Lamination stacks are vital in electric motors, generators, vehicles, and other electromechanical systems. Two of the most critical components are stator and rotor lamination stacks in motors. But, do you know what’s the difference between stator and rotor laminations? In this post, we’ll explore what these two components are, how they differ, and their role in the functioning of electric motors.
What are Motor Stator Lamination?
At the most basic level, a motor’s stator is the stationary part of the motor that surrounds the rotor. Its main job is creating a magnetic field that interacts with the rotor’s magnetic field, causing it to spin and generate power. However, creating an effective magnetic field is only half the challenge. The other half is managing the electrical currents that flow throughout the motor.
This is where stator laminations come in – they are the laminated sheets of metallic alloy that form the stator core. Stator lamination stacks are made from thin, insulated metal sheets stacked and bonded together to form a rigid core. These sheets are typically made from low-carbon steel alloys, which are easily magnetized and demagnetized.
Laser-cutting stator lamination is suitable for lamination prototyping. It is a highly effective method for producing stator laminations for electric motors and generators.

The benefits of stator laminations
The purpose of stator laminations is to minimize power loss and reduce vibration and noise. The laminated construction of the stator core helps to reduce eddy currents, which reduces power loss and increases efficiency. The laminated construction also helps reduce vibration and noise by reducing magnetic flux and magnetic iron loss.
What are Motor Rotor Laminations?
Like stator lamination stacks, rotor laminations are also made from laminated sheets of metallic alloy. But they are much more complex in design. While the stator’s main job is to create a magnetic field. The rotor’s job is to respond to that magnetic field in a way that generates rotational motion.
Rotor lamination stacks are typically made from thicker sheets of metal alloys that can be easily magnetized and demagnetized. The stacks consist of several stacks of steel laminates that are cut into the precise shapes necessary to create the rotor’s electromagnetic field when paired with the stator.
The rotor is typically the moving component of the motor, with its central shaft running through the center of the stator. Without the rotor, the motor would not be able to generate power, as the interaction between the stator’s magnetic field and the rotors current create rotational motion.
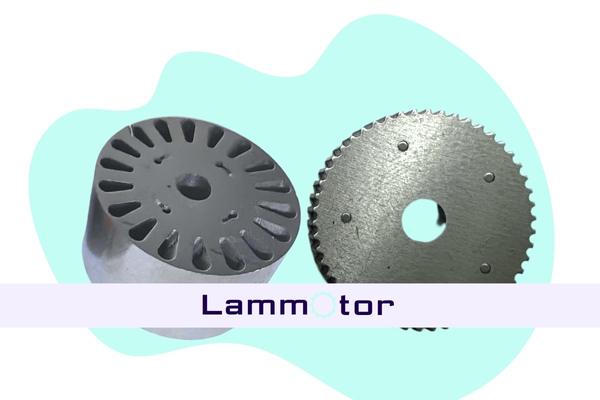
Key Differences Between Motor Stator and Rotor Lamination
Although rotor and stator lamination stacks are made from laminated sheets of metallic alloy, they differ in several ways.
Application in the motor
One of the most significant differences is their application within the motor. Simply put, the stator core is a stationary component that creates a magnetic field, whereas the rotor is the rotating component that responds to that magnetic field.
Thickness
Another difference is in their respective designs. Stator lamination stacks are made from thin metal sheets, typically only a few hundredths of an inch thick.
In contrast, rotor lamination stacks are made from thicker metal sheets, often several times thicker than those used for stator lamination stacks.
Materials
The materials used for stator stacks are typically low-carbon steel alloys. These alloys are inexpensive, easy to work with, and offer high magnetic permeability, making them ideal for creating a magnetic field.
On the other hand, rotor stacks require thicker laminates, such as nickel or cobalt, which have a higher magnetic saturation point than low-carbon steel.
Function
Functionally, stator stacks minimize power loss and reduce vibration and noise. This is accomplished through their stacked, laminated design, which helps to reduce eddy currents and improve magnetic flux.
Conversely, rotor stacks respond to the magnetic field created by the stator, generating the mechanical rotation required to generate power.
