Many of us have an induction motor in our homes and probably use it daily. But induction motors are not the only motor option out there. There are synchronous motors that can often do a better job at running your equipment. This blog will discuss the differences between induction and synchronous motors, their work, and which motor is right for you.
What is an Induction Motor?
An induction motor (also called an asynchronous motor) is a widely used AC motor.
In an induction motor, the current needed to generate torque in the rotor is induced by the rotating magnetic field produced by the stator windings. The rotor can be either a squirrel-cage rotor or a wound rotor.
Induction motors are called “asynchronous” because their operating speed is lower than the synchronous speed.
To understand this, we first need to know: What is synchronous speed?
Synchronous speed is the speed at which the magnetic field of a rotating motor rotates. It depends on the motor’s drive frequency and the number of poles. The operating speed of an induction motor is always less than its synchronous speed. The rotating magnetic field produced by the stator induces flux in the rotor, causing it to rotate.
Because the flux current in the rotor lags behind the flux current in the stator, the rotor can never reach the speed of the rotating magnetic field (i.e., synchronous speed).
Types of Induction Motors
Induction motors are mainly classified based on their input power. There are two main types:
Single-phase Induction Motor
A single-phase induction motor uses a single-phase AC power source. It is commonly used in small household appliances and low-power machines, such as electric fans, washing machines, refrigerators, air conditioners, range hoods, drills, medical devices, small blowers, and domestic water pumps.
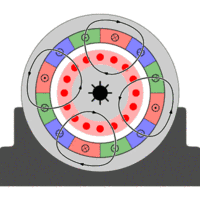
In China, the single-phase voltage is 220V, while in other countries, the voltage varies: 120V in the U.S., 100V in Japan, and 230V in Germany, the UK, and France. Be sure to check that the motor’s rated voltage matches the power supply voltage when using motors from other countries.
Types of single-phase induction motors include:
- Single-phase capacitor-start induction motor
- Single-phase resistance-start induction motor
- Single-phase capacitor-run induction motor
- Single-phase dual-capacitor induction motor
- Single-phase shaded-pole induction motor
Three-phase Induction Motor
Squirrel-cage Induction Motor
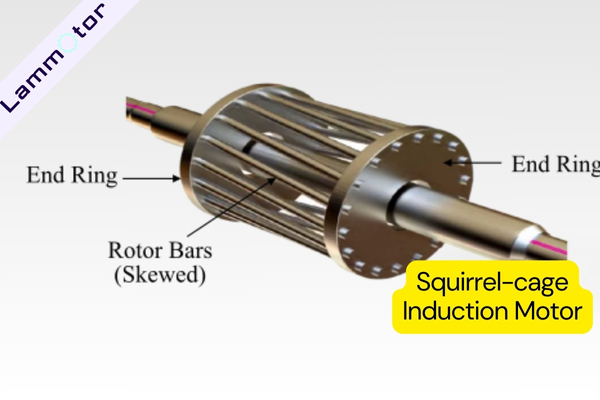
The squirrel-cage rotor is made of a cylindrical laminated iron core with grooves that are nearly parallel or inclined to the shaft. Each groove contains an uninsulated copper or aluminum bar (rotor conductor). At both ends of the rotor, the rotor conductor is short-circuited by end rings made of the same material.
Most industrial three-phase induction motors use squirrel-cage rotors because they are simple, sturdy, and durable. These motors can operate in the harshest environments. However, they have the drawback of low starting torque.
Wound Rotor Induction Motor
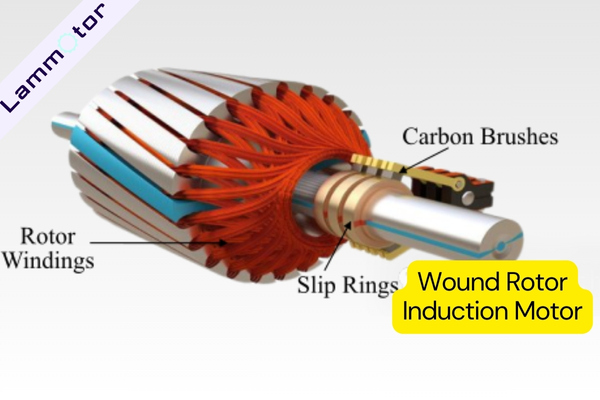
The wound rotor consists of stacked cylindrical armature cores. The rotor has grooves on its surface, which are filled with insulated conductors. These conductors are arranged in a three-phase distributed winding, similar to the stator winding. The rotor windings are connected in a star formation.
The open ends of the star circuit are located on the rotor’s outer surface and connected to three insulated slip rings. These slip rings are mounted on the rotor shaft and are connected to brushes. The brushes connect to three variable resistors, which are also arranged in a star connection. Slip rings and brushes connect external resistances to the rotor circuit.
