In electrical engineering, the production of axial flux stator cores laminations is a crucial endeavor. Crafting these laminations with precision is paramount for optimal motor performance. High-quality stator laminations play a pivotal role in enhancing efficiency and reliability.
This guide is curated to illuminate the intricate process of producing axial flux stator laminations, offering insights into the materials, tools, and steps involved.
If you would like to learn about axial flux motor vs radial flux motor, please click the link.
What Are Axial Flux Stator Cores?
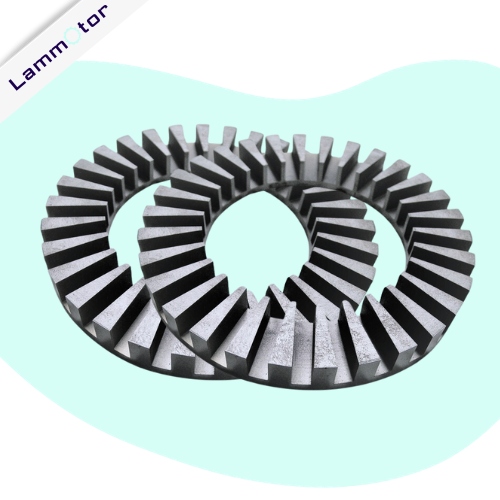
Axial flux stator cores are essential components in axial flux motors. The stator is the stationary part of the motor that generates a magnetic field, interacting with the rotor to produce mechanical motion.
In axial flux motors, the stator core is designed in a disc or pancake shape, with the magnetic flux flowing parallel to the axis of rotation. This configuration allows for a more compact and efficient motor design.
The stator core typically consists of laminated iron or other magnetic materials arranged to facilitate the efficient generation of a magnetic field when an electric current is applied. The axial flux stator cores play a crucial role in axial flux motors’ overall performance and efficiency.
Materials Required

To embark on the journey of crafting axial flux stator laminations, a thoughtful selection of materials is paramount. The process demands a meticulous consideration of each element’s properties and suitability. The importance of choosing the right materials cannot be overstated, as they directly influence the stator’s performance and longevity. Among the commonly employed materials, silicon steel takes center stage.
This alloy, known for its magnetic properties and high electrical resistivity, serves as a foundation for durable and efficient laminations. Its integration ensures optimal flux distribution, contributing to the overall effectiveness of axial flux stator cores in electric motor applications.
Equipment Required
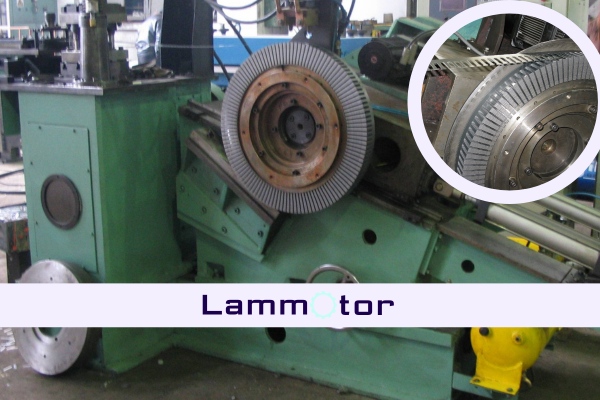
The axial flux stator lamination stamping machine with winding is a technological marvel in the realm of electric motor production. This cutting-edge machine seamlessly combines the crucial processes of lamination stamping and winding, streamlining the manufacturing of axial flux stator cores.
Through precision stamping, it crafts laminations with meticulous accuracy, ensuring optimal performance. Simultaneously, the winding mechanism intricately places coils, a vital step in enhancing the motor’s electromagnetic efficiency.
This integrated machine not only accelerates the production cycle but also upholds the high standards required for axial flux stator laminations, showcasing the synergy between innovation and functionality.
Manufacturing Process of Axial Flux Motor Stator Laminations
Cut Or Buy Silicon Steel Acquisition:
Procure or cut silicon steel sheet to the specified width, a critical initial step in axial flux stator lamination manufacturing. The chosen material must meet design requirements, ensuring optimal performance and characteristics for the subsequent stages of the process.
Slot Shape Design and Punching:
Develop the slot shape punching tooling and employ a specialized punching machine for axial flux stator lamination. This machine precisely punches slots with desired dimensions into the silicon steel. The accuracy of the slot design is crucial, as it determines the effectiveness of the stator core. The punching process carried out with precision, establishes the foundation for the subsequent stages in creating a high-quality axial flux stator lamination.
