Have you ever felt confused by the different drone motor parameters when choosing a motor? KV rating, maximum power, internal resistance… What do these numbers mean? How do they affect motor performance? For drone manufacturers and enthusiasts, understanding these key parameters can help you choose the right motor, improve overall performance, and optimize your flight experience.
This article will explain the most common drone motor parameters, including size, KV rating, no-load current, maximum power, and efficiency, to help you better understand their role and selection tips.
1. Brushless Motor Size
The size of a drone motor depends on the stator dimensions, which are represented by four digits in the model name.
You may have seen numbers like 2206 or 2306 on the outer casing of an outrunner motor. These four digits indicate the motor’s size.
For all drone motors, the first two digits refer to the stator diameter, and the last two digits refer to the stator height, both measured in millimeters. This does not refer to the rotor casing.
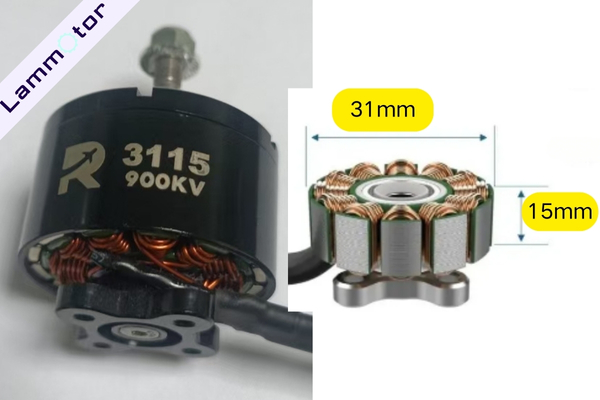
For example, a 3115 motor has a stator diameter of 31mm and a stator height of 15mm.
2. KV Rating
The KV rating of a brushless motor (measured in RPM/V) indicates how fast the motor spins per volt of input without a propeller.
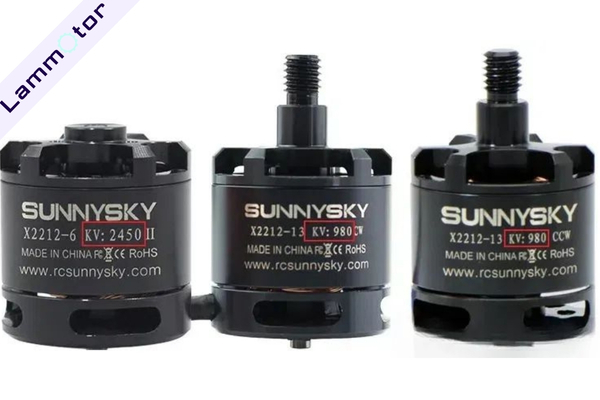
KV rating is a key drone motor parameter that defines how much speed increases for every additional volt applied.
For example, a motor with a KV rating of 1000 and an input voltage of 11V will have a maximum no-load speed of:
Lower kv motor has more turns of wire, allowing them to handle higher power and produce greater torque for larger propellers. Higher KV motor generates less torque and are suited for smaller propellers.
3. No-Load Current and Voltage
During a no-load test, a voltage (typically 10V or 24V) is applied to the motor, and the resulting current is measured as no-load current. This is a crucial drone motor parameter that helps evaluate motor performance and energy loss.
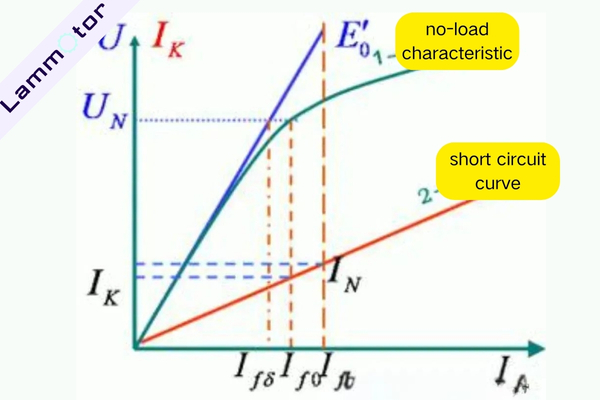
Main uses of no-load current:
- Estimating internal resistance – Helps determine energy loss due to winding resistance.