What is a Synchronous Motor?
In contrast to induction motors, synchronous motors maintain a constant speed under normal operation. Unlike induction motors, where the speed decreases as the load increases, the motor’s speed does not change with varying loads.
The rotor of a synchronous motor can be either a permanent magnet or an electromagnet.
Permanent Magnet Synchronous Motor
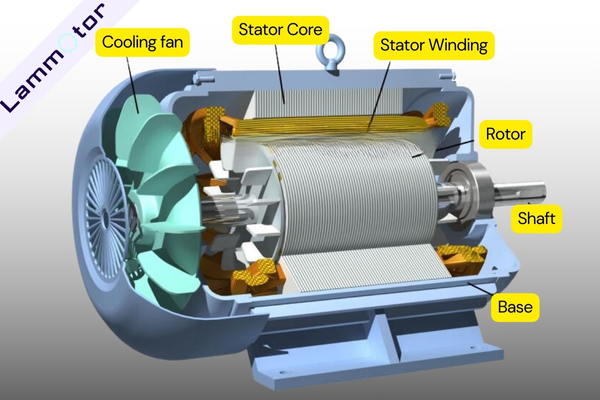
A permanent magnet synchronous motor does not require external excitation. It has no excitation losses and does not need to draw reactive power from the grid. This motor is highly efficient and has a high power density, making it a promising type of motor.
Electromagnetic Synchronous Motor
An electromagnetic synchronous motor can adjust its power factor by changing the excitation. It can operate at a power factor of 1 or even lead the power factor.
If you want to learn more about electric motor types, please click the link.
At present, the electric vehicles on the market generally use induction motor and permanent magnet synchronous motor. If you want to learn more about the motors used in Tesla’s Model 3 cars, click on the link.
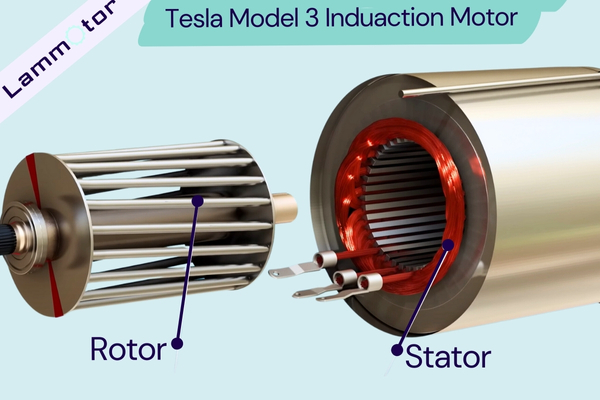
12 Key Differences Between Induction motor and Synchronous Motor
Synchronous Motor | Induction Motor | |
Type of Machine | A synchronous motor is an AC motor, a double excitation machine. | While an induction motor is also an AC motor, a singly excited machine. |
Speed | The speed of a synchronous motor is constant. | The speed of an induction motor varies depending on the load. |
Efficiency | A synchronous motor operates at maximum efficiency when it runs at its rated speed, | while an induction motor operates at the most efficiency when it runs slightly below its rated speed. |
Starting | A synchronous motor has to be started with an external auxiliary power source. | Whereas an induction motor can self-start by itself. |
Power Factor | The power factor in a synchronous motor is either lagging or unity and can be adjusted within these ranges as per needs, | whereas that of an induction machine remains lag by default and cannot be changed. |
Excitation System | Synchronous motors require external excitation for operation. | No external excitation system is needed for induction motors. |
Relative Motion | In the case of the synchronous machine, the rotor rotates concerning the stator winding. | No relative motion like sliding or slipping in the case of induction machines. |
Cost | A synchronous machine costs more than an induction machine owing to its complexity and comparatively higher manufacturing cost. | Induction motors, on the other hand, are cheaper to produce, implement, maintain, and repair. |
Construction | It has salient features on its rotors, such as salient poles or nonsalient poles. | It has squirrel cage rotors without any winding slots. |
Starting Torque | It remains almost constant irrespective of load variations. | It falls with increased loads due to lower slippage for light loads. |
RPM | runs from 150 to 1800 rpm | runs at less than 1500 rpm. |
Applications | Driving mechanical loads constantly, power factor correction of electrical systems, etc. | Driving mechanical loads only |
Type of Machine
A synchronous motor is an AC motor, while an induction motor is also an AC motor but operates differently.
Speed
The speed of a synchronous motor is constant, while the speed of an induction motor varies depending on the load.
Efficiency
Synchronous motors have higher efficiency than induction motors, especially at lower speeds and power factors.
Induction motors, on the other hand, have rotor losses that reduce their overall efficiency. Synchronous motors power their stator while induction motors power their rotor, inducing current and causing torque.
Asynchronous induction motors create slip, which increases torque but reduces efficiency. In synchronous motors, current flows continuously in one direction, thus requiring less power input.