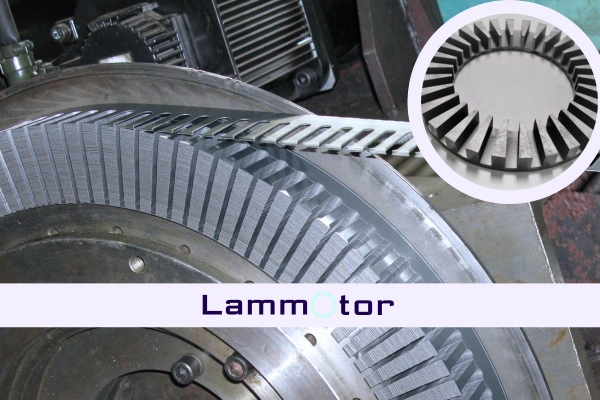
Axial Flux Stator Lamination Scroll:
Utilize a specialized punching machine designed for axial flux stator lamination. This machine scrolls the stators to the desired Inside Diameter (ID) and Outside Diameter (OD), ensuring precise slot alignment across different layers with tolerances of +/-0.5mm for OD and ID dimensions.
Welding for Stability:
After completing the stator lamination, employ laser welding or TIG welding techniques to secure the laminations, preventing any potential loosening.
Quality Inspection and Dimension Measurement:
Conduct a thorough inspection, including dimension measurements, to verify the accuracy and quality of the axial flux stator lamination. This step ensures the final product meets the required standards and specifications.
Conclusion
In conclusion, the process of producing axial flux stator laminations involves meticulous steps, from acquiring and shaping silicon steel to precise punching and welding. This manufacturing journey underscores the significance of each stage in crafting efficient and compact axial flux motors. The attention to detail in slot design, dimensions, and welding techniques ensures the final product’s stability and performance.
As industries increasingly embrace axial flux motors for their versatility and high power density, understanding the intricacies of their lamination production becomes crucial. This comprehensive approach contributes to the seamless integration of axial flux motors in various applications, propelling advancements in electric propulsion and renewable energy systems.
Ready for top-notch axial flux motor stator cores? Look no further. Please contact us, your trusted China manufacturer, for quality and efficiency in every core. Elevate your motor performance today!
FAQS
Advantages of Axial Flux Stator Cores
Compact Design: Axial flux stator cores enable a more compact motor design compared to traditional radial flux motors. The disc or pancake shape contributes to a reduced axial length, making them suitable for applications with space constraints.
High Power Density: The unique configuration of axial flux stator cores allows for a higher power density, meaning these motors can deliver more power in a smaller and lighter package. This makes them ideal for applications where weight and size are critical factors, such as in electric vehicles.
Improved Heat Dissipation: The disc-shaped stator cores promote efficient heat dissipation due to the shorter radial distance from the center to the outer edges. This helps in maintaining optimal operating temperatures, contributing to the motor’s longevity and reliability.
Enhanced Efficiency: Axial flux motors, facilitated by their stator cores, often exhibit higher efficiency levels. The improved magnetic circuit design and reduced losses contribute to better overall energy conversion, making them energy-efficient solutions.
Versatility in Applications: Axial flux stator cores make motors versatile and suitable for a range of applications, including electric vehicles, renewable energy systems, and various industrial uses. The compact design and high power density broaden their applicability across diverse sectors.
Ease of Cooling: The disc-shaped stator cores provide a more direct path for cooling mechanisms, enhancing the motor’s thermal management. This feature is crucial for applications demanding sustained high performance.
Responsive Control: The design of axial flux stator cores allows for responsive and precise control of the motor, contributing to better performance in dynamic operating conditions. This is particularly advantageous in applications requiring variable speed and torque control.
What Are Axial Flux Motors?
Axial flux motors, also known as pancake or disc motors, are a type of electric motor where the magnetic flux flows parallel to the axis of rotation.
Unlike traditional radial flux motors, axial flux motors have a disc-shaped design with a shorter axial length.
This configuration allows for a more compact and lightweight motor, making them suitable for various applications, including electric vehicles and renewable energy systems.
The design often involves placing the stator and rotor discs on either side of a thin air gap, promoting efficient heat dissipation and enabling higher power density. Axial flux motors are valued for their versatility and energy efficiency.
Can Axial Flux Motor Be Used as a Generator?
Yes, axial flux motors can function as generators. When the motor is mechanically driven, it generates electrical power through the principle of electromagnetic induction. This dual functionality enhances their versatility, making axial flux motors suitable for applications where both motor and generator capabilities are needed, such as in wind turbines or regenerative braking systems.
Applications of Axial Flux Motors
Axial flux motors find applications in diverse fields, including electric vehicles, renewable energy systems, industrial machinery, and robotics. Their compact design, high power density, and efficiency make them ideal for situations where space, weight, and energy conservation are critical factors. Additionally, axial flux motors excel in variable speed and torque applications, contributing to their widespread adoption across various industries.