Soft magnetic composites may not sound like the most exciting topic, but for motor manufacturers, they could very well be the key to unlocking a brighter, more efficient future. These innovative materials offer a range of benefits that traditional magnetic materials simply can’t match. From improved efficiency and reduced energy loss to greater design flexibility, the potential of soft magnetic composites is truly staggering.
In this blog post, we’ll delve into why these materials are causing such a stir in the industry and how they could revolutionize the way motors are designed and manufactured. So if you’re a motor manufacturer looking to stay ahead of the curve and drive innovation in your products, this is one blog you won’t want to miss!
What Are Soft Magnetic Composites?
Soft Magnetic Composites, or SMCs, are advanced materials engineered for their magnetic properties. Unlike traditional magnetic materials, SMCs comprise insulated iron powder particles dispersed in a non-conducting matrix, such as epoxy or polymer. This unique composition allows for tailored magnetic properties and versatile applications.
The development of SMCs traces back to the late 20th century when researchers began exploring methods to improve the performance of magnetic materials. Over the years, advancements in material science and manufacturing techniques have led to significant breakthroughs in SMC technology, making them increasingly popular across various industries. Today, SMCs are at the forefront of innovation, driving efficiency, sustainability, and reliability in countless applications.
The Unique Properties of Soft Magnetic Composites
Soft Magnetic Composites are created by coating each iron particle with an insulation material. Soft Magnetic Composites materials boast a plethora of unique properties that set them apart from traditional magnetic materials:
High Permeability and Low Coercivity
SMCs exhibit exceptional magnetic permeability, allowing them to channel magnetic flux efficiently. This property, coupled with low coercivity, enables precise control and manipulation of magnetic fields, essential for various applications.
Customizable Shapes and Sizes
By powder metallurgy techniques, SMC materials offer unparalleled flexibility in shaping and sizing. Manufacturers can tailor these materials to meet specific design requirements, resulting in intricate and customized components for diverse applications.
Superior Performance at High Frequencies
Unlike conventional magnetic materials, SMCs maintain their magnetic properties even at high frequencies. This attribute makes them ideal for applications demanding rapid magnetic field changes, such as in transformers, inductors, and high-frequency power supplies.
High Material Efficiency and Low Production Energy
SMCs are characterized by high material efficiency, as they minimize waste during production. Additionally, the manufacturing process of SMCs requires relatively low energy consumption, contributing to overall sustainability and cost-effectiveness.
Elimination of Joining Multiple Laminations
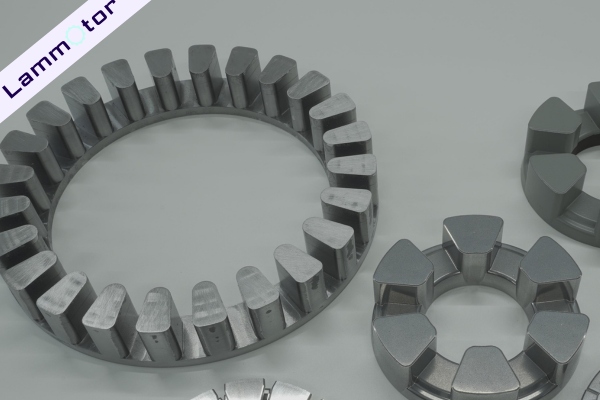
Unlike traditional silicon steel laminated cores, SMCs remove the need for joining multiple laminations by interlocks or welding or glue bonding. Both welding and stacking significantly increase the core loss (heat) generated by the device. This simplifies the manufacturing process, reduces assembly time, and enhances overall reliability by eliminating potential points of failure.
3D Magnetic Flux Pathway
SMC components offer the unique advantage of a 3D magnetic flux pathway. Unlike electrical steel motor cores where the flux path is constrained to the plane of the laminations, SMCs allow for multidirectional flux flow, providing greater design flexibility and efficiency in magnetic circuits.
Lower Overall Core Losses at Higher Frequencies
SMCs exhibit lower core losses, particularly at higher frequencies, compared to silicon steel and amorphous materials. The starting material is an insulated fine ferrous powder, which confines losses to individual particle sizes, resulting in improved efficiency and performance in high-frequency applications.
These remarkable properties make SMCs indispensable in modern engineering, offering unparalleled versatility and performance across a wide range of applications. Whether in automotive, renewable energy, or electronics, SMCs continue to redefine the boundaries of magnetic technology.
Conclusion
In conclusion, the transformative potential of Soft Magnetic Composites (SMCs) is undeniable. With their unique properties, including high permeability, customizable shapes, and superior performance at high frequencies, SMCs are poised to revolutionize numerous industries.
From electric vehicles to renewable energy systems, SMCs offer efficiency, sustainability, and reliability like never before. As we continue to innovate and integrate SMC technology into various applications, the future looks brighter and more magnetic than ever.
So, let’s embrace the power of SMCs and unlock a future where efficiency and sustainability go hand in hand, with a touch of magnetic charm!
FAQs
What are soft magnetic composites (SMCs) made of?
Soft Magnetic Composites (SMCs) are primarily composed of insulated iron powder particles dispersed within a non-conducting matrix, such as epoxy or polymer. This unique composition enables tailored magnetic properties and versatile applications across various industries. SMCs are engineered to exhibit high magnetic permeability, low coercivity, and superior performance at high frequencies.
What are the main applications of soft magnetic composites?
Soft Magnetic Composites (SMCs) find widespread use in various applications, with electric motor cores being a primary application. SMCs are utilized in electric vehicles, renewable energy systems, power electronics, and aerospace, among others. Their unique properties, including high permeability and low core losses, make them ideal for efficiently channeling magnetic flux in motor cores, enhancing performance and energy efficiency.
How does the soft magnetic material affect the performance of an axial flux motor?
Soft magnetic materials determine the motor’s efficiency, power density, and overall performance. By efficiently channeling magnetic flux and minimizing core losses, SMCs enhance the motor’s electromagnetic properties, enabling higher power output, reduced energy consumption, and improved thermal management. It helps to reduce vortex losses and increase the thrust of the machine.
Additionally, SMCs enable compact and lightweight motor designs, further enhancing their performance in axial flux motor applications.