Electric motor laminations serve as crucial components in the heart of various electrical devices. The choice of material can have a significant impact on performance and efficiency. Two popular options on the market are amorphous metal laminations and silicon steel laminations. But which one is the better choice?
In this blog post, we will compare amorphous metal and silicon steel for electric motor laminations, examining their properties, benefits, and drawbacks.
Whether you’re an engineer or a manufacturer in the electrical industry, this comparison will help you make an informed decision about which material is best suited for your needs.
So, let’s dive in and explore the differences between amorphous metal and silicon steel for electric motor laminations.
What Is Amorphous Metal?
Amorphous metal, also known as metallic glass, defies conventional crystalline structures, setting it apart in the materials landscape. Crafted through a rapid cooling process, it eschews the regular atomic arrangement found in traditional metals. This uniqueness grants it exceptional properties vital for diverse applications.
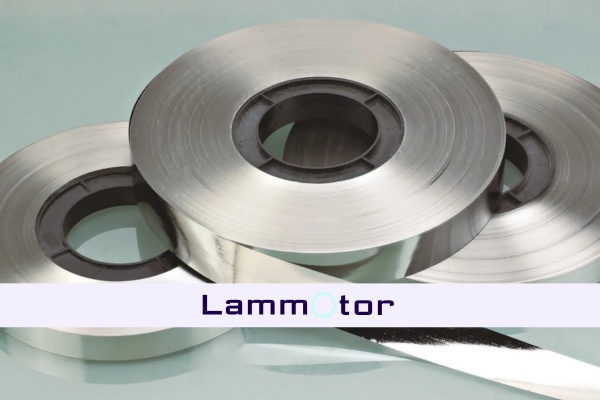
The Process
The production process involves rapid cooling of molten metal, preventing the formation of a crystalline structure. This results in a disordered atomic arrangement, contributing to its amorphous nature. Unlike conventional metals, amorphous metal possesses a distinct lack of grain boundaries, enhancing its mechanical strength.
Amorphous Metal For Electric Motor
In electric motor applications, amorphous core materials emerge as a game-changer. Its exceptional magnetic properties foster heightened efficiency, reducing energy consumption and contributing to superior performance. Additionally, its high electrical conductivity facilitates optimal functioning within electric motor systems.
Key properties of amorphous material include its impressive magnetic permeability, low coercivity, and high saturation magnetization. These attributes collectively contribute to reduced energy losses and enhanced overall performance in electric motor laminations. The unique combination of characteristics makes amorphous metal a compelling choice for modern electric motor designs.
Silicon Steel: The Traditional Choice
Silicon steel, also referred to as electrical steel or lamination steel, is a specialized alloy predominantly composed of iron with varying silicon content.

This alloy is meticulously crafted to exhibit distinctive magnetic properties, making it indispensable in the production of electrical devices like transformers and electric motors.
The silicon content enhances the material’s magnetic permeability, reducing core losses and optimizing energy efficiency.
Silicon steel is renowned for its role in creating thin laminations through precision cold-rolling, ensuring optimal performance in electrical applications.
The manufacturing process of Silicon Steel Laminations
The manufacturing process of silicon steel laminations involves a meticulous series of steps.
Beginning with the alloy composition of iron and silicon, the material undergoes precision cold-rolling to achieve the desired thinness. This method ensures the creation of laminations that optimize magnetic flux, minimizing energy losses.
Precision in each step is paramount, as the cold-rolling process enhances the material’s magnetic permeability. The result is a finely tuned product, ready to play a crucial role in the efficiency of electric motors and transformers.
Benefits and drawbacks of Silicon Steel Laminations
Silicon steel laminations offer noteworthy benefits but come with inherent drawbacks. On the positive side, their excellent magnetic permeability and low core loss enhance the overall efficiency of electric motors. However, drawbacks include susceptibility to corrosion and a degree of brittleness that may affect durability.
