In the bustling world of automation and robotics, motors play an indispensable role. Amidst the plethora of motor types, the debate between stepper motors and servo motors remains persistent. This comparison delves deep into the stepper motor vs. servo motor problem, guiding you to an informed decision.
Stepper Motor vs. Servo Motor: Basic Definitions and Fundamentals
Understanding the nitty-gritty of how each type functions lays the foundation for any comparison in the vast ecosystem of motors and their applications. The epicenter of our current exploration—the stepper motor vs. servo motor debate—requires a brief grasp of their mechanisms and functionalities.
What is Stepper Motor?
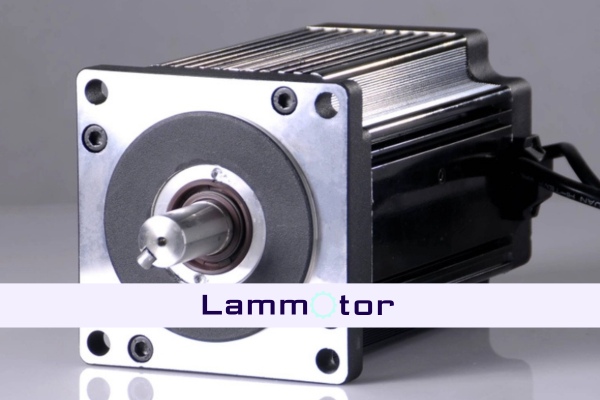
A stepper motor is a type of brushless DC motor. Essentially a digital device, a stepper motor transforms electronic pulses into proportionate mechanical rotations. Each electrical pulse results in the motor turning a specific angle, also known as a ‘step.’ The lack of a feedback mechanism makes its operation open-loop, meaning it runs sequences without constantly adjusting for external factors.
Due to their high pole count, Stepper motors offer precision drive control for motion control applications. They have a high torque at low speeds and are relatively inexpensive and widely available.
What is a Servo Motor?
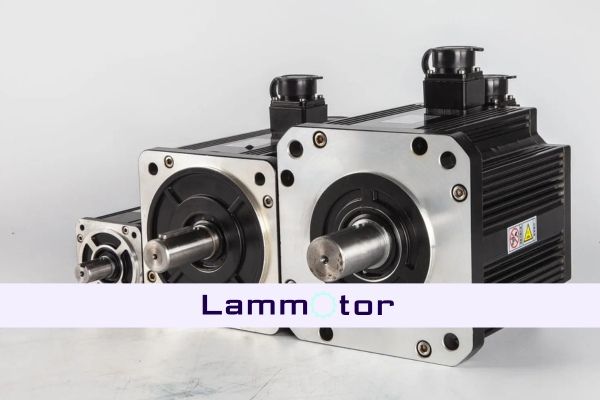
This motor stands out due to its continuous rotation abilities and an inherent feedback system. It aligns its movement based on an input signal, achieving a precise rotation angle. The integrated feedback mechanism monitors and adjusts the motor’s position, ensuring a closed-loop operation. This provides exact positioning and consistent torque throughout its operating range.
While both motors might seem similar in their pursuit of converting electrical signals to movement, their operational dynamics vary considerably. This distinction is crucial when diving deeper into the stepper motor vs. servo motor comparison.
Related Articles: Brushless VS Brushed DC Motors: What’s The Difference? Difference Between Synchronous Motor And Induction Motor
Stepper Motor vs. Servo Motor: Core Design and Mechanics
Their distinct architectures take center stage as we delve deeper into the stepper motor vs. servo motor showdown. Both are engineering marvels, but their internal designs largely dictate their functionalities and applications.
Anatomy of a Stepper Motor
Its structure is somewhat straightforward but genius. A stepper motor comprises a rotor and stator, with windings positioned in the latter. As electrical pulses are received, the stator generates magnetic fields that push or pull the rotor’s teeth, causing rotation in discrete steps.
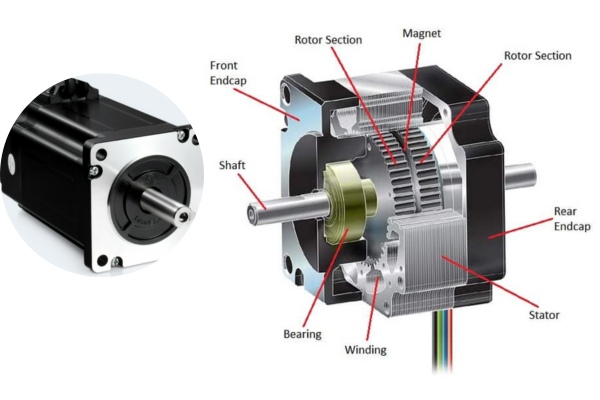
Anatomy of a Servo Motor
A bit more intricate, a servo motor harmoniously integrates a regular motor, an encoder for position feedback, and a control circuit. This ensemble allows the servo to precisely adjust its position based on external feedback, ensuring exactness in its operations.
