Do you know how motor lamination materials affect equipment efficiency and performance?
In the manufacturing of motors and transformers, choosing the right motor lamination material is crucial because it directly impacts core loss, power density, and operational stability.
So, what are the common types of motor lamination materials available in the market, and what are their pros and cons?
As a manufacturer with many years of experience in China, I will introduce different types of motor laminations in detail. From silicon steel to iron-based amorphous alloys, this guide will help you select the material that best suits your needs.
Silicon Steel
Silicon steel is a key component in motor laminations, mainly used to guide magnetic flux and reduce energy loss. Based on different manufacturing processes and silicon content, silicon steel can be categorized into several types. Each type has different characteristics and applications. Here are the details:
Classification by Manufacturing Process
(a) Hot-rolled Silicon Steel
Hot rolling is a process where steel is heated above its recrystallization temperature and then rolled. Hot-rolled silicon steel is typically used to make low-cost, mass-produced motor and transformer cores. Due to the poor orientation of the material during processing, its magnetic properties are inferior to those of cold-rolled silicon steel.
(b) Cold-rolled Silicon Steel
Cold rolling is a process where steel is rolled below its recrystallization temperature. Cold-rolled silicon steel offers better magnetic properties. It can be divided into two categories:
If you would like to know more about Grained Oriented Silicon Steel VS Non- Grain Oriented Silicon Steel, please click the link.
Non-Grain Oriented Silicon Steel
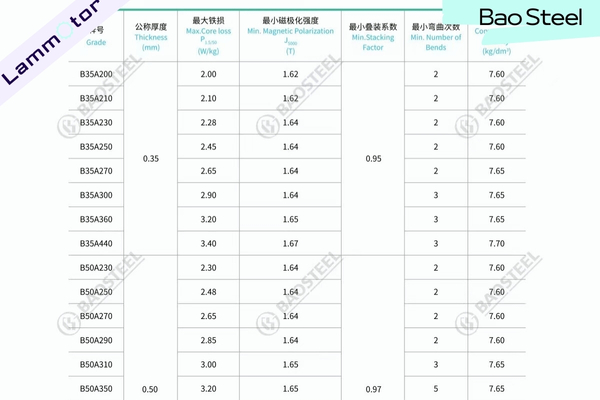
Non-grain oriented silicon steel is processed by cold rolling and contains 1%–3% silicon. It is coated with an insulating layer(C5 coating) and is widely used in motor laminations.
Characteristics:
- Saturation magnetic flux density exceeds 2T
- Excellent magnetic properties
- Easy to process, relatively low cost
- Dominates the global motor lamination market
Applications: Used in motors, welding transformers, and other electrical equipment.
Grain-oriented Silicon Steel
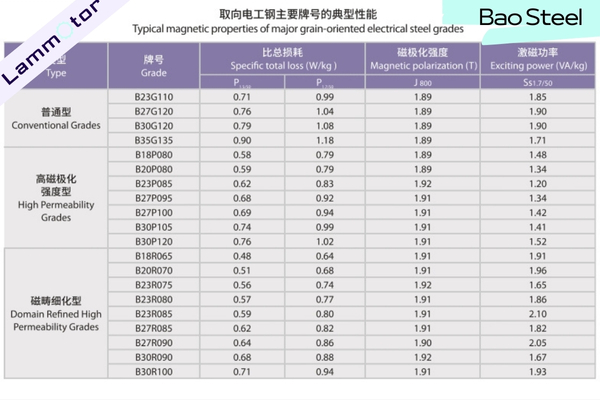
Grain-oriented silicon steel undergoes special cold rolling treatment to optimize its magnetic properties. It is commonly used in high-demand transformers and power supply equipment.
Characteristics:
- Performance superior to non-oriented cold-rolled silicon steel
- Replaces hot-rolled or low-end cold-rolled steel strips, greatly reducing energy consumption in transformers
- Good magnetic conductivity, low core loss, and high punchability
Applications: Common in power supply transformers, pulse transformers, and magnetic amplifiers.
Classification by Silicon Content
(a) Low Silicon Sheets (Silicon content ≤ 2.8%)
Low silicon sheets have a lower silicon content and good mechanical strength. Due to their good magnetic conductivity, they are mainly used in motor laminations. However, their magnetic properties are inferior to those of high-silicon sheets.
