Stepper motors, a specialized type of DC motor, stand out for their ability to rotate in precise steps, offering unparalleled control in positioning and speed. Unlike conventional motors that spin freely, stepper motors move in distinct step increments, allowing for exact control of motion. This distinctive feature makes them indispensable in applications demanding high precision, such as in robotics, 3D printing, and computer-controlled machining.
The purpose of this blog is to delve into the intricate world of stepper motors, exploring their types, applications, and the principles behind their operation. Our focus is to provide insights that demystify how these motors function and their pivotal role in precision motion control, equipping readers with knowledge critical for both hobbyists and professionals in fields where precise mechanical movements are paramount.
How Stepper Motors Work?
Lamination stacks in stepper motors play a crucial role in their design and efficiency. These stacks, composed of thinly layered laminations of electrical steel, form the core of the stator or rotor. The use of lamination reduces eddy current losses, a type of energy loss due to the swirling currents induced in the metal by the motor’s magnetic field.
By minimizing these losses, the motor operates more efficiently and generates less heat. The precise construction of these stacks is essential, as it directly impacts the motor’s performance, especially in terms of torque and precision. In essence, the quality and design of lamination stacks are fundamental in determining the efficiency, effectiveness, and reliability of stepper motors.
Stepper motors operate on a simple yet ingenious principle, distinguishing them from other motor types like servo motors. Essentially, these motors move in exact steps, each representing a fraction of a full turn. This precision arises from their internal design: they have multiple coils arranged in phases. Activating these coils sequentially causes the motor’s shaft to rotate step by step, allowing for extremely precise control of movement.
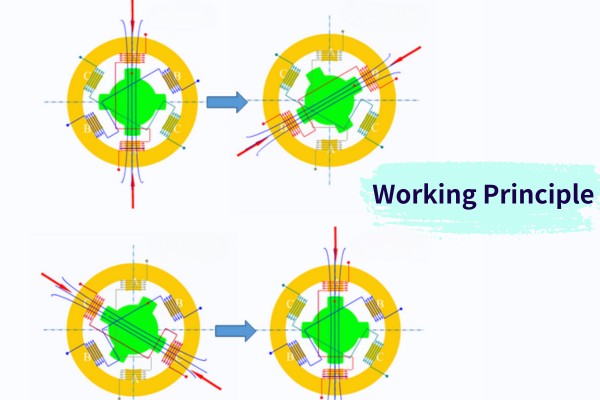
This step-by-step movement is what sets stepper motors apart. They excel in applications where precise positioning is crucial. Unlike standard electric motors that rotate continuously and freely, stepper motors advance in controlled, quantifiable increments. This feature is invaluable in tasks like 3D printing or CNC machining, where exact movements translate to accuracy in the final product.
Types of Stepper Motor
Stepper motors come in various types, each tailored for specific applications, and they can be broadly categorized into three main types: Permanent Magnet, Variable Reluctance, and Hybrid Synchronous motors. Additionally, they are configured as either unipolar or bipolar.
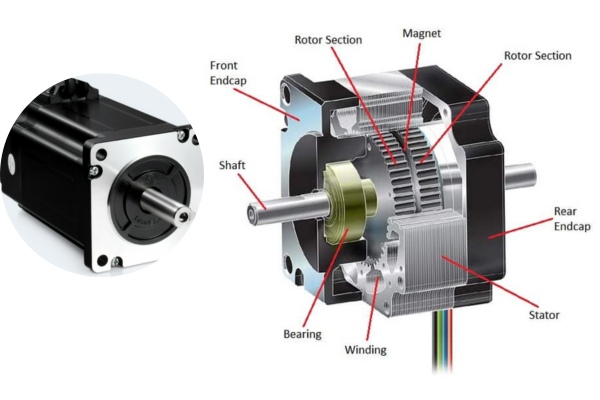
Permanent Magnet Stepper Motor:
This type integrates a permanent magnet in the rotor. The interaction between the rotor’s magnet and the stator’s electromagnets drives the motor’s steps. These motors are known for their robust holding torque at stationary positions. When energized, the rotor aligns itself with the magnetic field of the stator, resulting in motion. The strength of the permanent magnet enhances the motor’s detent torque, ensuring that the rotor maintains its position even when power is not applied.
Variable Reluctance Stepper Motor:
In contrast to permanent magnet types, variable reluctance motors do not use a permanent magnet. Instead, they have a plain iron rotor, making them lighter. They operate on the principle of minimizing magnetic reluctance. The absence of a permanent magnet means they typically have lower holding torque, but they can achieve higher step rates due to their lighter rotors.
Hybrid Synchronous Stepper Motor:
These motors combine the best features of both permanent magnet and variable reluctance types. The hybrid stepper motor offers better performance with higher torque at lower speeds and finer step resolution. This is achieved by using a rotor that contains both an iron core and a permanent magnet.
Unipolar and Bipolar Configurations:
The distinction between unipolar and bipolar motors lies in their coil activation. Unipolar motors have coils with a middle tap, and each half of the coil is activated alternatively, simplifying the driving circuitry. Bipolar motors, on the other hand, require current to be reversed through the entire coil for movement, necessitating more complex driving circuits. Bipolar configurations tend to offer better torque characteristics compared to unipolar motors.
Each type of stepper motor and configuration has its advantages and is chosen based on the specific requirements of the application, such as precision, torque, speed, and ease of control.
