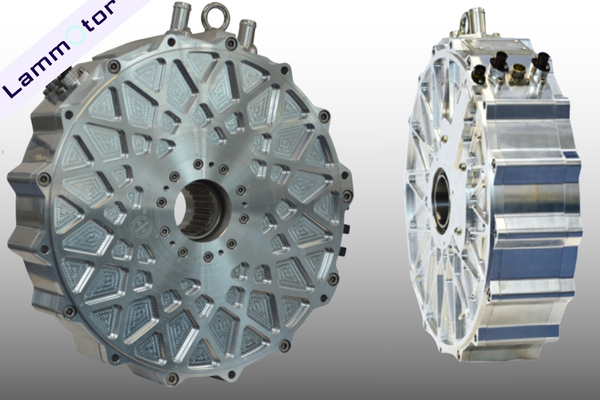
- Power Output: Maximum output power of 750 kW, offering strong acceleration for high-performance electric race cars and heavy-duty electric vehicles.
- Torque Density: The YASA 750R provides extremely high torque density, delivering sustained powerful performance with quick load response.
- Weight and Size: Despite its high power output, the YASA 750R is lightweight and compact, ideal for space-constrained applications.
- Wide Application: In addition to electric vehicles, the YASA 750R can be used in electric aircraft, robotics, and other high-performance systems.
Contact Lammnotor to Manufacture Axial Flux Motor Stator and Rotor
In conclusion, YASA’s axial flux motor, with its high power density, lightweight design, and outstanding thermal efficiency, has become an important technology in the electric vehicle industry.
As a professional manufacturer of axial flux stators and rotors in China, we have extensive experience in this field and are committed to providing high-quality motor core components to customers worldwide.
If you have any questions about motor core materials or technologies, or if you’d like to customize an axial stator, feel free to contact us. We’re happy to assist you!