In the bustling world of industrial machinery and advanced electronics, DC motors are unsung heroes, powering countless devices and systems around us. These motors have transformed industries with distinct designs and versatile applications, driving innovation everywhere. The journey of DC motors, from their inception to their pivotal role in contemporary applications, is fascinating.
As experts in manufacturing the DC motor cores that form the heart of these motors, we’re excited to delve deep into the intricacies of DC motors: their foundational principles, diverse types, and indispensable presence in today’s dynamic industry landscape.
History and Evolution of DC Motors
Journeying back to the late 19th century, the genesis of the DC motor marked a watershed moment in technological advancements. American inventor Thomas Davenport pioneered the first practical DC motor in 1834. But it wasn’t until the diligent efforts of scientists like Nikola Tesla and Thomas Edison that DC motors began to evolve and find a foothold in various industries.
The Early Beginnings:
The initial versions of DC motors were bulky, less efficient, and expensive. Built primarily with rudimentary materials, they were primarily utilized for niche applications. Over time, with better materials and more precise manufacturing techniques, these motors became smaller, more efficient, and more accessible to a broader range of applications.
The 20th Century Surge:
As industries burgeoned during the 20th century, the demand for reliable and efficient power sources skyrocketed. With their unparalleled controllability and range of speeds, DC motors perfectly fit the bill. The automotive industry, in particular, embraced these motors, particularly useful in starter mechanisms and later in the realm of electric vehicles.
Modern Innovations:
The dawn of the 21st century witnessed a leap in technology and materials science. Advanced composites, more resilient and conductive materials, and state-of-the-art manufacturing processes have supercharged the efficiency and durability of direct current motors. Brushless motors, in particular, emerged as a game-changer, offering longer lifespans and minimal maintenance, further solidifying the ubiquitous presence of DC motors in every sector.
Fundamentals of DC Motors
At their core, DC motors revolve around a simple yet profound principle: converting direct current (often sourced from batteries) into mechanical energy. This conversion is achieved through the interaction of magnetic fields and current-carrying conductors. A DC motor transforms electrical energy into mechanical energy by creating a magnetic field powered by direct current. Let’s break this down a bit.
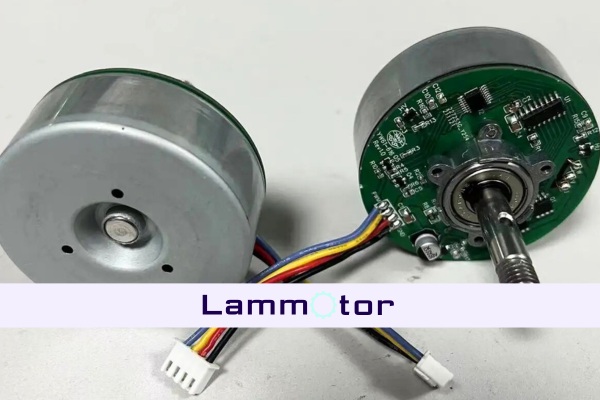
Basic Working Principle:
When a current flows through a conductor within a magnetic field, a force acts upon it. This force, governed by Lorentz’s Law, instigates motion. In a DC motor, this movement is harnessed to create rotational motion, driving everything from fans to electric cars.
Key Components and Their Roles:
Integral to this system are a few vital components. The armature is the primary current-carrying conductor, often wound into coils. The commutator and brushes work to ensure unidirectional current flow in the armature. Lastly, the field windings create a magnetic field, which can be externally or internally located.
The beauty of DC motors lies in their versatility, ensuring they can be tailored for myriad applications. Through advances in design and core manufacturing, the efficiency and performance of these motors have reached unprecedented levels.
How Does DC Motors Work?
A DC motor, or a direct current motor, works through the interaction between a magnetic field and an electrical current. The basic structure of a DC motor consists of a rotor and a stator. The rotor contains a coil, the armature, while the stator consists of a fixed magnetic field.
When an electric current passes through the coil, it generates a magnetic field that interacts with the stator’s magnetic field. This interaction creates a torque, causing the rotor to rotate. The direction of rotation can be reversed by changing the direction of the current flow within the coil. Direct current motors are commonly used in various applications, such as electric vehicles, robotics, and industrial machinery.
Related Articles: Brushless VS Brushed DC Motors: What’s The Difference? Stepper Motor Vs. Servo Motor: A Comprehensive Comparison Difference Between Synchronous Motor And Induction Motor
Types of DC Motors
As industries have evolved, so have the requirements of motors. Catering to various needs, different types of motors have been developed. Each comes with its unique set of characteristics, advantages, and ideal applications.
