Are you a hobbyist looking to explore the world of micro motors? If so, you’ve come to the right place. In this article, we’ll walk you through everything you need to know about these mini motors and how they can be used in various projects.
We’ll discuss their advantages compared to larger motors, their work, and the types available. Whether building a model airplane or creating a custom drone, understanding micromotors is essential for any hobbyist. So read on to learn more about these miniature powerhouses!
What are micro motors?
Micro motors are small electric motors designed to fit into tight spaces while providing high power. They operate on the same underlying principles as larger electric motors but have been adapted to smaller devices such as medical equipment, robotics, and electronics.
What is the Advantage of micro motors?
One of the major advantages of micromotors is their size. These devices can be as small as a few millimeters in diameter. Therefore, they are ideal for use in miniature machines or other compact devices where space is at a premium. Despite their small size, micro motors can deliver impressive torque and rotational speed levels.
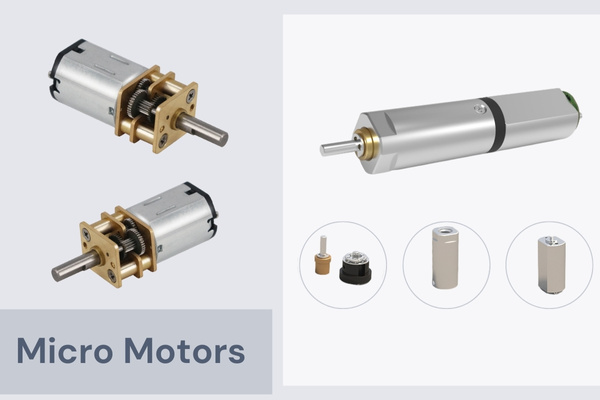
Common Materials Available for Micro Motor Stator and Rotor Lamination
Some of our most commonly used materials for micromotor stator and rotor lamination include:
Cobalt alloys
Nickel alloys
Silicon steels
Thin-gauge electrical steel
Different Types of Micro Electric Motor
Micro-electric motors are small devices that convert electrical energy into mechanical energy. These motors play a crucial role in various industries, especially healthcare.
They can power medical devices such as insulin pumps, pacemakers, and surgical tools. Different micro electric motors are available in the market, each with unique features and applications.
DC micro motor
DC motor core is the most common type of micro motors used today. It converts direct current into mechanical energy by interacting with a magnetic field and an electric current.
The second type is the stepper motor which moves in precise increments or steps instead of continuous motion. This makes it ideal for applications that require high precision, such as robotics and automation systems.

Brushless DC Micro Motor (BLDC)
The brushless DC motor represents a significant advancement in micro electric motor technology. Its superior efficiency and increased reliability make it an attractive option for engineers designing high-performance systems with strict power requirements.
Unlike traditional brushed DC motors, BLDC motors use a permanent magnet rotor and electronic commutation to control the speed and direction of rotation.
The lack of brushes also means less friction, reducing wear and tear on the motor. This makes BLDC motors ideal for applications where reliability is crucial, such as medical devices or aerospace equipment. Additionally, they are more cost-effective since they require less maintenance than their brushed counterparts.
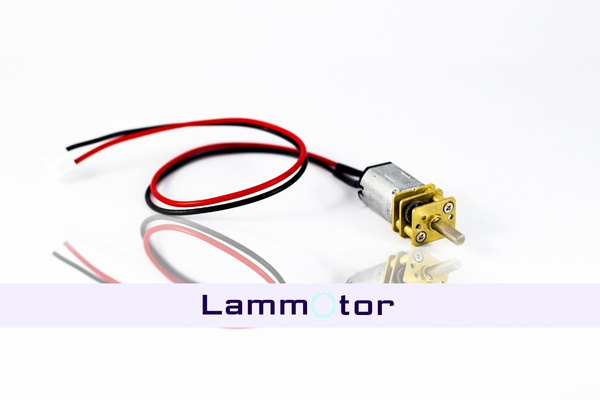
Industrial Applications of Micro-motors
Micro motors are small and compact DC (direct current) motors with various industrial applications. These tiny powerhouses can drive small mechanical systems like pumps, valves, and robotic actuators. They are also ideal for applications requiring precise rotational speed or torque control.
Medical Industry
One area where micromotors have become increasingly popular is the medical industry. These small but powerful devices can power miniature surgical tools, such as endoscopes and laparoscopic equipment.
Their small size allows them to fit easily into tight spaces within the body, reducing the risk of tissue damage during surgery. Additionally, their precise control over speed and torque makes them ideal for delicate procedures that require precision movement.
Automotive Industry
Another industrial application for micromotors is in the automotive industry.
One of the most common applications is in electric power steering systems. Micro motors are used to control the amount of assistance that a driver receives when turning the wheel. This ensures that the car responds smoothly and efficiently to every turn.
Another use of micromotors in automobiles is in door locks and windows. In modern cars, these features are controlled by electrical systems rather than manual mechanisms.
Micromotors are crucial in ensuring that these systems work properly and reliably. They provide precise control over the movement of doors and windows, allowing drivers to adjust them easily while maintaining road safety.
In addition to these applications, micromotors can be found in other parts of an automobile’s electrical system, such as air conditioning units, fuel injectors, and engine management systems.
