Ever wondered why segmented stator cores are creating such a buzz in the electric motor world? As a seasoned motor core lamination manufacturer in China, with years of experience under our belt, we’re here to shed some light on this fascinating topic.
We’ve seen it all, from the classic to the segment, and today, we’re sharing why segmented stator laminations are essential for modern electric motors. So, buckle up and get ready for a journey through the intricacies of motor design.
Why Need to Segment Stator Lamination?
Segmented stator laminations are electric motor components where the stator laminations are divided into smaller sections. For larger stators or when minimizing waste is crucial, segmenting becomes essential.
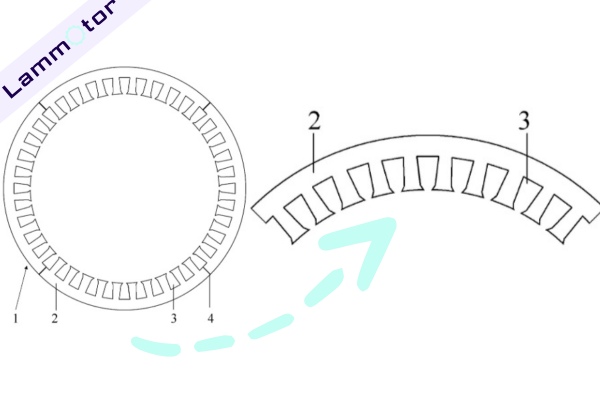
The main reason for segmenting lamination is to meet the unique demands of high-power motors. This approach ensures better performance, easier manufacturing, and reduced material wastage.
By segmenting, we can cater to the specific requirements of powerful motors, making them more efficient and durable.
Benefits of Segmented Stator Cores
Segmented motor stator cores offer a range of benefits that make them indispensable for modern electric motors.
1. Simplify the winding process.
By breaking the stator into segments, winding becomes more manageable and precise, leading to improved overall efficiency and performance.
2. Segmented cores are easier to transport and assemble.
Their smaller size means they can be handled and installed with less hassle, saving time and effort during the manufacturing process.
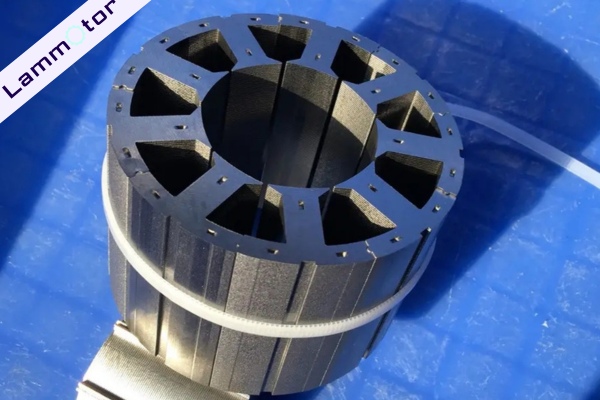
3. More choice of material
Segmentation allows for the use of different silicon steel materials for the stator and rotor, including oriented steel. This flexibility enables manufacturers to optimize each component for its specific function, enhancing the motor’s efficiency and performance.
4. Improve material utilization
Segmented stator cores improve material utilization, reducing costs and minimizing waste. By optimizing the use of materials, manufacturers can lower production costs and create more sustainable products.
5. Increase reluctance torque.
The enhanced magnetic properties of segmented designs result in higher torque output, making the motors more powerful and efficient.
In summary, segmented stator cores simplify winding, ease transportation and assembly, allow for diverse material use, enhance material efficiency, and boost reluctance torque. These advantages make them a smart choice for high-performance electric motors.
Disadvantages of Segmented Stator Cores
While segmented stator cores offer many benefits, they also come with potential drawbacks. One issue is increased cogging torque compared to traditional integral stators, which can lead to higher noise levels and reduced average torque.
Additionally, segmented designs can cause higher machine saturation and more cutting edges, which may affect performance. Stamping the segments can alter the magnetic and loss characteristics near the steel cutting edges, potentially impacting efficiency.
These factors need careful consideration to ensure that the advantages of segmentation outweigh the disadvantages for specific motor applications.
Conclusion
Segmented stator cores are a game-changer in the world of electric motors. They simplify winding, ease transportation and assembly, allow for diverse material use, enhance material efficiency, and boost reluctance torque. However, it’s important to consider the potential drawbacks such as increased cogging torque and noise. Despite these challenges, the benefits often make segmented stator cores a superior choice for high-performance motors.
Ready to elevate your motor designs with segment electrical steel laminations stator? Contact us today to discuss how we can customize the perfect solution for your needs. Let’s transform your motor technology together!