In motor design and applications, do you often wonder how to choose the most suitable motor for a specific application? DC motors, AC motors, asynchronous motors, synchronous motors, stepper motors, and servo motors—all these types of electric motors have different working principles, structural features, and application scenarios.
If the wrong motor is selected, it may lead to wasted performance or project failure. As a motor designer or engineer, you need to deeply understand these motors’ characteristics to make the best choice for your projects.
As an experienced China motor manufacturer, we specialize in motor core production while accumulating extensive industry knowledge.
We will summarize common types of electric motors and their features to help you make efficient decisions during design. You will find the best solution for industrial equipment, automation systems, or new energy vehicles.
By Power Supply Type
1. DC Motors
DC motors use DC power as the energy source. They generate torque by the interaction between the current-induced magnetic field and the rotor magnetic field. Known for their excellent speed regulation and precise control, they are widely used in many scenarios. Based on their structure and commutation methods, we divided several types of DC motors.
1.1 Brushless DC Motors
Brushless motors are direct current motors without mechanical commutators, relying on electronic commutation to alternate the rotor’s magnetic field. They are an upgrade to traditional brushed motors.
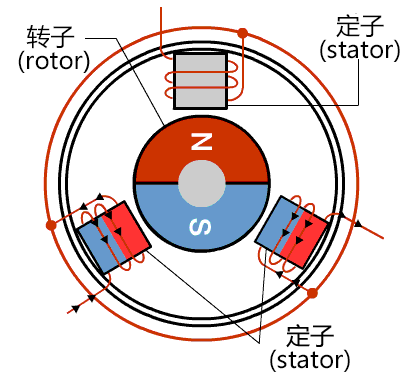
Features: No mechanical brushes, longer service life; low noise, high efficiency, and precise control.
Structure: Composed of a permanent magnet rotor, multi-pole wound stator, and position sensors.
Working Principle: Position sensors detect rotor position and commutate the current in stator windings in a certain sequence. Electronic switch circuits, controlled by position sensor output, supply the stator winding’s working voltage.
Applications: BLDC motor used in home appliances (e.g., air conditioners, fans), industrial automation equipment, electric vehicles, and drones.
1.2 Brushed DC Motors
Brushed DC motors are traditional DC motors that use mechanical commutators and brushes to alternate the rotor’s magnetic field.
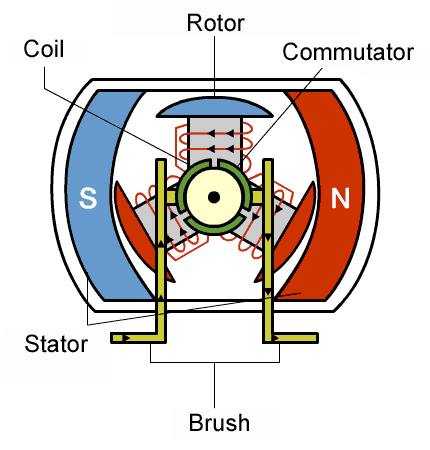
Features: Simple structure, low cost, easy torque and speed control, but the brushes wear out and require regular maintenance.
Structure: Includes a stator, brushes, commutators, and a rotor. The commutators and brushes are key components.
Applications: home appliances (e.g., vacuum cleaners), toys, and starter motors for vehicles.
Permanent Magnet DC Motors
Permanent magnet DC motors use permanent magnets as the source of the stator magnetic field, eliminating the complexity of electromagnetic designs.
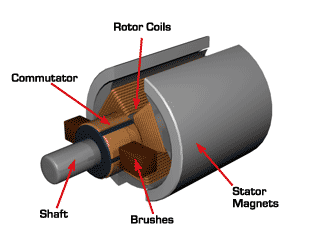
Types:
- Samarium cobalt permanent magnet DC motors.
- Ferrite permanent magnet DC motors.
- Alnico permanent magnet DC motors.
Applications: robotics, electronic devices, and small electric vehicles.
Electromagnetic DC Motors
Electromagnetic DC motors generate magnetic fields using electromagnets to drive rotor motion.
Features: Adjustable magnetic field strength, suitable for high-power applications, but more complex and less efficient than permanent magnet motors.
Structure: Composed of stator magnetic poles, rotor (armature), commutator (commonly called a rectifier), brushes, housing, and bearings.
Applications: industrial equipment, rail transit, and heavy machinery.
