As a drive motor manufacturer with years of experience in electric drive motor cooling system design, I often get asked: how do electric vehicles manage the enormous heat generated by high-performance motors?
Whether it’s a pure electric car or a hybrid, e-drive systems deliver impressive acceleration and power—but they also bring significant cooling challenges. So how are these heat issues solved?
Today, I’d like to share some ideas and examples of drive motor cooling system design.
Common Drive Motor Cooling Methods: Comparison of Pros and Cons
Air Cooling
Air cooling uses a built-in fan or external air duct to blow air across the motor housing or heat sinks, carrying the heat away.
Advantages:
- Simple structure, low cost
- Compact and lightweight
Disadvantages:
- Low cooling efficiency
- Performance affected by ambient temperature
Applications:
- Low-power, small motors such as those in fans, pumps, and small electric vehicles
Due to its limited cooling capacity and low cost, air cooling is typically used in small motors. In contrast, liquid cooling systems offer much higher cooling efficiency—often dozens of times better under the same conditions.
Water Cooling
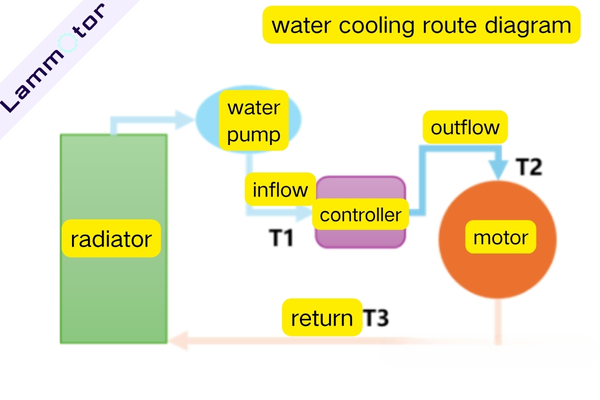
In water cooling systems, coolant ( synthetic liquid composed of pure water, ethylene glycol, and additives. The different proportions and additives result in varying performance.) circulates through water jackets inside the motor housing to absorb and remove heat. This system requires a pump and radiator to complete the cooling loop.
Advantages:
- High cooling capacity
- Supports higher power density
- Quieter operation
Disadvantages:
- Complex cooling structure, larger size
- Heat must pass through insulation layers, which lowers efficiency slightly
Applications:
- Mid- to high-power motors, such as EV drive motors, rail traction motors, and large industrial servo motors
Water cooling is currently the mainstream method, especially for systems requiring continuous operation and high power density.
Points to Consider:
- Heat must pass through insulation before reaching the coolant, making the thermal path relatively long
- Tolerance and fit impact heat transfer efficiency
The internal cooling channels in water-cooled motor housings typically come in several configurations: radial, spiral, axial, or a hybrid design.
Coolant flows through these channels, exchanging heat with the mechanical structure of the motor. The system must be both compact and well-sealed.
Oil Cooling
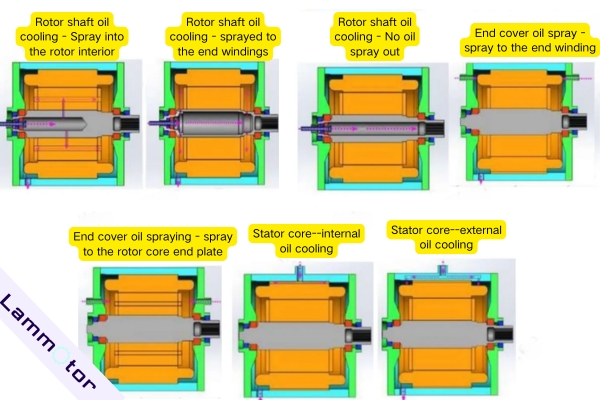
According to the contact form between the cooling oil and the stator core, it can be mainly divided into direct oil cooling and indirect oil cooling methods. Direct oil cooling includes two types: immersion oil cooling and spray oil cooling.
