Have you ever wondered what drives the heart of drones, robot vacuums, or electric vehicles? These high-tech machines all rely on BLDC motors, and inside these motors, there’s a fascinating difference in stator winding methods—some follow the “concentrated” camp. In contrast, others belong to the “distributed” side. Don’t underestimate these winding styles—they affect everything from motor efficiency and noise to cost and performance. Behind them are countless engineers’ clever design decisions.
In this article, we’ll take you inside the stator and reveal the secrets of concentrated winding and distributed winding. By the end, you’ll know which one is best for your application—and it might even impact the success of your next project.
If you would like to know more types of winding, please click this link.
What Is Concentrated Winding?
As the name suggests, concentrated winding means that the coil windings are concentrated in a few stator slots. This makes the structure simpler and lowers manufacturing costs. These windings usually have fewer turns, which helps generate a stronger magnetomotive force.
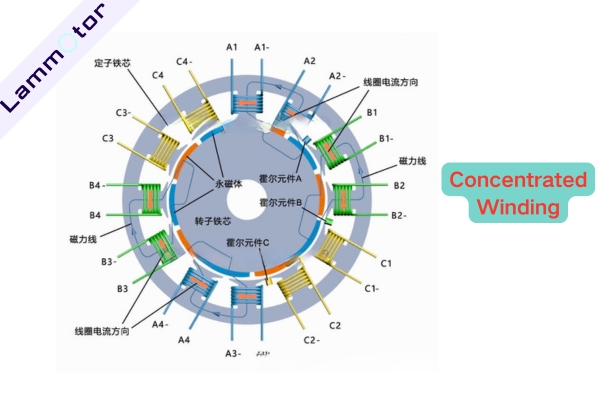
You’ll often find BLDC motor stator winding with concentrated windings in applications that require small size and low cost but don’t demand high motor performance, like toy motors.
Since the coils are tightly packed, space is used efficiently, allowing the motor to be more compact. However, this also brings disadvantages. The uneven winding distribution creates higher harmonic content in the magnetic field, which may lead to more noise and vibration during operation.
In a typical concentrated winding, each stator tooth carries one coil. Different colors are used to represent the U, V, and W phases. Two coils form one phase, and the three phases can be connected in either a star (Y) or delta (Δ) configuration.
What Is a Star Connection (Y)?
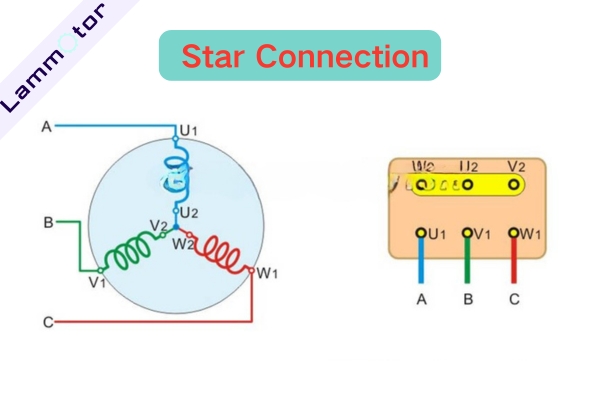
In a star connection, the start ends of the three phases (W1, U1, V1) are connected together, and the other ends (U2, V2, W2) are connected to the power lines. In a motor junction box, the top row is connected together, and the bottom three wires are connected to the power supply, as shown in the diagram below.
What Is a Delta Connection?
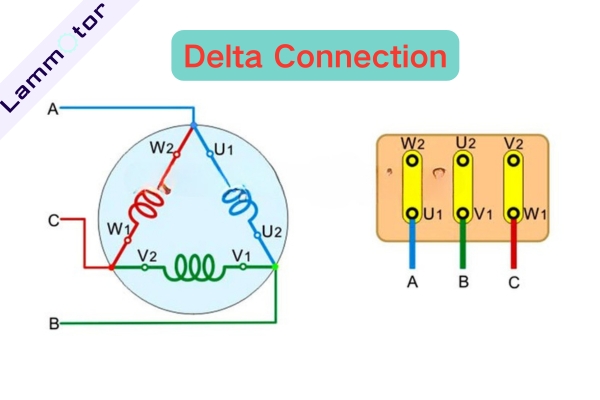
In a delta connection, W2 is connected to U1, U2 to V1, and V2 to W1. These connections are then linked to the power lines. The wiring method inside the motor junction box is shown below.
What Is Distributed Winding?
Distributed winding is different. Here, the windings are spread across multiple slots, evenly covering the stator core. This type of BLDC motor stator winding generates a smoother, more sinusoidal magnetic field, reducing harmonic content significantly.
As a result, the motor runs more quietly and with less vibration. That’s why this method is widely used in high-performance motors, such as industrial drive motors and electric vehicle propulsion systems.
Because the winding is spread over more slots, the structure becomes more complex, the manufacturing process is more difficult, and the cost is higher.
In a distributed winding, at least two stator teeth are wound, as shown in the diagram. The number of teeth covered is called the coil span, and it depends on the number of stator slots and the number of pole pairs in the rotor.
