In the rapidly evolving world of electric vehicles (EVs) and high-efficiency motors, self-bonding technology in motor lamination stacks stands out as a game-changer. This innovative approach is revolutionizing how motor laminations are designed and manufactured, offering significant improvements in motor performance and efficiency.
At its core, bonding technology involves unique methods of layering and bonding thin metal sheets to form the core of electric motors.
This blog delves into the intricacies of self-bonding technology, exploring its key features, benefits, and the transformative impact it has on the motor industry.
What Is Self-Bonding Technology? And What’s the Bonding Process?
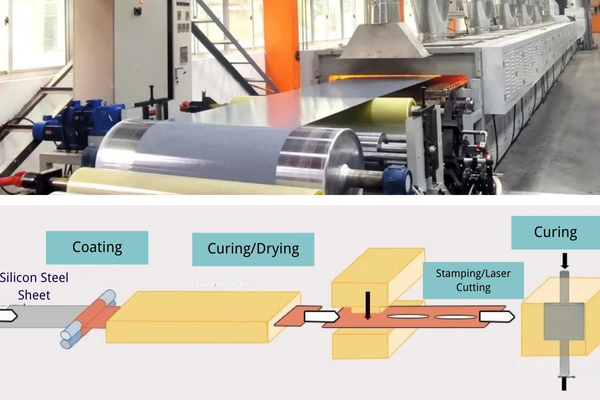
Self-bonding technology in electrical steel lamination stacks is a cutting-edge process used in the manufacturing of electric motors, particularly for electric vehicle motors. It involves the strategic bonding of thin metal sheets, typically made of silicon steel, without the need for conventional welding or interlocking techniques.
This bonding process is achieved through specialized adhesives or varnishes that are applied during the lamination process. The result is a highly integrated, compact motor core with improved electrical and mechanical properties. T
his technology not only enhances the motor’s efficiency and performance but also significantly reduces noise, vibration, and heat generation, making it a cornerstone in modern EV motor design.
10 Key Features of Self-Bonding Motor Lamination Stacks
Self-bonding motor lamination stacks are revolutionizing the electric vehicle (EV) industry with their unique properties. Each feature contributes significantly to the overall performance and efficiency of EV motors. Let’s explore these key features in detail:
High Intensity
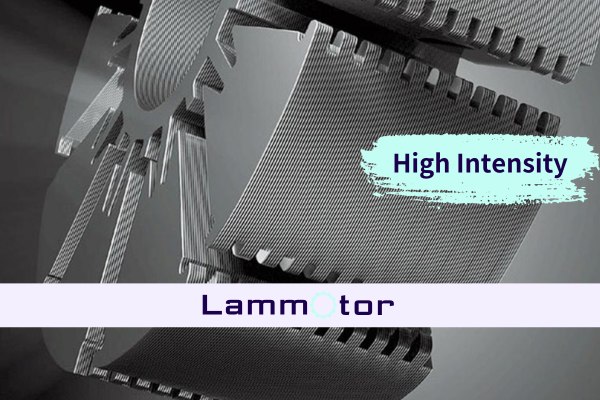
Adhesive bonding lamination stacks boast a remarkable tensile shear strength of 14-18N/mm², making them robust enough for secondary processing like turning, grinding, and drilling. This high intensity ensures durability and longevity, essential for the demanding environments in which EV motors operate.
High Precision
The uniformity of surface contact in self-bonding lamination stacks is significantly enhanced, improving flatness and verticality by more than 50%. This precision, measured with a feeler gauge thickness of just 0.05mm, ensures optimal performance and alignment within the motor, leading to smoother operation and reduced wear and tear.
Reduce Vibration
Vibration levels in motors are reduced by 5% with these lamination stacks. This reduction not only contributes to a more stable and efficient motor operation but also enhances the overall driving experience by minimizing the vibrations felt inside the vehicle, leading to a smoother and more comfortable ride.
High Power Density
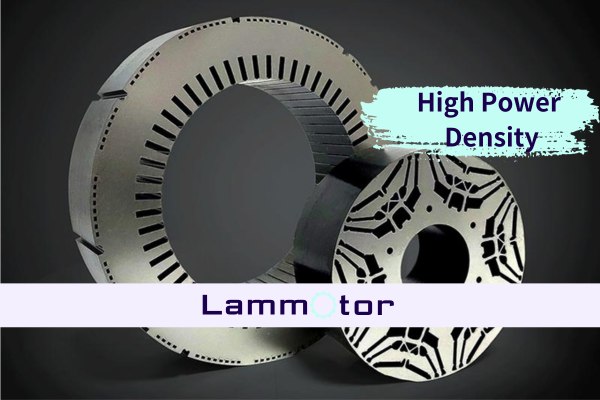
These stator and rotor lamination stacks offer a higher power density, characterized by a smaller size and lighter weight while maintaining a high stacking coefficient of over 98.5%. This feature is crucial for compact yet powerful motor designs, allowing for more efficient use of space and materials in EVs.
Reduce Noise
A notable reduction in noise by 5dB is achieved through self-bonding lamination stacks. This decrease in acoustic emissions is particularly beneficial in urban environments, where noise pollution is a growing concern. Quieter motors contribute to a more pleasant and less intrusive presence of EVs on the roads.