Oil-based cooling uses fluids with excellent insulation properties that can flow directly inside the motor, maximizing heat transfer by directly contacting internal components like the windings and core. The oil is sprayed, circulated, or used to immerse these parts, then cooled and reused through a heat exchanger.
Advantages:
- Best cooling effect, highest efficiency
- Oil can directly touch the windings due to its insulating nature
- Resistant to boiling at high temperatures and freezing at low temperatures
Disadvantages:
- Complex system, higher cost
- Requires excellent sealing to prevent leaks
Applications:
- High-power, high-speed, high thermal-density scenarios such as electric race cars, flat wire motors, and heavy-duty electric drive systems
Although oil has lower heat capacity and thermal conductivity compared to water, direct-contact oil cooling offers significantly better performance than indirect methods and even outperforms many water-cooling systems.
Common Liquid-Cooled Housing Flow Channel Designs
There are generally three different cooling channel designs for water-cooled housings:
- Axial
- Radial
- Spiral
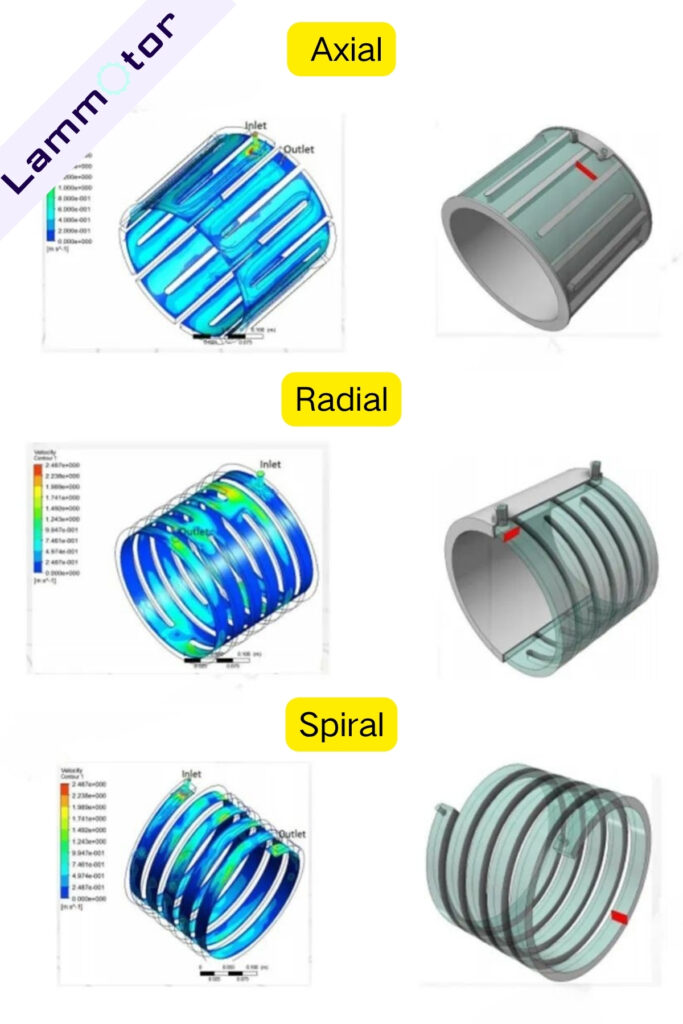
Water pressure comparison:
- Axial has the highest inlet/outlet pressure
- Spiral has the lowest
Heat transfer efficiency comparison:
- the axial type has the highest efficiency, but the flow resistance is the highest and the flow loss is the highest.
- The spiral type has the simplest structure and the lowest flow resistance, but the worst heat transfer efficiency.
Radial flow channels are a popular and balanced choice. Typically, 3–6 channels are used.
For axial channels, increasing the number improves performance, but also increases flow resistance and internal pressure drop.
A balanced approach is required. Spiral flow channels with 4–6 paths generally offer good performance—but should always be validated with fluid-thermal simulation.
