Laser cutting rotor laminations is an advanced production method that has revolutionized how prototypes are created. It is a perfect method for motor lamination stack prototyping due to its accuracy, repeatability, and precision, which can be achieved with minimal effort.
Laser cutting also offers significant cost savings compared to traditional fabrication methods, making it an attractive option for small-scale production runs. This article will discuss the advantages of laser cutting and why it is so widely suitable for rotor lamination prototyping.
What is laser cutting rotor lamination?
Laser cutting lamination is a high-precision manufacturing process used to make the laminations used in electric motors. This process employs a laser beam to cut out various shapes from sheets of metal accurately. The resulting shapes are stacked and bonded to form the complex laminations required for electric motors.
Laser cutting rotor lamination ensures a consistently precise cut every time, resulting in perfectly uniform laminations that are critical for the smooth operation of electric motors. This cutting-edge technology is suitable for various industries, from automotive to aerospace, to create the most efficient and reliable electric motors.
What are the benefits of laser cutting rotor laminations for motors?
Laser cutting rotor laminations for motor lamination prototyping offers several benefits.
Firstly, the precision of laser cutting ensures that the lamination plates are cut to exact specifications, ensuring high precision in the final product. This can help to reduce the risk of errors and waste while also improving the overall efficiency of the production process.
Also, laser cutting is a non-contact process, which means there is less wear and tear on the machinery, leading to lower maintenance costs and a longer lifespan. Laser cutting is also faster than traditional cutting methods, which can help to reduce lead times and bring products to market more quickly.
Finally, using laser cutting for motor lamination prototyping allows for greater versatility in terms of design options. Laser cutting can create intricate and complex shapes, ensuring the final product is functional and aesthetically pleasing.
Laser-cutting rotor laminations offer advantages for anyone creating high-quality motor laminations for various applications.
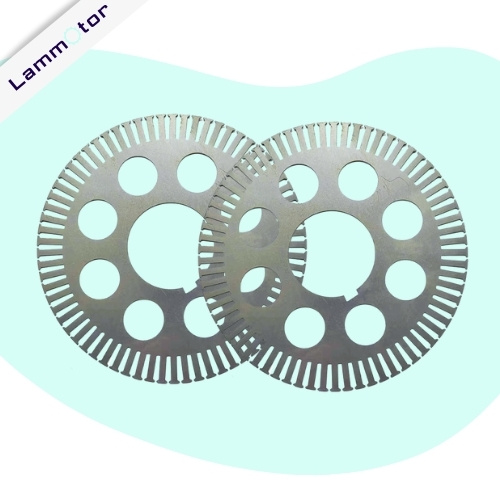
Different Materials Available For Rotor Lamination
Rotor lamination is essential to electric motor manufacturing, and several materials are available.
Silicon steel is the most common material for rotor lamination due to its high permeability and low core losses.
Cobalt and nickel alloys are also popular for their excellent magnetic properties, making them ideal for high-performance motors.
Thin-gauge electrical steel is another option for rotor lamination and is often suitable for high-efficiency applications.
All of these materials have their advantages and disadvantages, and the selection of material will depend on the specific application and the performance requirements of the motor.
Choosing the right material is crucial to ensure that the motor functions efficiently and reliably and ultimately provides the desired performance.
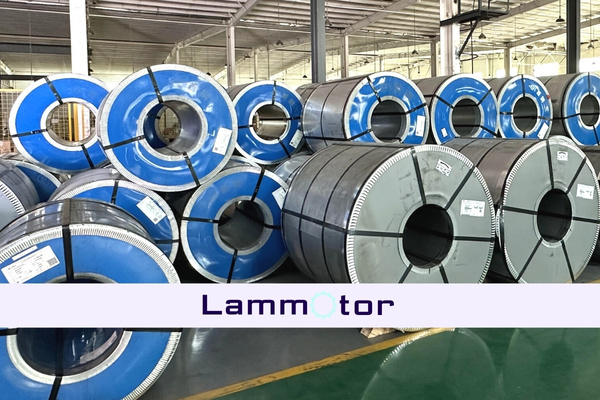
Rotor Laser Cut Laminations Industries Served
Automotive Industry: The automotive industry significantly uses motor rotor lamination. Motor rotors are suitable extensively in engines, transmissions, and starters. They provide the necessary support to the rotating parts of these systems and help reduce vibration and noise levels.
