As an experienced engineer in motor technology, I often hear this question: “What are the differences between axial flux motors and radial flux motors? Which one is better?”
This debate isn’t new. Back in 1889, Nikola Tesla patented axial flux technology. From an electromagnetic perspective, axial flux motors offer several advantages in topology and theoretical performance.
However, over 100 years later, most electric vehicles still use radial flux motors. Does this mean axial flux motors are overlooked? Not really. Radial flux motors are more mature in design, simpler to manufacture, and early technology couldn’t fully unlock the potential of axial flux motors.
In recent years, the demand for efficient motors in electric vehicles, airplanes, and industrial applications has reignited interest in axial flux motors. Companies and researchers are exploring their potential, and these motors are starting to appear in high-performance applications.
So, what are the key differences between axial flux motors and radial flux motors? Let’s dive into this interesting topic.
If you would like to learn more about how to produce axial flux stators, please click the link.
Comparison of Motor Design Structures
Axial Flux Motor Structure:
The outer and inner diameters of the stator and rotor cores of an axial flux motor are the same, but the axial length differs. The axial flux stator and rotor are assembled along the axial direction.
Normally, axial flux motors are divided into four structural types.
Single Stator/Single Rotor Structure:
- One stator and one rotor.
- Simple and compact structure but has strong unbalanced magnetic pull, high bearing load, large vibration noise, and risks of stator-rotor friction, reducing motor lifespan.
Single Stator/Dual Rotor Structure:
- Two outer rotors and one inner stator.
- High power density, suitable for traction systems, aerospace, and similar fields.
The YASA motor is an example of a dual-rotor single-stator topology, which reduces manufacturing complexity and enables automated mass production. These motors achieve power densities of up to 10 kW/kg at speeds ranging from 2000 to 9000 rpm.
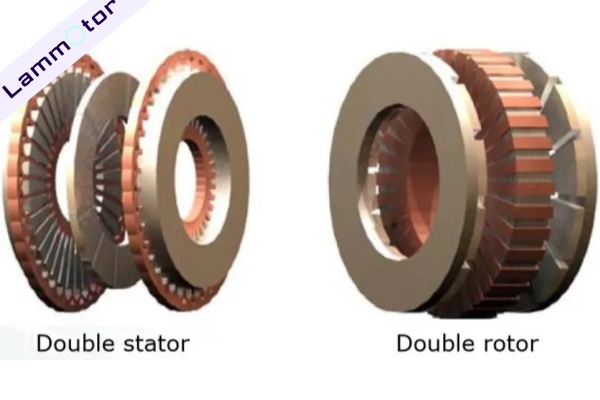
Dual Stator/Single Rotor Structure:
- Two outer stators and one inner rotor.
- Offers good symmetry and relatively smaller unbalanced magnetic pull, making it more suitable for wind power generation systems.
Multi-Stator/Multi-Rotor Structure:
- Multiple stators and rotors.
- Suitable for high-torque scenarios such as ship propulsion systems, large wind turbines, and hydroelectric generators.
However, more complex structures are not always better.
For example, dual-rotor axial motors face significant thermal issues. This is because the windings are located deep inside the stator and between two rotor disks, making heat dissipation challenging.
Yokeless Segmented Axial Flux (YASA) Motors
The newly developed yokeless segmented armature structure (YASA) motors are an improved version of traditional disc motors. In traditional designs, the stator yoke is required to conduct magnetic flux.
The traditional stator has a yoke. YASA adopts a yokeless segmented structure.
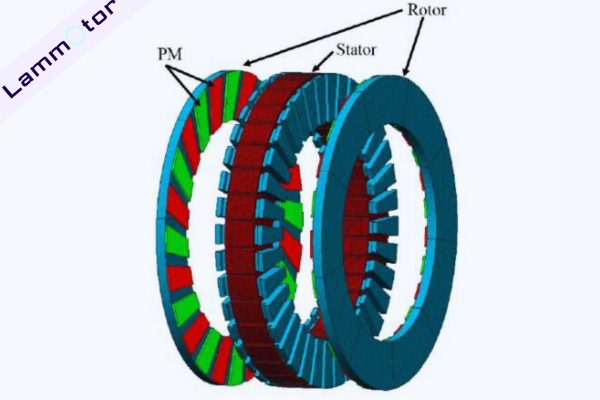
The YASA design uses two outer rotors with surface-mounted magnets and an inner stator made of multiple segmented windings.
