Brushless DC motors, often abbreviated as BLDC motors, are revolutionizing the world of electronics and machinery. Unlike their brushed counterparts, these motors rely on electronic commutation, ensuring a more efficient and longer-lasting performance. Their significance in modern applications, ranging from household gadgets to industrial equipment, cannot be overstated.
The purpose of this post is to delve deep into the intricacies of brushless DC motors, shedding light on their structure, operation, and unparalleled advantages. Whether you’re a tech enthusiast or someone simply curious about the buzz around BLDC motors, this guide promises to equip you with essential knowledge on the subject.
Basic Principles of Brushless DC Motors
A Brushless DC Electric Motor (BLDC) is an electric motor powered by a direct current voltage supply and commutated electronically instead of by brushes like in conventional DC motors. At the heart of understanding brushless DC motors lies the distinction between them and their brushed counterparts. Firstly, traditional brushed motors rely on brushes for commutation, which often leads to wear and tear over time. In contrast, BLDC motors eliminate this mechanical component entirely.
Instead, they utilize electronic commutation, a process that stands out as both efficient and durable. This pivotal change not only reduces maintenance but also enhances the motor’s lifespan. Furthermore, electronic commutation actively adjusts the motor’s speed and direction, offering more precise control.
So, while both types serve the fundamental purpose of converting electrical energy into mechanical energy, it’s the method of commutation that sets them apart. In essence, the transition to electronic commutation in BLDC motors represents a significant leap forward in motor technology.
Structure and Components of BLDC Motors
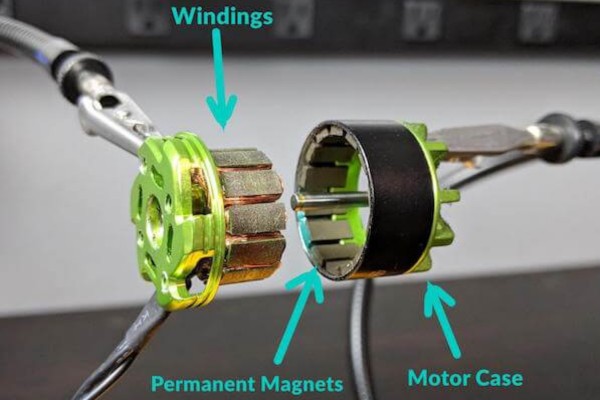
Diving into the anatomy of brushless motors, one can appreciate the intricacy of their design. Central to the motor’s structure are two main components: the rotor and the stator. The rotor houses a permanent magnet, which plays a crucial role in generating a consistent and stable magnetic field.
On the other hand, the stator, typically positioned around the rotor, contains coils that, when energized, produce an electromagnetic field. This interaction between the rotor’s permanent magnet and the stator coil is what drives the motor to spin. The synchronization of these components is paramount, ensuring efficient energy conversion and optimal performance.
In essence, the harmonious collaboration between the rotor’s magnet and the stator coil is the backbone of a BLDC motor, making it a marvel of modern engineering.
Controlling BLDC Motors
Controlling a brushless DC motor is an art, and there are three predominant methods to master this art.
First up is the Trapezoidal control, often referred to as “six-step” control. This method energizes two out of the three phases at any given time, resulting in a trapezoidal-shaped back electromotive force (EMF) waveform.
Next, we have the Sinusoidal control. As the name suggests, this method drives the motor using sinusoidal current waveforms, ensuring smoother torque but often at the cost of reduced efficiency.
Lastly, the Field-oriented control (FOC) stands out as the most advanced. It dynamically adjusts the current based on the rotor’s position, ensuring optimal torque and efficiency.
Each of these control methods offers unique advantages, and the choice often boils down to the specific requirements of the application. In essence, mastering these controls is pivotal for harnessing the full potential of BLDC motors.
Advantages and Disadvantages of Brushless DC Motors
Brushless DC (BLDC) motors have gained immense popularity in various applications due to their distinct features. However, like any technology, they come with their set of pros and cons.
Advantages:
Longer Lifespan: Without brushes to wear out, BLDC motors tend to have a longer operational life.
Higher Efficiency: They convert a higher percentage of electrical energy into mechanical energy, reducing energy loss.
Low Maintenance: The absence of brushes means fewer parts to replace and less maintenance.
Quieter Operation: BLDC motors produce less noise due to the lack of friction from brushes.
Better Torque: They can provide consistent torque at high speeds, making them suitable for various applications.
Reduced Heat Production: With no brushes causing friction, they generate less heat, which can extend the life of other components.
Disadvantages:
Cost: BLDC motors are generally more expensive than brushed DC motors due to their complex electronic control systems.
Complex Control: They require sophisticated electronics for communication, which can complicate their integration into systems.
Sensitivity to Heat: While they produce less heat, they can be more sensitive to high temperatures, which can affect their magnets.
