Motor lamination stacks play a crucial role in the performance and efficiency of electric motors. Selecting the right materials for motor lamination stacks is essential to ensure the optimal functioning and longevity of the motor. In this article, we will explore the factors to consider when choosing the material for the motor lamination stack.
The material used for motor lamination stacks significantly impacts the motor’s performance. It affects various parameters such as core losses, magnetic properties, and thermal characteristics. Therefore, selecting the right material is crucial to maximize efficiency and minimize energy losses.
Importance of Motor Lamination Stack
The motor lamination stack serves as the core of the motor, providing a path for magnetic flux and reducing energy losses. It is made up of thin laminations that are stacked together to form a solid core.
The lamination thickness plays a crucial role in determining the motor’s efficiency and performance. A thinner lamination provides a smoother flow of magnetic flux and reduces losses due to eddy currents. However, thinner laminations are also more expensive.
And the choice of material for these laminations is critical to achieving desired motor performance.
Common Materials for Motor Lamination Stack
The choice of material for the motor lamination stack is crucial in determining the performance and efficiency of electric motors. Different materials offer varying magnetic properties, core losses, and mechanical characteristics. There are three common materials for motor lamination stacks: silicon steel, nickel alloys, and cobalt alloys. We will discuss the pros and cons of each material to help you make an informed decision.
Silicon Steel
Silicon steel, also known as electrical steel or transformer steel, is one of the most widely used raw materials for motor lamination stacks. It is a type of alloy that contains iron with varying amounts of silicon. Here are the pros and cons of silicon steel:

Pros:
High Magnetic Permeability: Silicon steel exhibits excellent magnetic properties, including high magnetic permeability. This allows for efficient flux distribution and reduces energy losses due to hysteresis and eddy currents.
Low Core Losses: Silicon steel has low core losses, making it an ideal choice for applications where energy efficiency is a priority.
Cost-effective: Silicon steel is relatively affordable and readily available, making it a cost-effective option for motor lamination stacks.
Cons:
Limited Saturation Flux Density: Silicon steel has a relatively low saturation flux density, which can limit its application in high-performance motors that require high magnetic flux density.
Susceptible to Magnetic Aging: Over time, silicon steel can experience magnetic aging, leading to an increase in core losses and reduced motor efficiency.
Nickel Alloys
Nickel alloys are another group of materials in motor lamination stacks. These alloys typically contain nickel as the primary element, along with other alloying elements such as iron, cobalt, and chromium. Let’s examine the pros and cons of nickel alloys:
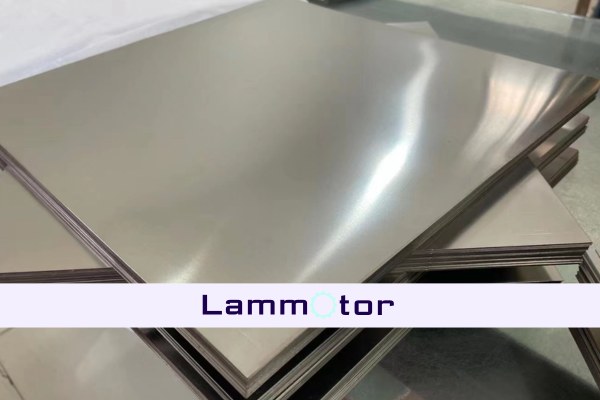
Pros:
High Saturation Flux Density: Nickel alloys exhibit higher saturation flux density compared to silicon steel. This makes them suitable for applications where high magnetic flux density is required.
Good Resistance to Corrosion: Nickel alloys offer excellent resistance to corrosion, making them suitable for motors operating in harsh environments or exposed to moisture.
High-Temperature Stability: Nickel alloys can withstand elevated temperatures without significant degradation in magnetic properties, making them suitable for high-temperature applications.
Cons:
Higher Core Losses: Nickel alloys generally have higher core losses compared to silicon steel. This can result in reduced motor efficiency, especially in applications where energy efficiency is critical.
Higher Cost: Nickel alloys tend to be more expensive compared to silicon steel, which may impact their suitability for cost-sensitive applications.
Cobalt Alloys
Cobalt alloys are a group of materials that contain cobalt as the primary element, along with other alloying elements such as iron, chromium, and nickel. Here are the pros and cons of cobalt alloys for motor lamination stacks:
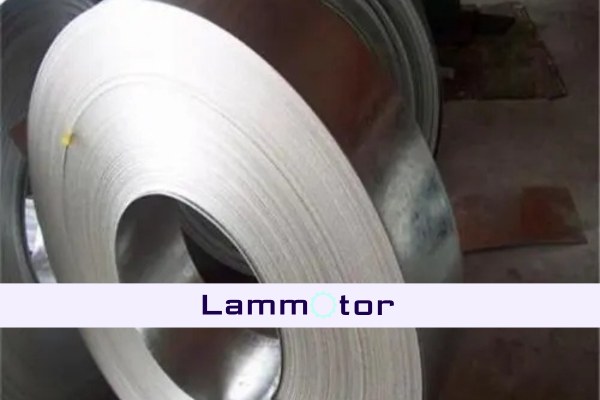
Pros:
High Saturation Flux Density: Cobalt alloys offer high saturation flux density, making them suitable for applications that require strong magnetic fields.
