Electric motors and generators are essential components of countless worldwide appliances, machines, and tools. A motor core is a key part of their successful operation. This article will explore a motor core and discuss why it is so important in electric motors and generators.
What Is a Motor Core?
A motor core is an assembly of metal plates called laminations that form the basic structure of an electric motor or generator. It is the base for all component parts, such as rotors, stators, wiring, and housings.
The motor core is the part that generates the magnetic field responsible for the rotational motion of the motor. The size of this part varies from a few mm in tiny motors to several inches in larger ones.
The basic shape of the motor core can vary depending on its purpose. But usually consists of several individual laminations stacked on top of each other to create one piece.
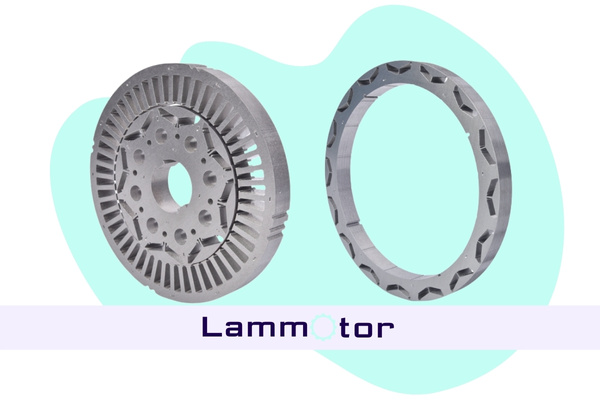
The Role Of The Motor Core In Electric Motors And Generators
The primary role of the motor core is to provide structural integrity for all other components placed within the assembly. Without it, these components would rattle around, causing instability and thus decreased performance from the motor or generator being built with them.
In addition, having strong laminations ensures that no wires become damaged while the device is running due to vibration caused by inadequate rigidity during operation.
Finally, due to their unique design, which makes them mechanically rigid yet electrically isolated from each other, they can produce magnetic fields that help drive current through their respective devices when energized by external power sources such as batteries or AC/DC wall outlets, respectively.
Types of Motor Cores
Motor cores are suitable for various electric motors and generators, from the simplest DC motor to more complex machines like servo motors and stepper motors.
DC Motor Core
DC motor cores are typically made of silicon steel laminations with a wire winding between them, making them lightweight and efficient.
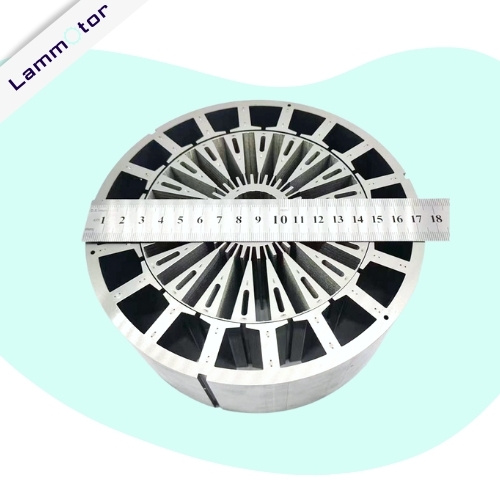
Stepper Motor Core
Stepper motor cores comprise multiple laminations with teeth cut into them to provide precise step control.
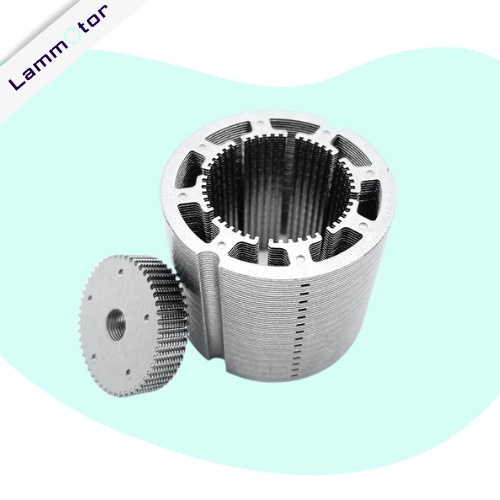
Induction Motor Core
Induction motor cores are also composed of multiple laminations with coils windings to induce a current in larger industrial equipment systems such as pumps and fans.
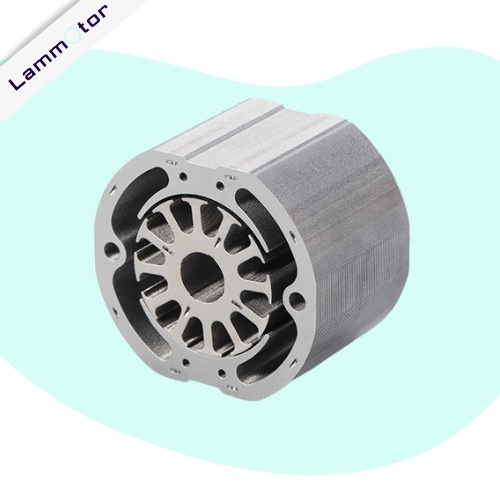
Servo Motor Core
Finally, servo motor cores have the same components as an induction motor core but come with individual feedback sensors that allow them to accurately sense position or speed so that they can be tightly controlled in smaller applications such as robotics.