Compared to other topologies, YASA structures offer several advantages:
- Short end windings allow for high slot fill factor and low copper loss.
- Larger air gap range when size is restricted.
- Reduced inter-phase coupling increases independence and fault tolerance.
- The absence of a stator yoke reduces stator weight and iron loss, improving efficiency.
- YASA stators use Soft Magnetic Composite (SMC) materials, composed of surface-insulated ferromagnetic particles, which can be pre-alloyed powders or pure iron powders.
The manufacturing process involves the following steps:
- Mixing ferromagnetic particles with insulating materials, which can be organic, inorganic, or a combination of both.
- Adding auxiliary components like binders and lubricants based on specific requirements.
- Using a one-step pressing process at high temperatures to form parts with complex shapes and isotropic properties.
Currently, axial flux motors are mainly used in high-end applications like supercars. But, it has not achieved large-scale production.
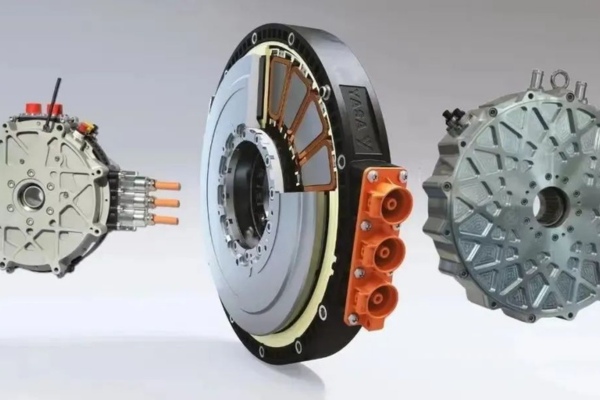
For example, Swedish Koenigsegg Regera and Hongqi S9 supercars are equipped with three motors provided by YASA MOTORS.
Among them, two YASA 750 motors are located on the rear axle’s left and right sides, directly driving the wheels, while one YASA 400 motor is located at the front end of the engine, connected to the crankshaft to supplement engine power output.
Overall, most of the advantages of yokeless axial flux motors over radial flux motors come from the higher utilization of copper, electrical steel, and magnets.
Radial Flux Permanent Magnet Motor Structure:
Radial flux permanent magnet motors are a common motor type, with magnetic flux flowing radially (from the rotor to the stator or vice versa). Key features include:
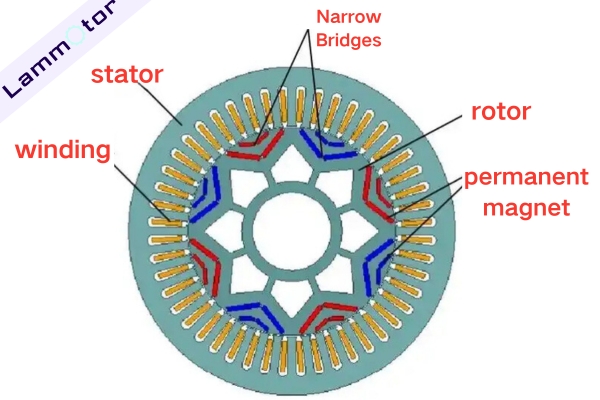
Basic Structure:
- The rotor is inside the stator: The rotor is usually installed at the center of the stator core, and the height of the stator and rotor cores is consistent.
- Stator windings: Typically embedded in slots to create rotating magnetic fields.
- Permanent magnets: Can be surface-mounted or embedded in the rotor.
Characteristic | Radial Flux Motor | Axial Flux Motor |
Magnetic Flux Direction | Flux flows radially | Flux flows axially |
Structure | Rotor is inside the stator | Disc-shaped; rotor and stator are parallel |
Volume | Longer with a smaller diameter | Flat and compact |
Power Density | High but limited by stator slots | Higher, especially in low-speed high-torque applications |
Cooling Performance | Better suited for sustained high-load | Requires design optimization for heat dissipation |
Applications | Widely used in EVs and industrial machines | Suitable for drones, EVs, and compact wind turbines |
Characteristic | Radial Flux Motor | Axial Flux Motor |
Magnetic Path Direction Comparison
The magnetic path directions differ significantly between AFPM and RFPM motors.
