There are many types of pumps on the market, such as centrifugal pumps, gear pumps, piston pumps, and more. Each has its own advantages and specific application scenarios. However, without understanding their characteristics, it’s easy to choose the wrong one, which can lead to inefficiency or frequent problems during use.
As a water pump motor manufacturer with years of experience, we deeply understand the importance of selecting the right pump. In this article, I will explain the working principles and performance features of 8 common types of pumps to help you find the one that suits your needs best.
Let’s get started!
1. Centrifugal Pumps
When centrifugal pumps work, the pump casing is filled with liquid, and the impeller rotates at high speed. The liquid gains high velocity under the effect of centrifugal force. As the high-speed liquid passes through the gradually widening passage of the pump casing, its dynamic pressure converts into static pressure.
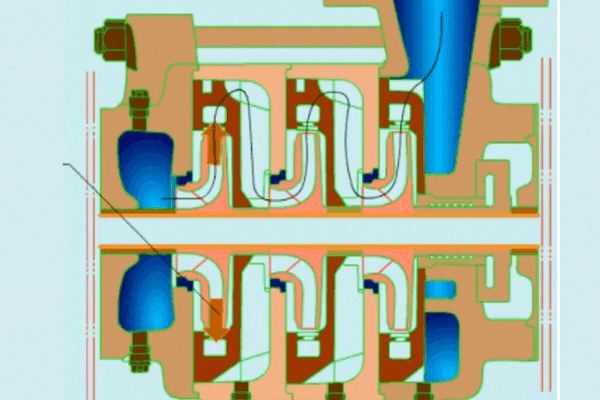
Difference Between Single-Stage and Multistage Centrifugal Pumps
Single-stage centrifugal pumps: Have only one impeller and are suitable for low to medium head scenarios.
Multistage centrifugal pumps: Have two or more impellers that work in series to increase liquid pressure step by step, enabling the delivery of water to greater heights. By adjusting the number of impellers, the head of multistage pumps can be flexibly customized.
Types of Multistage Centrifugal Pumps
Vertical multistage centrifugal pumps:
Impellers and pump shafts are arranged vertically, offering a compact structure and small footprint.
Suitable for spaces with limited installation room, such as high-rise building water supply and boiler feed water.
Horizontal multistage centrifugal pumps:
Impellers are arranged horizontally, making maintenance and servicing convenient.
Commonly used in industrial water supply, large-scale mine drainage, and long-distance liquid transport.
Both types have similar head and flow performance but can be selected based on installation environment, space constraints, and maintenance requirements.
Compared to reciprocating pumps like piston pumps and diaphragm pumps, multistage centrifugal pumps can deliver larger flow rates. With high efficiency, they meet the needs of high-head and high-flow conditions and are widely used in industries such as petrochemicals, chemicals, power, construction, and firefighting.
2. Diaphragm Pumps
A diaphragm pump is a positive displacement pump that uses a diaphragm to separate the air chamber from the liquid medium. It is mainly used for transferring corrosive or specialized liquids. Air-operated diaphragm pumps use compressed air as the power source, avoiding the limitations of electric devices. They are highly adaptable and perform reliably.
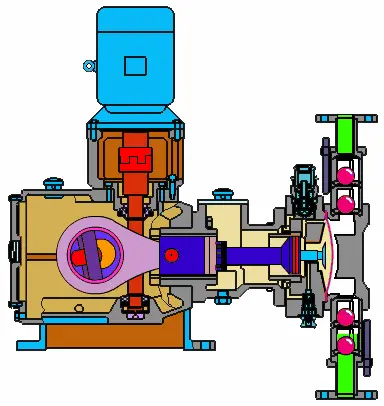
Working Principle
The core of an air-operated diaphragm pump is the separation of liquid and pneumatic chambers by a flexible diaphragm. The diaphragm’s reciprocating motion completes the suction and discharge of liquids. This design protects the piston from direct contact with corrosive liquids and allows the pump to handle various liquid media.
Material Classification
Based on pump body materials, air-operated diaphragm pumps are classified as follows:
- Plastic: Highly corrosion-resistant, suitable for the chemical industry.