Tesla Model S Motor Cooling Example
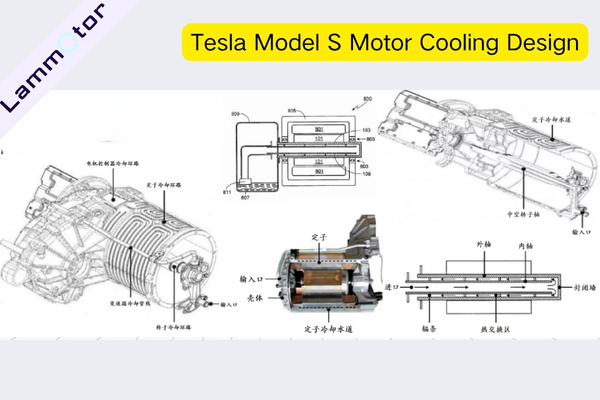
Tesla uses a hollow shaft oil cooling system (Patent No: US7579725) requiring an external electric oil pump and heat exchanger for drive motor cooling.
The motor housing combines axial and radial flow channels into a labyrinth-style cooling system for better heat dissipation.
Motor End-Winding Oil Spray Cooling
This technique is ideal for flat wire windings and involves spraying oil directly at the motor’s winding ends.
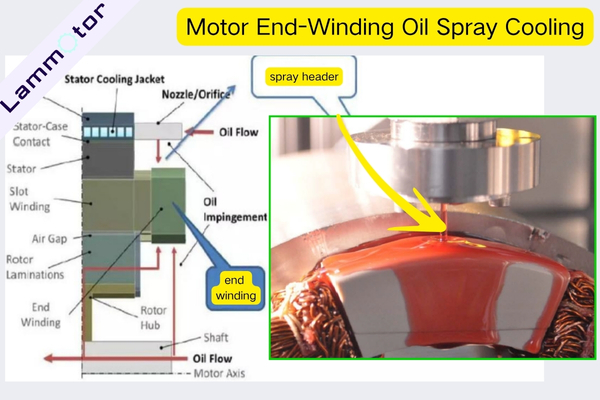
- Reduces winding temperatures by over 68%
- Increases power and torque density
- Windings with high slot-fill rates conduct heat 150% better than low-fill designs
- Thermal conductivity in the axial direction is 100x better than radial direction due to anisotropy
Examples of Stator Oil Cooling Systems for Electric Vehicles
1. Lucid Motors – Axial high-flow micro-spray design
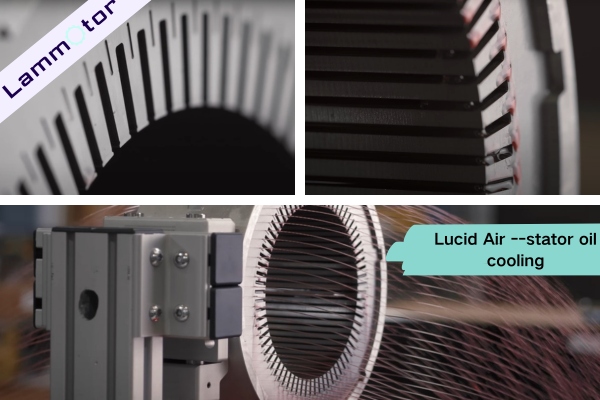
Unlike Tesla’s radial oil-spray approach, Lucid took a different path in cooling its stator windings by adopting an innovative axial oil-spray technique, with at least one coolant duct per tooth. This method uses carefully engineered high-flow axial micro-jet channels to deliver coolant directly onto the surface of the stator windings, enabling rapid and efficient heat removal.
