When it comes to electric motors, there are two main types that you need to know about inner rotor and outer rotor motors. While they may look similar on the surface, these two motor designs have some key differences that can impact their performance and applications.
In this blog post, we’ll dive into the details of inner and outer rotor motors, exploring how they work, what sets them apart, and which one might be the best fit for your specific needs.
So if you’re curious about the inner workings of electric motors or want to understand the nuances between these two rotor motor lamination designs, keep reading!
What Are Inner Rotor Motors?
Inner rotor motors, a cornerstone in modern motor technology, boast a distinct design that sets them apart. At their core, these motors consist of a rotor positioned inside the stator, a configuration that fuels their efficiency.
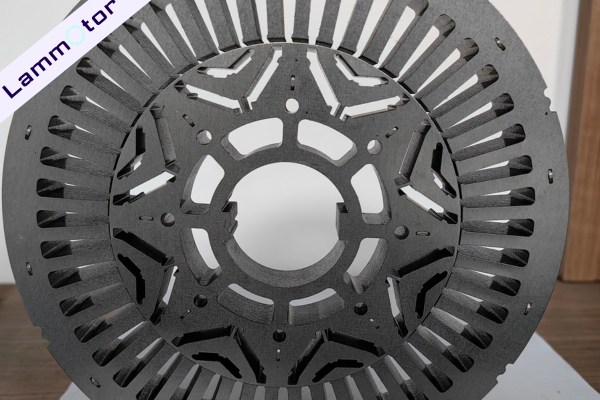
The inner rotor motor structure comprises essential components, each contributing to its seamless functionality. The rotor, a central element, rotates within the stator, generating the desired motion.
This motion is harnessed by key components such as the winding and magnets, working in tandem to propel the motor’s performance.
Advantages of Inner Rotor Motor Design
Compact Size: Inner rotor motors exhibit a compact design, making them ideal for applications with limited space constraints.
Higher Efficiency: The internal rotor configuration enhances the efficiency of these motors, translating electrical energy into mechanical power more effectively.
Quick Response: Due to their design, inner rotor motors offer rapid response times, crucial for applications requiring swift and precise movements.
Low Inertia: The placement of the rotor within the stator reduces inertia, enabling quicker acceleration and deceleration.
Versatile Applications: Inner rotor motors find applications in a diverse range of industries, from automotive systems to robotics, showcasing their adaptability and versatility.
What Are Outer Rotor Motors?
Outer rotor motors, also known as external rotor motors, differ from traditional inner rotor motors in terms of their design. Instead of having the rotor positioned within the stator, outer rotor motors have the rotor located on the outer circumference. This configuration enhances heat dissipation, resulting in improved overall efficiency.
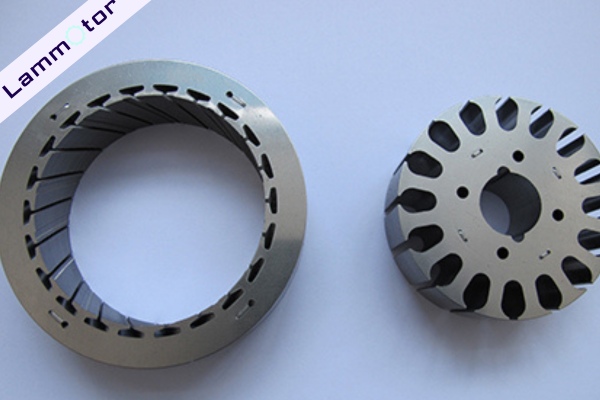
Moreover, outer rotor motors exhibit a compact structure and reduced inertia, contributing to quicker response times and higher torque density.
These motors find applications in various fields, including robotics, aerospace, and electric vehicles, where their unique design characteristics offer advantages in terms of size, weight, and performance.
Benefits of Outer Rotor Motor Design
Enhanced Cooling: The external rotor design facilitates better heat dissipation, preventing overheating and ensuring prolonged operational life.
Higher Torque: Outer rotor motors often exhibit higher torque values, making them suitable for applications demanding increased rotational force.
Improved Stability: The external rotor configuration enhances stability, reducing vibrations and providing a smoother operation in various industrial settings.
Ease of Maintenance: Access to external components simplifies maintenance tasks, allowing for quicker and more straightforward servicing.
Space Utilization: Outer rotor motors can offer efficient use of available space, particularly in applications where the external configuration aligns with spatial requirements.