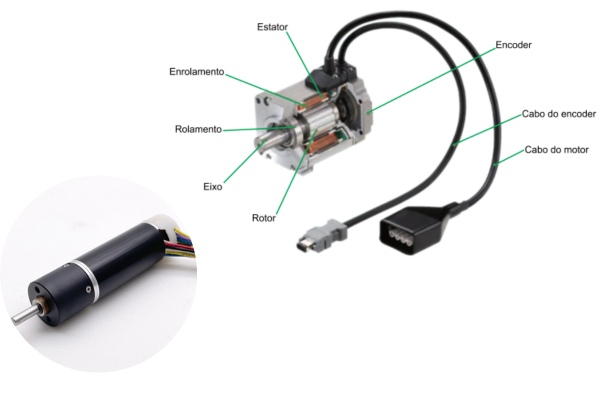
Stepper Motor vs. Servo Motor: Key Features & Characteristics
Navigating through the intricate maze of servo motors and stepper motors comparisons, their features and characteristics illuminate the path, offering clarity to users.
Precision and Accuracy:
Stepper motors inherently operate in fixed increments. These steps provide a level of precision. However, they can’t adjust for external discrepancies without a feedback mechanism. Servo motors, endowed with their feedback loops, adjust in real-time, gifting them an edge in accuracy, especially under varying load conditions.
Speed and Torque:
Servo motors usually steal the limelight regarding sheer speed and torque over a vast range. Their design allows consistent torque across different speeds. In contrast, stepper motors lose torque as they approach higher speeds, making them better suited for medium-speed applications.
Feedback Mechanisms:
The essence of a stepper motor’s operation is open-loop; it doesn’t adjust based on external conditions. However, the servo motor’s feedback mechanism constantly refines its movement, ensuring optimal performance.
Efficiency and Heat Dissipation:
Thanks to their feedback and controlled operation, servo motors often use power more efficiently, resulting in less wasted energy as heat. Conversely, stepper motors, especially when overdriven, can become notably warmer.
Pros and Cons Analysis of Stepper And Servo Motors
When evaluating stepper motors and servo motors, weighing their advantages and disadvantages provides clarity. Here’s a breakdown of each motor’s strengths and limitations:
Advantages of Stepper Motors:
Cost-effective: Generally more affordable in terms of initial outlay.
Simplicity in Control: No need for complex feedback systems, making it easier to integrate into systems.
Reliability: Predictable and reliable for applications that don’t require feedback.
Consistent Torque at Low Speeds: Deliver optimal torque at slower speeds, making them suitable for specific applications.
Disadvantages Stepper Motors:
Heat Generation: Tendency to produce more heat, especially when overdriven.
Lack of Feedback: With feedback mechanisms, they can maintain steps by notifying the system.
Torque Declines at High Speed: Not suitable for applications that require consistent torque at high speeds.
Noisy Operations: Can be noisier than servo motors, especially at higher speeds.
Advantages of Servo Motors:
High Precision: Integrated feedback systems ensure precise positioning.
Efficient Power Consumption: Use power based on demand, ensuring energy efficiency.
Consistent Torque Across Speeds: Deliver uniform torque at both low and high speeds.
Quieter Operations: Less noise production compared to stepper motors.
Disadvantages of Servo Motors:
Higher Initial Cost: The sophistication comes with a heftier price tag.
Complexity: Requires intricate setup and tuning, especially for feedback systems.
Maintenance: Though minimal, they may need more regular checks due to the complexity of components.
Application Areas of Stepper Motor And Servo Motor
When considering stepper motor vs. servo motor for your needs, applications matter.
Common Uses of Stepper Motors
3D Printers: These machines demand precise incremental movements, making stepper motors a go-to choice.