This is accomplished through the rotor’s complex shape and the precise arrangement of its laminated sheets.
Shape
The design differences between stator and rotor lamination stacks extend beyond their shapes, extending even to the general shape of the motor itself.
The stator typically has an annular shape surrounding the rotor, while the rotor is a simple cylinder with or without fins on the outside.
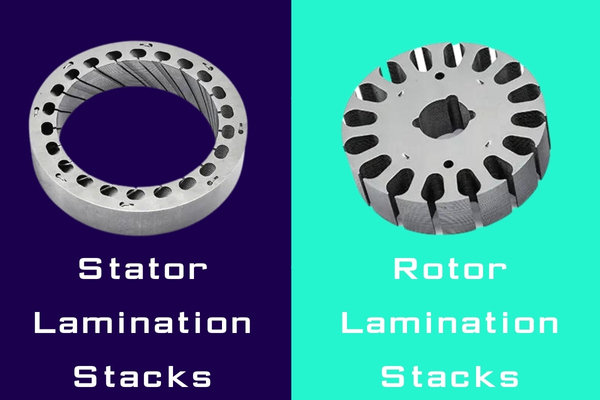
The Role of Motor Stator and Rotor Lamination Stacks in Electric Motors
The role of stator and rotor stacks in electric motors is critical to their overall functionality. The primary role of the stator stack is to create a magnetic field. Because of their laminated design, stator stacks minimize power loss and reduce vibration and noise, helping to make the motor efficient and functional.
On the other hand, the rotor stack responds to the magnetic field created by the stator, generating the necessary mechanical rotation to generate power. Without a properly functioning rotor, the motor will not generate any power, making it useless.
The stator and rotor laminations work at the most basic level to produce rotational motion. When electrical energy is applied to the motor, it creates a magnetic field in the stator stack, which then causes the rotor to rotate. This action creates a mechanical force that generates energy in the form of motion or rotation.
Common Applications of Stator and Rotor Lamination Stacks
Electric motors are suitable for various applications, and laminated cores are essential. Some common applications include:
Industrial equipment and machinery
HVAC systems
Electric vehicles
Power tools
Kitchen Appliances
Electric motors also play a key role in renewable energy systems, such as wind turbines, where the rotor laminations are essential in converting wind energy into electrical energy.
Our Capability For Stator And Rotor Lamination Stacks
We can design and manufacture a range of high-quality stator and rotor lamination stacks for electric motors, including stamping, mold designing and manufacturing, and stacking. We ensure that every component we produce is made to the highest standard, meeting the precise requirements of our clients.
With our expertise in motor components, we can provide customized solutions that meet the unique needs of our customers, ensuring that their motors run efficiently and effectively. Whether you require a high-volume production run or a custom-made component, we have the experience and capabilities to handle all your needs.
From stamping to insulation, bonding, assembly, and quality testing, we offer a simplified supply chain and short lead times for motor laminations prototypes and mass production.
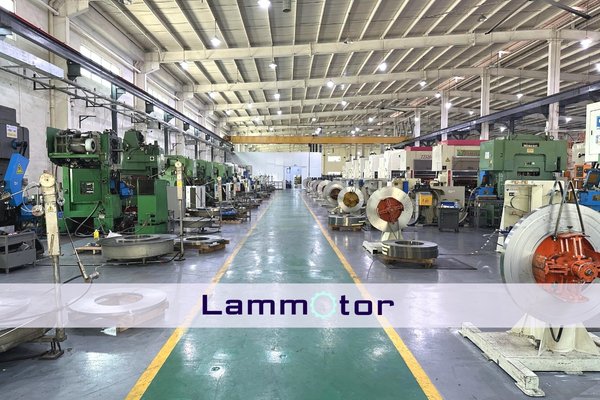
Conclusion
In conclusion, motor stator and rotor lamination stacks are two critical components in the functioning of electric motors.
While their relative designs and materials may differ, their role in creating magnetic fields and rotating forces to drive machines and equipment is fundamental to industrial operations.
Understanding the differences between the two laminated components and their unique roles is critical for properly selecting and maintaining electric motors.