Performance Comparison: Inner VS Outer Rotor Motors
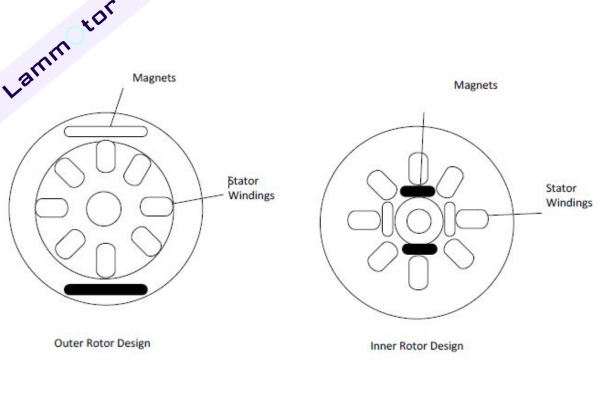
A. Efficiency and Power Output
Inner rotor motors, with their compact structure, often exhibit higher efficiency due to reduced internal losses. They efficiently convert electrical energy into mechanical power, making them suitable for applications demanding precision and responsiveness.
On the other hand, outer rotor motors, with their external configuration, boast higher torque values, contributing to increased power output.
The choice between the two depends on the specific requirements of the application, weighing factors such as energy efficiency, and the magnitude of rotational force needed.
B. Size and Weight Considerations
Considering size and weight, inner rotor motors shine in applications with space constraints. Their compact design allows for easy integration into systems where size is a critical factor.
Outer rotor motors, while potentially larger, leverage their external arrangement to provide advantages in specific scenarios where size is less restrictive.
Balancing these considerations is essential in selecting the motor that aligns best with the spatial and weight requirements of a given application.
Applications in Industries
A. Inner Rotor Motors in Industry
Within various industries, inner rotor brushless motors find versatile applications, leveraging their compact design and efficiency.
Automotive Systems: Powering components such as electric power steering and fans.
Robotics: Enabling precise and rapid movements in robotic arms and automation systems.
Medical Devices: Driving equipment like pumps and surgical tools with accuracy.
B. Outer Rotor Motors in Industry
Outer rotor brushless motors, with their unique external structure, excel in specific industrial applications.
HVAC Systems: Providing efficient airflow in heating, ventilation, and air conditioning units.
Wind Turbines: Harnessing wind energy with the external rotor design for power generation.
Industrial Fans: Offering high-torque performance for applications requiring substantial rotational force.
Choosing the Right Motor for Specific Applications
When selecting a motor for specific applications, careful consideration of various factors is crucial. The choice between inner and outer rotor motors depends on specific requirements. Here are key considerations:
Space Constraints: Evaluate the available space for motor installation.
Heat Dissipation: Assess the thermal requirements of the application and choose a motor that ensures efficient heat dissipation.
Response Time: Inner rotor motors offer quick response times, while outer rotor motors may provide advantages in certain applications due to reduced inertia.
Torque Density: Consider the desired torque output and select a motor that meets the application’s torque density requirements.
Weight: Evaluate the weight limitations of the system and choose a motor that aligns with those constraints.
Application Type: Different applications may benefit from the specific advantages offered by inner or outer rotor motors. Consider the application’s demands and characteristics.
Efficiency: Assess the overall efficiency of the motor to the application’s power requirements.
By carefully weighing these factors, you can make an informed decision on whether an inner or outer rotor motor is best suited for your specific application.
Conclusion
In conclusion, the disparities between external rotor motors and internal rotor motors are pivotal in understanding their distinct applications.
Inner rotor motors, with their efficiency and compact design, excel in industries demanding precision. Conversely, outer rotor motors, offering higher torque and stability, find their niche in applications requiring robust rotational force.
The significance of choosing the right motor cannot be overstated. Aligning the motor type with specific needs ensures optimal performance, efficiency, and longevity in diverse industrial settings.
FAQs
Which motor type is more energy-efficient?
Inner rotor motors typically exhibit higher energy efficiency compared to outer rotor motors due to their compact design and reduced inertia.
In what industries are inner rotor motors commonly used?
Inner rotor motors find common usage in industries such as robotics, automotive, and precision equipment, benefiting from their quick response times and compact size.
Can outer rotor motors be used in small-scale applications?
Yes, outer rotor motors can be used in small-scale applications, leveraging their advantages in heat dissipation and compact structure for specific requirements.