How to Choose Right Drive Motors for New Energy Automobiles? Which One is More Efficient and Reliable?
Why do some new energy vehicles (NEVs) accelerate quickly and run smoothly, while others struggle with weak power and range anxiety? The answer lies in the type, design, and materials of the drive motor for new energy automobiles. Different motors have their own advantages and disadvantages in efficiency, torque, and energy consumption, which directly impact vehicle performance.
As an experienced drive motor manufacturer, we understand how motor technology determines the core competitiveness of an NEV. Today, we will explore the five main types of drive motors for new energy automobiles, discussing their features, pros and cons, and the vehicles that use them.
Five Types of Drive Motors for New Energy Automobiles
Drive motors are one of the most critical components of an NEV. They affect not only power output but also driving range and energy efficiency. Currently, the most common drive motors for new energy automobiles can be classified into the following five types:
1. DC Motor
DC motors were widely used in early electric vehicles (EVs). They operate with brushes and a commutator to convert electrical energy into mechanical motion. However, as technology advanced, the drawbacks of low efficiency, large size, and high maintenance costs became apparent, leading to their replacement by AC motors.
✅ Pros: Simple control, wide speed range, high starting torque.
❌ Cons: Low efficiency, large size, frequent brush wear, high maintenance costs.
Applications
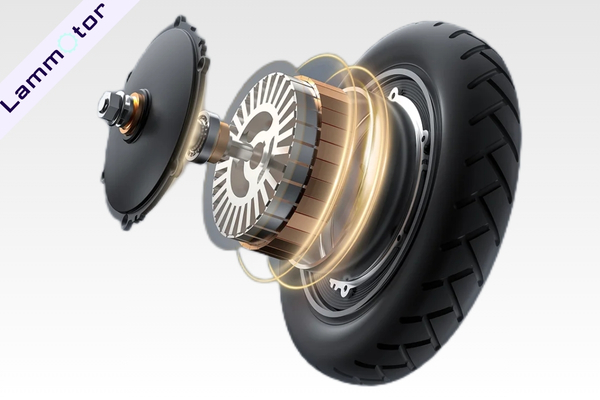
With technological advancements, DC motors are now rarely used in modern EVs. They are mostly found in older or low-speed electric vehicles, such as:
- General Motors EV1 (1996)
- Low-speed EVs (e.g., golf carts, electric tricycles)
2. Induction Motor (Three-Phase Asynchronous Motor)
Induction motors generate a rotating magnetic field using three-phase AC power. The rotor is energized through electromagnetic induction, causing it to spin.
- Uses 120-degree phase-shifted AC power to create a strong and even rotating magnetic field.
- The rotor is typically squirrel-cage type, made of copper or aluminum bars.
- Copper bars improve efficiency but are more expensive.
- Aluminum bars are cheaper and widely used.
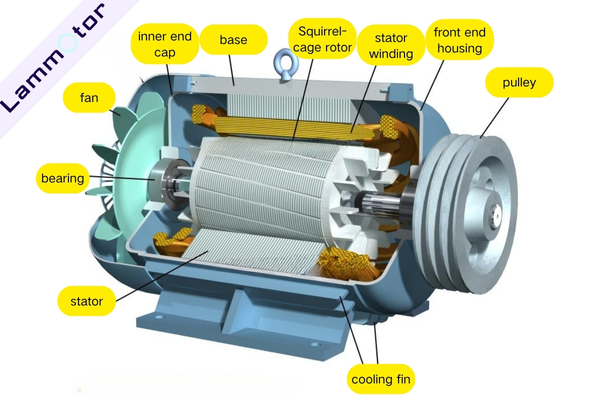
Features
✅ Pros: Simple structure, low cost, durable, no rare earth materials required.
❌ Cons: Lower efficiency than PMSM, especially at low speeds, and lower power density.