Comparing Key Properties: Amorphous Metal vs Silicon Steel Laminations
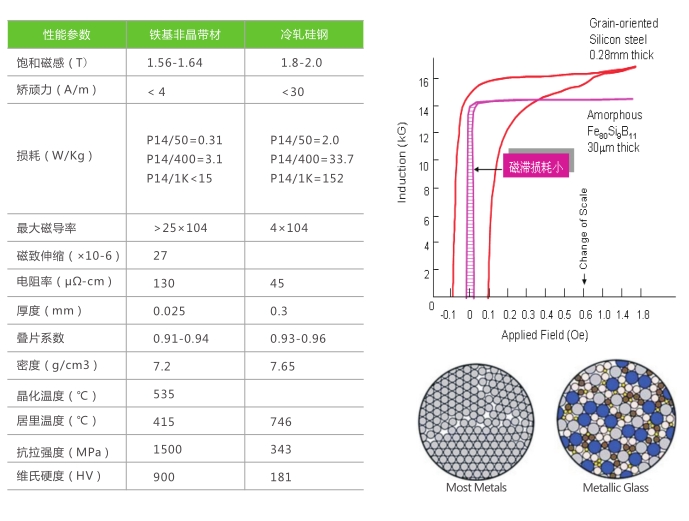
A. Magnetic Properties:
Amorphous metal motor lamination boasts superior magnetic properties due to its lack of grain boundaries, resulting in reduced energy losses. In contrast, silicon steel, while efficient, may experience higher losses due to its crystalline structure. The amorphous structure in metallic glass allows for enhanced magnetic permeability, contributing to improved overall performance in electric motors.
B. Electrical Conductivity:
Amorphous metal exhibits high electrical conductivity, facilitating optimal functioning within electric motor systems. Silicon steel, though conductive, may not match the efficiency levels of amorphous metal. The streamlined atomic arrangement in metallic glass enhances the flow of electrons, reducing electrical losses in the system.
C. Mechanical Strength and Durability:
Silicon steel is known for its mechanical strength, but it comes with a degree of brittleness. Amorphous metal, on the other hand, combines mechanical strength with flexibility, reducing the risk of fractures. This advantage makes amorphous metal a preferred choice in applications where mechanical stress and durability are critical factors.
D. Heat Resistance:
Amorphous metal exhibits impressive heat resistance, outperforming silicon steel in this aspect. Its unique atomic structure allows it to withstand higher temperatures, making it suitable for applications where heat dissipation is a concern. This characteristic contributes to the longevity of electric motor systems.
E. Cost Considerations:
While amorphous metal laminations offer several advantages, they tend to be more expensive to produce than silicon steel. The cost considerations become crucial factors in decision-making, especially for industries with budget constraints.
Silicon steel, with its proven track record and lower production costs, remains an economically viable option for many applications.
F. Reduce Iron Loss:
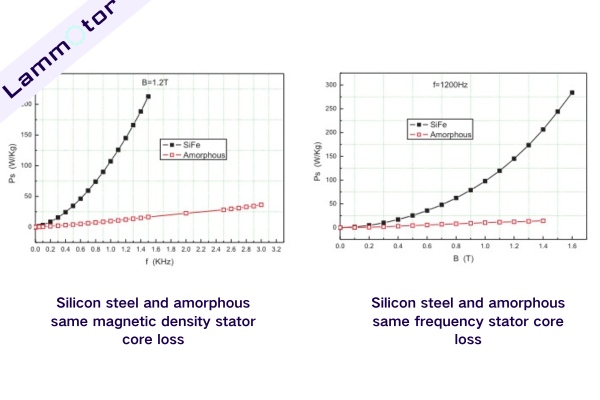
Both amorphous metal and silicon steel aim to reduce iron loss in electric motor laminations. Amorphous metal motor laminations achieve this by minimizing eddy current losses and hysteresis losses due to their unique atomic arrangement.
Silicon steel laminations, though effective, may experience slightly higher losses. The quest to reduce iron loss is a common goal, but the methods employed by each material vary, influencing their overall efficiency in electric motor applications.
In conclusion, the choice between amorphous metal and silicon steel for electric motor laminations depends on the specific requirements of the application. While amorphous metal shines in terms of magnetic properties, electrical conductivity, and heat resistance, silicon steel offers a cost-effective solution with a reliable track record. Understanding the nuanced differences in key properties is essential for making informed decisions in electric motor design.