Excellent Temperature Stability: Cobalt alloys exhibit excellent thermal stability and retain their magnetic properties even at high temperatures.
Good Mechanical Strength: Cobalt alloys have good mechanical strength, allowing them to withstand mechanical stresses and vibrations experienced in motor operation.
Cons:
Higher Core Losses: Cobalt alloys generally have higher core losses compared to silicon steel, which can impact motor efficiency.
Higher Cost: Cobalt alloys tend to be more expensive compared to silicon steel and nickel alloys, making them less suitable for cost-sensitive applications.
Amorphous Metal Alloys
Amorphous metal alloys are relatively new materials in stator and rotor lamination stacks. They possess unique magnetic properties, including low core losses and high saturation magnetization. Amorphous metal alloy laminations can significantly improve motor efficiency.
Soft Magnetic Composites
Soft magnetic composites (SMCs) are composite materials made up of ferromagnetic particles and a non-magnetic binder. SMCs offer excellent magnetic properties, reduced eddy current losses, and improved mechanical strength compared to traditional laminations. They are gaining popularity in motor lamination applications.
Factors Affecting Material Selection
Several factors influence the material selection for stator and rotor lamination stacks. These include magnetic properties, electrical resistivity, thermal conductivity, mechanical strength, and cost.
Core Losses and Efficiency
One of the primary considerations when selecting a material for motor lamination stacks is core losses. Core losses consist of hysteresis losses and eddy current losses.
Hysteresis losses occur due to the reversal of magnetization in the laminations, while eddy current losses arise from circulating currents induced within the laminations. Both these losses contribute to energy dissipation and reduce motor efficiency.
Cost and Availability
The cost and availability of the chosen material should also be taken into account. Some materials may offer superior performance but could be expensive or difficult to source. It is important to strike a balance between performance requirements and budgetary constraints.
Other Considerations
Apart from the material’s magnetic and electrical properties, other factors should be considered during material selection. These include thermal conductivity to dissipate heat effectively, mechanical strength to withstand mechanical stresses, and availability and cost of the material.
Conclusion
Choosing the right material for motor lamination stacks is crucial for achieving optimal motor performance. Silicon steel, nickel alloy, cobalt alloys, amorphous metal alloys, and soft magnetic composites are some of the common materials in motor lamination stacks. Each material has its advantages and limitations, and the choice depends on specific motor requirements.
Are you in need of high-quality motor lamination stacks for your electric motor manufacturing? Look no further! We specialize in providing top-notch motor lamination stacks in China. With our expertise and dedication to excellence, we can meet your specific requirements and deliver outstanding products.
Contact us today to discuss your stator lamination stack needs. Our team of experts is ready to assist you in finding the perfect solution. Whether you need silicon steel laminations, nickel alloy laminations, cobalt alloy laminations, or any other custom requirements, we have you covered.
Why Choose Us For Your Motor Lamination Stack Needs?
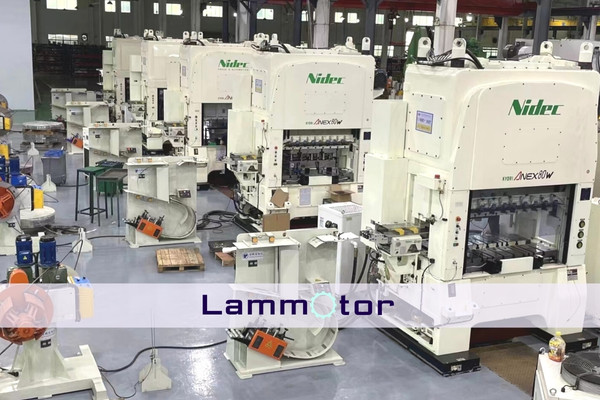
Superior Quality: We prioritize quality in every aspect of our manufacturing process. Our motor lamination stacks are made from premium materials and undergo rigorous testing to ensure they meet the highest standards.
Customization Options: We understand that every motor application is unique. That’s why we offer customization options to tailor the motor lamination stacks to your specific needs. We can accommodate different sizes, shapes, materials, and other specifications.
Competitive Pricing: We believe that high-quality motor lamination stacks should be accessible without breaking the bank. Our competitive pricing ensures that you get the best value for your investment.
Timely Delivery: We understand the importance of meeting deadlines in the manufacturing industry. With our efficient production processes and streamlined logistics, we strive to deliver your motor lamination stacks on time, every time.
Excellent Customer Support: Our team is dedicated to providing exceptional customer service. We are here to address any inquiries, offer technical assistance, and provide guidance throughout the process. Your satisfaction is our priority.
FAQs
1. Can I Use Any Material For Motor Lamination Stack?
No, the material selection for the motor lamination stack should be based on factors like core losses, magnetic properties, thermal characteristics, and cost.
2. What Are The Best Common Materials Used For Motor Lamination Stacks?
Silicon steel is best commonly used material for motor lamination stacks. There are many grades of silicon steel.
Silicon steel, also known as electrical steel or transformer steel, is a widely used material for motor lamination stacks. It exhibits excellent magnetic properties and low core losses, making it an ideal choice for many applications. Silicon steel laminations are typically coated to reduce eddy current losses further.