Lower the Temperature
Enhanced heat conduction in these stacks leads to optimal axial heat transfer, effectively lowering the motor’s temperature by 5-10℃. This improved thermal management is vital for maintaining motor efficiency and preventing overheating, thereby extending the lifespan of the motor and ensuring consistent performance under various operating conditions.
Flexible Design
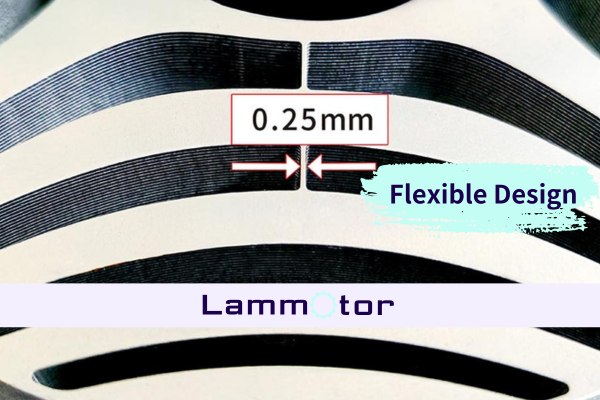
The improved strength of self-bonding lamination stacks allows for more flexible and innovative design choices, including smaller magnetic bridge designs ranging from 0.25-0.50mm. This flexibility opens up new possibilities for motor design, enabling engineers to create more efficient and compact motors tailored to specific applications and requirements.
Improve Efficiency
Motors equipped with these lamination stacks experience a 5% increase in torque and a similar improvement in efficiency. This enhancement is crucial for EVs, where every increment in efficiency translates to better performance, longer range, and reduced energy consumption, making the vehicles more appealing and practical for consumers.
High Efficiency and Energy Saving
The absence of magnetic flux blocking and a reduction in iron loss by 15-30% lead to significant energy savings. This efficiency not only prolongs battery life but also reduces energy consumption overall. Additionally, the reduced need for insulating varnish contributes to both cost savings and environmental benefits.
High Cleanliness
High cleanliness levels in self-bonding lamination stacks improve motor performance and extend its service life. This cleanliness is crucial in maintaining the integrity of the motor components, ensuring that they function optimally over time. A cleaner motor is a more reliable one, offering Consistent Performance And Reducing The Need For Frequent Maintenance Or Replacements.
Bonding Varnish And Glue-Dot Bonding
Recent advancements in self-bonding techniques have significantly enhanced the efficiency and reliability of motor lamination stacks. One notable development is the refinement of bonding varnishes. These specialized coatings have been formulated to provide stronger and more uniform adhesion, leading to improved structural integrity and electrical performance of the motor cores.
Additionally, the emergence of glue-dot bonding represents a breakthrough. This method involves the precise application of adhesive dots, ensuring consistent bonding strength and thickness across the lamination stack. These innovations in bonding varnishes and glue-dot techniques are pivotal, offering more robust, efficient, and adaptable solutions in motor manufacturing for various applications.
Conclusion
As we look towards the future, self-bonding technology in motor lamination stacks stands as a beacon of innovation in the electric vehicle (EV) industry. Its ability to enhance motor efficiency, reduce noise and vibration, and improve thermal management marks a significant leap forward in motor design. The compactness and precision it offers are pivotal in meeting the evolving demands for more efficient and sustainable EVs.
As this technology continues to advance, we can expect even greater improvements in motor performance and a broader adoption in various applications. Self-bonding technology is not just a current trend; it’s a key component in shaping the future of electric mobility.
FAQs
What are the primary benefits of self-bonding technology in motor lamination stacks?
Self-bonding technology in motor lamination stacks offers enhanced efficiency, reduced noise and vibration, and improved thermal management. This technology enables more compact motor designs, crucial for space-sensitive applications. It also ensures higher precision and uniformity in the motor core, leading to better performance and longevity of electric motors.
How does self-bonding technology improve the efficiency of electric motors?
Self-bonding technology improves electric motor efficiency by minimizing air gaps and magnetic flux leakage in the lamination stacks. This results in reduced electrical losses and better magnetic properties, leading to lower energy consumption. Additionally, the improved thermal management capabilities of self-bonding help maintain optimal operating temperatures, further enhancing efficiency.
What materials are commonly used in self-bonding motor laminations?
The most commonly used materials in self-bonding motor laminations are silicon steel and nickel-iron alloys. These materials are chosen for their excellent magnetic properties, which are crucial for efficient motor operation. Silicon steel, also electrical steel, in particular, is favored for its low core loss and high permeability, making it ideal for high-efficiency electric motors.
What are the main challenges in manufacturing self-bonding laminations?
Manufacturing self-bonding laminations presents challenges such as ensuring uniform adhesive application, achieving consistent bonding strength, and maintaining precision in lamination alignment. The process also requires specialized equipment and expertise. Additionally, balancing the thermal expansion properties of different materials to prevent delamination under operational stress is a key challenge.
What is the Future Outlook for Self-Bonding Technology in the EV Industry?
The future outlook for self-bonding technology in the EV industry is highly promising. As the demand for more efficient and compact EV motors grows, self-bonding technology is expected to play a crucial role in meeting these needs. Ongoing research and development are likely to further enhance its capabilities and applications, solidifying its position as a key technology in the advancement of electric mobility.