Comparing Motor Applications: Amorphous Metal Motor Core vs Electric Steel Motor Core
Applications of Amorphous Metal Motor Core:
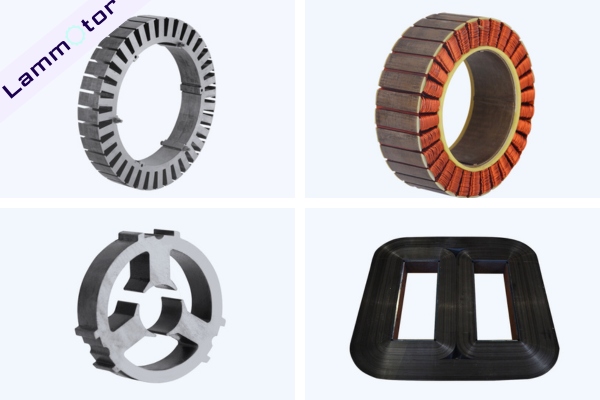
Amorphous metal motor cores find diverse applications in cutting-edge technologies. Their superior magnetic properties make them ideal for energy-efficient appliances, electric vehicles, and power tools.
The flexibility and mechanical strength of amorphous metal suit high-frequency applications, making it a preferred choice for variable-speed drives and advanced robotics and transformer cores.
In challenging conditions, such as those encountered in industrial settings, amorphous metal motor cores demonstrate their resilience, contributing to enhanced performance and efficiency in various application domains.
Applications of Silicon Steel Motor Core:
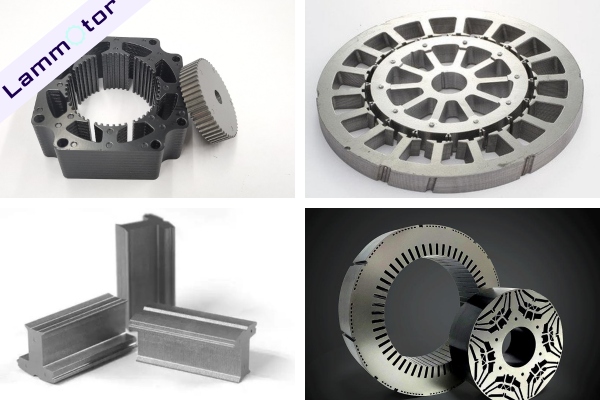
Silicon steel motor cores, being a longstanding and reliable choice, are widely utilized in traditional electric motors. Their magnetic permeability and low core loss make them ideal for applications where cost-effectiveness and proven performance are priorities.
Silicon steel cores are commonly found in new energy vehicles, industry, drone, household appliances, and power distribution systems. The material’s ability to maintain stability under varying conditions makes it a staple in motors used across a broad spectrum of applications.
While perhaps not as cutting-edge as amorphous metal in certain areas, silicon steel sheets continue to be the workhorse in many essential and everyday devices.
FAQs
What are the cost differences between amorphous alloy and silicon steel for electric motor laminations?
Amorphous metal tends to be more expensive due to its intricate production process. Silicon steel, with lower production costs, remains a cost-effective choice for industries with budget constraints, making it a preferred option for electric motor laminations in certain applications.
Can amorphous metal be used as a direct replacement for silicon steel in existing motors?
While technically feasible, transitioning from silicon steel to amorphous alloy in existing motors may require adjustments. Factors such as core design and manufacturing specifications must be considered for a seamless replacement, ensuring optimal performance and efficiency.
How does the manufacturing process of amorphous material compare to that of silicon steel?
The manufacturing processes for amorphous material and silicon steel differ significantly. Amorphous metal involves rapid cooling to create a non-crystalline structure, while silicon steel undergoes precision cold-rolling to achieve thin laminations. These distinctions impact cost, efficiency, and application suitability.
What are the primary factors influencing the choice between amorphous metal and electrical steel in electric motor design?
Several factors influence the choice between amorphous metal and silicon steel in electric motor design. These include performance requirements, budget considerations, application-specific needs, and the overall goals of the motor system. Balancing these factors is crucial for achieving optimal efficiency and cost-effectiveness in motor design.