A. Brushed DC Motors
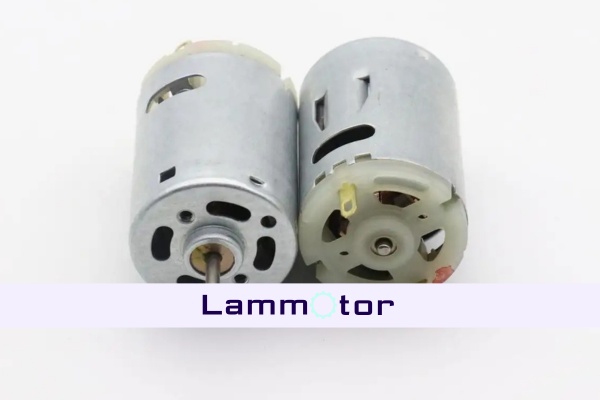
Central to brushed DC motors is the presence of brushes, which maintain contact with the motor’s commutator.
Working Principle: The brushes transfer current to the commutator, supplying the armature winding. As the armature rotates within the magnetic field, torque is produced, resulting in motion.
Pros and Cons:
Advantages: Simplicity in design, cost-effective, and good torque at low speeds.
Disadvantages: Regular maintenance is required due to brush wear, less efficient than brushless variants, and limited lifespan.
Series DC Motors:
Characteristics: Field windings are connected in series with the armature. High torque, but the speed varies with the load.
Suitable Applications: Starters in automobiles and tools where sudden torque is beneficial.
Shunt DC Motors:
Characteristics: Field windings connected in parallel with the armature. Offers consistent speed but with less torque.
Typical Usage Scenarios: Fans, blowers, and centrifugal pumps where consistent operation is crucial.
Compound DC Motors:
Characteristics: A fusion of series and shunt motors. Field windings are both in series and parallel to the armature.
Industries Where They Shine: Printing presses and elevators with high torque and stable speed are essential.
PMDC Motors (Permanent Magnet DC Motors):
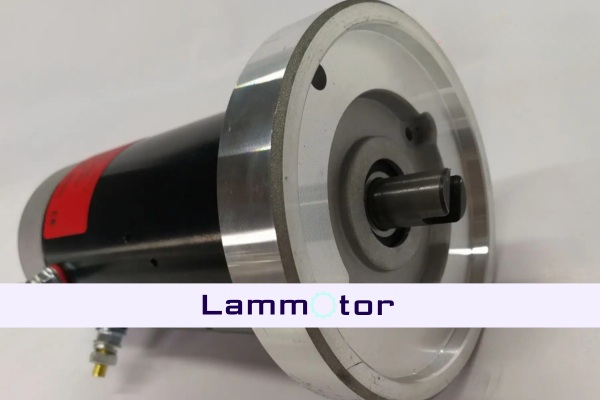
Characteristics: Instead of field windings, permanent magnets produce the magnetic field. Compact in design and efficiency.
Suitable Applications: Toys, computer drives, and personal care appliances.
B. Brushless DC Motors
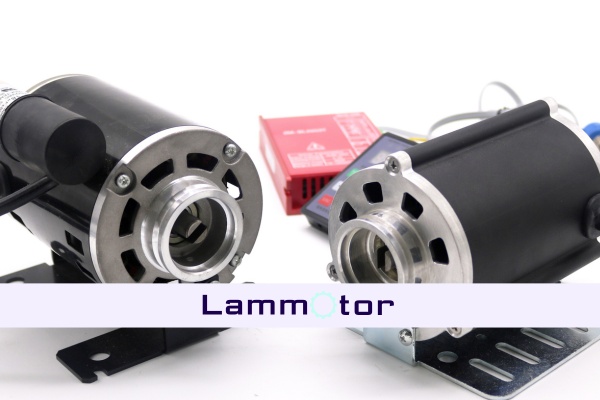
The evolution of direct current motors gave birth to brushless versions, eliminating brushes and the commutator.
How They Differ from Brushed Motors: The main distinction is the absence of brushes. They utilize an electronic controller instead of the mechanical commutation to rotate the motor.
Benefits of Using Brushless Technology:
Advantages: Longer lifespan, less maintenance, higher efficiency, and quieter operation. They also offer better performance and torque over a wider speed range.
Uses of DC Motors in Today’s Industry
The versatility and efficiency of direct current motors have paved the way for their integration into many applications. Their adaptability ensures they remain at the forefront of numerous industries, continually shaping the modern world.
A. Automation and Robotics:
In automation and robotics, precision, reliability, and adaptability are paramount. Direct current motors fit seamlessly into this domain. Their capacity to offer consistent speed control is instrumental in tasks ranging from precise assembly line functions to the fluid movements of robotic arms.
B. Electric Vehicles (EVs):
The global push towards sustainable and eco-friendly transport solutions has underscored the importance of electric vehicles. Here, direct current motors shine brilliantly. Their efficiency and ability to provide high torque at low speeds make them ideal for propelling EVs, ensuring smoother acceleration and better performance.