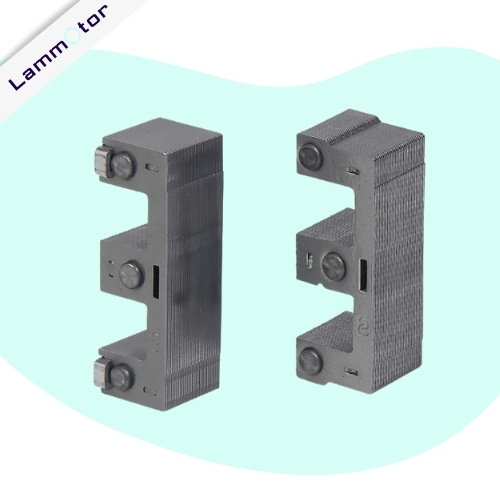
Benefits Of Using Motor Cores In Electric Motors And Generators
There are numerous benefits associated with using motor cores within electric motors and generators:
Increased efficiency
Keeping individual magnetizing sections separate rather than grouping them together as traditionally done via welding techniques allows manufacturers greater control over flux paths within their designs, leading to higher power outputs even at lower speeds.
The Core Motor Controller can control two 9-15 volt DC Motors and automatically change between them based on certain conditions. This allows for faster operation and improved efficiency of the motor.
Last longer
Additionally, motor cores reduce losses due to eddy currents which occur naturally in motors. Furthermore, using motor cores decreases the energy consumed by the motor and increases its durability, allowing it to last longer.
Reduced hum
Induction motors use a laminated core to reduce the humming generated by the alternating current in the core. Using SMC in the stator can further reduce the losses experienced by the motor, thereby reducing the hum caused by the motor.
Soft magnetic composite is a flexible material perfect for complex designs, allowing manufacturers to optimize their motor designs better to reduce hum.
Overall, using a laminated core in induction motors can help improve performance, reduce noise, and save energy.
Our strong manufacturing motor core capability
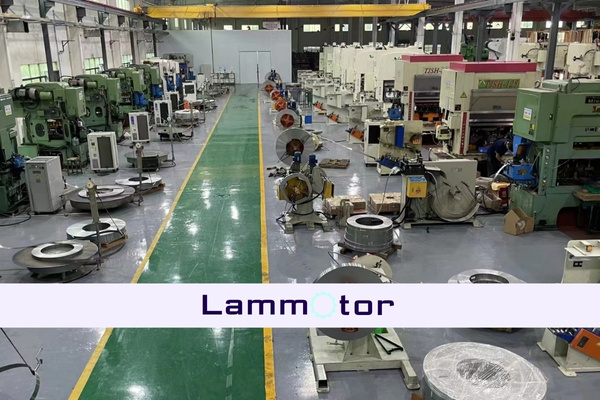
We are a China leader in motor core manufacturing. We can manufacture motor cores for various applications, such as hydroelectric and wind power generators, blowers, freezers, and industrial devices. The motor cores are made of iron and silicon steel and are used in both stator and rotor cores.
We have many stamping technologies, such as progressive, compound, and rotary notching. We also have automated quality inspection systems to ensure precise products. Our motor cores are suitable for automotive drive systems for green cars, with dozens of types currently in use.
What are the applications of motor cores?
Motor cores play an integral role in many everyday applications and industries.
One of the most common uses for motor cores is found in home appliances, like washers, dryers, vacuums, and other small electronics. In these instances, motor cores are designed to withstand high levels of heat and vibration while providing strong structural support for the electrical components inside them.
In addition to common household use cases, motor cores can be suitable for various industrial settings. They are suitable for hydroelectric, wind power generators, and large blowers and freezers.
Automated machines on assembly lines often rely on powerful motors with large core diameters for increased precision and force output (torque).
What are the materials of motor cores?
Motor cores are the backbone of any motor and require special materials that can withstand high temperatures and magnetic fields.
Silicon steel, cobalt alloys, and nickel alloys are three materials used to produce motor cores.
Silicon steel is a ferromagnetic alloy composed primarily of iron with up to 4.5% silicon content by weight. It is known for its high permeability, low coercivity, and low hysteresis losses. Therefore, it is an ideal material for motors due to its ability to maintain a constant level of magnetism under varying loads.
Cobalt alloys contain up to 50% cobalt content and other metals such as iron, chromium, molybdenum, or tungsten.
Conclusion
Motor cores have been integral to electric motors and generators for decades. The production of a high-quality electric motor or generator depends on the quality of the motor core. It is vital to provide enough strength, rigidity, and electrical insulation to withstand the high pressure and temperature inside the electric motor or generator.
We can manufacture motor cores, and we have years of experience producing them for various industries. If you want strong manufacturing motor core capability, contact us today!