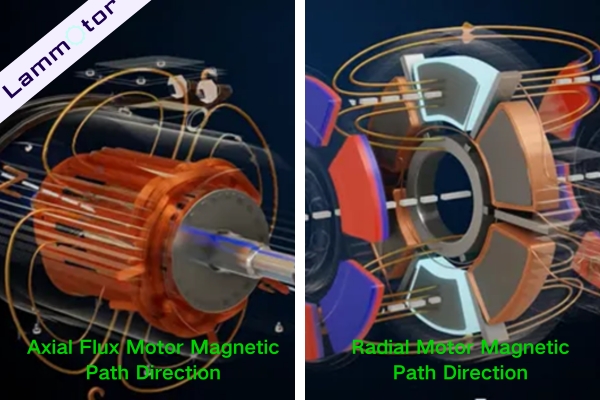
In Axial Flux Motors, the magnetic flux flows axially through the stator yoke and then circumferentially before closing the loop.
In Radial Flux Motors, the magnetic flux flows radially and then circumferentially before completing the circuit.
Stator Winding Comparison
Axial flux motors have advantages in winding efficiency compared to radial flux motors. They offer higher copper utilization and less wasted winding at the ends. This increases the potential for more turns and reduces heat caused by end effects.
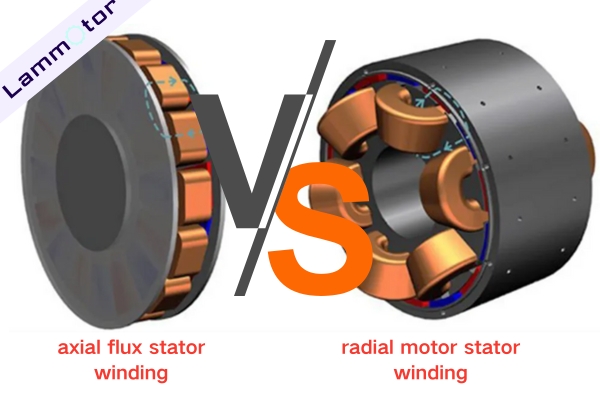
Axial flux motors typically use concentrated windings, while radial flux motors mainly use distributed windings. and can use various types of copper windings including hairpin windings.
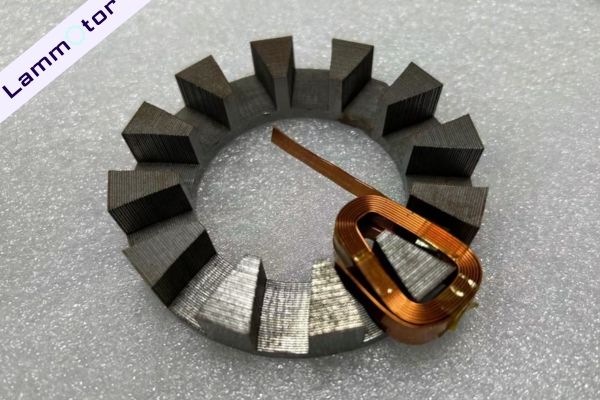
Concentrated Windings: Each stator tooth has a separate coil, making modular and automated manufacturing easier. Additionally, the shorter end windings reduce extra weight, cost, resistance, and heat loss compared to distributed windings.
Manufacturing Process of Cores
Radial flux motor cores are made using high-speed continuous stamping or composite stamping techniques.
Axial flux motor stator cores are manufactured using one-step punching and rolling processes, resulting in very high material utilization. This reduces raw material costs by about 30% compared to stamped cores.
The unique magnetic flux structure of axial flux motors makes their axial thickness about two-thirds thinner than conventional motors.
Material Comparison
Both motor types use silicon steel sheets for cores, so there is no difference in this aspect.
However, for axial motor cores, SMC materials are becoming a new choice. Powder metal soft magnetic composites (SMC) are used to produce innovative axial flux motors with outstanding features.