Applications: Primarily used in motor manufacturing.
(b) High Silicon Sheets (Silicon content 2.8%–4.8%)
High silicon sheets have better magnetic properties, but they are more brittle. They are usually used for electrical equipment with high magnetic conductivity requirements.
Applications: Mainly used in transformer laminations, also known as transformer silicon steel sheets.
(c) 6.5% Silicon Non-oriented Electrical Steel (6.5% Si-Fe)
This material contains 6.5% silicon and has an insulating coating on its surface. 6.5% Si-Fe has a very low magnetostriction coefficient, significantly improving magnetic properties and reducing core loss.
It is difficult to process and typically manufactured using chemical vapor deposition (CVD) methods, with only one global supplier currently providing this material (JFE Steel), and its annual supply is measured in thousands of tons.
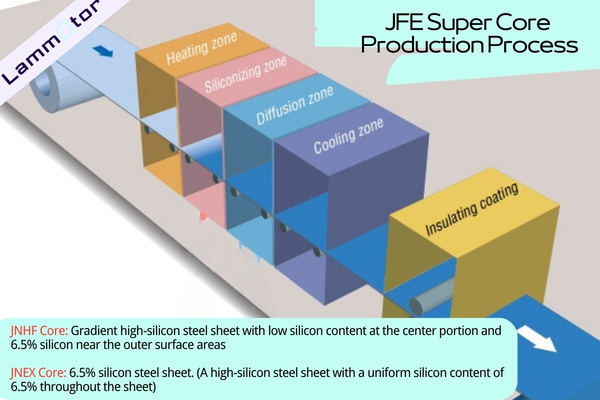
Characteristics:
- Superior magnetic properties, significantly reduced core loss
- Minimal magnetic degradation during processing
- Higher cost, usually around ten times that of ordinary non-oriented silicon steel
Applications: Mainly used in high-end motors and transformers where higher magnetic performance is required.
Magnetic Properties and Usage Considerations for Silicon Steel
Magnetic Flux Density: The magnetic flux density of silicon steel affects the efficiency of motors and transformers. Silicon steels with higher silicon content generally have greater magnetic flux density.
Core Loss: Core loss is a major source of energy loss in motors and transformers. High-silicon steel and grain-oriented steel can significantly reduce core loss, improving equipment efficiency.
Eddy Current Loss: As working frequency increases, eddy current loss increases. Therefore, in high-frequency applications, thinner silicon steel sheets are typically chosen, such as 0.1mm, 0.15mm, or 0.2mm silicon steel sheets.
Processing Performance: The processing performance of silicon steel directly impacts production efficiency and product quality. Cold-rolled silicon steel, with its better processing performance, is often used in precision electromagnetic equipment.
Fe-Co Alloy
Fe-Co alloy, also known as iron-cobalt alloy, is widely used in high-performance soft magnetic materials, especially in applications requiring high magnetic flux density. The notable feature is that the ratio of iron to cobalt is usually close to 1:1, giving it excellent magnetic properties and high-temperature resistance.
Features:
- High Magnetic Flux Density: Fe-Co alloy is one of the materials offering the highest magnetic flux density, making it suitable for electromagnets that require high magnetic performance.
- Excellent Soft Magnetic Properties: It has low coercivity and high saturation magnetic induction, which makes it perform well in magnetic applications.
- Brittleness: During annealing and conventional processing, Fe-Co alloy may become brittle or prone to deformation. To solve this issue, metal injection molding (MIM) technology is often used to produce complex shapes or thin-walled parts.
- Additive Elements: Some Fe-Co alloys include small amounts of vanadium (V) to improve their brittleness. The amount of vanadium added is usually between 0.8% and 1.2%.
Typical Grades:
HiperCo Fe-Co Alloy:
Produced mainly by HiperCo Company, typical grades include HiperCo 50, HiperCo 27, HiperCo 50-V, and HiperCo 27-V.
These alloys offer high magnetic flux density and low hysteresis losses, making them widely used in high-performance electromagnetic devices and precision instruments.