2. BorgWarner – Centripetal Oil Cooling
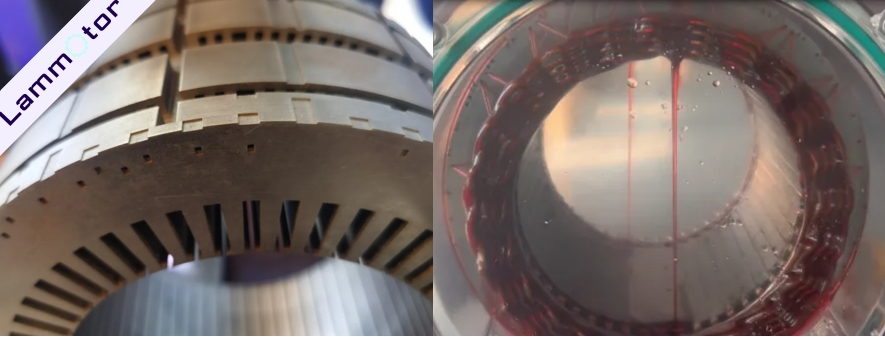
The key to oil-cooled motors lies in achieving consistent oil distribution and keeping the cooling system cost-effective.
BorgWarner’s centripetal oil-cooled stator features a circular spray pattern that directs oil from the outer edge toward the center. This design makes full use of the stator core’s thickness and angular layout, allowing the cooling oil to flow directly over both the core and the windings, ensuring fast and even heat dissipation throughout the motor.
3. MAHLE – Immersion Cooling
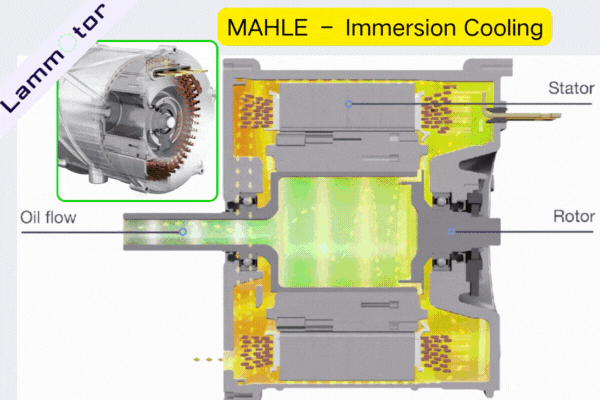
MAHLE’s SCT motor uses a full immersion cooling method. Not rotor oil-slinging methods.
The entire end winding is soaked in oil for direct and thorough cooling.
When the right-side chamber is filled with fluid, the cooling oil flows along the channel. This channel is formed between the stator surface and the inner wall of the housing. The oil then enters the left-side chamber. Finally, it exits through the outlet on the left.
4. Schaeffler – In-slot Oil Cooling
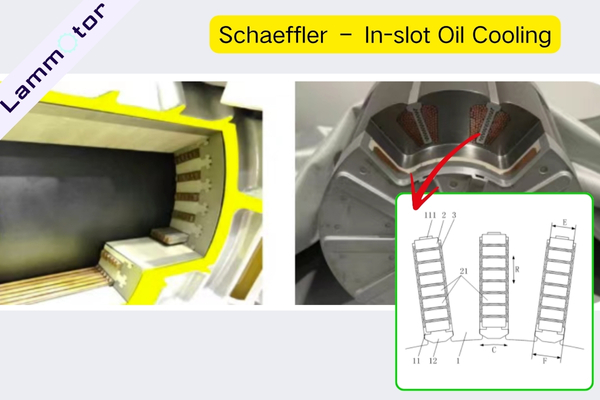
Schaeffler’s in-slot oil cooling technology involves forming multiple winding slots in the stator core, with each slot containing windings made of multiple conductors. These conductors are arranged radially along the stator core and secured in place using elastic fixtures.
The wave-shaped segments of the elastic fixtures create gaps between adjacent conductors, forming axial oil channels that run through the stator core to enable effective in-slot cooling.
From air cooling to advanced oil spray and immersion techniques, cooling system design is key to unlocking the full performance potential of drive motors—especially in demanding new energy vehicle applications. The choice of cooling method depends on your motor’s power level, structure, and application scenario.
Ready to Build a High-Performance EV Motor?
If you’re looking for a partner to manufacture high-efficiency drive motor stator and rotor cores for new energy vehicles, we’re here to help.
Contact us today to learn more about our custom motor solutions.