Applications
Induction motors are widely used in Tesla vehicles, particularly in early models and AWD systems:
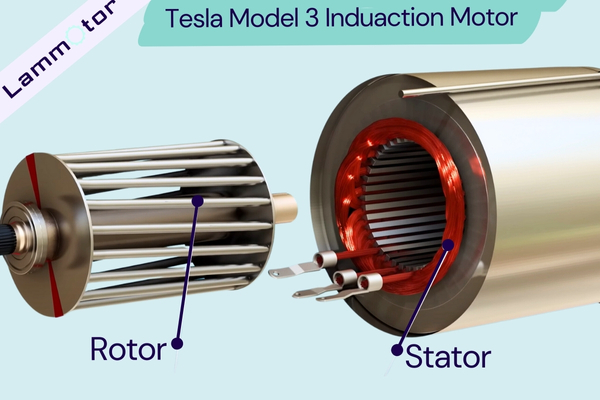
- Tesla Model S/X (Rear axle induction motor)
- Tesla Model 3/Y (Some versions use an induction motor on the front axle)
- Toyota Mirai (Hydrogen fuel cell vehicle, uses an induction motor)
3. Permanent Magnet Synchronous Motor (PMSM)
PMSMs replace traditional excitation windings with permanent magnets in the rotor, ensuring high efficiency and precise speed control. The interaction between the rotating magnetic field from the stator and the fixed magnetic field from the rotor enables smooth and synchronous motion.
Features
✅ Pros: Small size, high efficiency (over 95%), high power density, fast response.
❌ Cons: Relies on rare earth materials (e.g., neodymium magnets), expensive, performance may drop at high temperatures.
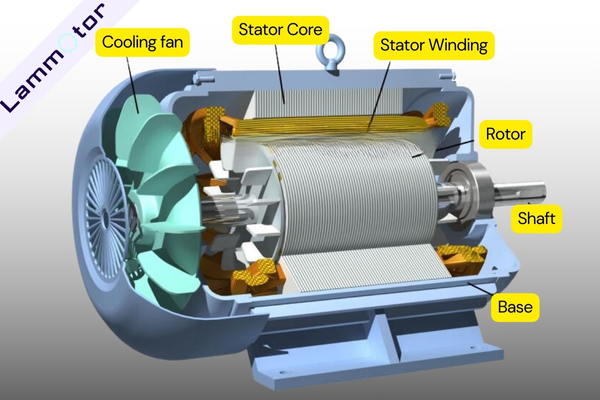
Applications
PMSMs are now the dominant drive motors for new energy automobiles, used in nearly all major EV and hybrid brands:
- BYD (DM-i hybrid models, EV models)
- Tesla Model 3/Y (Rear axle PMSM)
- Toyota & Honda hybrids (e.g., Corolla Hybrid, Accord Hybrid)
- BMW i4, Audi e-tron, Mercedes-Benz EQ series
- Li Auto L7/L8/L9 (Front axle PMSM)
Interior Permanent Magnet Synchronous Motor (IPMSM)
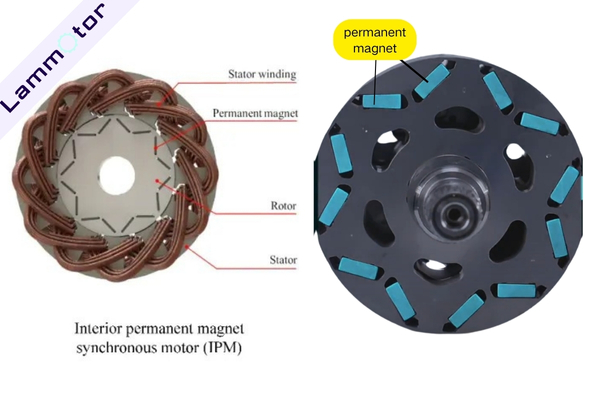
The IPMSM is the most widely used PMSM today. It offers higher efficiency, better flux-weakening capability, and superior high-speed performance.
Tesla Model 3/Y, BYD DM-i, Toyota THS (Hybrid System) all use IPMSMs.
For the PMSM rotor design, if you would like to learn more, please click the link.
4. Switched Reluctance Motor (SRM)
SRMs generate motion by controlling the magnetic reluctance in the rotor. The stator windings receive pulsed currents, which create an alternating magnetic field to attract the rotor into position.