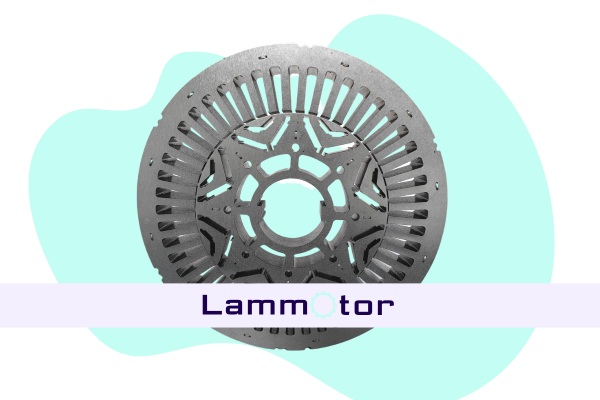
C. Medical Equipment:
Whether it’s powering respiratory devices, driving infusion pumps, or facilitating surgical tools, the precision and reliability of DC motors ensure that critical medical equipment functions optimally, sometimes even making the difference between life and death.
D. Consumer Electronics:
Our homes are replete with gadgets and appliances, many of which owe their functionality to direct current motors. From the spin of a DVD player to the oscillation of a desktop fan, these motors have woven themselves into the fabric of our daily lives, enhancing comfort and convenience.
E. Industrial Machineries:
Heavy-duty applications in industries demand robust and durable motors. With their ability to offer high torque and withstand demanding operational scenarios, the DC motor is a mainstay in many industrial machines. From lathes to milling machines, their presence ensures that industries churn out products efficiently and consistently.
Conclusion
As we navigate the intricate landscape of DC motors, one thing becomes clear: their importance in today’s world is undeniable. From powering innovations in burgeoning industries to facilitating everyday conveniences, direct current motors have cemented their place in the annals of technological evolution. Their adaptability, efficiency, and versatility resonate with the demands of the modern era, making them an integral component in shaping the future.
If you’re as captivated by the potential of DC motors as we are, it’s time to dive deeper. Whether you’re in the industry seeking customized motor core laminations or simply curious about electric motors, we’re here to guide and assist. Explore our range of services, tap into our expertise, and let’s embark on a journey of innovation together. Click here to contact our team of experts or delve further into our treasure trove of resources.
FAQs
What’s the primary difference between DC and BLDC (Brushless DC) motors?
The most significant difference lies in how they are constructed and operated. DC motors use brushes and a commutator to transmit electrical current, whereas BLDC motors eliminate brushes, relying instead on an electronic controller for commutation. This leads to less maintenance, a longer lifespan, and greater efficiency in BLDC motors compared to traditional brushed DC motors.
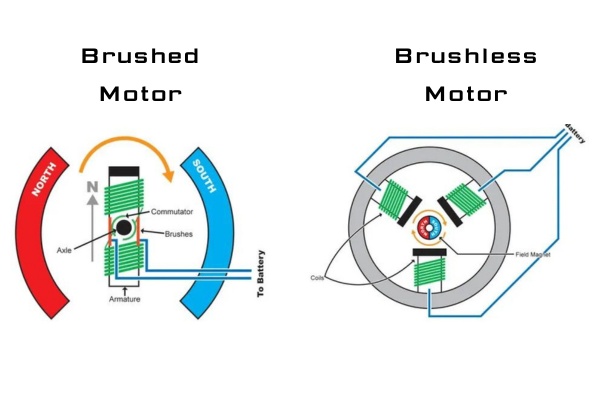
How do DC motors differ from AC motors?
The primary distinction is the type of electrical current they run on. DC motors utilize direct current (DC), often sourced from batteries, while AC motors operate on alternating current (AC) typically supplied from the power grid. The AC motors include induction motors and synchronous motors. This fundamental difference also affects their construction, performance characteristics, and applications. The DC motor often provides better torque at low speeds, whereas AC motors can be more efficient at higher speeds and are commonly used in large industrial applications.
Can DC motors be used in place of AC motors and vice versa?
While in some applications, it might be possible to interchange them, it’s not always practical. Each motor type has its inherent advantages and drawbacks. The decision depends on the application’s specific requirements, like speed control, torque needs, efficiency, and overall system design.
What are the maintenance requirements for DC motors?
Due to brush and commutator wear, traditional brushed DC motors require more frequent maintenance than their brushless counterparts. This includes checking and replacing brushes, cleaning the commutator, and ensuring proper lubrication. On the other hand, BLDC has fewer wear-prone parts, resulting in reduced maintenance needs.
Why are DC motors commonly used in electric vehicles?
DC motors, especially BLDC types, provide high torque at low speeds, making them ideal for the stop-and-go nature of city driving. Their simplicity, efficiency, and performance characteristics align well with the requirements of electric vehicles, facilitating smoother acceleration and adaptability to varying driving conditions.