In conclusion, while BLDC motors offer numerous advantages, it’s essential to weigh these against their drawbacks to determine their suitability for a specific application.
Applications of Brushless DC Motors
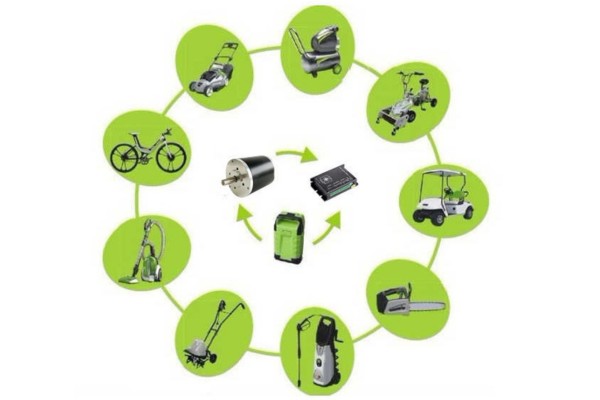
There are various types of motor in common use. Brushless DC motors have carved a niche for themselves across a myriad of industries, thanks to their efficiency and durability. Here’s a glimpse into some of their most prominent applications:
Household: From vacuum cleaners to washing machines, BLDC motors power a range of home appliances, ensuring quieter and more energy-efficient operations.
Automobile: Modern vehicles, especially electric cars, rely on these motors for their propulsion systems, offering smoother rides and better battery life.
Medical Care: Precision is paramount in medical devices, and BLDC motors deliver just that, driving equipment like ventilators and surgical tools.
Industrial Equipment: In factories and production lines, these motors are the workhorses behind conveyor belts, robotic arms, and more, ensuring consistent performance and reduced downtime.
In essence, the versatility of BLDC motors is evident in their widespread adoption across diverse sectors.
Maintenance and Care of BLDC Motors
Ensuring the longevity of brushless DC motors goes beyond just their initial installation. Regular maintenance and care can significantly extend their lifespan. Here are some essential tips:
Regular Inspection: Periodically check for any signs of wear or damage, especially in the bearings and windings.
Cleanliness: Keep the motor free from dust and debris, which can hinder its performance over time.
Lubrication: While BLDC motors require less maintenance than their brushed counterparts, ensuring proper lubrication of bearings can prevent premature wear.
Avoid Overloading: Always operate within the motor’s specified limits to prevent overheating and potential damage.
Stay Updated: Firmware updates for electronic controllers can enhance motor performance and efficiency.
By adhering to these guidelines, you can ensure that your BLDC motor remains in optimal condition, delivering consistent performance for years to come.
What’s the Difference Between Brush and Brushless Motors?
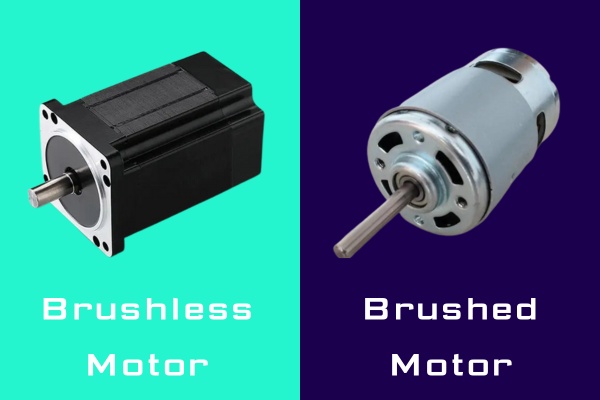
When comparing BLDC (Brushless DC) motors to traditional DC motors, several distinctions emerge. BLDC motors, with their electronic commutation, offer a longer lifespan due to the absence of brushes that wear out.
They also provide higher efficiency, reduced noise, and better torque at high speeds.
On the other hand, traditional DC motors are simpler in design and can be more cost-effective for certain applications. However, they require more maintenance due to brush wear and can be less efficient.
In essence, while BLDC motors are often superior in terms of performance and longevity, the choice between BLDC and DC motors largely depends on the specific application and budget constraints.
Conclusion
Brushless DC motors stand as a testament to modern engineering prowess, combining efficiency with durability. Their widespread applications, from household gadgets to industrial machinery, underscore their importance and adaptability. In a world that constantly seeks innovation, the versatility of BLDC motors undeniably marks a significant stride in technological advancement.
What is a stepper motor?
A stepper motor is an electromechanical device that converts electrical pulses into precise mechanical movements. It is widely used in applications that require accurate positioning, such as robotics, automation, and computer numerical control (CNC) machines.
Unlike other types of motors, a stepper motor moves in discrete steps instead of rotating continuously. It achieves this by dividing a full rotation into a fixed number of steps and rotating the shaft incrementally according to the input pulses. This makes stepper motors highly controllable and suitable for applications where precise positioning is crucial.