VACOFLUX Fe-Co Alloy:
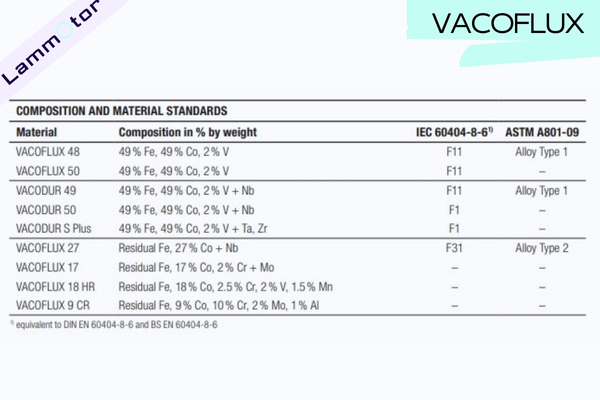
Produced by VACOFLUX (Vacuum Metallurgy Company), typical grades include VACOFLUX 50, VACOFLUX 48, VACOFLUX 35, VACOFLUX 27, and VACOFLUX 50-V.
They perform excellently in high magnetic flux density and low loss, suitable for applications like electron microscopes, medical devices, and superconducting magnets.
Fe-Ni Alloy
Fe-Ni alloy, also known as Permalloy, is made from varying amounts of nickel and iron. The nickel content ranges from 35% to 90%. The main feature of Fe-Ni alloys is their high permeability in weak magnetic fields, with saturation magnetic induction generally between 0.6 T and 1.0 T.
Features:
- High Permeability: Fe-Ni alloys have a high initial permeability, which improves the magnetic response speed of devices.
- Sensitivity: This alloy is highly sensitive to small changes in magnetic fields, making it widely used in magnetic heads, magnetic solenoids, and similar applications.
- Modified Elements: The magnetic properties of Fe-Ni alloys can be adjusted by adding elements such as copper, chromium, or molybdenum to improve their performance.
Applications: Fe-Ni alloys are commonly used in high-sensitivity magnetic applications such as magnetic heads, sensors, and electromagnetic valves.
Soft Magnetic Composites (SMCs)
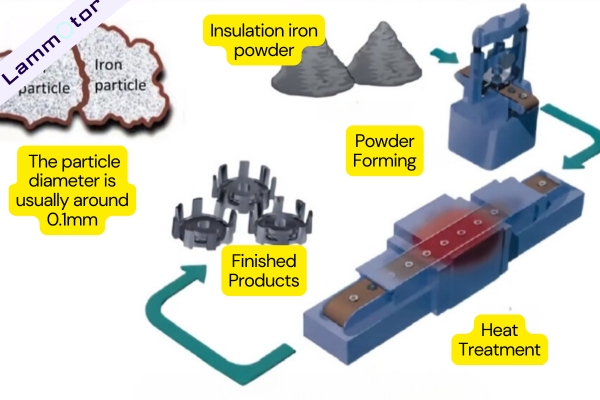
Soft Magnetic Composites (SMCs), also known as magnetic powder cores, are magnetic materials made by uniformly mixing an insulating binder with a magnetic matrix and then pressing the mixture into a specific shape followed by heat treatment.
The particle diameter of SMCs is usually around 0.1mm. The inorganic insulation layer applied on the surface effectively reduces eddy current losses. Common SMC material is Somaloy.
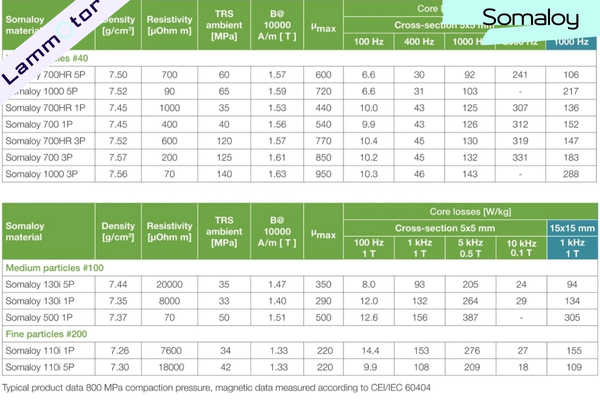
Advantages:
- Soft magnetic composites have low eddy current losses, high permeability, low coercivity, and high resistivity, combining the advantages of both metallic soft magnetic materials and soft magnetic ferrites.
- Compared to metallic soft magnetic materials, SMCs have higher resistivity, which helps reduce eddy current losses at high frequencies.
- Compared to soft magnetic ferrites, SMCs offer higher flux density, making them suitable for smaller electronic components.