Household appliances:
Micro-motors are used in shavers, hair dryers, coffee makers, water purifiers, and vacuum cleaners.
Industrial machinery:
Micro-motors drive machineries such as pumps, fans, and compressors.
Robotics:
Robots use micro-motors for tasks such as grasping objects and moving parts.
Toys:
Micro-motors are used to control the movements of toy cars and robots.
Aerospace:
Micro-motors are used in aircraft for tasks such as actuating valves, controlling airflow, and powering landing gear systems.
Agriculture:
Micro-motors are used to power agricultural machineries such as irrigation pumps and harvesters.
Our Company Capabilities For Manufacturing Micro Motor Stator And Rotor Lamination Stacks
We specialize in manufacturing motor stators and rotor lamination for various applications. We offer an extensive range of micro motor lamination, including custom stator lamination designs to meet any customer requirements.
In addition to our standard sizes and shapes, we can produce stators and rotors with high-precision dimensions down to the micron level. Our experienced teams can accurately mimic several complex shapes and sizes to meet needs.
Moreover, we use advanced technologies and processes to manufacture high-quality stator and rotor lamination. This includes specialized EDM (electrical discharge machining) technology that ensures accurate cutting and forming of various materials, including electrical and silicon steel.
Furthermore, our stator and rotor lamination products are designed to meet the highest quality standards. We employ stringent testing and validation processes from the prototype throughout production to guarantee that only the best products reach our customers.
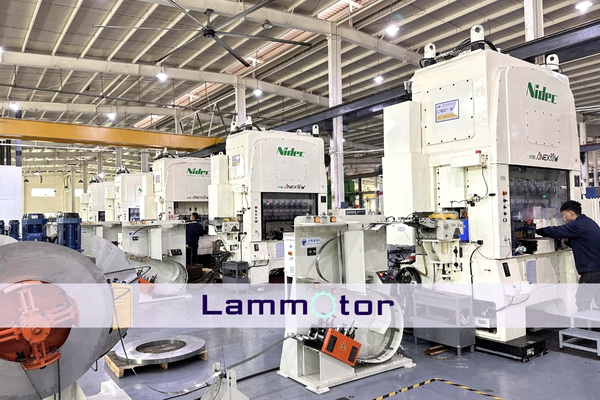
Conclusion
Micro motors are small, powerful motors that are used in a wide variety of applications. Micromotors are essential to various technologies, from smartphones to robots to medical devices.
Understanding the different types, their uses, and their benefits can help you better choose the right motor for your project. You can create reliable and efficient solutions for any task with the right micromotor.
So if you’re looking for a motor that can power your next invention or project, look no further than micro motors! Contact us for motor lamination stacks!
FAQs
What are Micro Electric Motor Lamination Stacks?
Micro-electric motor lamination stacks are essential components in constructing electric motors.
These stacks consist of thin layers of metal, typically made from materials such as silicon steel or nickel cobalt iron, which are tightly bound together to create a sturdy and efficient core for the motor.
The laminations themselves can be cut into various shapes and sizes, depending on the specific requirements of the motor.
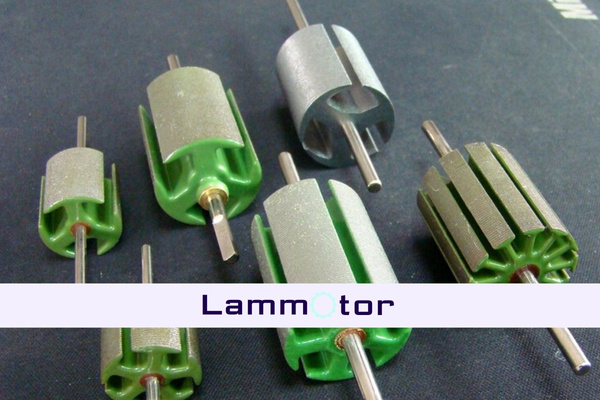
What Are The Differences Between Micro Servo Motor And Servo Motor?
Servo motors are electric motors that can accurately control a rotating shaft’s angular position, speed, and torque.
Micro servo motors are similar to regular ones but are usually much smaller and have a lower torque output. The main difference between micro servo motors and servo motor is their size; micro servos are typically less than 20mm in diameter, while regular servos can be up to 40mm or larger.
Also, micro servo motors are more cost-effective than regular servos due to their smaller size and limited torque output. They also often require less current and power to operate, making them ideal for applications that require precision movement but don’t require much force. Micro servos are often used in robotics and automated machines where space is at a premium.
What Are The Differences Between Brushed vs. Brushless Micro Motors?
Brushed and brushless micromotors are two types of motors used in various applications. The main difference between the two is the way they generate electrical current.
Brushed micro motors use brushes to create electrical current, while brushless micro motors use permanent magnets.
Brushless motors are more efficient and quieter than brushed ones but require more complex control systems.
Additionally, brushless motors generally have higher maximum speeds than brushed motors, making them ideal for high-speed applications.
Brushless motors also tend to be more expensive than brushed ones due to their complexity and efficiency advantages.
Ultimately, the choice between brushed or brushless micromotor depends on the application and required performance parameters.