- Aluminum alloy: Suitable for transporting clean liquids.
- Cast iron: High strength, ideal for general industrial applications.
- Stainless steel: Offers excellent corrosion resistance and hygiene, suitable for the food and pharmaceutical industries.
Performance Features
- Adaptability to various liquids: Capable of transferring low to high viscosity, corrosive, or thick liquids.
- High reliability: Powered by compressed air, eliminating the risk of electric sparks. Can run dry without damaging the pump.
- Material-friendly design: Low shear force ensures sensitive liquids remain intact.
- Energy efficiency: Self-priming and submersible capabilities, with adjustable flow rates.
- Strong adaptability: Safe and environmentally friendly for various conditions, including mining, chemicals, food processing, and pharmaceuticals.
3. Gear Pumps
A gear pump is a common volumetric pump that moves liquids through the meshing and separation of gears. It is widely used in hydraulics, lubrication, chemicals, and other industrial fields due to its simple structure and reliable operation.
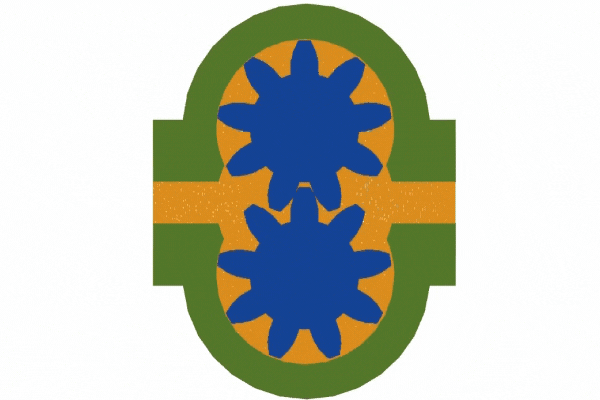
Working Principle
- Liquid suction: As the gear teeth separate, a low-pressure zone forms, pulling liquid into the pump.
- Liquid transport: The liquid is carried along the pump casing by the rotating gears.
- Liquid discharge: At the discharge port, the gear teeth mesh, creating high pressure to expel the liquid.
Advantages
- Compact structure and simple design.
- Strong self-priming ability, suitable for various scenarios.
- Resistant to impurities, allowing operation in harsh conditions.
Disadvantages
- Radial force imbalance may cause bearing wear.
- Flow pulsation can lead to system vibration.
- Higher noise levels, unsuitable for noise-sensitive environments.
4. Screw Pumps
Screw pumps resemble gear pumps in design. One screw rotates and drives another screw, trapping liquid in the meshing chamber. The liquid moves along the screw axis and is discharged centrally.
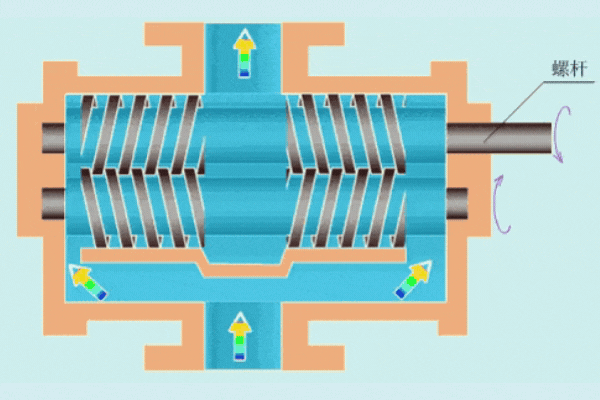
Advantages
- Wide pressure and flow range.
- Handles diverse liquids and viscosities.
- Operates with low noise and minimal vibration.
Disadvantages
High precision required for screw manufacturing and assembly.
5. Piston Pumps
Piston pumps, also called reciprocating pumps, use the back-and-forth motion of a piston inside a cylinder to move liquids. These pumps perform exceptionally well in high-pressure, low-flow applications and are widely used in industries like oil, chemicals, and machinery manufacturing.