SMCs are widely used in applications like axial flux motors due to their isotropic magnetic properties and high material utilization.
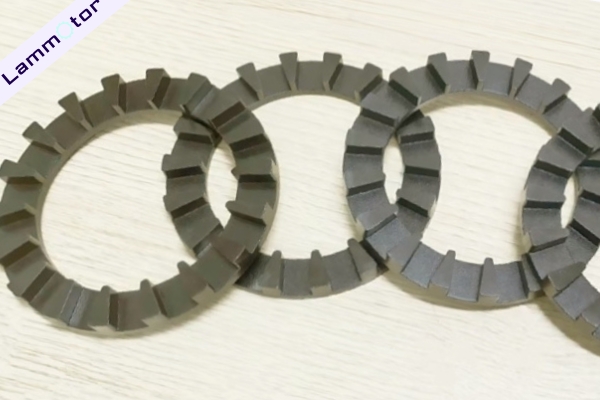
Iron-Based Amorphous Alloys
Iron-based amorphous alloy motor lamination materials have very low iron losses, higher resistivity, and lower eddy current losses. The manufacturing process typically uses a single roller liquid quenching method for continuous casting.
For example, Metglas 2605SA1 (SA1) is made by spraying an alloy liquid of iron, silicon, and boron onto a cooled metal roller, achieving a rapid solidification rate of over 106°C/s. This prevents the growth of crystallization nuclei and results in the production of thin iron-based amorphous strips.
During this casting process, an insulating film of about 10nm naturally forms on the surface of the alloy, so no additional insulation treatment is necessary for most motors and transformers.
Processing Challenges with Iron-Based Amorphous Alloys
However, iron-based amorphous alloys have significant internal stress and a higher magnetostrictive coefficient (27×10^-6), which can affect their magnetic properties. Therefore, they are usually heat-treated in a nitrogen atmosphere at 350°C to relieve stress and improve magnetic characteristics. However, heat treatment can make the material brittle and affect its mechanical strength in motor applications.
Without heat treatment, iron-based amorphous alloys have lower iron losses compared to other core materials, which is their main advantage as motor core materials. However, their saturation flux density (Bs) is only 3/4 of that of non-oriented electrical steel, which is a disadvantage.
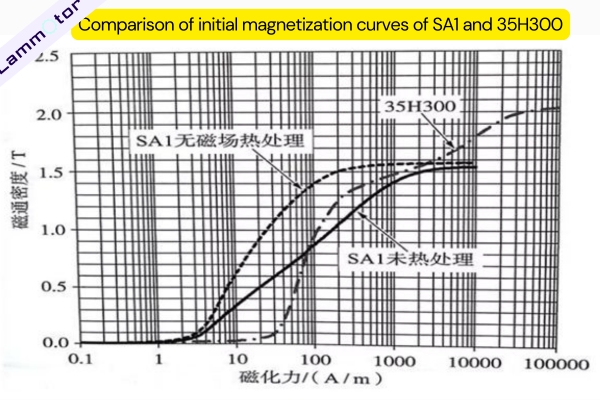
For SA1, to reduce the stress applied to the alloy during casting, a heat treatment in a nitrogen environment without a magnetic field can improve its magnetic properties.
However, SA1 becomes brittle after heat treatment, so it is generally not heat-treated when used in motors.
When the magnetization exceeds Bm=0.8T, SA1’s magnetic field strength becomes higher than 35H300, but its magnetic permeability decreases.
Apart from the degradation of magnetic properties after heat treatment, the main challenge with amorphous alloy cores is their difficulty in processing.
Currently, the common method we use is wire cutting. However, wire cutting takes longer, making it unsuitable for mass production. It is mainly used for simpler applications, like in solar cars, EV go-karts, or experimental prototypes.
Contact Lammotor for Motor Laminations!
In conclusion, selecting right motor lamination materials requires balancing magnetic properties, processing performance, cost, and application needs. Each material has its unique advantages and specific use cases.
As a professional motor lamination manufacturer, Lammotor provides high-quality core materials, including oriented silicon steel, non-oriented silicon steel, Fe-Co alloy, and iron-based amorphous alloys. We can meet the needs of your different motor and transformers.
If you have any questions or need advice on motor lamination materials selection, feel free to contact us. We are happy to offer professional guidance and solutions!