Applications of Stepper Motors
Stepper motors, renowned for their precision in control and movement, find extensive applications in various fields. Here’s a list highlighting some of their key uses:
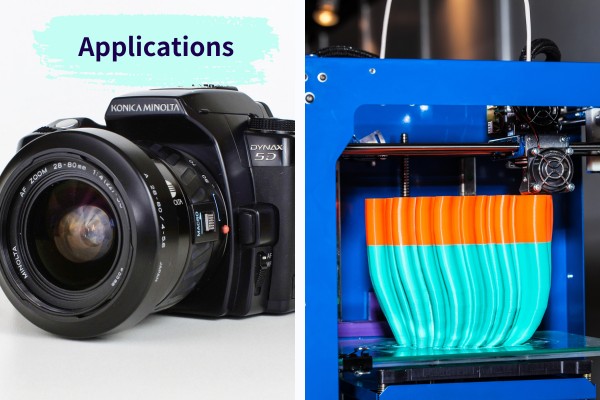
Computing: Stepper motors are integral in computer peripherals. They are used in disk drives for precise head positioning and in printers for paper feed control. Their ability to execute precise movements makes them ideal for these applications.
Robotics: In robotics, stepper motors are essential for achieving controlled motion. They are used to drive robotic arms, enabling precise movements and positioning, which is crucial in assembly lines and automated processes.
Cameras: Stepper motors play a critical role in cameras, particularly in autofocus and zoom functions. Their precision allows for smooth and accurate adjustment of the lens position, enhancing image quality.
3D Printers: One of the most prominent applications of stepper motors is in 3D printers. They control the movement of the print head and the platform, allowing for layer-by-layer construction with high accuracy.
CNC Machines: In CNC (Computer Numerical Control) machinery, stepper motors are used to control the position of the tool. They facilitate precise cutting, drilling, or engraving on various materials, making them indispensable in manufacturing and prototyping.
Medical Devices: Stepper motors are employed in medical equipment like scanners and digital dental photography, where precise movement is critical.
Consumer Electronics: They are used in devices like computer scanners, digital watches, and camera focus mechanisms.
Each of these applications leverages the unique ability of stepper motors to perform exact movements, and repeatable steps, and maintain precise positioning, which is essential in technology-driven industries.
Advantages and Limitations of Stepper Motors
Stepper motors, while widely used for their precision control, have both advantages and limitations that define their suitability for various applications. Here’s a brief list highlighting these aspects:
Advantages:
Precision Control: They offer exact positioning and repeatability, crucial for applications like robotics and 3D printing.
Low-Speed Torque: Stepper motors provide maximum torque at low speeds, ideal for applications that require stable, controlled movements.
No Feedback System Required: Unlike servo motors, they operate efficiently without a feedback mechanism, simplifying their design and use.
Reliability: Their simple construction leads to high reliability and low maintenance requirements.
Ease of Control: Stepper motors can be easily controlled with digital circuits and microcontrollers, making them versatile for various technological applications.
Limitations:
Low Efficiency: These motors consume power even when stationary, leading to lower overall efficiency and heat generation.
Limited High-Speed Performance: At higher speeds, stepper motors tend to lose torque, limiting their effectiveness in applications requiring high-speed operations.
Resonance and Vibration: Stepper motors can exhibit resonance or vibration at certain speeds, which may require additional damping methods to mitigate.
Noise: They can be noisier than other types of motors, especially at higher speeds.
Conclusion
In conclusion, stepper motors, with their distinct ability for precision control and versatile applications, are pivotal in modern technology. Understanding their types, applications, and selection criteria is crucial for optimal utilization in diverse fields. This comprehensive exploration provides valuable insights, ensuring informed decisions in stepper motor usage for effective and efficient outcomes.
FAQs
What distinguishes a stepper motor from other motor types?
Stepper motors differ from other motor types mainly in their movement control. They rotate in precise, small increments, known as steps, offering exceptional control in positioning and speed. This contrasts with standard motors that rotate continuously. The stepper motor’s ability to move in exact increments makes it ideal for applications requiring high-level precision, like robotics and 3D printing, where exact positioning is crucial.
Can stepper motors operate at high speeds efficiently?
Stepper motors typically excel at low to medium speeds but may lose efficiency and torque at higher speeds. Their design prioritizes precision and control over speed. At higher speeds, they can experience a reduction in torque and may struggle to maintain precision. Therefore, while they can operate at high speeds, their efficiency and effectiveness are optimized at lower speeds, making them ideal for applications that demand accuracy over rapid movement.
How do you determine the right stepper motor for a specific application?
Selecting the right stepper motor requires evaluating several factors: the required torque and precision, the motor’s size and type (permanent magnet, variable reluctance, or hybrid), and the electrical characteristics like voltage and current. The application’s specific needs, such as the environment in which the motor will operate and the desired control method (unipolar or bipolar), also play a crucial role in this decision-making process.
What are the key considerations for maintaining a stepper motor?
Maintaining a stepper motor involves regular inspection for wear and tear, ensuring proper lubrication, and monitoring for overheating. It’s important to keep the motor clean and free from dust and debris. Regular testing of the motor’s performance and electrical connections is also vital. Keeping the motor within its operating limits and using it in suitable environmental conditions ensures longevity and consistent performance.
How does the choice of stepper motor impact the performance of a 3D printer or CNC machine?
The choice of stepper motor significantly affects the precision and accuracy of a 3D printer or CNC machine. A motor with appropriate torque and a suitable step angle ensures precise movement and positioning, which is crucial for detailed work. The motor’s reliability and control method (unipolar or bipolar) also influence the machine’s overall performance, affecting its ability to produce high-quality, consistent outputs.