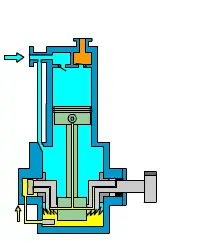
Working Principle
- Suction phase: As the piston moves backward, the cylinder volume increases, creating low pressure to draw liquid in.
- Discharge phase: When the piston moves forward, the cylinder volume decreases, forcing the liquid out efficiently.
Types of Piston Pumps
- Single-cylinder pumps: Use one piston for liquid transfer.
- Multi-cylinder pumps: Utilize multiple pistons working alternately for smoother flow.
Features
- Suitable for high-pressure, low-flow scenarios, with discharge pressure exceeding 9.8 MPa.
- Strong suction capability, handling various liquid media, including low and high viscosity fluids.
- Depending on material, can transport corrosive liquids, high-temperature tar, slurry, and more.
Applications
Piston pumps are extensively used in oilfields, mechanical industries, paper manufacturing, food processing, and pharmaceutical production.
6. Submersible Pumps
Submersible pumps, also known as rainwater, sewage, or sump pumps, are widely used in building services, homes, industries, and municipal applications. These pumps operate underwater, transporting rainwater, groundwater, sewage, or even food-grade liquids.
Features
- Impeller options: Include closed, vortex, multistage, single-channel, cutter, or grinder impellers.
- Flexibility: Suitable for high or low flow rates and head requirements.
- Applications: Used in flood control, drainage, and sewage treatment.
7. Axial Flow Pumps
Axial flow pumps feature impellers designed for axial flow, achieving high flow rates at high speeds. When combined with sufficient motor power, large impeller diameters, and wide pipeline dimensions, these pumps can handle enormous flow volumes.
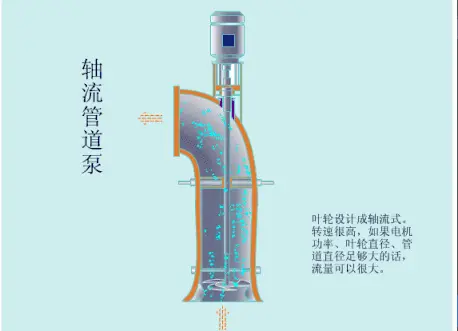
Performance Features
- Compact pipeline structure, integrating pump and motor for space-saving installation.
- Low noise and vibration, with completely leak-proof operation.
- Easy to install directly into pipelines, like a valve.
Applications
Axial flow pumps are ideal for high-flow, low-pressure scenarios, commonly used in flood drainage, irrigation, and cooling systems.
8. Self-Priming Water Pumps
Self-priming pumps work by filling the pump casing with liquid before starting. As the impeller rotates at high speed, the liquid is pushed outward, creating a vacuum that draws liquid into the pump.
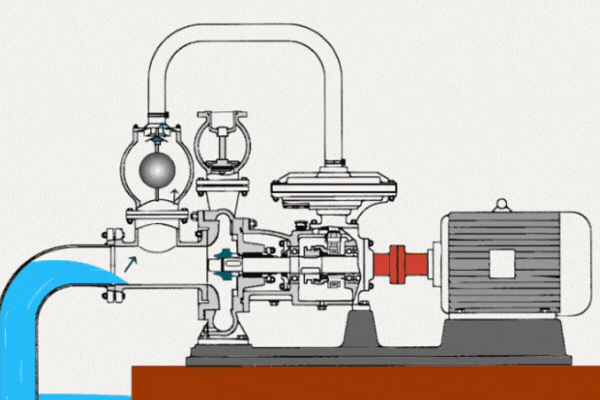
Features
- Compact structure and easy operation.
- High efficiency and strong self-priming ability.
- No need for a foot valve, reducing installation costs.
- Suitable for different liquids using various pump materials.
Contact Us for Industrial Water Pump Motor Cores
After reading this article, do you have a clearer understanding of the different types of pumps? With years of experience in water pump motor core manufacturing, we offer comprehensive solutions from customization to mass production.
Whether you need prototypes or bulk production, we can meet your requirements. We also provide a range of standard mold options to help reduce development costs.
If you have any questions or requirements, feel free to contact us. We’re happy to provide professional support!