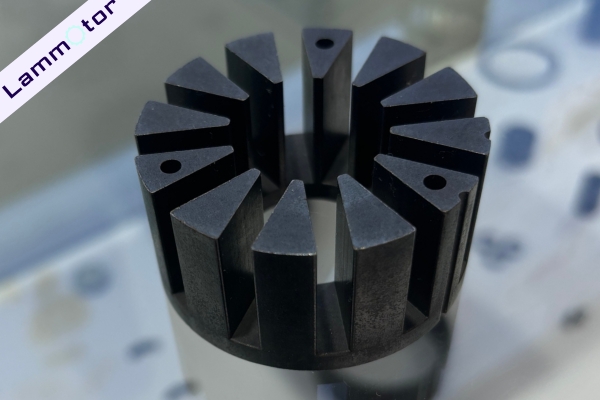
SMC materials are easy to mold, require simple heat treatment, and are suitable for mass production. They also support 3D printing, enabling more flexible and diverse designs that balance performance and cost.
Cooling Method Comparison
Due to differences in structure, cooling methods also vary:
- Radial Flux Motors: Cooling channels are placed on the radial side of the casing. Liquid cooling, such as adding water channels, is used to regulate the stator’s temperature without direct contact.
- Axial Flux Motors: The stator is located in the center, so cooling channels in the casing cannot be arranged uniformly to control temperature. Additionally, smaller size and limited space make heat buildup easier.
Currently, YASA adopts an oil cooling method with dual paths for the inner and outer. This approach poses higher demands on maintenance, casing sealing, and precision control.
Advantages of Axial Flux Motors
Even though radial designs have been the standard for decades, axial flux motors offer unique features and performance benefits.
Today, they are a top choice for applications in automotive, aerospace, and industrial fields.
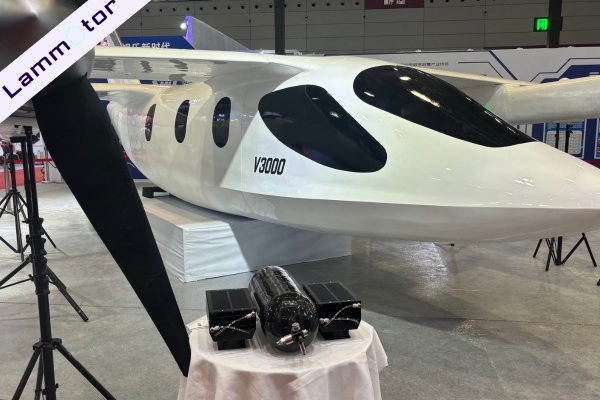
When delivering the same power output, axial flux motors outperform radial flux motors in several ways. They are smaller, lighter, and offer higher torque and power density.
1. Lightweight Design
Axial flux motors have a similar outer diameter to radial motors but are about half as long. This means their overall size is more than 50% smaller.
With no major changes in raw materials, their weight is also about 50% less than radial motors.
For example, a 5.5 kW axial motor from a Chinese pancake motor company requires only 87.5 mm in axial length and weighs just 11 kg. This reduces size by about 56% and weight by about 45%. This lightweight design saves installation space and allows for more flexible equipment layouts.
2. High Torque and Power Density
Thanks to their disc-shaped rotor and stator structure and one-dimensional axial magnetic flux path, axial flux motors offer 30% more torque density and 1%-2% higher efficiency than traditional radial motors.
Take the YASA motor as an example: despite being half the size and weight of a similar radial motor, it delivers 800 Nm of torque. Its torque density is four times that of comparable radial flux motors.
Which One Is Better?
Right now, more and more motor manufacturers are diving into axial flux motors. Companies like YASA, Koenigsegg, EMRAX, EVO, Magnax, Saietta, Siemens, and Traxial are all working on developing and producing these motors.
That said, even with all the technical advantages axial flux motors offer, they still face challenges in cost, heat management, and large-scale manufacturing. Meanwhile, radial flux motors remain the top choice because of their mature production processes and wide market acceptance.
So, as technology keeps improving, can axial flux motors overcome these hurdles and achieve mass production? Will they replace radial flux motors, or will the two coexist, each thriving in different applications?
And who knows—will future motor designs bring even more groundbreaking innovations? These are the questions motor engineers will need to think about as the industry evolves.