Subtypes by Excitation Method:
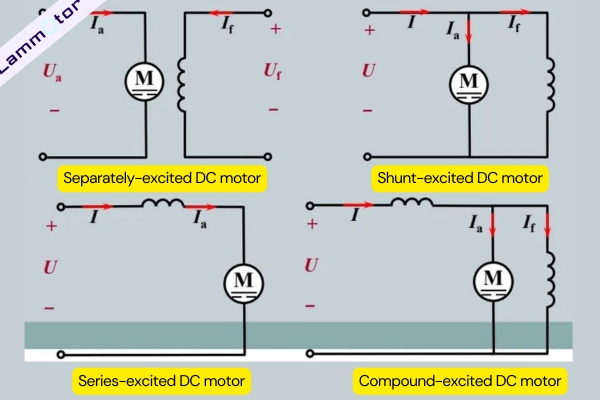
Series DC Motors: Stator windings and rotor windings are connected in series, providing high starting torque, ideal for heavy-load starting applications.
Shunt DC Motors: Stator windings and rotor windings are connected in parallel, ensuring good speed stability and smooth operation, commonly used for precision control.
Compound DC Motors: Combine series and shunt characteristics, suitable for strong starts and stable operation.
Separately Excited DC Motors: Allow separate power sources for stator and rotor, enabling better control over the armature winding to generate flux.
2. AC Electric Motors
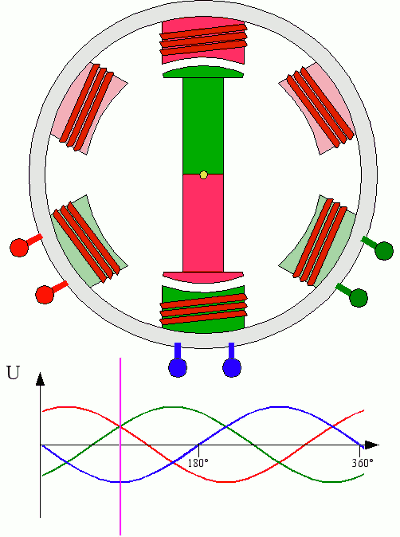
AC motors use alternating current as the power supply and drive rotor motion through alternating magnetic fields. Due to the wide availability of AC power, AC motors are the most commonly used motor type in both industrial and household applications. Based on power phases, they can be divided into single-phase AC motors and three-phase AC motors.
2.1 Single-Phase AC Motors
Single-phase AC motors operate on single-phase AC power and are suitable for low-power applications.
Features: Simple structure, small size, and low cost; however, they have low starting torque, suitable for light loads.
Structure: Mainly composed of a stator, rotor, and starting device (e.g., capacitor).
Applications: household appliances (e.g., fans, washing machines) and small pumps or compressors.
2.2 Three-Phase AC Motors
Three-phase AC motors are driven by three-phase AC power and produce rotating magnetic fields to drive the rotor.
Features: High efficiency, large power output, stable operation, suitable for industrial and high-power applications.
Structure: Includes a stator with three-phase windings, a rotor (cage-type or wound), and a housing.
Applications: machine tools, hoisting equipment, fans, pumps, and compressors.
Classification by Structure and Working Principle
Electric motors can also be categorized by structure and working principle into three main types: DC motors, asynchronous motors, and synchronous motors. Each motor type can be further divided into several subcategories based on its specific structure and operating method. Below, we focus on asynchronous and synchronous motors.
1. Asynchronous Electric Motors
1.1 Induction Motors
Induction motors are widely used AC motors that operate on the principle of electromagnetic induction. Without physical contact, they induce a current in the rotor, generating torque. We divided induction motors into single-phase and three-phase types based on the power supply.
Single-Phase Induction Motors
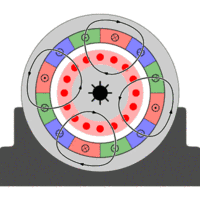
Single-phase asynchronous motors use single-phase AC as the power source and are suitable for low-power equipment. Their starting relies on auxiliary devices (such as capacitors) to overcome the disadvantage of lack of a rotating magnetic field.
Features: Simple structure, compact size, and affordability. They have lower starting performance but stable operation, making them suitable for light loads.
Structure:
- Stator: Contains a main winding for operation and an auxiliary winding for starting.
- Rotor: Typically cage-shaped, made of copper or aluminum bars forming a conductive circuit.