- Checking motor quality – Low and stable no-load current indicates good motor quality.
- Assessing efficiency – Lower no-load current means higher efficiency, as less energy is wasted.
- Matching components – Ensures the motor is compatible with the electronic speed controller (ESC).
4. Maximum Current / Power
The maximum current and power define the highest electrical load a drone motor can safely handle.
For example, if a motor has a maximum continuous current of 25A/30s, it means the motor can safely operate at 25A for 30 seconds. Exceeding this limit for too long can damage the motor.
5. Motor Efficiency
Motor efficiency is a key drone motor parameter used to evaluate performance. It is calculated as:
Motor efficiency varies based on input voltage and propeller load. As voltage increases, efficiency may decrease due to higher energy loss and heat generation.
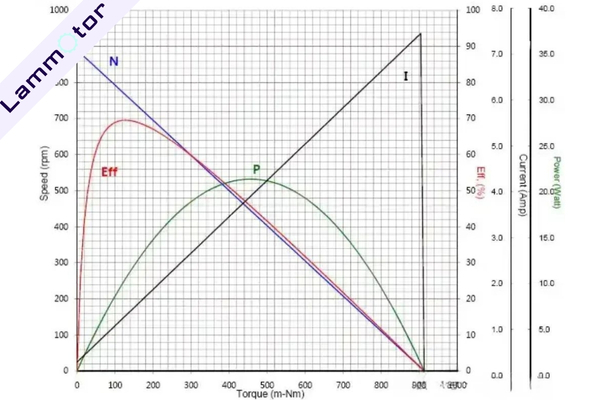
The following graph illustrates motor performance under different torque conditions:
- Torque (m-Nm) – The horizontal axis represents the output torque.
- Speed (RPM) – The blue curve shows motor speed.
- Current (A) – The black curve shows current draw.
- Power (W) – The green curve shows power consumption.
- Efficiency (%) – The red curve shows efficiency.
From this, we can observe:
- Speed decreases as torque increases.
- Current increases with torque.
- Power first increases, then decreases with torque.
- Efficiency peaks at an optimal torque range, then declines.
6. Thrust-to-Power Ratio
A drone’s thrust-to-power ratio measures how efficiently the motor and propeller work together. It is defined as:
A higher ratio means more efficient power use. It helps:
- Optimize motor-propeller combinations for better flight performance.
- Reduce battery consumption for longer flight times.
- Improve energy efficiency for cost-effective operation.
- Predict drone performance under different conditions.
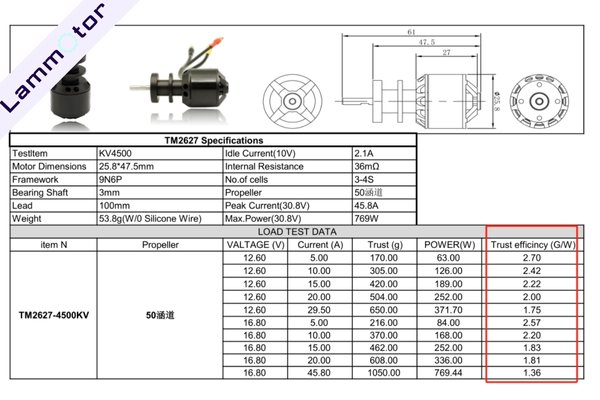
The overall performance of a drone power system depends on how well the motor and propeller work together. This is measured using the thrust-to-power ratio, which indicates how efficiently electrical power is converted into thrust. It is calculated as:
Since both propeller efficiency and motor efficiency change under different conditions, the thrust-to-power ratio is not a constant value—it varies based on operating conditions such as throttle level, voltage, and load.
Why Thrust-to-Power Ratio Matters
- Optimizing Power Systems – Comparing different motor-propeller combinations helps find the best setup for flight performance.
- Evaluating Energy Efficiency – A higher thrust-to-power ratio means more thrust per watt, reducing battery consumption and extending flight time.
- Guiding Component Selection – Helps drone designers select motors and propellers that deliver the best lift and control.
