Are you curious about how the Tesla Cybertruck achieves 845 horsepower? As a highly anticipated electric pickup truck, what makes its motor configuration and design unique?
If you are interested in Tesla’s motor technology, we recommend first reading our articles “Comparison of Motor of Tesla, BYD, and Huawei” and “Tesla Model S Plaid vs. Lucid Air Motor” to explore the details of cutting-edge motor technology comparisons.
Tesla Cybertruck is an electric pickup truck that has attracted much attention. Today, let’s dive into the technological highlights and performance advantages of the Tesla Cybertruck motor.
Three Motor Configurations of Cybertruck
The Cybertruck offers three configurations: tri-motor all-wheel drive (AWD), dual-motor AWD, and single-motor rear-wheel drive (RWD).
Single Motor: A permanent magnet motor is mounted on the rear axle, providing rear-wheel drive.
Dual Motor: The front axle is equipped with an induction motor, and the rear axle has a permanent magnet synchronous motor, achieving all-wheel drive. The front induction motor produces a maximum power output of 303 horsepower (226 kW), while the rear permanent magnet motor delivers 297 horsepower (221 kW), with a total output of 600 horsepower (450 kW).
Tri-Motor: Two induction motors are installed on the rear axle, and a permanent magnet synchronous motor is on the front axle. This configuration provides higher power and performance. The tri-motor AWD version, known as the “Cyberbeast,” delivers 845 horsepower (630 kW). The front motor produces 276 horsepower (206 kW), and each rear motor produces 284 horsepower (212 kW).
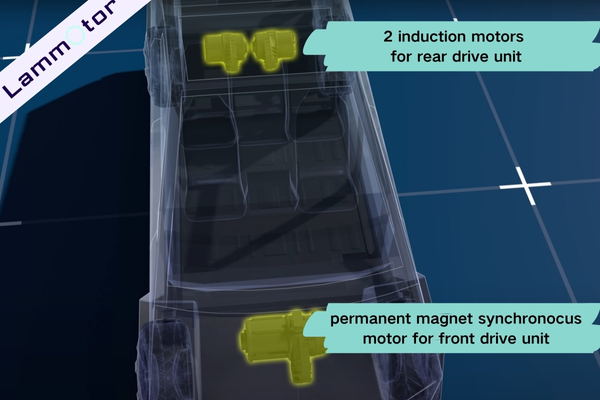
Front Drive Unit: Permanent Magnet Synchronous Motor
Permanent Magnet Synchronous Motor Stator
In the tri-motor configuration of the Tesla Cybertruck, the front motor is a permanent magnet synchronous motor.
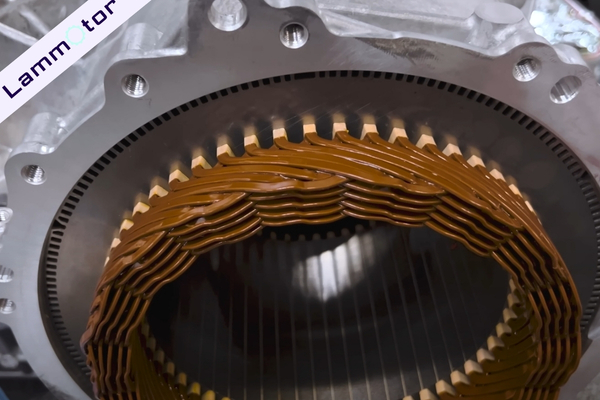
Its stator features an 8-layer flat wire winding design, unlike the 10-layer design used in the Model 3 motor stator.
This design difference reflects specific technical considerations and application needs. Here are some possible reasons:
1. Size and Structural Optimization
The Cybertruck, as a large pickup, requires a balance between power output and weight.
The 8-layer flat wire design reduces heat accumulation in the windings and simplifies the cooling structure.
It suits higher torque demands, as reducing the coil layers decreases resistance losses while maintaining efficiency.
2. Thermal Performance Optimization
Fewer layers mean shorter heat dissipation paths, making it easier for heat to transfer to the cooling system. This is crucial for heavy-duty use like off-road or towing.
The 10-layer design increases winding density but may trap heat, causing local overheating during extended high-load operations.
3. Manufacturing Process and Cost
A 10-layer design requires more precise equipment and stricter tolerance control, raising complexity and costs.
An 8-layer design simplifies the process, improves production efficiency, and reduces error rates.
4. Different Application Needs
The Cybertruck requires strong low-speed traction for off-road and towing. The 8-layer design, combined with an optimized drive system, ensures better low-speed torque.
The Model 3 prioritizes high-speed performance and efficiency, making the 10-layer design more suitable.
Permanent Magnet Synchronous Motor Rotor
Tesla engineers divided the rotor into three segments: a wider center and narrower sides.
