Ever wondered what makes electric motors and transformers run more efficiently? The answer lies in the advanced technology of Backlack lamination bonding.
This cutting-edge stacking method not only enhances performance but also cuts down on energy losses.
Next, we’ll dive into the intricacies of Backlack bonding, explaining why it’s considered the best stacking technology for stator and rotor lamination stacks.
By the end, you’ll have a solid understanding of how this process works and why it’s a game-changer for various industries. Let’s get started!
What is Backlack Lamination?
Backlack lamination is an advanced bonding technique used in the manufacturing of electric motor and transformer cores. Unlike traditional methods that rely on welding or interlocking, Backlack uses a special type of bonding agent applied to the lamination sheets. When heated, this agent fuses the sheets together, creating a strong and efficient bond.
The adhesive materials commonly used in Backlack lamination include specialized bonding agents such as EB540, EB546, EB548, and EB549 glue. These agents are designed to enhance the electrical and mechanical properties of the lamination stack, ensuring optimal performance. By using these adhesive materials, Backlack lamination achieves a precise and uniform bond, significantly reducing energy losses and improving the overall efficiency of the electrical components.
Process of Backlack Bonding Lamination Stacks
The process of Backlack bonding for lamination stacks begins with the application of a self-bonding coating solution on both sides of electrical steel sheets. This coating is then baked on a production line, creating a partially cured semi-finished product. The key to this process lies in the multi-stage heating and curing of the Backlack coating.
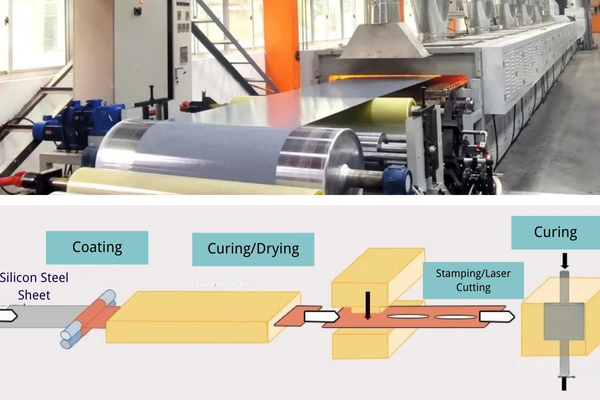
In the initial stage, the Backlack coating is softened by raising the temperature. During this phase, the viscosity of the coating drops dramatically, allowing it to diffuse and mix effectively. This stage largely determines the quality of the bond, as the thorough melting of the coating results in high bonding strength and significant resistance to various environmental factors.
Following this, the lamination stacks undergo a heat curing process. This step significantly increases the viscosity and bonding strength between the laminations. The cured bonds in the motor core eliminate the stresses and iron loss variations typically caused by welding or riveting electrical steel, thus enhancing the overall performance of the motor. Additionally, the bonded core reduces vibration and noise during the core’s rotation, making it particularly suitable for high-frequency, high-speed motors.
By avoiding traditional methods like welding and riveting, Backlack bonding technology maintains the integrity of the electrical steel, resulting in higher efficiency and reliability. This innovative technique ensures that the motor cores have minimal internal stresses and optimal magnetic properties, which are crucial for high-performance applications.
Benefits of Bonding Varnish/Bonding Lamination Stacks
Bonding varnish for lamination stacks offers several significant benefits that enhance the performance and reliability of electric motors and transformers.
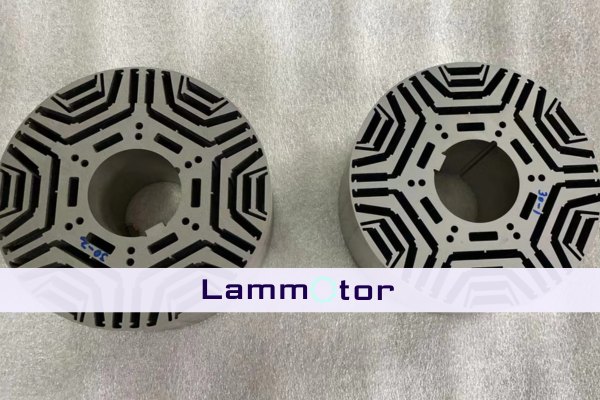
1. Improved Mechanical Stability:
The bonding process creates a robust and uniform bond between the laminations, increasing the overall mechanical stability. This stability is crucial for maintaining the structural integrity of the core during high-speed operations.
2. Enhanced Electrical Performance:
Bonded lamination stacks exhibit superior electrical properties. The uniform bond ensures minimal electrical resistance between laminations, leading to improved conductivity and overall electrical performance.
3. Reduced Eddy Current Losses:
The application of bonding varnish significantly reduces eddy current losses. By minimizing these losses, the efficiency of the motor or transformer is enhanced, leading to lower energy consumption and better performance.
4. Reduces Both Vibration and Noise:
The bonded lamination stacks are tightly held together, which effectively reduces vibration and noise during operation. This reduction in mechanical noise contributes to a quieter and more efficient machine.
5. No Short Circuits Between Laminations:
Bonding varnish prevents direct short circuits between the laminations, resulting in better magnetic properties and fewer losses. This feature ensures that the magnetic flux is efficiently contained within the core, enhancing the overall performance and reliability of the device.
In conclusion, the use of bonding varnish in lamination stacks offers numerous benefits, including improved mechanical stability, enhanced electrical performance, reduced eddy current losses, decreased vibration and noise, and better magnetic properties with fewer losses.
Other Common Stacking Technologies for Motor Lamination Stacks
Motor lamination stacks can be assembled using various stacking technologies, each with its own advantages:
1. Interlocking: This method involves creating tabs and slots on the laminations that fit together, ensuring precise alignment and mechanical stability. It is a cost-effective solution that requires minimal additional materials.
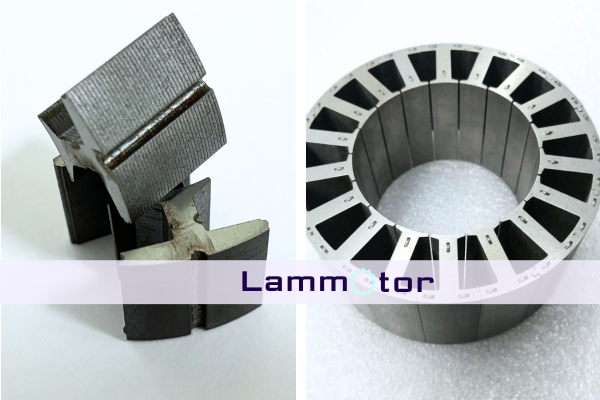
2. Cleat: Cleating uses small metal strips to secure the laminations together. This method provides strong mechanical integrity and is often used in larger motors.
3. Rivet: Riveting involves inserting and securing metal rivets through the lamination stack. This method offers robust mechanical strength but can introduce additional stress and potential for electrical losses.
4. Laser Welding: Laser welding uses focused laser beams to join the laminations. It offers high precision and minimal thermal distortion, resulting in a strong and clean bond ideal for high-performance applications.
Conclusion
In summary, Backlack bonding stands out as the premier technology for motor lamination stacks. It offers improved mechanical stability, enhanced electrical performance, reduced eddy current losses, and minimized vibration and noise. This advanced method ensures optimal magnetic properties and efficiency, making it a game-changer in the industry.
Ready to upgrade your motor cores with Backlack bonding? Contact us today to customize your lamination stacks and experience the future of motor performance.