Have you ever wondered what makes a coreless motor perform at its best? As a seasoned coreless motor manufacturer in China with years of experience, we know that winding types play a crucial role in motor efficiency. Among the nearly 30 steps in producing a coreless motor, the most critical is the winding process.
Today, we’re diving into the three most common types of coreless motor windings: straight winding, skewed winding, and saddle winding. Each type has its own unique advantages and applications. We’re here to help you understand which might be the best fit for your needs.
Straight Winding in Coreless Motors
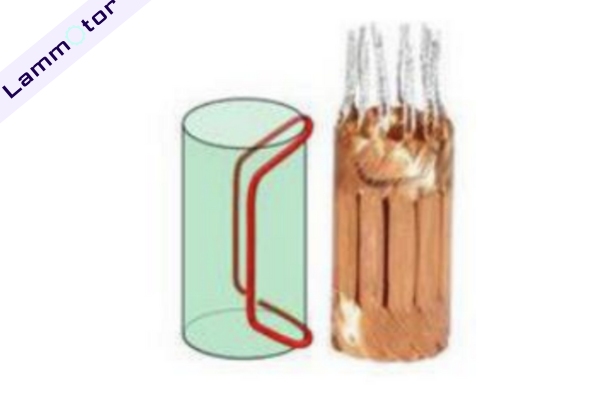
Straight winding in coreless motors is characterized by coils that run parallel to the motor’s axis, forming a concentrated winding structure.
The design begins with winding the enameled wire around a winding mold according to the required turns.
Then, the wires are connected to a spindle to form the winding. which is finally cured with adhesive at both ends.
While this method achieves a high slot fill factor and a thin middle wall in the winding cup. The irregular wire arrangement can lead to uneven electromagnetic force distribution.
This can result in less-than-optimal efficiency or torque fluctuations during operation, making straight winding less common in automated winding processes.
Skewed Winding
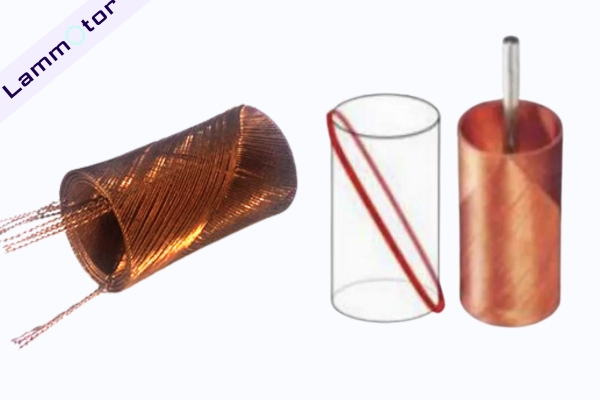
Skewed winding, also known as honeycomb winding, involves tilting the effective edges of the winding at an angle relative to the armature axis to enable continuous winding.
A specialized spindle with two rows of pins is used during this process. As the spindle rotates along with the winding machine, the enameled wire wraps around the spindle, reducing torque ripple and improving operational smoothness.
This winding method is favored by top global coreless motor manufacturers, such as Germany’s Faulhaber.
Saddle Winding / Concentric Winding
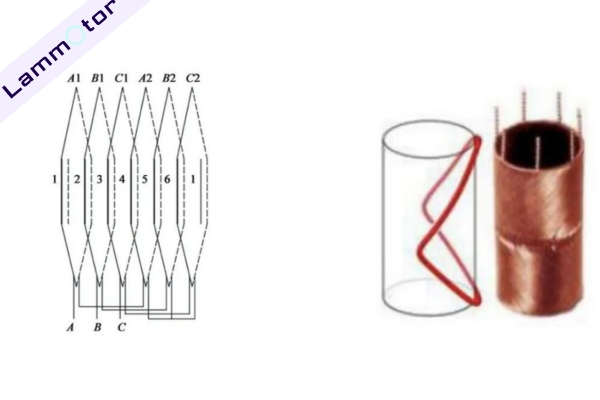
Saddle winding, also known as concentric or diamond winding, involves creating multiple individual diamond-shaped coils first, which are then arranged according to the design specifications. Each coil is shaped and positioned using specialized tools to form a cup-shaped structure.
This method allows for precise control of the coreless motor’s dimensions and improves the slot fill factor, making it ideal for high-efficiency production.
Additionally, saddle winding is well-suited for mass production due to its efficiency. Swiss motor manufacturer Maxon employs this winding technique, known for producing motors with exceptional performance.
Winding Process for Coreless Motor
Coil winding methods can be divided into semi-winding and one-step automated winding.
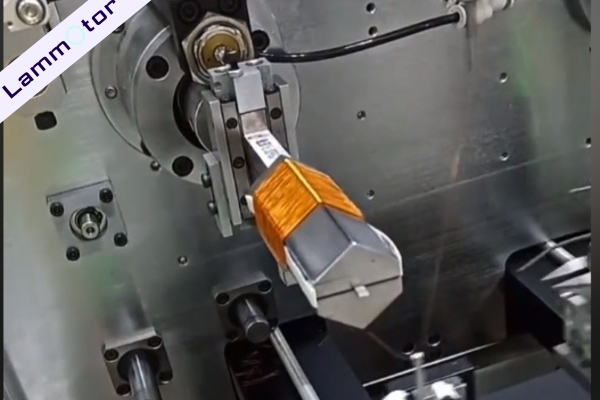
Internationally, the one-step automated winding process is widely used, where coils are formed directly around the axis, leading to a more efficient and streamlined production process. However, in China, where labor is abundant and relatively inexpensive, manual winding still plays a significant role. This reliance on manual labor results in lower production efficiency and limitations in wire diameter.
The semi-winding process involves two main steps: first, winding the coil blank on a winding machine, then flattening it, wrapping it into a cylindrical shape, and soldering the connections. This method is more suited for larger coreless motors, typically around 20-30mm in diameter, and struggles with coils smaller than 7mm. So, this makes it less effective for motors with diameters under 10-12mm.
In contrast, the one-step automated winding technique allows for coils to be wound directly on the axis. It simplifies the process and enhances production efficiency.
Conclusion
Understanding the different winding types—straight, skewed, and saddle—is crucial when choosing the right coreless motor for your application.
Each winding type offers unique advantages that can enhance motor performance, depending on the specific needs of your project.
By selecting the appropriate winding, you can optimize efficiency, reduce torque ripple, and achieve smoother operation.
Ready to find the perfect coreless motor for your needs? Contact us today to discuss your custom coreless motor requirements. Our team of exp