Aerospace Industry: Aircraft manufacturers use motor rotor laminations for various components, such as engines and propellers. They need laminations that are lightweight yet strong enough to handle the high speeds and temperatures experienced by aircraft components.
Industrial Motors: Motor rotor laminations are suitable for industrial motors to provide support and stability and reduce vibration. They help ensure the motors operate smoothly and can handle higher loads and temperatures.
Appliances: Motor rotor laminations are suitable for various appliances, from washing machines to air conditioners. They help ensure that the motors used in these products perform reliably over time.
Electric Power Generation: Motor rotor laminations are vital in electric power generation. They provide the necessary structure and support for the rotors to ensure that they can withstand the high speeds and temperatures associated with generating electricity.
Marine Industry: Motor rotor laminations help reduce vibration, noise, and heat levels in marine applications like generators, pumps, and motors. The laminations also ensure that the motor rotors can withstand the forces of the water and environment they are exposed to.
Our Capabilities for Laser Cutting Lamination
We provide customers with high-quality electric motor stators and rotor lamination stacks. Our production process starts with selecting raw materials, ensuring that only the highest-grade materials are used in our products. We can provide laser cut and wire EDM for prototyping laminations.
We then precision-cut each lamination with laser technology, providing uncompromised accuracy and detail on every lamination. Our experienced engineers ensure that each rotor lamination meets your motor design’s exact specifications and requirements.
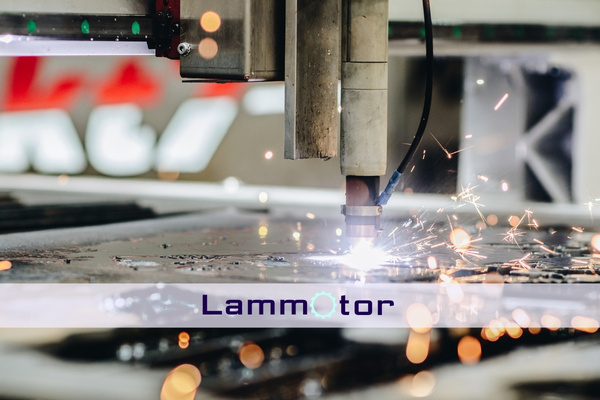
conclusion
Laser cutting is a great way to quickly and accurately cut rotor laminations for prototyping. The precision and speed of the laser make it ideal for producing complex shapes and small or intricate parts.
Additionally, the process is highly cost-effective and can quickly produce multiple copies of a single prototype. With laser cutting, businesses can reduce production costs while ensuring their prototypes are precise and meet all specifications.
If you’d like to learn more about how laser cutting can benefit your prototyping needs, don’t hesitate to contact us today for more information about motor lamination stacks.
FAQs
What is the best material for laser-cut motor rotor lamination stacks?
The best material is silicon steel for laser-cut motor rotor lamination stacks.
Silicon steel, also known as electrical steel, has high magnetic permeability, low core loss, and excellent electrical conductivity. These properties make it an ideal material for use in high-performance motors, generators, and transformers.
The precision cutting capabilities of laser technology make it possible to create intricate designs that optimize the performance of the motor, and silicon steel is the best choice for achieving both efficiency and durability in these applications.
In short, silicon steel is the clear choice for achieving optimal performance and reliability in laser-cut motor rotor lamination stacks.
What are rotor lamination stacks?
Rotor lamination stacks refer to the assembly of thin electrical steel laminations stacked together to form the rotor core in an electric motor.
These stacks are typically designed with a peculiar shape that allows them to work cohesively when rotating around the motor axis.
The lamination stacks are essential components of the rotor, as they assist in generating the magnetic flux necessary for the motor’s function.
Additionally, the thin sheets in the lamination stacks help reduce electrical losses due to eddy currents that are created in the rotor.
Rotor lamination stacks are an integral part of the design of electric motors, providing maximum efficiency and performance.