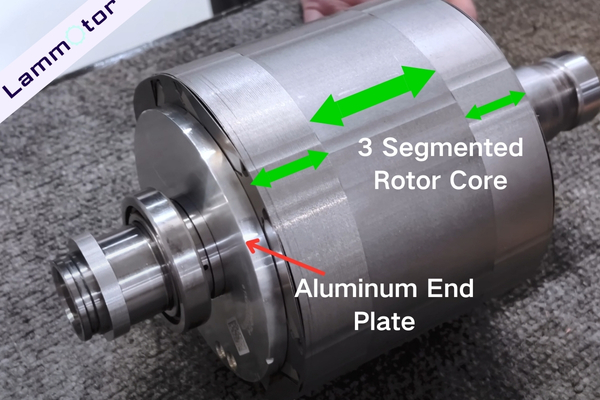
Each section is slightly offset to reduce torque ripple and noise, similar to the 3D7 motor design.
The aluminum end plate of the rotor does not extend to the outer diameter of the rotor laminations to reduce weight.
The Cybertruck’s front motor rotor uses a single solid piece of permanent magnet instead of the segmented design in the Model 3. This choice primarily aims to reduce costs.
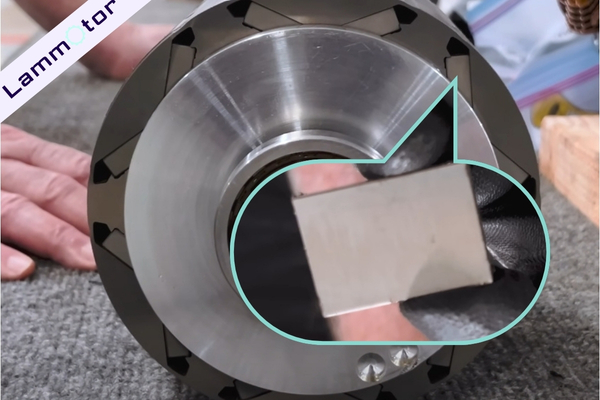
Benefits of Segmented Permanent Magnets
Segmented permanent magnets first appeared in Tesla Model 3 motors. The advantages include:
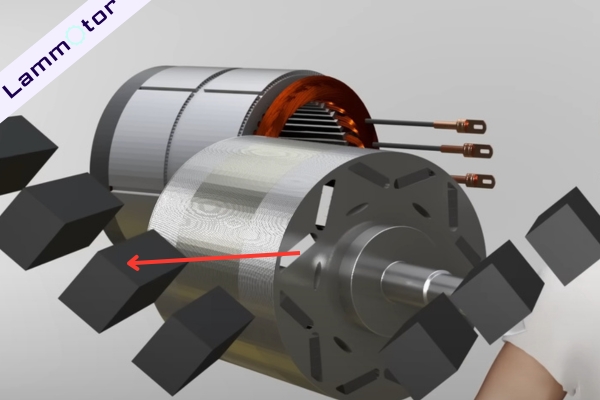
1. Reducing High-Frequency Harmonic Losses
Segmented permanent magnets can adjust the size, angle, or spacing of each segment, reducing high-frequency harmonics during motor operation. This helps lower torque ripple and energy losses.
2. Improving Heat Dissipation
Gaps between segmented magnets provide pathways for heat to escape. This design reduces rotor temperature rise and extends the lifespan of the permanent magnets.
3. Reducing Mechanical Stress
During high-speed rotation, the rotor experiences centrifugal force. Segmented magnets distribute the stress evenly, minimizing concentrated stress damage and enhancing structural strength.
4. Reducing Demagnetization Risks
Solid permanent magnets are prone to local demagnetization under high temperatures or strong reverse magnetic fields, leading to performance decline. Segmented designs limit the impact of local demagnetization, preserving the overall magnetic field.
Rear Drive Unit: Induction Motors
Induction Motor Stator
The tri-motor Cybertruck has two induction motors on the rear axle, symmetrically distributed. The stator diameter matches that of the front permanent magnet synchronous motor, both using an 8-layer flat wire winding design.
Induction Motor Rotor
Normally, induction motor rotors are skewed, with laminations at a slight angle. However, the Cybertruck’s rotor is straight.
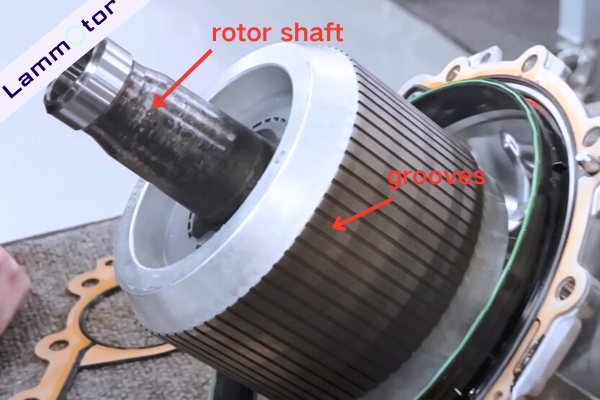
Tesla engineers added small grooves to reduce noise.
The rotor shaft uses a non-machined surface design to lower costs while maintaining mechanical performance and reliability.
Contact Us for EV Motor Stator and Rotor
The Tesla Cybertruck motor design is slightly less advanced than the motors in the Model 3 or Model S Plaid. However, this is understandable, given the Cybertruck’s different positioning and performance requirements.
We are a professional manufacturer of EV motor cores. If you are interested in motor core stamping or EV motor core products, visit our prototype and stamping pages or EV motor core product pages to learn more about our expertise.