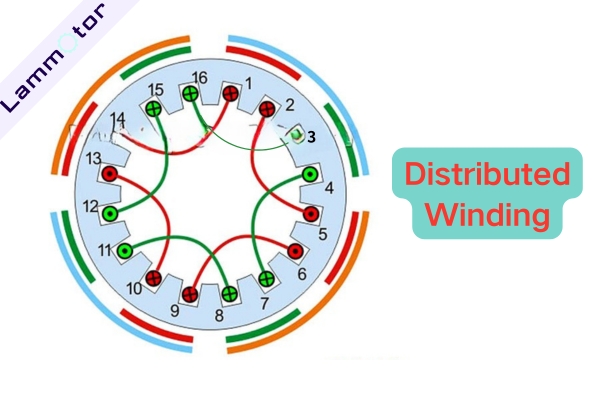
Types of Distributed Winding: Concentric and Lap Winding
Concentric Winding
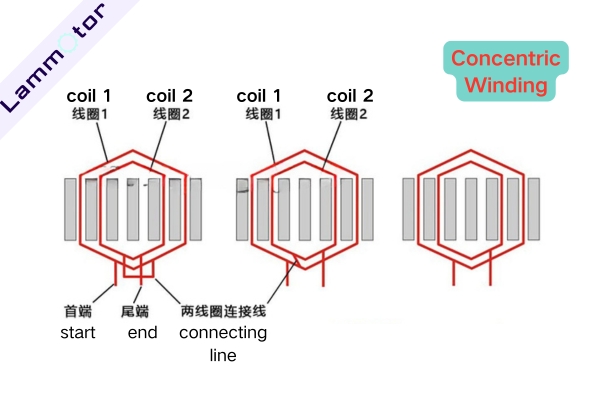
Concentric winding uses multiple coils of similar shape but different sizes, arranged concentrically around a common center. These windings may be arranged in two or three planes, depending on the wiring method. Many single-phase motors and small three-phase motors with large coil spans use this configuration.
Lap Winding
Lap winding consists of coils with the same shape and size. Each slot is filled with one or two coil sides, stacked at the coil end.
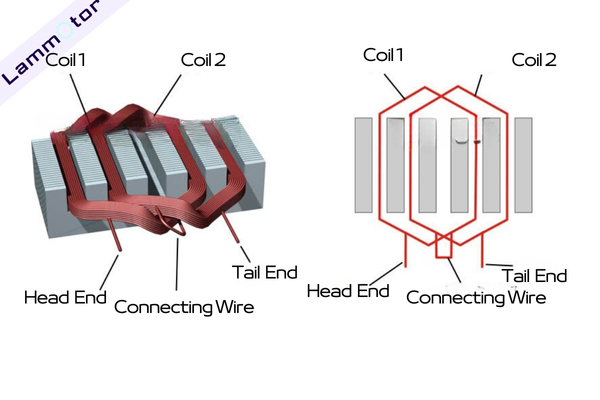
Lap winding can be divided into single-layer and double-layer types. If each slot contains only one coil side, it’s called single-layer lap winding. If each slot contains two coil sides from different groups—one in the upper layer and one in the lower—it’s called double-layer lap winding.
Based on further layout variations, lap winding can also be cross-type, concentric-cross, or a hybrid of single and double layers.
Today, most large three-phase induction motors use double-layer lap windings. Small motors typically use variations of single-layer lap winding, but rarely the pure single-layer type.
Comparison: Concentrated vs Distributed BLDC Motor Stator Winding
When designing a BLDC motor, the choice of stator winding structure directly affects motor efficiency, performance, production process, and cost.
Both concentrated and distributed winding methods are popular, each with its own advantages and drawbacks.
Here’s a detailed comparison to help you make an informed decision.
Comparison Item | Concentrated Winding | Distributed Winding |
Structure | Windings placed in specific slots | Windings spread across multiple slots |
Winding Process | Simple process, suited for automation | Complex, harder to insert |
Copper Loss | Shorter wire length, lower copper loss | Longer wire, slightly higher copper loss |
Magnetic Field | More concentrated, higher fluctuation | More uniform, smoother motor operation |
Torque Ripple | Higher ripple (obvious cogging torque) | Stable torque, ideal for precision control |
Electromagnetic Noise | Higher noise, needs extra damping | Quieter operation |
Power Density | Higher, great for compact high-power motors | Slightly lower, but better thermal management |
Heat Dissipation | Heat concentrated, needs better cooling design | Heat spread evenly, slower temperature rise |
Application Scenarios | Drones, power tools, small short-shaft motors | EV drive motors, servo motors, fan motors |
Production Cost | Lower, ideal for mass production | Higher, suited for high-performance motors |
BLDC motor stator winding design plays a crucial role in how well a motor performs. Concentrated winding, with its high power density and ease of automation, is increasingly favored in drones, portable devices, and small high-speed motors. On the other hand, distributed winding remains the top choice for EV drive motors and industrial control motors due to its stable torque and low noise.
When choosing between concentrated and distributed winding, the key lies in balancing performance, cost, and manufacturing complexity. Whether you’re designing for consumer electronics or industrial applications, understanding these winding structures helps you make smarter engineering decisions.
Contact Us for Custom BLDC Motor Stator Winding Solutions
Lammotor is a leading BLDC motor stator winding manufacturer based in China. We offer customized winding solutions for a wide range of electric motors, including BLDC motors, permanent magnet synchronous motors (PMSM), axial flux motors, and coreless motors.
Whether you need help with prototyping or mass production, our team is here to support your project from concept to completion.
📩 Ready to get started? Contact us today to discuss your motor winding needs or motor stator and rotor core needs and get a custom quote.