- Reducing Operational Costs – More efficient systems require less power, lowering energy costs and improving battery lifespan.
- Predicting Drone Performance – Helps engineers estimate flight endurance, lifting capacity, and motor heat generation under different loads.
7. Internal Resistance
Lower internal resistance means higher efficiency and better power output.
Although motor resistance is small, high current levels (often over 20A) make it significant. Internal resistance converts some electrical energy into heat, reducing efficiency and increasing the risk of overheating.
If a motor exceeds its current rating for 180 seconds, it could burn out.
8. Propeller Compatibility
The size and pitch of a propeller must match the motor specifications to achieve optimal thrust and efficiency.
- Larger propellers provide more thrust but require higher power.
- Smaller propellers are more efficient at high speeds.
Matching the right propeller to your drone motor parameters ensures stable and efficient operation.
9. Motor Weight
The weight of the drone motor directly affects drone weight, flight time, and maneuverability. Choosing the right balance of power and weight is crucial for optimal performance.
10. Number of Magnetic Poles (N and P)
When looking at drone brushless motor parameters, you might see a specification like 12N14P. What does this mean?
N (Stator poles) – This number refers to the electromagnetic coils in the stator. When energized, these coils create a magnetic field that drives the motor. Typically, drone motors have anywhere from 4 to 24 poles, depending on the application. The higher the pole count, the smoother and more precise the motor control, which is critical for applications like drone stabilization.
P (Rotor magnets) – This refers to the number of permanent magnets on the rotor. These magnets interact with the stator coils to generate rotation.
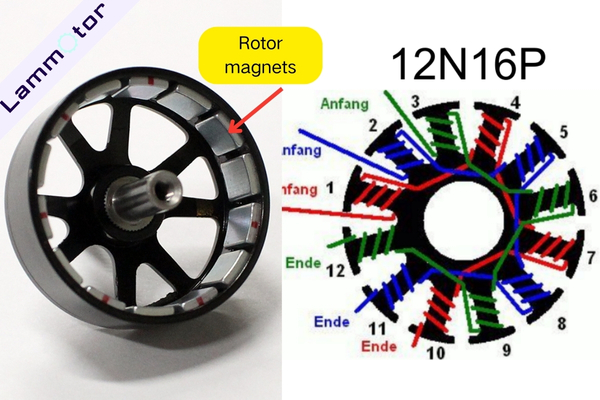
The number of poles affects the motor’s torque and speed characteristics:
- More poles (higher P count) – Lower speed but higher torque.
- Fewer poles (lower P count) – Higher speed but lower torque.
For example:
✔ A 2-pole motor spins twice as fast as a 4-pole motor at the same voltage.
✔ A 4-pole motor produces twice the torque of a 2-pole motor at the same power level.
In general, low KV motors with high pole counts are suited for large propellers that require more torque. High KV motors with low pole counts are better for smaller, high-speed propellers.
11. Motor Coil Turns (T)
Some drone motors list an additional specification: coil turns (T), such as 9T or 13T.
T (Turns) represents the number of wire windings around each stator pole.
✔ More turns (higher T count) – Lower KV, lower current draw, lower speed, but higher torque.
✔ Fewer turns (lower T count) – Higher KV, higher current draw, higher speed, but lower torque.
KV Rating and Coil Turns Relationship
For a drone brushless motor, adjusting the T value directly affects the KV rating.
For example:
✔ A 21T motor has more windings, leading to a lower KV, making it better for high-torque applications.
✔ A 9T motor has fewer windings, resulting in a higher KV, making it better for high-speed applications.
Choosing the right KV rating and coil turns ensures that your drone motor is optimized for either torque-heavy or speed-based applications.
Contact Us for Drone Motor Laminations
The performance of a drone motor depends on multiple parameters. Each factor impacts power, efficiency, and flight stability. From KV rating to coil turns, every detail matters. We hope this article helps you understand these drone motor parameters and make better decisions when selecting or customizing a motor.
If you need custom drone motor laminations, feel free to contact us! We specialize in high-performance brushed and brushless motor cores for drones to help optimize your drone power system.