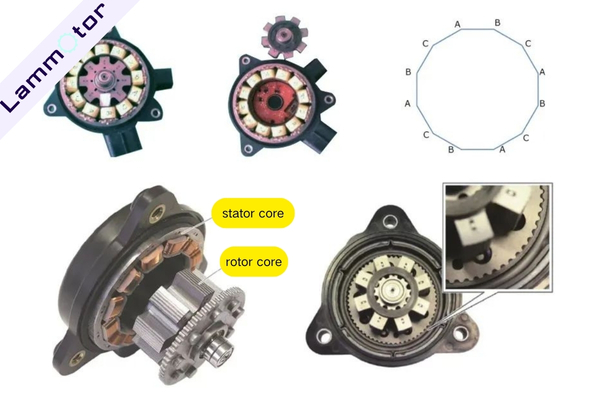
Features
✅ Pros: No rare earth materials, high efficiency, strong temperature adaptability, high reliability.
❌ Cons: Complex control algorithm, high noise and vibration.
Applications
SRMs are still in the early stages of application in drive motors for new energy automobiles, with some brands and commercial EVs adopting them:
- NIO ET7 (Uses SRM as an auxiliary motor)
- Faraday Future FF91
- Electric trucks and buses
5. Axial Flux Motor (AFM)
Axial flux motors differ from traditional radial flux motors. Their magnetic field is aligned along the axial direction, making them more compact while delivering higher power density.
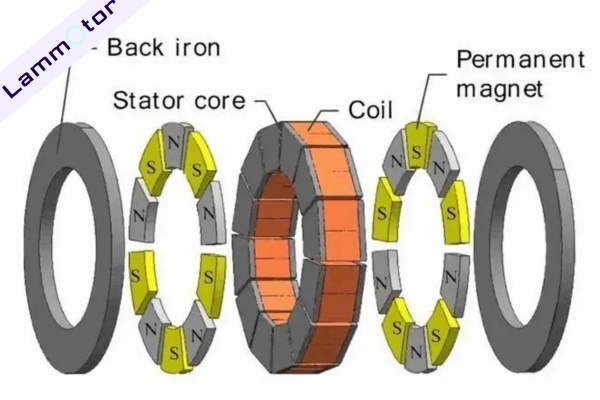
Generally, axial flux motors are divided into four structural types.
- Single stator single rotor
- Single stator double rotor
- Single rotor double stator
- Multiple stators multiple rotors
Features
✅ Pros: Small size, high torque density, high efficiency, ideal for hub motors and high-performance EVs.
❌ Cons: Complex manufacturing, high cost, still in early-stage commercial adoption.
Applications
Axial flux motors are gaining popularity in high-performance EVs and racing cars:
- Koenigsegg Gemera (Uses Rimac axial flux motors)
- McLaren Artura PHEV (Uses axial flux motors for range extension)
- Mercedes-Benz EQXX (Uses YASA axial flux motors)
- Formula E race cars (Some use axial flux motors)
Conclusion
The future of drive motors for new energy automobiles focuses on higher efficiency, better power density, cost reduction, and intelligent control. Permanent Magnet Synchronous Motors (PMSM) remain the mainstream choice, while Induction Motors (IM) continue to be widely used, especially by Tesla. Switched Reluctance Motors (SRM) and Axial Flux Motors (AFM) are emerging as promising solutions for high-performance and specialized applications.
Motor Type | Pros | Cons | Representative Models |
DC Motor | Simple control, high starting torque | Low efficiency, high maintenance | Early EV1, electric tricycles |
Induction Motor (IM) | Simple, no rare earths, durable | Lower power density, less efficient at low speeds | Tesla Model S/X/Y, Toyota Mirai |
PMSM | High efficiency, high power density | Uses rare earths, expensive | BYD DM-i, Tesla Model 3/Y, BMW i4 |
SRM | No rare earths, high efficiency | Noisy, complex control | NIO ET7, electric trucks |
AFM | Compact, high torque density | Expensive, complex production | Mercedes-Benz EQXX, Koenigsegg Gemera |
As new energy vehicle technology evolves, choosing the right drive motor will be key to improving vehicle performance and efficiency. If you are looking for high-quality laminated cores for drive motors, we are here to help!
Contact us today to discuss your motor stator and rotor core manufacturing needs and get customized solutions for new energy vehicle drive motors.