This is due to the speed-torque characteristics of the synchronous motor being constant over a range of speed and voltage settings.
A synchronous motor provides higher efficiency than an induction motor at lower speed and power factor values.
Starting
Synchronous motors typically start with cage winding embedded in the pole faces to give an induction-motor torque when the stator is energized. The motor is started with full or reduced stator voltage and brought up to about synchronous speed, usually with the field winding short-circuited to protect it from excessive induced voltage.
Asynchronous motors can start when they supply power to the stator, eliminating the need for a power source to excite or start the rotor.
These motors are typically more power-efficient than synchronous motors and are, therefore, widely used in applications where speed accuracy is of primary importance.
Power Factor
The power factor of a synchronous motor can be adjusted within a range of lagging to unity, while the power factor of an induction machine remains lag by default and cannot be changed. This allows synchronous motors to adjust their power factor depending on the user’s needs, whereas induction motors are stuck with lagging power factors.
Excitation System
Synchronous motors require external excitation for operation. However, no external excitation system is needed for induction motors.
Synchronous motors require an external excitation system to be operational, whereas induction motors do not need any external excitation systems.
This difference affects the ease of operation for both motor types; synchronous motors may require more time and effort, but they can offer greater control than induction motors.
Relative Motion
Synchronous machines have a rotor that rotates in synchronization with the field, while induction machines rely on the principle of electromagnetic induction to produce relative motion between the stator and rotor.
Synchronous motors are used in applications where precise speed control is required, as they can precisely adjust their operating speed to match the frequency of an alternating current supply. This makes them useful in applications such as AC power generators, high-speed printing presses, and robotic systems.
On the other hand, induction motors provide reliable operation at low cost and low maintenance requirements; they are used in most industrial processes, such as fans and pumps.
Cost
no relative motion like sliding or slipping in the case of induction machines. Due to the complexity involved in their production and operation. Induction motors, on the other hand, are cheaper to produce, implement, maintain, and repair.
Synchronous motors require an external excitation system which adds additional costs and may make it more expensive than an equivalent induction motor.
Additionally, synchronous motors have more parts that must be constructed and assembled.
On the other hand, due to their simpler design and single-phase winding structure, induction motors are usually cheaper than synchronous machines.
However, compared with synchronous machines, induction motors usually have a lower power factor and less efficient performance.
Construction
Synchronous machines have salient features on their rotors, such as salient poles or nonsalient poles, which enable them to produce a magnetic field directly due to current passing through the rotor coil, thus resulting in a rotating magnetic field inside the stator coils hence generating torque.
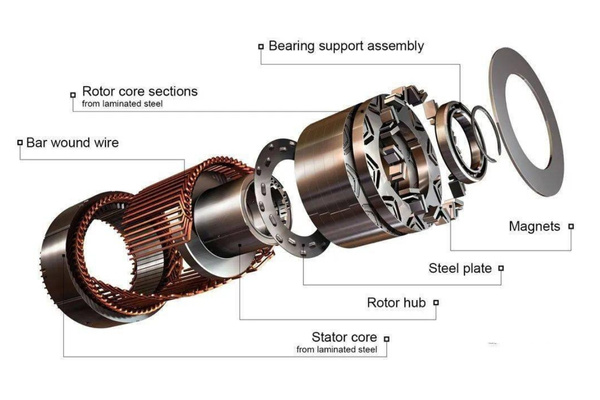
construction of synchronous motor
On the other hand, Induction motors have squirrel cage rotors without any winding slots, so they don’t possess any way to generate a magnetic field as such hence making use of induced currents from the stator only, which results in a rotating Magnetic Field, thereby producing torque in the rotation direction.
Starting Torque
Starting torque for synchronous motors remains almost constant irrespective of load variations. However, induction motors starting torque falls with an increase in loads due to lower slippage present for light loads & rises sharply with an increase in loads due to higher slippage occurring from high load cases.
RPM
The speed of synchronous motors is constant, while the speed of induction motors varies depending on the load.
The speed of a synchronous motor can be controlled with its excitation system, while the speed of an induction motor cannot be adjusted but only vary depending on the load applied.
Applications
Synchronous motors are generally used where very precise control over speed/torque is required, like paper mills & compressors, and so on. However, induction motors are widely used where variable speeds are needed & also employed in applications like pumps, fans, elevators, compressors, etc.
- Relatively low cost
- High starting torque over a wide speed range
- Very rugged construction and simple maintenance requirements
- High efficiency compared to other types of motors
- Ability to be designed as both single-phase and poly-phase motors
- Can operate with variable frequency drives for more precise speed regulation
Conclusion
We hope you have found this comparison helpful and helped you make a better-informed decision. If you are looking for motor cores that efficiently provide power, we have just the thing for you – our range of motor cores. Want to know more? Contact us today!