- Starting Device: Includes capacitors or centrifugal switches to improve starting torque.
Applications: household appliances such as fans, washing machines, and refrigerator compressors, as well as small machinery like pumps and tools.
Three-Phase Induction Motors
The three-phase asynchronous motor is the most commonly used type of motor in industry, using three-phase alternating current to generate a rotating magnetic field to drive the rotor.
Features: High efficiency, robust structure, and easy maintenance. They operate reliably and deliver high power output, suitable for industrial environments.
Structure:
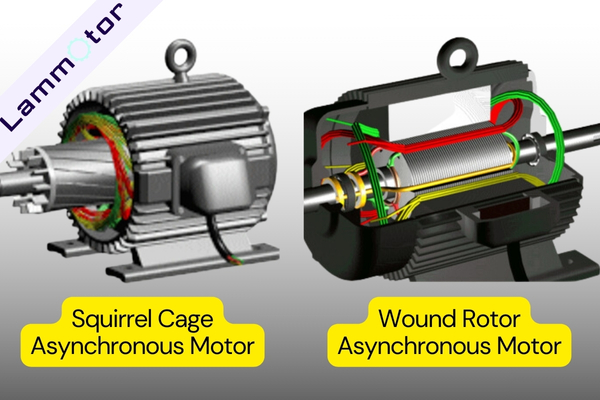
- Stator: Features three-phase windings that produce a rotating magnetic field.
- Rotor: Can be cage-type or wound, with cage rotors being more common.
- Housing: Typically made of cast iron or aluminum for mechanical protection.
Applications: industrial power equipment like machine tools, fans, pumps, compressors, and construction systems such as elevators and air conditioning systems.
Shaded-Pole Motors
The shaded-pole asynchronous motor is a special low-power asynchronous motor suitable for light-load operation and is commonly used in household appliances.
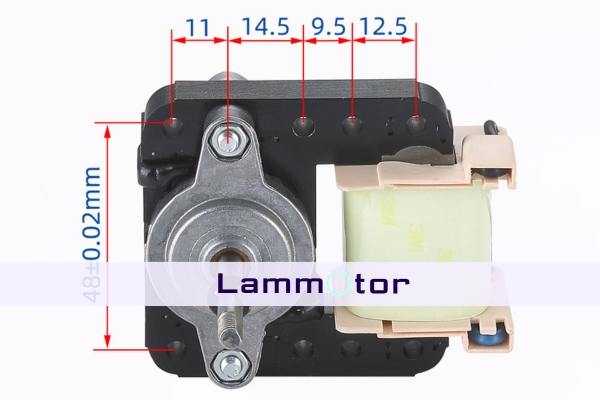
Features:
- Simple and inexpensive, suitable for light-load applications. No additional starting equipment is required, but their efficiency is relatively low.
- Structure:
- Stator: Includes shaded coils that create an asymmetric magnetic field to start the motor.
- Rotor: A cage-type rotor.
- Housing: Made of metal or plastic, protecting internal components.
Applications: Found in household devices such as fans, microwaves, and air conditioner fans, as well as in light industrial equipment.
1.2 AC Commutator Motors
AC commutator motors combine the commutation principles of DC motors with AC power supply operation. They are widely used in applications requiring high starting torque and speed adjustment.
Single-Phase Series Motors
The single-phase series-wound motor is a high-torque motor named because the stator and rotor windings are connected in series and can be used for both AC and DC power supply.
Features:
- Provide high starting torque and speed, suitable for heavy-load applications. However, they are noisy, wear quickly, and require regular maintenance.
- Structure:
- Stator: Contains series windings that produce the main magnetic field.
- Rotor: Connected in series with the stator windings via a commutator, ensuring current flows in the same direction.
- Commutator and Brushes: Switch the current direction.
Applications: household appliances like vacuum cleaners, blenders, and power tools, as well as in traction motors for electric vehicles.
Universal Motors
AC/DC dual-purpose motors can operate in both AC and DC environments and have good compatibility.
Features: Operable on both AC and DC power supplies, offering excellent flexibility. Compact and efficient.
Structure:
- Stator and Rotor Windings: Connected in series.
- Commutator and Brushes: Provide current switching.
Applications: Found in household and industrial equipment such as electric shavers, hair dryers, and small tools.
Repulsion Motors
The stator windings are powered by single-phase electricity, while the rotor is a short-circuited armature winding with brushes. When the brushes deviate from the geometric axis, the rotor generates torque in the opposite direction of the brush offset.