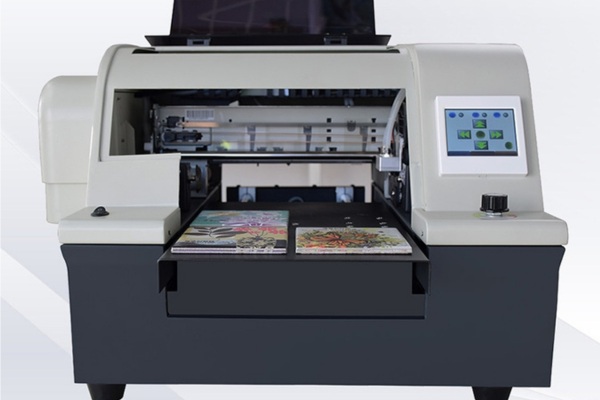
CNC Machines: For tasks like milling and engraving where medium precision suffices, stepper motors often find their place.
Scanners: Scanners’ repetitive and controlled movement leverages stepper motors’ predictability.
Digital Cameras: For autofocus mechanisms, the step-by-step adjustment capability proves beneficial.
Common Uses of Servo Motors
Robotics: Servo motors, such as robotic arms, reign supreme in high-precision and speed applications.
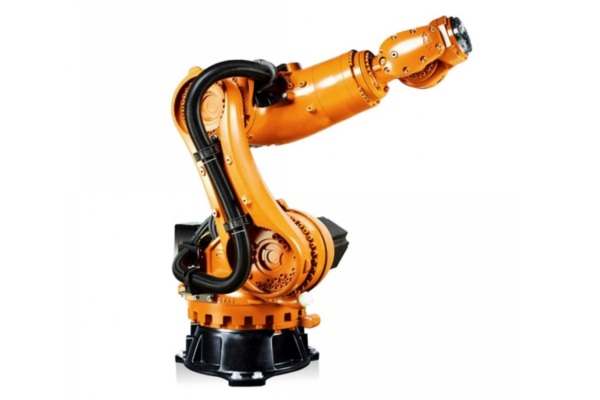
CNC Machinery: Servo motors are preferred for high-end CNC machines demanding impeccable precision.
Conveyor Belts: In industries where items move at variable speeds with different weights, the adaptive torque of servo motors comes in handy.
Drones: The need for precise and rapid adjustments in drones’ flight systems makes servo motors invaluable.
Both stepper and servo motors have carved unique niches for themselves. Their application realms sometimes overlap, but their specialized functionalities make them indispensable in specific industries.
Cost Implications
Budget often plays a pivotal role in the stepper motor vs. servo motor debate.
Initial Investment: Stepper motors usually have a friendlier price tag initially, whereas servo motors, given their complexity, cost more upfront.
Maintenance and Long-Term Costs: While stepper motors have fewer maintenance needs, over time, the efficiency and durability of servo motors may offer better long-term value.
Conclusion
The stepper motor vs. servo motor debate isn’t about superiority; it’s about applicability. Your specific needs, budget, and long-term plans should guide your choice.
Here’s hoping that this deep dive has provided clarity, enabling you to harness the power of these motors more effectively in your endeavors.
High-Quality Motor Core Laminations at Lammotor
Discover unparalleled precision with Lammotor’s top-tier motor core laminations. Tailored to perfection, our laminations ensure optimal performance, longevity, and efficiency for your motors. Whether it’s for stepper or servo applications, Lammotor promises unmatched quality, fostering enhanced motor functionality. Choose Lammotor, where excellence in stepper motor cores and servo motor cores meets your every need.
FAQs
What is an AC servo motor?
An AC servo motor is designed to provide high precision and control in various industrial applications. It is typically used in systems that require accurate and continuous rotational motion. AC servo motors are equipped with a feedback control mechanism, such as encoders, to provide information on the actual position of the motor shaft. The motor controller then uses this feedback to adjust the voltage and current supplied to the motor, enabling precise control over the motor’s speed, position, and torque. As a result, AC servo motors are widely used in industries such as robotics, CNC machinery, and automation systems.
What’s the primary difference between stepper motors and servo motors?
A stepper motor moves in discrete steps, while a servo motor uses feedback for precise positioning.
Which motor is more cost-effective initially?
Typically, stepper motors are more budget-friendly initially compared to servo motors.
Where would I commonly find servo motors in use?
They are often used in robotics, CNC machinery, and high-speed conveyor systems.
Can stepper motors be used in high-precision applications?
While stepper motors offer medium precision, for extremely high precision, servo motors are preferable.
How do motor core laminations affect the efficiency of these motors?
They play a crucial role in minimizing energy wastage and optimizing performance.