Features: High starting torque but relatively low efficiency.
Applications: Previously used in old electric trains and specific industrial equipment.
2. Synchronous Motors
Synchronous electric motors are unique motors where the rotor speed matches the speed of the stator’s rotating magnetic field (synchronous speed). Based on the source of the rotor’s magnetic field and structural characteristics, synchronous motors are classified into three main types:
2.1 Permanent Magnet Synchronous Motors (PMSM)
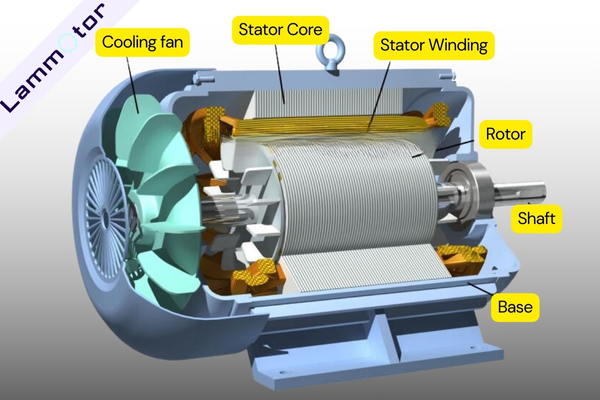
Permanent magnet synchronous motors are classified based on the structure of the permanent magnets in the rotor. There are three main types: surface-mounted permanent magnet synchronous motors (SPMSM), embedded permanent magnet synchronous motors (IPMSM), and hybrid permanent magnet synchronous motors.
Surface-Mounted Permanent Magnet Synchronous Motors (SPMSM):
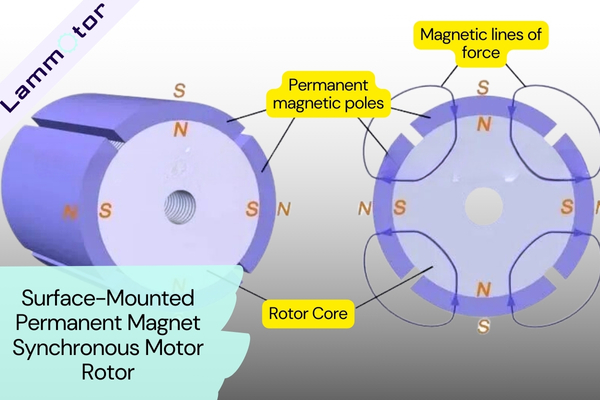
In this type, the permanent magnets are mounted on the surface of the rotor. This structure is relatively simple and cost-effective. These motors are suitable for medium- and low-power applications, with good magnetic field utilization. However, their rotor inertia is relatively large, limiting their high-speed performance.
Applications: Common in household appliances, fans, and small electric vehicles, where high efficiency is required but extreme performance is not.
Embedded Permanent Magnet Synchronous Motors (IPMSM):
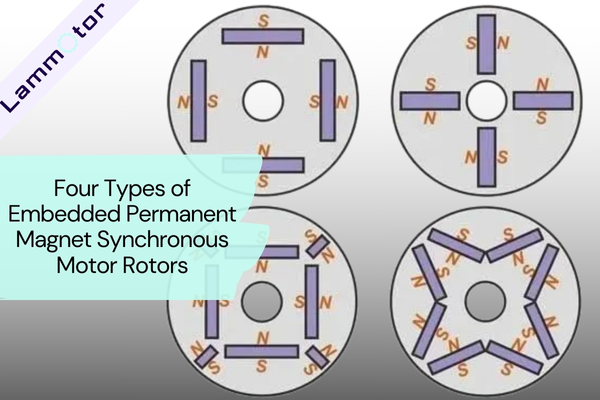
In these motors, the permanent magnets are embedded within the rotor. This design protects the magnets, improves mechanical strength, and allows for higher rotational speeds. Additionally, the embedded structure enhances torque output through magnetic reluctance effects.
Applications: Widely used in high-performance scenarios.
For example, Tesla’s Model 3 and Model Y utilize embedded permanent magnet synchronous motors, which deliver high power density and efficiency, improving vehicle range and acceleration.
Hybrid Permanent Magnet Synchronous Motors:
This type combines permanent magnets with reluctance effects. The rotor structure includes embedded magnets and materials that utilize magnetic reluctance to enhance performance.
Applications: Used in industrial equipment and specialized machinery, such as high-end robots and aerospace motor systems, requiring both high efficiency and high torque.
2.2 Reluctance Synchronous Motors (SRSM)
Reluctance synchronous electric motors rely on the difference in magnetic reluctance in the rotor to generate torque. These motors do not use windings or permanent magnets on the rotor, and the rotor is purely made of iron cores. The unique design makes them highly reliable and cost-effective.
Structure:
- Stator: Similar to traditional synchronous motors, with three-phase symmetrical windings.
- Rotor: Composed of iron cores designed to create significant radial and circumferential magnetic reluctance differences.
Features:
- Low Cost: Simple rotor design without permanent magnets reduces costs.
- High Reliability: No brushes, commutators, or magnets, making them suitable for harsh environments.
- Moderate Efficiency: Efficiency is lower than permanent magnet synchronous motors.
- Noise and Vibration: Magnetic reluctance torque can cause vibrations and noise, requiring advanced control algorithms.
Applications: Reluctance synchronous motors are commonly used in pumps, fans, compressors, and low-end industrial devices. They are also alternatives to induction motors in scenarios where permanent magnet motors are unsuitable.
2.3 Hysteresis Synchronous Motors
Hysteresis synchronous motors operate by utilizing the magnetic hysteresis properties of rotor materials to generate torque. These motors are known for their smooth operation and quiet performance, making them ideal for precision applications.
Structure:
- Stator: Features three-phase symmetrical windings to create a rotating magnetic field.
- Rotor: Made of materials with high magnetic hysteresis, without windings or permanent magnets.
Features:
- Smooth Starting: Can start smoothly without additional equipment.
- Quiet Operation: Almost no mechanical noise during operation.
- Lower Efficiency: Torque density is low, unsuitable for high-power applications.
Applications: precision instruments, laboratory equipment, clocks, and small synchronous drives.
Other Types of Motors
1. Stepper Motors
Stepper motors convert electrical pulse signals into mechanical angular displacement. They operate in discrete steps, with each pulse causing the rotor to rotate by a fixed angle. By controlling pulse frequency and number, precise speed and position control can be achieved.
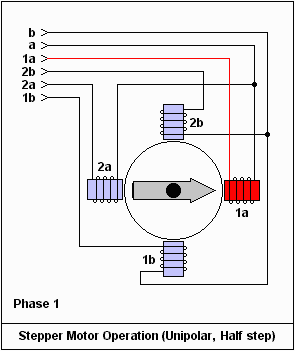
Features:
- Precise open-loop control without feedback.
- Quick start, stop, and reverse responses.
- High torque at low speeds but poor high-speed performance.
- Lower efficiency, prone to overheating during extended use.
Structure:
- Stator: Contains multiple windings arranged to produce a magnetic field. Stepper motors are commonly two-phase, three-phase, or five-phase.
- Rotor: Includes permanent magnet and reluctance rotor types.
- Driver System: Includes controllers and driver circuits to generate pulse signals.
Applications: 3D printers, CNC machines, robotic joints, camera gimbals, medical devices, and positioning systems in automated production lines.
2. Servo Motors
Servo motors offer precise control of position, speed, and acceleration, typically used in closed-loop control systems. Real-time feedback from position sensors allows for high accuracy and dynamic adjustment of motor operations.
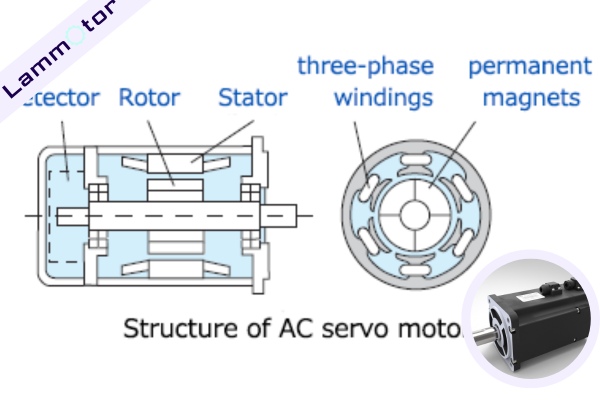
Structure:
- Stator: Contains three-phase windings to produce a rotating magnetic field.
- Rotor: Made of permanent magnets or conductive materials.
- Control System: Includes sensors (e.g., encoders) and servo drives for closed-loop control.
Features:
- Fast dynamic response with a wide speed range.
- High precision, suitable for complex motion control.
- Stable operation with high-performance output.
Applications: industrial automation (e.g., robotic arms), precision CNC machines, automated production lines, medical equipment (e.g., surgical robots), and new energy vehicles.
3. Switched Reluctance Motors (SRM)
Switched reluctance motors operate on the principle of magnetic reluctance. Their rotors have no windings or magnets, relying solely on reluctance effects. By sequentially energizing stator windings, magnetic attraction rotates the rotor.
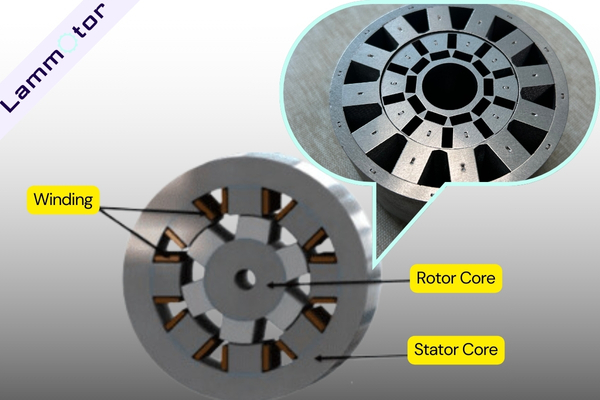
Structure:
- Stator: Contains multiple-phase windings to create magnetic fields.
- Rotor: Made of iron cores without windings or magnets.
- Control System: A specialized controller adjusts phase currents for efficient operation.
Features:
- Simple rotor design, low cost, and high reliability.
- No brushes, suitable for high-temperature and harsh environments.
- Higher noise and vibration, requiring advanced control methods.
Applications: electric vehicles, industrial pumps, fans, washing machines, and compressors.
4. Gear Motors
Gear motors combine an electric motor with a gear reducer to lower the motor’s speed while increasing output torque. By adjusting the gear ratio, the motor’s high-speed output is converted to low-speed, high-torque output.
Structure:
- Motor: Typically an AC or DC motor.
- Gear Reducer: Includes gears or worm mechanisms for torque conversion.
- Connection: Shafts or flanges link the motor and reducer.
Features:
- Compact structure and easy installation.
- Provides high output torque for heavy loads.
- Supports various speeds and load requirements.
Applications: conveyors, robotic arms, industrial mixers, automatic doors, and medical equipment.
5. Linear Motors
Linear motors directly convert electrical energy into linear motion without intermediate mechanical transmission. By creating a moving magnetic field in the stator, electromagnetic force moves the rotor along a track.
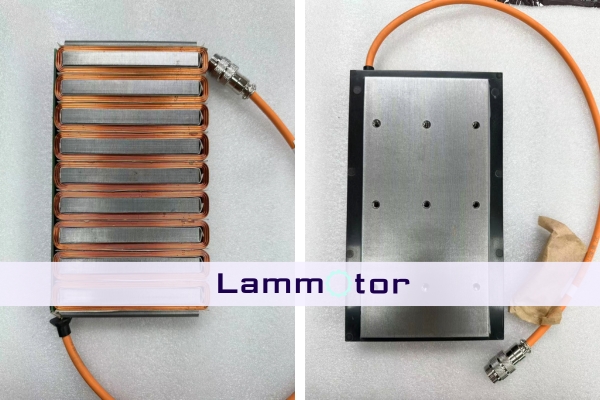
Structure:
- Stator: Long and linear, containing windings that produce a moving magnetic field.
- Rotor: A slider or guide containing magnets or conductive materials.
- Support System: Ensures smooth motion along the linear path.
Features:
- No mechanical transmission, resulting in high efficiency.
- Quick dynamic response with precise positioning.
- Simple structure, ideal for high-speed linear motion.
Applications: Linear motors are used in CNC machines, semiconductor manufacturing, maglev trains, automated transportation systems, and precision measuring instruments.
Contact Us for Motor Core Laminations!
There are many types of motors. Understanding the different types of motors can help you improve your design efficiency and ensure the success of your project.
As a professional motor core manufacturer, Lammotor provides high-quality motor core solutions for various types of electric motors. From prototype design to large-scale production, we meet your specific needs. Contact us today for premium motor cores and expert support. Let us help you succeed in your projects!